All published articles of this journal are available on ScienceDirect.
Physicomechanical Properties of Carbon Nanotubes Reinforced Cementitious Concrete – A Review
Abstract
Though concrete is one of the most widely used construction materials, there are some concerns and shortcomings associated with it. Cementitious materials' quasi-brittle behavior, which leads to cracking and a loss of durability, is a major concern in structural applications. In this review, the latest research on reinforcing cementitious concrete with carbon nanotubes (CNTs) is reviewed, with an emphasis on the material's structural performance in building and a comparison of CNTs to other reinforcing fibers. The improvement of the macro mechanical properties of carbon nanotube-reinforced composite structures has been discussed in the form of functionally graded carbon nanotubes reinforced composites (FG-CNTRC). Several researches have, in the past, used other forms of reinforcements to enhance the properties of concrete till the implementation of nanotechnology in concrete production by incorporating CNTs into the concrete mixes. Concrete's crucial mechanical properties as a structural material and the durability of conventional cement-based building materials can both be improved by CNTs. They have drawn a lot of interest because they are an engineering material with a wide range of uses. The creation and characterization of cement-based materials reinforced with CNTs have been studied by researchers. Comparisons between the effects of CNT and other fibers on concrete have also been made. This concrete reinforcement type's environmental impact and sustainability have also been discussed. According to studies, CNT can greatly enhance the performance of cement-based materials.
1. INTRODUCTION
There are not many new raw materials available today that cementitious materials (like concrete) may integrate to increase their durability and strength while lowering their environmental impact [1-4]. Investigations into the characteristics of building materials have historically only been feasible on a large scale. Innovative resources have been initiated though, and understanding their behavior at the nanoscale is crucial. An effective strategy for creating concretes with superior qualities and more controlled deterioration is illustrated in this study, and an evaluation has been made of the cement matrix and the way it reacts alongside different concrete design components.
Cement-based materials have poor torsional strength and fracture toughness, resulting in cracking (i.e., quasi-brittle behavior). To make up for the poor tensile strength, fibers of all sizes have been used throughout the past few decades [5-7]. The form and size of the fibers, their surface textures, the interfacial connection strength between the fibers and the matrix, crack bridging capabilities, and energy dissipation during crack propagation are all factors that influence fiber contributions depending on the fiber type [8, 9]. Smaller fibers are more effective at stopping comparable-sized cracks at an earlier stage of cracking. Meanwhile, because fracture nucleation begins at the nanoscale [10], even microfibers are unable to avoid crack formation [11, 12]. They can, however, nevertheless prevent crack growth until the crack width approaches the microscopic scale [13, 14]. The discovery of carbon nanotubes (CNTs) has opened up new possibilities for improving the microstructure of cement-based products. CNTs outperform regular fibers in terms of strength, toughness, and specific surface area.
Unlike microfibers, nanofibers and nanotubes, particularly CNTs, have been shown not to trigger or delay crack nucleation at the nanoscale [15, 16]. According to the number of internal layers, CNT is divided into two main types (Fig. 1):
i. Single-walled carbon nanotubes (SWCNTs)
ii. Multi-walled carbon nanotubes (MWCNTs)
Both of these types have been used in cement-based materials. SWCNTs typically possess diameters up to 2 nm, whereas MWCNTs can have diameters ranging from 5 to about 100 nm [17].
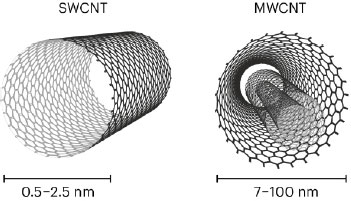
CNTs can be characterized as graphene sheets rolled into a cylindrical tube with a length of 1 to 100 µm. These structures were initially identified in 1991 by Japanese scientist Iijima [19]. CNTs can be produced using several methods, for example, electric arc discharge, laser ablation, and chemical vapor deposition. The last one is currently the most used method. CNTs have very good physicomechanical properties [20, 21].
Graphene nanoplatelets (GPL) are a different substance that is quickly gaining popularity as a nanofiller. Graphene and other graphene derivatives are not preferred reinforcing elements, so they are becoming an emerging nanofiller in the field of nanocomposites due to their simplicity and low cost of production. A growing body of research on GPL-reinforced materials and structures has been published in recent years, with GPL-reinforced beam, plate, and shell structures receiving a lot of attention [22].
Numerous industrial fields, including metallurgy [23, 24], the polymer industry [25, 26], and of course the concrete industry [27, 28], may get an advantage from the usage of CNT as a reinforcement matrix. Other nanomaterials, such as nano-silica, may have intriguing effects on cementitious composites. There have been various nano-silica experiments conducted. Their findings back up the theory that incorporating nano-silica into the cement matrix improves the mechanical properties of cement composites [29]. However, the primary focus of this research is on the incorporation of CNT as a dispersed form of cement matrix reinforcement in cementitious composites.
The length of CNTs ranges from less than several hundred nanometres up to several centimeters [30, 31]. Because of the high aspect ratio (length-to-diameter ratio) of CNTs along with their nanoscale size, the distance between adjacent nanotubes can be reduced [32]. As a result, there are many CNTs at the crack plane, delaying crack propagation. CNT possesses extraordinary features that have the potential to be as crucial for industry development as the discovery of the steam engine. CNTs exhibit excellent mechanical, thermal, and electrical properties, including an elastic modulus of around 1 TPa, tensile strength ranging from 11 to 63 GPa, a volumetric weight of about 1300 kgm3, and a surface area ranging from 70 to 400m2gl [33, 34]. Carbon nanotube characteristics are depicted in Table 1.
Internal Diameter | Approximately 5–12 nm |
---|---|
Outer diameter | Approximately 30–50 nm |
Length | 10–20 𝜇m |
Bulk density | 0.22 g⋅cm−3 |
True density | 2.1 g⋅cm−3 |
The authors of a study [36] highlighted the work done to create CNT-strengthened deformable structures, fabrication techniques, and modeling and analysis of the mechanical behavior by concentrating primarily on engineered CNT distributions throughout the matrix. As a result, the discussion on grading, aligning, and positioning the CNT fibers to achieve the highest efficiency has also been reviewed. They realized that combining large amounts of CNTs with a matrix might be expensive. The impact of various CNT gradings on the static and dynamic behavior and stability of various types of structures has also been discussed within the context of both linear and non-linear analyses.
Concrete is the most used building material. Researchers consistently seek techniques to boost the strength of concrete to overcome the brittleness problem because this material has a well-known weakness that causes excessive crack propagation and it eventually collapses. This research has paved the way for the use of micro and microfibers, reinforcement bars, and other additives in concrete because of the improved benefits of nanoparticles. The primary purpose of this work was to examine and provide an assessment of previous research on cementitious materials-reinforced CNTs. The incorporation of carbon nanotubes (CNTs) into concrete has improved the properties of cementitious materials, which has led to the major goal of this paper. Fig. (2) depicts the steps taken to achieve the goal of this work. As the properties of CNTs in concrete stand some limitations, they could affect the full purpose of the CNTs.
2. LIMITATION OF CNTs
CNTs involve some limitations, as listed below.
i. Lack of solubility in most solvents compatible with the biological milieu (aqueous-based).
ii. The production of structurally and chemically reproducible batches of CNTs with identical characteristics.
iii. Difficulty in maintaining high quality and minimal impurities.

Material | Material Young’s Modulus (GPa) | Tensile Strength (GPa) | Density (g/cm3) |
---|---|---|---|
Single wall nanotube | 1054 | 150 | N/A |
Multi-wall nanotube | 1200 150 2.6 | 150 | 2.6 |
Steel | 208 | 0.4 | 7.8 |
Epoxy | 3.5 | 0.005 | 1.25 |
Wood | 16 | 0.008 | 0.6 |
Table 2 compares some properties of CNTs to other structural materials.
Once the limitations of a material have been identified, the methods and implementation of the material can be identified to overcome or reduce the limitation of CNTs, and hence their dispersion.
3. DISPERSING CNTs
Precision dispersion and uniform distribution are essential for the successful application of the cement matrix because CNT has the propensity to form bundles [20]. The two primary ways for dispersing nanotubes nowadays are mechanical processes and chemical processes that change the surface energy of materials. Mechanical methods include high shear mixing and cavitation, specifically hydrodynamic cavitation (cavitation brought on by rapid liquid flow) or acoustic/ultrasonic cavitation (cavitation brought on by high-energy acoustic waves traversing a liquid medium). The combination of methods for dispersing CNT, such as the ultrasonic method and a suitable surfactant, is discussed in the literature. After being subjected to ultrasonication, carbon nanotubes may tend to clump together. Surface-active compounds may help them detangle more easily [37-39]. It is essential to make sure that the additional surfactant has no negative effects on how concrete or cement mortar sets and hardens. One of the most important elements in the creation of improved cement-based composite materials is CNTs' excellent dispersion. CNTs are attracted to one another by van der Waals forces because they have a large surface energy and a very high aspect ratio. These characteristics cause a significant propensity for them to group or form bundles. Bundles weaken the matrix, which is where the earliest cracks are formed following loading, thereby reducing the material's total strength [40].
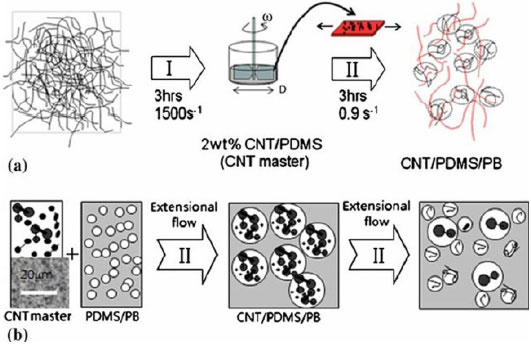
CNTs with surfactants inserted into their structure are a recent development. The structure of graphene sheets could be harmed or even destroyed if the supplied acoustic energy is surpassed when CNT is dispersed in an aqueous medium via ultrasonication, depending on the concentration of CNT. The projected improvement in the physicomechanical characteristics of specimens increased with CNT is lessened by CNTs' deformation [13, 41]. Fig. (3) shows the schematic diagram of the dispersion of CNTs.
When the methods and processes of dispersing CNTs in concrete have been identified, incorporation becomes necessary.
4. INCORPORATION OF CNTs IN CEMENTITIOUS MATERIAL
At the micro level, the impact of including CNTs in the concrete mix has been observed and researched [43]. The microstructure of a concrete mix without CNT reinforcement was examined, and it was found that the area where the surfaces of the aggregates and cement particles met crystallized calcium hydro-silicate was structurally weak. On the other hand, the dispersion of CNTs in a concrete mix resulted in creating a strong covering (with a thickness of 1 to 5 μm) for the solid particles, including cement and fillers, which caused these particles to be more interlocked with the aggregates’ surfaces.
Since the interlock between the aggregates and the binder is strengthened after adding CNTs to the mix, it is easy to assume that dispersing CNTs in a cement concrete mix will raise the overall strength of the concrete. CNTs, as opposed to macro or microfibers, stop cracks from forming at the nanoscale and prevent them from spreading to the microscale [11, 44].
4.1. Mechanical Properties of Cementitious Material Consisting of CNTs
Because CNTs tend to form bundles, their optimal dispersion and uniform distribution are crucial for the cement matrix to function properly [20]. Currently, chemical techniques that alter the surface energy of materials and mechanical techniques are the two main means of dispersing nanotubes. Cavitation and high-shear mixing are two examples of mechanical methods. Cavitation can be caused by either high-energy acoustic waves passing through a liquid medium (acoustic/ultrasonic cavitation) or by high-speed liquid flow (hydrodynamic cavitation). According to the literature, CNT dispersion techniques can be coupled, for example, by applying a suitable surfactant and utilizing an ultrasonic method.
Nanomaterial research has already led to the creation of low-cost, high-performance cement compositions that are widely employed in civil engineering [45, 46]. The distribution and size of the aggregate particles determine the fluidity and workability of concrete in its unhardened state, while the strength and durability of concrete in its hardened state are influenced by both the size of the aggregate particles and the arrangement or grouping of the aggregate [47].
The ability of nanoparticles employed in the construction sector to provide mechanical reinforcement to concrete structures is one of their most attractive qualities. This can be accomplished by adding CNTs to cement compounds because of their exceptional qualities, creating a new class of cement products that are beneficial to the building sector [48, 49].
The cementitious materials' molecular structure is altered by the nanotubes, improving their mechanical and physical properties. These nanotubes have a direct impact on the concrete structure's mechanical performance, volumetric stability, durability, and sustainability [50, 51].
Nowadays, CNTs are also being used to reinforce many types of materials, including metals [52]. Studies have demonstrated that the contact between a polymer and CNT may transfer pressure above 500 MPa; this strength is ten times more than the interface between a polymer and carbon fibers [53]. The addition of a low concentration of MWCNTs to the cement composites led to a boost in early-age compressive strengths, according to the authors of a study [54].
A research conducted earlier [55] found that cement samples incorporating CNTs had higher tensile strength and a better stress-strain relationship in direct tension. MWCNTs can reduce the water absorption and permeability coefficient of reinforced cement-based materials, as demonstrated by Han et al. [56]. According to the research conducted [57], MWCNTs with an outer diameter (OD) of 20 nm or less had compressive strengths that were higher than those of MWCNTs with larger ODs when employed in mortar, with the smallest size MWCNTs having the highest compressive strengths.
The compressive strength of cement composites decreased with the increase in the CNT dosage. This research used different dosage rates of MWCNTs, ranging from 0.00% to 0.12% by weight of cement [58]. In a study to create surface-treated, MWCNT-reinforced cement composites based on their flexural and compressive strengths, an appropriate mix fraction has been suggested [59]. It was reported that CNT reinforcement could provide durable and superior cementitious composites.
A group of researchers [60] experimented on a cementitious compound containing CNTs under compression and found that SWCNTs and MWCNTs increased the compression resistance compared to that of pure cement at 6% and 30%, respectively. Also, L. Y. Chan and B. Andrawes [61] conducted experiments to investigate the effectiveness of the CNTs, uniformly dispersed and randomly oriented, for the reinforcement of cementitious composites.
Results of the works carried out previously [48, 62, 63] have shown that cementitious material's mechanical characteristics, compactness, and durability may all be significantly enhanced by nanomodification. There has not yet been agreement among the numerous researchers who have studied the effects of various CNT concentrations on the durability of cement-based products [63].
The impact of incorporating CNTs into cement composites has been the subject of numerous tests and investigations. In an experiment, CNTs that were the same size but variable in length and concentration were added [15]. The results at 28 days of age revealed an improvement in flexural strength compared to the plain cement composite. Flexural strength was enhanced and improved by CNTs of various lengths and concentrations. This suggests that an increase in CNT content causes an increase in flexural strength without any change in the CNTs' length [63].
Maximum load and deflection are improved by the inclusion of CNTs, but CNTs cement composites exhibit an increase in maximum load before failure when compared to composites without CNTs. As a result, despite the increased maximum load, there is no increase in deformation. This is due to CNTs’ role in cement composite as a reinforcing material, which increases flexural strength [63-65].
The inclusion of CNTs to cement composites also affects the tensile or elastic modulus. The slope of the stress-strain curve is used during the tensile test to calculate elastic modulus. No matter how many CNTs are present in the sample, the results always indicate the samples with CNTs to have a larger elastic modulus than plain samples [66].
Regarding the structural effectiveness of CNT-reinforced concretes, Hunashyal et al. [55] reported an experimental investigation that showed that adding 0.25% weight of MWCNTs to cement-based beams only significantly increased their toughness and flexural capacity. CNT-reinforced cement beams (with 0.25% weight of cement MWCNTs) have been shown to have a 47% greater flexural capacity, on average, and a toughness increase of 25% when compared to beams cast from cement alone. Additional comparable tests against a reference beam made of plain cement have demonstrated the overall flexural performance of reinforced beams to be significantly improved by adding CNT at percentages as low as 0.025% weight of cement to the concrete mix [55].
4.2. Microstructure Cementitious Material Consisting of CNTs
Microstructure is regarded as a surface produced by substances, like cement composite. The characteristics of materials that reflect and regulate the broad scale of material to be employed in industrial practice can be determined by this microstructure [65].
It is widely accepted that when cement components are combined with water, they get hydrated and form hydration products, such as C-S-H and Ca(OH)2. The hydration products and CNTs are attracted to one another, which improves the microstructure of cement composites. Scanning electron microscopy (SEM) study is used to examine micrographs of cement composite, including CNTs, to better understand the improvement that results due to the incorporation of CNTs.
CNTs have a huge surface area, which increases their attraction to hydration products that coat the surface of the CNTs. As a result, CNTs are simple to identify by SEM at an early stage [67].
A study conducted by Li et al. [68] compared cement composites made with and without CNTs. The hydration products of C-S-H gel and Ca(OH)2 were visible in the micrograph of the planar cement composite, which did not include CNTs. Pores and fissures were also visible. Contrarily, the microstructure of the composites containing CNTs displayed fewer cracks, fewer holes, and a homogeneous hydration product.
Both the mechanical and durability characteristics of cement composites are influenced by porosity, with large pores harming both [69]. Porosity and pore size decrease with the addition of CNTs into cement composites [70]. The porosity of cement composites can be reduced by filling the pores with CNTs because of their small size, which is measured in nanometers. Porosity lowering is likewise influenced by different CNT addition percentages, with a larger CNT content being associated with reduced porosity [71].
By incorporating 1% CNTs into cement composite, SEM examination was used to look into the microstructure's characteristics. The micrograph revealed that CNTs interact favorably with the cement's hydration product, indicating that they serve as a filler to create thick microstructure [10]. Using SEM examination, Chaipanich et al. investigated a composite made of fly ash, cement, and CNTs. They discovered that adding 0.5% and 1% of CNTs helped fill in the pores, greatly enhancing the mechanical properties of the composite. It is also obvious from the micrograph that CNTs and the fly ash-cement composite interact well [72].
Furthermore, the addition of CNTs has been studied [64] with different content of CNTs from low to high. The high energy of CNTs surfaces enhances the hydration process of the cement. The microstructure showed the CNTs surrounding the cracks where these cracks only appeared on the areas that were not reinforced with CNTs. This occurred in the sample that contained low content of CNTs, that is 0.025%. The second sample, which had 0.1% CNT content, demonstrated CNTs to be evenly distributed throughout the cement composite. The samples with low and medium CNT concentrations showed no signs of aggregation. The final sample, which had a 0.2% concentration of CNTs, exhibited a strong correlation with hydration products. However, only the central portion of the microstructure exhibited CNT aggregation. Agglomerated CNTs may produce a weak zone that appears as pores. Therefore, adding too many CNTs does not improve the qualities of cement composite, but occasionally, it can cause them to degrade. Hence, the production of better CNT-reinforced structures is required.
5. FUNCTIONALLY GRADED CNT-REINFORCED STRUCTURES
Evidence suggests that the amount and placement of CNTs in a composite material may have a significant impact on a structure's mechanical properties [73]. The researchers pondered on how to enhance the macro-mechanical characteristics of carbon nanotube-reinforced composite structures in the case of low content. Functionally graded carbon nanotube-reinforced composite structures were first put forth by Shen [74, 75], who described how the volume content of CNTs is distributed in the material in a gradient. Since the composite now has a satisfying reinforcing agent and a designable characteristic, functionally graded carbon nanotube reinforced composites (FG-CNTRC) research has gained popularity in recent years. Since FG-CNTRC is a composite material with a precise composition or structure, it is likely to be used to create components with particular local properties that are desired. For the material properties of this composite material to be graded in the thickness direction, it follows the FG pattern of CNT reinforcement being uniaxially aligned in the axial direction [75]. Additional research has been done to explore the many characteristics of FG-CNTRC structures [75].
Since each component works in harmony with the others, composite materials are well known for their exceptional material properties. A sharp transition in the properties of the composite materials at the interface can result in component failure by delamination [76, 77] when the composite structures are subjected to extreme working conditions. Niino [78] was the first to suggest the idea of functionally graded materials (FGM) as a solution to this issue. Only uniform or random CNT dispersion was permitted by the conventional fabrication process for nanocomposites, which naturally gave CNRTCs uniform elastic properties in space. The concept of FGM [79] can, however, be used to overcome this limitation in producing the spatial material-property distribution. These materials could eliminate interface issues, like stress concentrations and poor adhesion, because they swap the sharp interface for a gradient interface that results in a smooth transition of properties from one material to the next [80].
In FGMs, the volume fractions of the base constituents through the thickness can be artificially designed to maximize the target performance. The structural and conductive characteristics of these new composite materials were reported by Smaranda and others [81] after they prepared composites in the free membrane form. Having been inspired by the idea of FGMs, Shen [74] and Ke et al. [82], to suppress bending deformation and control vibration, presented a deliberate CNT distribution with CNTRCs throughout the thickness. The three most representative functionally graded CNT distributions are FG-V, FG-O, and FG-X. These CNTRCs are referred to as FG-CNTRCs, and they have quickly risen to the top of researchers' lists [83-85] due to their functional CNT distributions.
6. COMPARING CNTs AND FIBERS USED AS CONCRETE REINFORCEMENT
The researchers [16] provided proof by measuring the hardness that CNTs can influence cement hydration in their initial state, as well as evidence that a solid link between cement paste and CNTs is conceivable. According to their findings, nanotubes play a specific function in preventing cracking in composite materials because they are more evenly spread than the reinforcement fibers in terms of size and proportion when inserted into the matrix.
According to Balaguru and Chong [86], the development of nanoscience for concrete is necessary because it can be used to create new products with significantly better performance thanks to properties, like low shrinkage, resistance to high and low temperatures, compatibility with various types of fibers, and responsiveness to nanomaterials, like CNTs. Due to their resistance to fracture propagation and other irregularities, CNTs and carbon nanofibers seem to be some of the most promising nanomaterials for enhancing the mechanical properties of cementitious materials [87]. Every reinforcement material has its uniqueness. Therefore, it is ideal to know the way each behaves and the design procedures. The next section discusses the modeling and designing of cementitious materials bearing CNTs.
7. MODELING FOR THE MIX OF CEMENTITIOUS MATERIALS CONTAINING CNTs
Numerous factors, including CNT type [48], CNT concentration [88], dispersion surfactants, CNT treatment [68, 69], dispersion technique, interaction with cementitious materials and bond strength, the water-cement ratio [40, 69], and CNT geometry [57, 89, 90], can affect how well carbon CNTs reinforce structures. Despite ongoing research, a significant barrier prevents CNT from finding widespread use in the building sector [66, 91]. The difficulty in predicting the mechanical properties may be related to the interplay between several parameters.
It has been noted by a few researchers that prediction models have this problem. To determine the mechanical properties utilizing several parameters, such as the dispersion procedure, testing age, and CNT concentration, strong interactions between various parameters have been found in the results [92].
Different methods have been used to disperse CNT or carbon nanofibers (CNF) [28], such as the combined use of surfactants and sonication, the modification of the nanotube surface, or functionalizing (incorporating molecular groups to the fiber’s surface to improve the affinity with the matrix) [67, 93] and even the direct growth of CNF on unhydrated cement particles [94]. Sanchez [95] studied a dry mixture of cement, CNF, and silica fume, and its latter mix in water, concluding that the silica fume, due to its small particle size, helps in fiber dispersion and improves interfacial interaction between the CNF and the cement hydrated phases. In another study, Yazdanbakhsh [96] reported significant challenges, including the detrimental effect of using a lot of surfactants (sufficient for CNF and CNT dispersion) during cement hydration, the CNT breaking and shortening due to excessive ultrasonic energy, or even the deterioration of cement-composite properties while using cement with small particle size.
CNTs' uneven dispersion and weak bonding to cement paste are the main issues in using them as an addition in cementitious composites. Since CNTs tend to agglomerate due to their enormous surface area, adding them to paste alone has no effect. To achieve a high CNT dispersion, CNTs are often utilized as an aqueous suspension in the presence of a surfactant that has previously undergone sonication. Supercritical-fluid chromatography (SFC) methods were applied for this purpose [10, 15]. As a surfactant among others, H2SO4, HNO3 [68, 97], and isopropanol [98] were used. A stable dispersion of CNTs was also obtained using sodium dodecyl sulfate (SDS) [99, 100], sodium dodecyl benzene sulfonate (NaDDBS), and di-methyl acetamide (DMAc) [21]. UV spectroscopy and transmission electron microscopy (TEM) were used to examine the effects of SDS on the formation of an extremely high degree of CNT dispersion and a stable aqueous solution (stable for a few months) [101]. Although there have been some studies on the utilization of CNT dispersion with SDS [102], NaDDBS [103], and DMAc for cementitious composites, further study is still needed in this area.
8. SUSTAINABILITY AND ECOLOGICAL IMPACT OF CARBON NANOTUBES CONCRETE
CNTs have been lauded as a new “wonder material” ever since they were discovered in the early 1990s. They are tiny building blocks that have the enormous potential to be used to create fibers, films, filaments, wires, and circuits for a wide range of industrial applications, including reinforced concrete, clothing that is resistant to tearing, stronger and lighter tennis rackets, and bicycle parts. They can also be used to create revolutionary electronics that are at the center of many billion-dollar industries in the twenty-first century.
Another challenge facing the mass production and the usage of CNTs in the construction industry comes from an environmental perspective. Jackson et al. [104] investigated any potential environmental effects that could arise from the mass manufacture of CNTs. The effects of direct exposure to CNTs are still not well understood, according to scientists. Additionally, they assert that a variety of factors affect how hazardous CNTs are, including the total surface area of the particles, the chemistry of those surfaces, functional groups, coatings, polarity, solubility, particle shape, photochemistry, and the process used to make the CNTs. The key conclusions reached by Jackson et al. [104] are as follows:
i. CNTs do not pass through organic matter easily (negligible percentage only).
ii. Aquatic creatures are more sensitive to the toxicity of CNTs than terrestrial ones.
iii. Invertebrates (bone-less creatures) are more sensitive to the toxicity of CNTs than vertebrates.
iv. SWCNTs are more toxic than MWCNTs.
v. It is possible to find certain concentrations of CNTs that do not have any environmental effects, but more experimental works/data are needed.
The growing usage of nanoscale particles has sparked debate over the environmental and toxicological consequences of direct or indirect exposure to such materials. The use of CNTs is preferred because they resemble asbestos. Asbestos fiber inhalation is recognized as a cause of asbestosis (a long illness), carcinoma, and mesothelioma. Because this mineral silicate has a fibrous structure, like nanofibers, size, ratio, and surface can all affect its toxicity. Because asbestos has dimensions measured in micrometers rather than nanometers, comparing nanotubes to asbestos should be done with caution. The harmful effects of nanotubes may arise from the mixture of high area and surface intrinsic toxicity. Unlike conventional materials, nanoparticles are also more toxic to the lung and even modify the structure of proteins [105, 106].
Nanoparticles can therefore cause inflammatory and immune reactions, which can affect how well tissues and the body as a whole operate. Extreme exposure to SWCNT inhalation may constitute a serious threat to occupational health, according to studies examining the toxicity of SWCNTs in mouse lungs. Poland et al. have shown that exposing mice's mesothelium to long MWCNTs caused pathogenic behavior concerned with the length, similar to asbestos. This resulted in granulomas, which are lesions, as well as inflammation. The results indicate the need for additional research and safety measures to prevent problems in circumstances involving prolonged exposure to nanoparticles [106].
9. DISCUSSION
One can understand that the endeavor to use nanotechnology in the field of construction materials was a very successful one by looking at what has been done in recent years regarding the reinforcement of cementitious materials with CNTs in the literature. This is because CNTs have improved several of the most crucial qualities in concrete, despite the lack of extensive research on them. CNTs have drawn the attention of numerous scientists and companies because of their exceptional mechanical properties and optimistic future. There have been numerous attempts to produce CNTs in large quantities while maintaining their quality [17].
The use of CNTs in concrete reinforcement is a development in concrete design, but standards, norms, and legislation should be established to make this kind of reinforcement teachable at all levels of education and businesses.
The use of CNTs as a reinforcing material for important structures has to be investigated in sub-Saharan African countries and coastline nations due to the excellent qualities associated with CNTs. By employing the proper percentage of CNTs in the concrete mix, the harmful effects of CNTs can be prevented.
It is crucial to take into account this form of reinforcement material in the effort to meet the Sustainable Development Goals of the United Nations because the production processes do not call for the rudimentary way of extracting natural minerals from the soil, which could pose environmental risks.
CONCLUSION
In conclusion, this paper has investigated the use of CNTs as concrete reinforcement, concentrating especially on the structural improvement of concrete as a result of this reinforcement. The features of CNTs, their cost, and sustainability, the prospective uses of CNT-reinforced concrete, the key difficulties this new technology faces, and the experimental techniques that could be used to reinforce concrete with CNTs in the lab have also been covered.
The properties of the cementitious matrix have been significantly improved by the addition of modest amounts of carbon nanotubes. From the review, it has been learned that adding CNTs to concrete has an impact on how easily it can work.
Without a doubt, CNTs are a material with immense promise that may lead to advancements in future technologies, such as electric machinery and biofields. As a result, CNTs can be used in future studies in the building sector.
To obtain positive benefits of CNTs in cement composite, an appropriate dispersion of CNTs is required. In this review paper, different dispersion methods have also been investigated, such as surfactant, where enhancement of the mechanical properties has been achieved. However, no significant improvement has been observed when poor dispersion of CNTs has occurred.
With regards to the compressive strength of cement composite, the addition of CNTs with various effects has been noted. While other CNTs additions have indicated a decrease in compressive strength, certain CNTs additions have revealed an improvement in compressive strength. Overall, adding a percentage of CNTs and using the right dispersion technique could provide production materials with excellent compressive strength.
The addition of CNTs enhances and increases the flexural strength of cement composites depending on the concentration of CNTs. Regardless of the length of the CNTs, optimum concentration can result in higher flexural strength, whereas some excessive concentration may lead to a reduction in the strength. Moreover, the elastic modulus shows an increment when CNTs are added.
In cement composites, CNTs serve as a filler that can seal pores, lessen porosity, and manage microcracks. The simple cement composite without CNTs is less thick and poorly packed, according to micrographs, than the microstructure involving CNTs.
Since reinforcing cementitious materials with CNTs is a new technology, many challenges must be considered before it becomes commonly practiced. As explored in this paper, the applications of CNTS are a lot, and thus, CNTs-reinforced cementitious materials are worth more extensive research.
RECOMMENDATIONS
More research should be done on the combined reinforcement of concrete with CNTs and different fiber types. To produce lightweight concrete, the use of CNTs for reinforcing expanded clay concrete should be researched. Chopped basalt fiber should be used as a form of hybrid fiber reinforcement with CNTs because of the excellent properties basalt fiber possesses. It has become a challenge to model some of the new reinforcement materials in finite element software as this software does not incorporate these new materials.
LIST OF ABBREVIATIONS
CNTs | = Carbon nanotubes |
FGCNTRC | = Functionally graded carbon nanotubes reinforced composites |
GPL | = Graphene nanoplatelets |
OD | = Outer diameter |
FGM | = Functionally graded materials |
CNF | = Carbon nanofibers |
CONSENT FOR PUBLICATION
Not applicable.
FUNDING
None.
CONFLICT OF INTEREST
The authors declare no conflict of interest, financial or otherwise.
ACKNOWLEDGEMENT
The authors are grateful to Afe Babalola University, Ado-Ekiti (ABUAD), Ekiti State, Nigeria, for financial support.