All published articles of this journal are available on ScienceDirect.
The Effect of Form Factors of Shock Absorption Mat’s Subunits on Attenuation of Force from Elderly’s Fall
Abstract
Background and Objective:
The purpose of this study was to investigate how differently various form factors of subunits of shock absorption mat attenuate force from the elderly’s fall.
Methods:
The study procedures were the following: (1) literature review: possible form factors affecting the shock absorbing capacity were analyzed and synthesized from the review; (2) synthesis of design criteria: criteria for force simulation were formulated based on the information from the review; and (3) simulation: simulation of force from elderly’s fall absorbed by such mats with the following control and independent variables that were analyzed and synthesized in the previous steps: (control variables): 1) impact force, 2) physical properties of the rubber material; (independent variables): 1) form of cross-section, 2) form of edges, 3) pattern of arrangement of subunits in the structural layer, and 4) dimensional proportion of subunits.
Results and Conclusion:
The simulation results show that the subunits with a circular-cross-section and hourglass-like-edge form factors were the best at attenuating impact force. The best pattern of subunit arrangement was a table arrangement. This study was a preliminary study to a design of subunits of shock absorption mat. The results would be used in the next, more comprehensive study.
1. INTRODUCTION
World Health Organization [1] has released the following statistics: one-third of the elderly population slips and falls at least once in a year, and the trend is that 28-35% of elderlies over 65 years of age will slip and fall in a year. This percentage increases to 32-42% for elderlies 70 years of age [2, 3]. As people grow old, they suffer calcium loss from bones [4], making them fragile. In combination with weaker muscles [5], their bones are easily broken from a fall [6, 7]. For each year, 23,000 elderlies have to spend a total of one billion US dollars for their recuperation from broken hip bone [9]. Moreover, among those who fall, 70% die from this cause [9]. From the results of a survey [10], it was found that 95% of the participated elderlies caught a hip injury from a fall [11]. Patients with hip fracture not only usually lose their lives in 1 year after the fall [12], but also suffer negative changes to their physical ability [13, 14]. Elderlies cannot change their behavior easily; therefore, a change in the environment is necessary to prevent and reduce their injury from a fall.
A study [15] states that the products for preventing injuries from slipping can be divided into two categories: 1) products for alleviating injuries after a fall such as padded shock-absorption underpants for alleviating hip injuries; however, they are not popular with elderlies in hot-weather countries because they are a little uncomfortable to wear, but this may not be a problem for elderlies in cold-weather countries; and 2) products for preventing slipping such as anti-slipping mat and safety rail for the bathroom. In the authors’ opinion, the main cause of injuries from slipping and falling especially hip injuries is from the high reaction force from the floor to the fallen body or hip. If the floor system can absorb some of the impact force of a fall, the injuries will be lessened. Therefore, an effective shock-absorption mat should be developed.
A distinction is made between a low-stiffness floor mat that can reduce foot fatigue in an airport, factory, or nursing home [16] and a full-fledged shock-absorption mat used in military vehicles or emergency speed boat [17]. The former does not attenuate the impact of a fall as much as the latter can. The latter can absorb a considerable amount of impact force by its specially designed structural layer of subunits that attenuates the reaction force that is reflected back to the fallen body.
The form of a subunit of a structural layer of a shock absorption floor mat can be described as the form of its cross-section and the form of its edges. They can be geometrical or free-form. Previous studies on subunits and impact force indicate that subunits with rectangular and cylindrical cross-sections were easily damaged by an impact force. Reference [18] states that there has been no in-depth study on the relationship between shock-absorption and forms of cross-section and edges of subunits.
Concerning our intended structural layer, it would consist of 3 layers [19]: upper and lower surface layers and a structural middle layer. The top and bottom layers would be designed with anti-slipping property in mind, while the middle structural layer would be the layer that absorbs the force of an impact [17] as shown in Fig. (1).
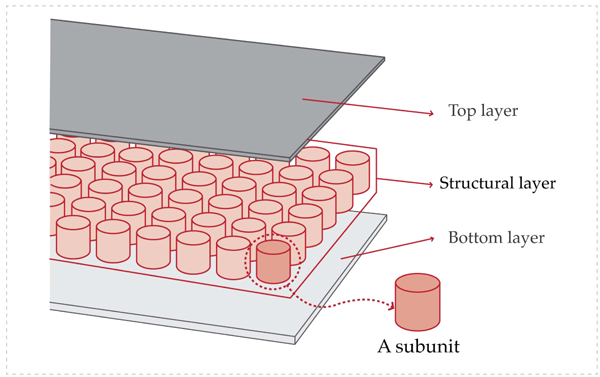
There have been several studies on impact attenuation of floor coverings. One of them is related to reducing health problem and fatigue from standing for a long time [20] which involved the investigation of various kinds of shock absorption mat [21]. Another study is on the cushioning effect on wounded soldiers of a floor mat system for military vehicles [22]. However, the mentioned study did not investigate the structural layer and the context of absorption of impact force from slipping and falling; therefore, its simulation results could not be used directly in our study. In the same vein, another paper suggests that information about the structural layer of shock absorption mats should be collected, specifically about subunits that are arranged in an even pattern [16]. A paper on a floor mat system for speed-boat transportation of patients [23, 24] did not report the dimensional proportion of the subunits and did not discuss the effects of their forms on attenuating the force of a fall. This study aimed to bridge this research gap.
2. THEORETICAL REVIEW
This study of the effects of form factors of shock absorption mat’s subunits on attenuation of force from elderly’s fall was based on the following:
2.1. The Mechanics of Human’s Falling Down on the Side of His or Her Body
This posture of a fall happens more frequently than other postures of a fall and the risk of broken hip from this kind of fall is 30 times higher than the risk of other kinds of injury from a fall [5]. Typically, a slip and fall are either to the front or the back of the falling person. It starts with a change in the normal posture of walking movement. In a typical fall, the elderly’s heel starts to move from behind the body, but as he or she slips, the muscles around the knee get stimulated and contracted hence the sole gets lifted off the floor and he or she starts to lose his or her balance as shown in Fig. (2) A study [5] reports detailed information about this kind of fall. It describes the average height of a typical elderly of 160 cm, the height from the floor to the hip of the elderly of 86 cm, the angle that his or her body makes with the floor as he or she starts to slip of 75 degrees, and the height from the floor to the center point of pelvic bones as he or she has fallen down to the ground of 10 cm. With these parameter values, the impact force from the fall on the hip was calculated to be ~4.050 Newton.meter/second [23, 25]. This magnitude of impact force from a typical scenario of slip and fall was taken to be a design criterion or control variable that was inputted into the ANSYS finite-element force simulation software. With another control variable and several independent variables, the software would yield predictions about the force experienced by the subunits of the structural layer and possible damage to the subunits of all of the devised models.
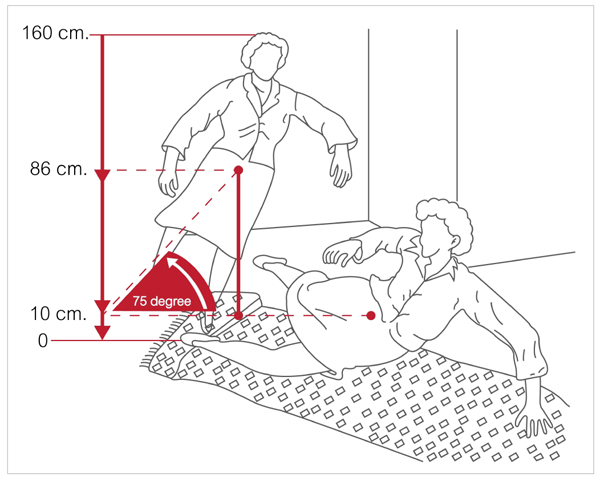
2.2. The Mechanical Engineering Principles Utilized
From the literature review of shock-absorption mat, it is typically composed of a top anti-slipping layer, an attaching bottom layer to the floor, and a middle structural layer. The structural layer is the layer that does the shock absorption. This layer consists of subunits evenly arranged into a honeycomb sandwich structure. This kind of subunit arrangement is very effective at shock absorption. The forms of these subunits can be cylindrical, triangular, or rectangular cubic which cushion the impact force transferred through the top layer. Besides the information about the form and arrangement of subunits, the mechanical properties of various subunits’ materials were also obtained from the literature review. The desired mechanical properties of the material for shock-absorption mat should include sufficient elasticity and durability; such material was selected according to the principles of material science which are a subset of mechanical engineering principles [26]; These properties were another control variable that would be inputted into the simulation software while the forms of cross-section and edges of subunits, their dimensional proportions, and their arrangement patterns were independent variables that were inputted into 3dsMax software to create their 3D models that were subsequently inputted into the ANSYS simulation software. The obtained simulation results were then analyzed and reported.
3. METHODOLOGY
From the mechanics of elderly’s fall and the mechanical engineering principles related to subunits, design criteria (control variables) and form factors (independent variables) were analyzed and synthesized as mentioned in the Section Theoretical review above. Then in phases 1 and 2 respectively, these variables were inputted as parameters into an ANSYS force simulation program. In phase 3, the simulation provided the magnitude of impact force that each kind of subunits with a different form factor was able to absorb without damage, hence showing the kinds of form factor that are suitable for construction of an effective shock-absorption mat. The phases in this study’s framework are shown in (Fig. 3).
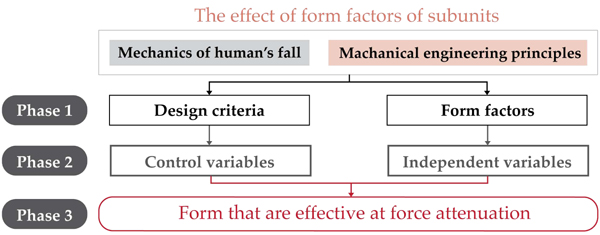
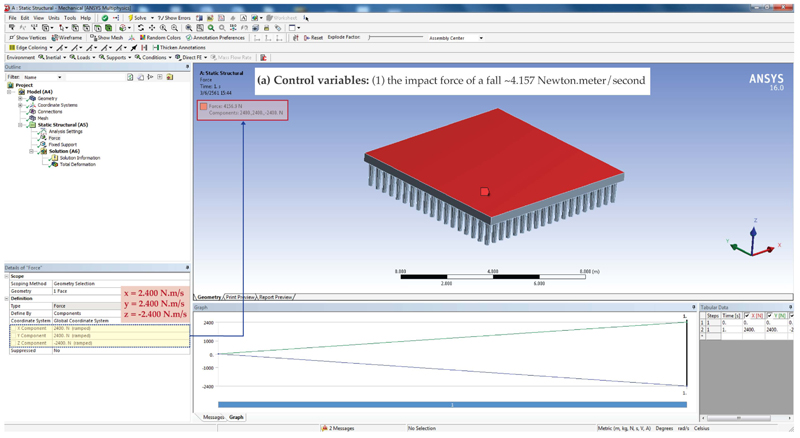
3.1. Phase 1
Selection of design criteria and form factors.
3.1.1. Purpose
1) To analyze and synthesize from reviewed papers the design criteria for subunits of the shock-absorption mat that would attenuate the impact force of human’s falling down on the side of his or her body and that took the physical properties of subunits’ material into account;
2) To analyze and synthesize possible form factors of subunits that affect the shock-absorbing capacity of a mat’s structural layer from reviewed papers (Table 1).
3.1.2. Method
The authors have reviewed the literature regarding floor mats for reducing fatigue from standing for a long time, shock-absorbing structural layer, and physical parameters of elderly’s slipping and falling on their hip and found valuable information in 7 articles [14, 16, 21, 25, 27-29]. From the review, the following design criteria and form factors that would be used in the simulation were formulated: (a) design criteria: 1) the fall was to one side of the body and the impact force of the fall was around ~4.050 N.m/s [23, 25, 30]; and 2) the mechanical properties of rubber as the chosen material for the mat among concrete, rubber foam, rubber, polyvinyl chloride, wood-plastic, and steel shown in (Table 1 and 2) form factors: Form of edges was chosen as an appropriate variable to use in our study because three of the articles mentioned above reported a wide range of impact forces that shock-absorption mats with different forms of edges in several nursing homes were able to withstand without damage. Similarly, the form of cross-section was chosen because a paper on shock absorption mats for various applications reported a wide range of impact forces that their subunits had to withstand [27, 31, 32]. The paper reported that shock absorption mats for the floor of a laboratory, an industrial factory, and a nursing home had different forms of a cross-section of subunits and were able to absorb the intended force without damage. Specific design criteria and form factors [14, 21] were also investigated in this study. All of these form factors are shown in Table 1.
No. | Side View | Perspective View | Design Criteria | Form Factors | Details | ||||
---|---|---|---|---|---|---|---|---|---|
Impact Force | Physical Properties of Rubber Material | Cross-Section | Edge | Arrangement Pattern of Subunits | Dimensional Proportion | ||||
L 01 |
![]() |
![]() |
= ~4.050 N.m/s | No data |
![]() |
![]() |
Cross-arrangement | Width 28 mm. Length 25 mm. Height 25 mm. Gbas 8 mm. |
This mat was used in a laboratory |
L 02 |
![]() |
![]() |
![]() |
![]() |
Table-arrangement | Width 28 mm. Length 25 mm. Height 25 mm. Gbas 5 mm. |
This mat was used in speed boat that carries emergency patients | ||
L 03 |
![]() |
![]() |
![]() |
![]() |
Table-arrangement | Width 28 mm. Length 25 mm. Height 25 mm. Gbas 8 mm. |
This mat were used in a laboratory, industrial factory, and airport | ||
L 04 |
![]() |
![]() |
![]() |
![]() |
Table-arrangement | Width 5 mm. Length 5 mm. Height 28 mm. Gbas 1 mm. |
This mat was used in nursing home | ||
L 05 |
![]() |
![]() |
![]() |
![]() |
Table-arrangement | Width 28 mm. Length 20.3 mm. Height 25 mm. Gbas 3 mm. |
This mat was used in military vehicles | ||
L 06 |
![]() |
![]() |
![]() |
![]() |
Line-arrangement | Width 28 mm. Length 20.3 mm. Height 25 mm. Gbas 3 mm. |
This mat was used in nursing home | ||
L 07 |
![]() |
![]() |
![]() |
![]() |
Line-arrangement | Width 28 mm. Length 20.3 mm. Height 25 mm. Gbas 3 mm. |
This mat was used in a car parking lot |
3.1.3. Results
The results of Phase 1 are described here. The selected design criteria were the followings: 1) impact force of a fall and 2) the physical property of rubber material. The selected form factors of subunits were the followings: 1) form of cross-section, 2) form of edges, (3) arrangement pattern of subunits, and 4) dimensional proportion of subunits of width x length x height x gap between adjacent subunits (gbas). Table 1 shows all of the form factors discussed in those articles along with summarized information about them that influenced our decision to choose particular form factors: side view, perspective view, design criteria, and form factors.
3.2. Phase 2
Formulation of control and independent variables.
3.2.1. Purpose
1) To obtain control variables for inputting into ANSYS engineering simulation software 16.0 gleaned from reviewed papers, design criteria would be encoded into simulation conditions. (Fig. 3).
2) To obtain independent variables that would be used to construct various models of shock absorption mat with 3ds Max software before they would be subsequently inputted into ANSYS.
3.2.2. Method
A finite element method for simulating impact force was used to simulate the action and reaction forces of a fall event on the mat; the method was packaged in the form of a software program called ANSYS; A simulation of a fall event is absolutely necessary because an actual experiment that has an elderly person intentionally make his or her body fall down is definitely not possible without any injuries; ANSYS is an established simulation software program that has been widely used in engineering and material science, hence it was most suitable for our objective.
From the literature review, an analysis and synthesis of control and independent variables needed to be inputted into ANSYS were performed. The variables involved were the following: (a)control variables: (1) the value of the impact force of a fall on the hip from a reliable paper [14] was entered in the ANSYS simulation software under the menu ‘static shortcut (A5)’ and submenu ‘impact force’ as x = 2.400, y =2.400, and z = -2.400 then the software displayed an impact force of ~4.157 N.m/s with a tolerance of not more than ± 0.1 N.m/s (Figs. 4 and 2) rubber material was chosen as the most suitable material for this purpose because it can absorb impact force and return to the original shape well [25]; the physical properties of the kind of rubber that would be used were determined in a laboratory and reported in [26]; these values were inputted into ANSYS under the menu ‘hyperelastic experimental data’, submenu ‘property of outline’, and input boxes called ‘biaxial test data’, ‘uniaxial test data’, and ‘shear test data’; under the submenu ‘coefficient name’, the ANSYS software then generated fitted curves of these data to be applied to the tested models (Fig. 6) independent variables: (1) form of cross-section, (2) form of edges, (3) arrangement pattern of subunit, and (4) dimensional proportion of subunits were inputted into 3ds Max software to construct a 3D model for each combination of the variables; the various resulting models were in .stl file format which could be inputted directly into ANSYS (Fig. 5).
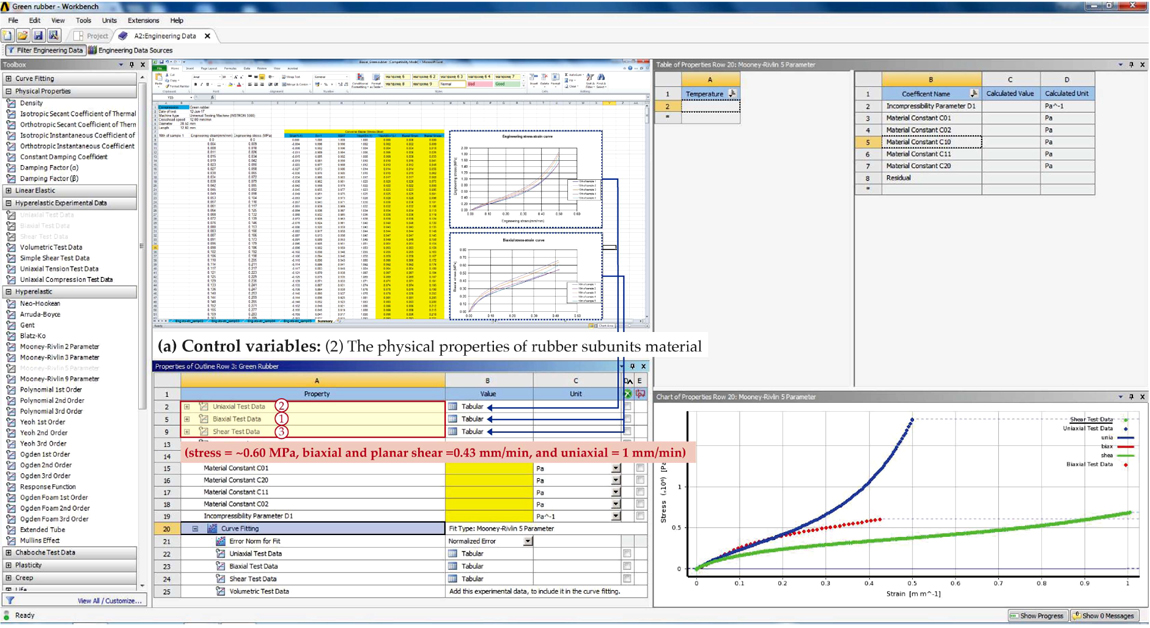
3.2.3. Results
The control variables obtained were the level of impact force of a fall on the side of the body of ~4.050 N.m/s or more and the actual physical properties of subunit’s rubber material (stress of ~0.60 MPa, axial and planar strains of 0.43 mm/min, and uniaxial strain of mixed rubber material of around 1 mm/min) [26]. The independent variables were the following: 1) form of cross-section: Square, circular, and triangular shape; 2) form of edges: Straight, rounded, spring-like, diamond, and trapezoidal shape; 3) arrangement pattern of subunits in the structural layer: Cross, table, and line arrangement; and 4) dimensional proportion of subunits: 28 mm x 25 mm x 25 mm x 5 mm of width x length x height x gap between adjacent subunits (gbas).
3.3. Phase 3
Simulation of form factors that affected force attenuation.
3.3.1. Purpose
To simulate the forces of a fall absorbed by various models of subunits with ANSYS engineering simulation 16.0 software. The simulated absorbed forces would show which kind of subunits are suitable for constructing a reliable shock absorption mat: the higher the force a type of subunits could absorb and withstand, the more suitable that type is for constructing a shock absorption mat.
3.3.2. Method
Seven subunit models were constructed from 3dsMax software, each with a combination of the synthesized independent variables: 1) pattern of arrangement of subunits in the structural layer, 2) form of cross-section, 3) form of edges, and 4) dimensional proportion of subunits. The constructed models were inputted into the ANSYS simulation software in combination with the design criteria which were the control variables: 1) impact force of a fall (~4.050 N.m/s or more) and 2) physical properties of the rubber material. The intended simulation outcomes were the force that each subunit and structural layer model was able to absorb without damage. The simulation software was run on a PC on Windows platform with an i5 CPU and 8 gigabytes of RAM. In this study, a different level of force that a type of subunits could withstand is represented by a different color-the lowest level is represented by red color and the highest is represented by blue as shown in the color scale in (Fig. 5).
3.2.3. Results
Fig. (7) shows a color-coded scale of force absorption capacity of an area in the simulation models depicted in Table 2. An area in the image of each model in this table has a color that indicates its force absorption capacity. An orange of a red color indicates that the area would collapse under an impact force of a fall. Adequate attenuation is color-coded as light-blue to light-green. It can be seen clearly from the results of the simulation in Table 2 that the subunits of models M 02 met our force-absorbing requirement: it was able to attenuate force of more than 4.050 N.m/s, shown as dark-blue to dark-green color in Fig. (5), and the structural layer of these models did not collapse. Three models failed to meet our requirement, M05, M06 and M07. Their force attenuating capacity is shown as yellow to red in Fig. (7). Their structural layers were damaged by the level of the force of a fall from slipping and would not be able to prevent hip injury in elderlies.
The model M 03 was able to withstand an amount of force but not as high as the set level of impact force at 4.050 N.m/s. Similarly, the models M 01 and M 04 were not able to attenuate it adequately, hence they would not help reduce the reaction force to the hip of a fallen body adequately.
No. | Control Variables | Side View | Perspective View | Independent Variables | Simulation View | Result (N.m/s) | ||||
---|---|---|---|---|---|---|---|---|---|---|
Impact Force | Physical Properties of Rubber Material | Cross-Section | Edge | Arrangement of Pattern of Subunits | Dimensional Proportion | |||||
M 01 | = ~4.050 N.m/s | Stress of = ~0.60 MP., Axial strains = 0.43 mm/min, Planar strains = 0.43 mm/min, and Uniaxial strain = 1 mm/min |
![]() |
![]() |
![]() |
![]() |
Cross-arrangement | Width 28 mm. Length 25 mm. Height 25 mm. Gbas 8 mm. |
![]() |
1.1190 |
M 02 |
![]() |
![]() |
![]() |
![]() |
Table-arrangement | Width 28 mm. Length 25 mm. Height 25 mm. Gbas 5 mm. |
![]() |
6.4900 | ||
M 03 |
![]() |
![]() |
![]() |
![]() |
Table-arrangement | Width 28 mm. Length 25 mm. Height 25 mm. Gbas 8 mm. |
![]() |
4.0262 | ||
M 04 |
![]() |
![]() |
![]() |
![]() |
Table-arrangement | Width 5 mm. Length 5 mm. Height 28 mm. Gbas 1 mm. |
![]() |
1.2391 | ||
M 05 |
![]() |
![]() |
![]() |
![]() |
Table-arrangement | Width 28 mm. Length 20.3 mm. Height 25 mm. Gbas 3 mm. |
![]() |
2.6003 | ||
M 06 |
![]() |
![]() |
![]() |
![]() |
Line-arrangement | Width 28 mm. Length 20.3 mm. Height 25 mm. Gbas 3 mm. |
![]() |
8.2280 | ||
M 07 |
![]() |
![]() |
![]() |
![]() |
Line-arrangement | Width 28 mm. Length 20.3 mm. Height 25 mm. Gbas 3 mm. |
![]() |
6.0476 |
From the results shown in Table 3 , it can be observed that several suitable form factors of subunits are following: 1) form of cross-section of subunits can be circular, 2) form of edges of subunits can be hourglass-like, 3) arrangement pattern of subunits can be table pattern, and 4) dimensional proportion of subunits can be 28 mm x 25 mm x 25 mm x 5 mm of width x length x height x gap between adjacent subunits (gbas).
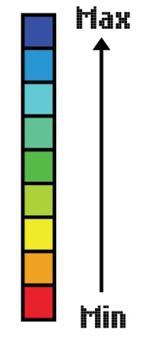
No. | Picture | Form Factor of Subunits | Details |
---|---|---|---|
(1) |
![]() |
Form of cross-sections | Circular shape |
(2) |
![]() |
Form of edges | Spring-like |
(3) |
![]() |
Arrangement pattern of subunits | Table-arrangement |
(4) |
![]() |
Dimensional proportion | Width 28 mm. Length 25 mm. Height 25 mm. Gap between adjacent subunits (Gbas) 5 mm. |
4. DISCUSSION AND CONCLUSION
Obtained from computer simulation were forces from elderly’s fall that were absorbed by various models of subunits. From these results, the following five points of observation were made. Firstly, subunits with circular cross-section forms were able to absorb more impact force from a fall than those with polygonal forms [23, 25] most likely because circular cross-section has a bigger area than polygonal cross-section of the same size [35]. Secondly, a form of edges of subunit in the form of hour-glass was able to absorb more impact force than those with straight edges which might be because the form resembles a spring suspension in a motorcycle or car. This result is consistent with the result of another study [36]. Thirdly, the table arrangement patterns of subunits were able to absorb a higher impact force than the cross and line arrangement patterns which is probably because in a table arrangement, subunits are more evenly arranged hence they are packed at a higher density than those in cross and line arrangements [37]. This result is in agreement with the result from a previous study [8]. Fourthly, the amount of impact force that subunits with different dimensional proportions were able to absorb were different; only a little difference in the dimensional proportion of subunits would cause a large effect on their capacity to absorb impact force. The relationship between the proportion and the force absorbed was similar to the relationship reported in [38]. Fifthly, M02 was indicated as the optimum design based partly on the assumption that the optimum height of a structural layer was 25 mm. This height was the height of layers in a mat that has been reported in the literature to be able to withstand the minimum impact force of a fall on the hip; from our results, all of the models with a shorter height collapsed to a higher or lesser degree as they experienced the specified simulated force, hence this 25 mm height would be at least the minimum height that could be optimal; however, we surmise that a slightly taller height may withstand even a higher force because the structural layer with such height would contain more shock-absorbing material, but too high a structural layer would contain too much material so that the mat would be too rigid to absorb an impact force readily. Lastly, it was observed that the size and number of subunits per unit area in the structural layer strongly affected the shock attenuation capacity of the mat which might be because they constrained the amount of shock-absorption material in a mat of a specific size and more material should be able to absorb more impact force. Therefore, the authors plan to investigate the density of subunits, i.e., the number of subunits per unit area, as an additional significant form factor in the next study.
To conclude, this study was an investigation of the effect of different forms of subunits of shock absorption mat on their shock attenuation capacity. A finite element method was used to estimate the force distributed in the structural layers of such mat under a plane strain condition. The investigated form factors were various forms of subunit’s cross-section and forms of its edges. Our main findings were that a circular cross-section and hourglass-like edges were the best at attenuating impact force. These main and other findings are useful for the design of a truly effective shock-absorption mat for alleviating the force of impact from elderly’s fall and other real-life, force-attenuation designs such as designs of the seat in an F1 race car or a space shuttle, of the sole of running shoes, and of a vibration-attenuation platform for industrial machinery.
CONSENT FOR PUBLICATION
Not applicable.
CONFLICT OF INTEREST
The authors declare no conflict of interest, financial or otherwise.
ACKNOWLEDGEMENTS
This research work was supported by the National of Research Council of Thailand (NRCT) as a scholarship for the first author’s doctoral study at the Multidisciplinary Design Research Program of the Faculty of Architecture at King Mongkut’s Institute of Technology Ladkrabang (KMITL).
Mr. Sedthawatt Sucharitpwatskul, Design and Engineering Research Unit, National Metal and Materials Technology Center (MTEC) analyzed the simulation data; Mr. Sira Meesaringkarn, Research Assistant from Rubber Technology Research Center (RTEC) contributed material analysis tools; Asst. Prof. Dr. Thitaphol Huyanan, Faculty of Engineering, Mechanical Engineering Department, Mahanakorn University of Technology (MUT), M.D. Piti Chalongviriyalert, Orthopedic Surgery, Ladkrabang Hospital, and Assoc. Prof. Dr. Manas Sangworasil, Faculty of Biomedical Engineering, Rangsit University (RSU) reviewed the final work in order to improve the outcome; Mr. Pratana Kangsadal revised the English.