All published articles of this journal are available on ScienceDirect.
Behavior of Structural Lightweight Polystyrene Foam Concrete Flat Slabs When Exposed to Fire
Abstract
Background:
Reinforced concrete flat slab is used in a wide range of applications. In addition, reduction of the weight of the concrete used increases the advantages of the flat slab.
Objective:
The main objective of this work is to study the performance of structurally reinforced foam concrete flat slab exposed to fire under eccentric and concentric loads.
Methods:
The experimental specimens included eleven tested square slabs with typical dimensions of 150 mm thickness and 1750 mm total length. The column cross section was 200 × 200 mm at the center of the slab. The density of the used lightweight polystyrene foam concrete was 1820 kg/m3. The crack patterns, load-deflection curves, steel strains, deflection during the fire, reduction in deflection during cooling by air, and residual deflection after fire and cooling were investigated.
Results:
The experimental results showed that the cracking load and maximum load of the tested slab with foam concrete were reduced compared to those of normal concrete.
Conclusion:
From the analysis of the results, it was found that the fire caused a reduction in the ultimate loads in the case of tested foam concrete slabs compared to that of normal-weight concrete slab. And also, the deformation of the tested foam concrete slab during the fire was increased comparing with normal-weight concrete slab. In a theoretical study, the modification factor for calculating the maximum allowable punching force was evaluated according to the ACI-318 and BS-8110 codes, and the reduction factors of compressive strength during the fire was done.
1. INTRODUCTION
Lightweight Concrete (LWC) has been used in construction since the eighteenth century. It is very important in decreasing the cost of Reinforced Concrete (RC) structures. The weight and type of coarse aggregate and the ratio between fine and coarse aggregate are the main parameters used to reduce the density of concrete (less than 1800 kg/m3) [1-4].
Foam with different forms is used in the construction field and can be used in the mixed material of concrete. Its application depends on its density [5, 6]. There are many studies on the used foam in reinforcement concrete structural element [7-15]. The use of foam to produce lightweight concrete in construction may become more widespread than traditional lightweight concrete because the manufacturing foam can be available in different countries.
M. Tech Scholar et al. 2014 [7] investigated two foam concrete mixtures produced with and without sand, and attempts have been made to select the proportions of foam concrete mix for the target plastic density of 1900 kg/m3. They concluded that the mixed proportion of foam concrete used in this research could not be used for structural purposes because the 28-day compressive strength of the foam concrete is less than 17.0 MPa. A.A. Hilal, N.H. et al. [8] presented an experimental study on the enhancement of pre-formed foam concrete with densities from 1300 to 1900 kg/m3 using two types of additives (silica fume and fly ash) together with a water reducer agent. The results showed that the additives improved the pore structure, increased the strength, reduced the water absorption, and slightly increased the thermal conductivity of foam concrete. Wan Ibrahim M. H et al. [9], investigated the effects of polyolefin fibers at a relatively low volume fraction (0.0%, 0.20%, 0.40%, and 0.60%) on the compressive and flexural properties of foam concrete with density ranging from 1300 to 1600 kg/m3. The test results showed that polyolefin fibers only slightly improved the compressive strength and flexural strength of the foam concrete by 4.3% and 9.3%, respectively.
Lee, Yee et al. (2017) [10] tested RC slabs and beams made of lightweight foamed mortar with density ranging from 1700 to 1800 kg/m3. The produced compressive strength was equal to 20 MPa. The results showed that reinforced lightweight foamed mortar beams caused a reduction in the maximum load from 8.0% to 34.0% compared with normal-weight RC with the same reinforcement configuration.
There are many works [16-18] that have studied the behavior of flat slabs exposed to fire; however, the behavior of polystyrene foam concrete exposed to fire has not been studied before. From the previous review, we found that, by using different additives and various fibers, the foam concrete can be successfully used in RC structures. The structural polystyrene foam concrete slabs can be used to replace hollow block slabs and thermally isolated layers.
The main task of this paper is to study the efficiency of structural lightweight polystyrene foam concrete flat slabs under different parameters when exposed to fire.
2. EXPERIMENTAL PROGRAM
2.1. Tested Specimens and Parameters
The experimental specimens included eleven tested RC square slabs with typical dimensions of 150 mm thickness and 1750 mm length. The clear span was equal to 1650 mm. The RC column is square with 200 mm in the case of the concentric load. In the case of an eccentric load, the column was extended above the slab compression face by 200 mm for all tested specimens. The typical concrete specimen's dimensions and reinforcement details are shown in Fig. (1).
The main parameters in this work are the effect of the percentage of tension steel reinforcement (0.40% and 0.70%) and type of vertical loads (concentric or eccentric) on the performance of flat slab when exposed to fire. Five specimens with normal-weight concrete and six specimens with polystyrene foam concrete slab were tested.
The eleven tested specimens were divided into four groups, as follows. The first group comprised three specimens, which were used to study the effect of load types and the main steel ratios on the behavior of normal-weight concrete. The second group, with two specimens, examined the effect of fire on the behavior of normal-weight concrete. The slabs were first loaded upto 30% of the ultimate load from the control test slabs as service existing load for slab in building. At this load, the slabs were exposed to fire to reach 500 °C for one hour. Then, the loading of the slabs was continued up to the ultimate load after cooling by air. The third group contained three specimens, and considered the effect of the load type and main steel ratios on the behavior of lightweight concrete. Finally, the effect of fire on the behavior of lightweight concrete was presented in the fourth group, as summarized in Table 1.
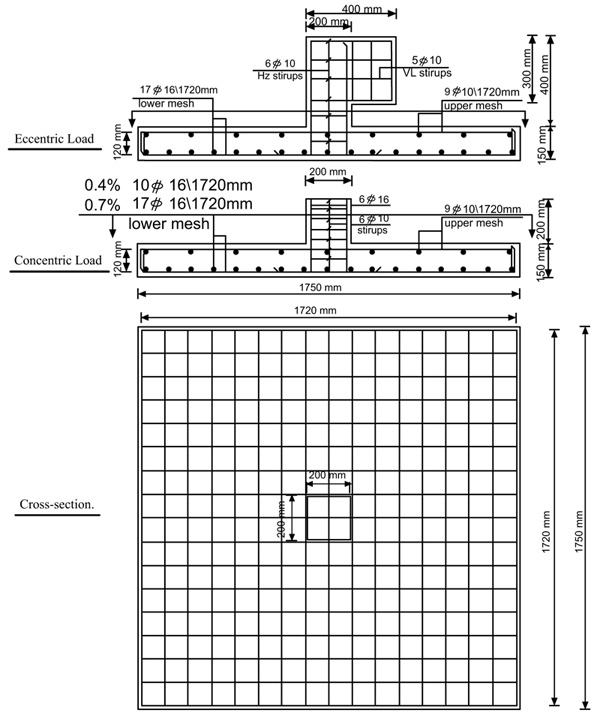
Group | Specimens | Specimens Code | Parameters | Results | |||||||
---|---|---|---|---|---|---|---|---|---|---|---|
Type of Concrete | Heating Temp (°C). |
Eccentricity(e\t) | Flexure Reinforcement Ratio% | Cracking Load (kN) |
Ultimate Load (kN) |
Maximum Deflection (mm) | EA** (kN·mm) |
Fcu MPa | |||
G1 | S1 | NACH | N | Non | No | 0.70% | 115 | 462 | 13.92 | 3307 | 31.0 |
S2 | NAEH | N | Non | 0.5 | 0.70% | 109 | 382 | 12.3 | 2241 | 31.0 | |
S5 | NACU | N | Non | No | 0.40% | 71 | 383 | 19.85 | 3450 | 31.0 | |
G2 | S3 | NFCH | N | 500 | No | 0.70% | --- | 444 | 15.15 | 2718 | 31.0 |
S4 | NFEH | N | 500 | 0.5 | 0.70% | --- | 298.7 | 15 | 1630 | 31.0 | |
G3 | S6 | LACH | L | Non | No | 0.70% | 107 | 430 | 17.72 | 3554 | 30.0 |
S7 | LAEH | L | Non | 0.5 | 0.70% | 87.2 | 367 | 11.4 | 2034 | 30.0 | |
S11 | LACU | L | Non | No | 0.40% | 82 | 343 | 15.5 | 2736 | 30.0 | |
G4 | S8 | LFCH | L | 500° | No | 0.70% | --- | 332 | 19.75 | 2575 | 30.0 |
S9 | LFEH | L | 500° | 0.5 | 0.70% | --- | 238 | 14.33 | 1712 | 30.0 | |
S10 | LFCU | L | 500° | No | 0.40% | --- | 278 | 15.9 | 2134 | 30.0 |
2.2. Material Properties
All the tested specimens were made from local materials. The polystyrene foam is a type of plastic produced from styrene. It is a lightweight, rigid cellular foam that was used in the concrete mix. Polystyrene foam has excellent resistance to moisture and is impervious to rot, mildew, and corrosion, as shown in Fig. (2), and silica fume was added to the mix. In order to achieve the workability of lightweight concrete, superplasticizer was used.
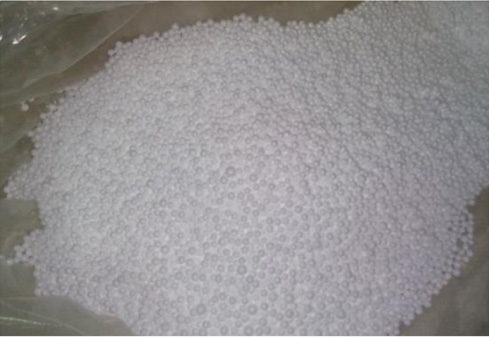
Moreover, the used polypropylene MasterFiber®012(BASF product) is 19 mm long. The tensile strength and modulus of elasticity were 350 MPa and 1000 MPa, respectively. The polypropylene fiber restricts the formation of small cracks during plastic shrinkage and premature drying in order to provide hardened cementitious material.
In order to achieve lightweight concrete with bulk density of 1820 kg/m3, more than thirty trial mixes were made. Polystyrene foam, silica fume, and superplasticizer were added to the mix, which consisted of natural sand as gravel with a maximum size of 10 mm. The LWC and NWC mixes are summarized in Table 2. Six concrete cubes with dimensions of 150 × 150 × 150 mm and two cylinders with 150-mm diameter and 300-mm length were cast from each batch. Table 3 summarizes the compressive strength for each batch.
Concrete Type | W (L) |
C (kg) |
S (kg) |
G (kg) |
Polystyrene Foam |
Silica Fume (kg) |
Superplasticizer (L) |
Polypropylene Fiber (kg) |
|
---|---|---|---|---|---|---|---|---|---|
(L) | (kg) | ||||||||
LWC | 135 | 500 | 630 | 630 | 400 | 3.2 | 40 | 20 | 0.9 |
NWC | 180 | 400 | 500 | 1000 | - | - | - | - |
Concrete Type | Mix No. | 28-day Average Compressive Strength (MPa) | Target Compressive Strength (MPa) | Average of Bulk Density (kN/m3) |
---|---|---|---|---|
LWC | 1 | 32 | 30 | 18.2 |
2 | 31 | |||
3 | 34 | |||
4 | 29 | |||
NWC | 5 | 30 | 31 | 25 |
6 | 32 |
The compressive strength of normal-weight and lightweight foam concrete is approximately 30 MPa, and the yield strength of the used steel bars, according to the manufacturer, was equal to 360 MPa.
2.3. Preparation of Specimens
Wood forms were used to cast all tested slabs simultaneously, as shown in Fig. (3). The strains of the main RFT mesh were then placed in their position in the forms. Before casting the concrete, the forms were wetted with water to ease the release of the slabs from the forms to prevent absorption of the forms.
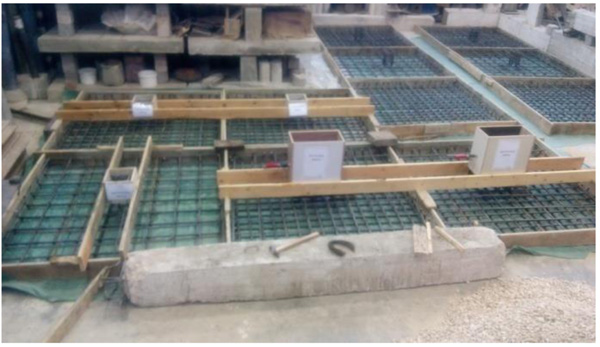
Mixing was accomplished by a concrete tilting drum mixer with a maximum capacity of 0.125 m3. In the first mixture, sand, dolomite, cement, silica fume and polypropylene fiber were dry mixed for approximately one minute until a homogenous color was observed. Then, the polystyrene foam and water were gradually added while mixing was continued for two minutes. The concrete was cast immediately after mixing.
2.4. Test Setup and Instrumentation
All tested specimens were supported in a special setup for testing during firing and loading, as shown in Fig. (4). The setup consisted of a steel frame formed of I-beams resting on four steel columns to support the beams during firing and loading. The span of the tested beams between supports was 1650 mm.
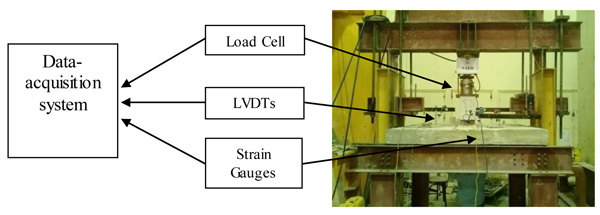
The special furnace consisted of two lines of gas pipes, as shown in Fig. (5), with 7 flame nozzles or each line. A wired digital temperature reader was connected to a thermal sensor by a thermal cable. The thermostat was used to adjust the temperature of the specimen, which was connected to the furnace and the digital temperature reader. A load cell was provided between the tested slab and a hydraulic jack to accurately measure the applied load up to failure.
The digital load cell with a capacity of 2000 kN was used to measure the applied loads. The values of the applied loads were recorded from the monitor connected to the load cell. Five vertical LVDTs of 0.001-mm sensitivity were placed below the specimens at five different locations to record the specimens’ vertical deflections. Two HPM electrical strain gauges were used to measure the strain of the main steel bars at the mid-span. A computer-controlled data-acquisition system was used to collect the measurement data at fixed intervals.
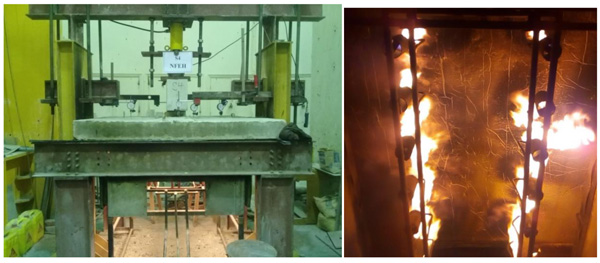
3. TEST RESULTS AND ANALYSIS
3.1. Crack Patterns and Modes of Failure
The crack patterns of the tested specimens are shown in Fig. (6). In general, for normal-weight concrete, with the increase in the percentage of steel reinforcement, the number of cracks increased and the failure changed from flexural failure to punching failure as the flexural cracks decreased and punching cracks became more obvious.
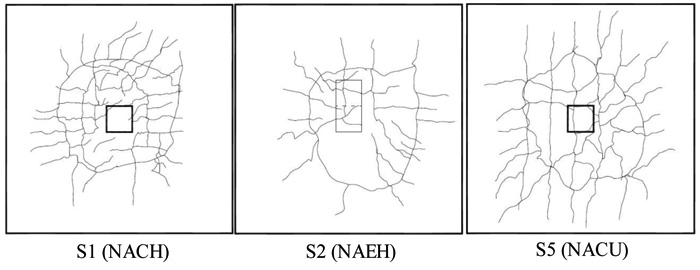
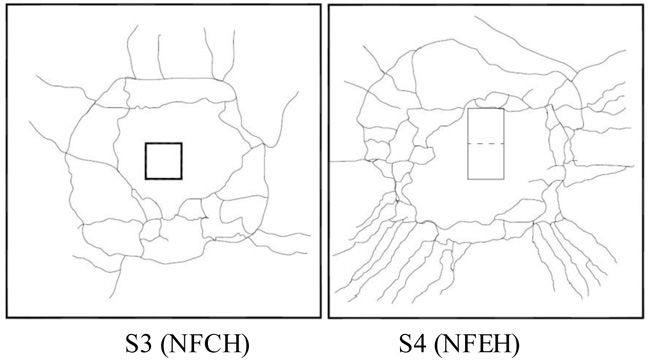
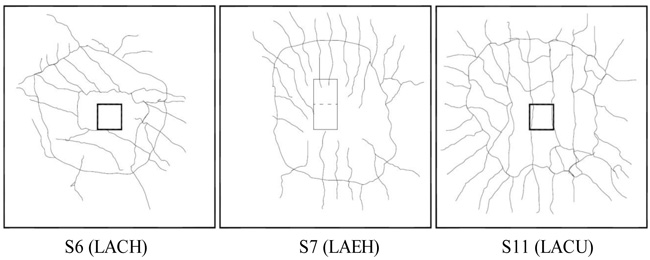
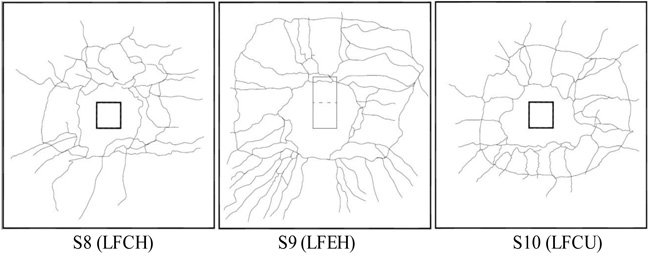
For normal-weight concrete, by comparing the cracks patterns in groups one and two, as shown in Figs. (6a and b), the number of cracks decreased with increasing crack width due to fire exposure. In contrast, for lightweight foam concrete, as shown in Fig. (6c and d), the number of cracks increased when the test specimens were exposed to fire. In addition, for lightweight polystyrene foam concrete, the flexural cracks do not reach to the columns; they stopped at the perimeter of the punching cracks. Based on this, we concluded that the resistance of the RC flat slab decreased due to the existing polystyrene foam. As shown in Table 1, the cracking load decreased in lightweight concrete compared to that of normal-weight concrete. From the previous results, we found that the polystyrene foam concrete may cause a decrease in the tensile strength and bond between concrete and steel due to the existing polystyrene foam, even though polypropylene fibers were used for enhancement of the cracking control of tested slabs.
3.2. Comparison of Load–Deflection Curve of Lightweight and Normal-Weight RC Flat Slabs under Different Parameters
In the case of a concentric load, with a steel ratio equal to 0.40% and 0.70, the maximum loads decreased by approximately 10.4% and 6.9% for lightweight polystyrene foam concrete and normal-weight concrete, respectively. From the load-deflection curves, as shown in Fig. (7a), in the case of the concentric load with a steel ratio of 0.7%, a slight decrease in the initial stiffness and flexural stiffness occurred, as well as a slight increase in ductility (the total area under the load-deflection curve). In the case of an eccentric load, as shown in Fig. (7b), with a steel ratio equal to 0.7%, the behavior of structural lightweight polystyrene foam concrete is approximately the same as that of the normal-weight concrete.
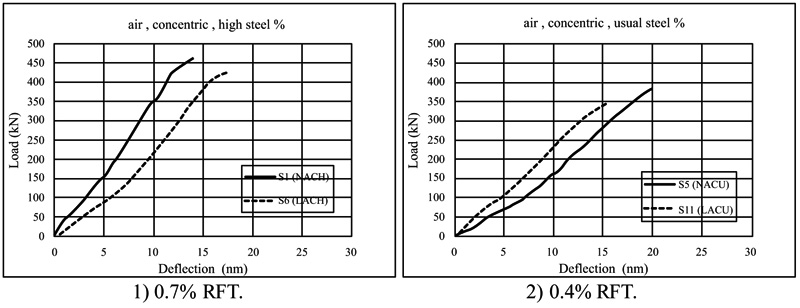
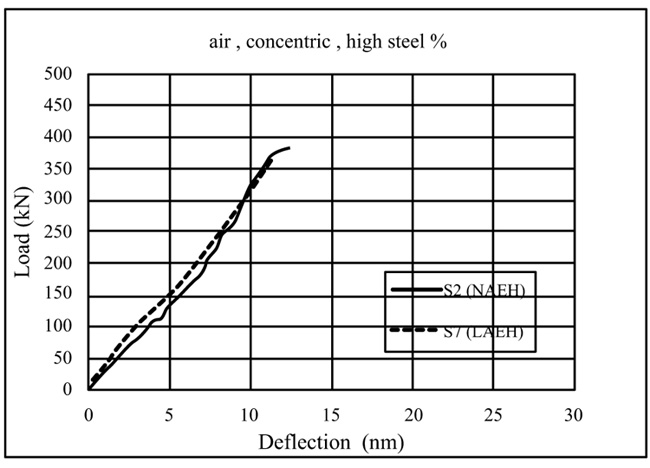
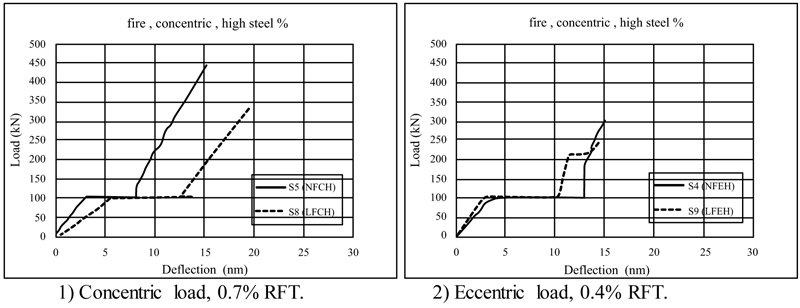
When normal-weight and lightweight polystyrene foam concrete slab were exposed to fire, as shown in Fig. (7c), more reduction in the ultimate load occurred in the lightweight than in normal-weight concrete. In the case of concentric loading, with a steel ratio of 0.70%, the maximum load of lightweight polystyrene foam concrete decreased by approximately 25.2% from the normal-weight concrete exposed to fire. Moreover, in the case of an eccentric load, the maximum load of lightweight polystyrene foam concrete decreased by approximately 20.3% from that of the normal-weight concrete. From this, we concluded that the lightweight polystyrene foam concrete slab is more strongly affected by fire than normal-weight concrete.
3.3. Comparison of Lightweight and Normal-Weight RC Flat Slabs in Fire
During the firing process (exposure to fire and cooling), three deflection values are recorded. The first value Δ1 is the increase in deflection under constant load during the fire exposure. The second value Δ2 is the reduction in the deflection during cooling by air. Finally, Δr is the residual deflection after fire and cooling. The relation between the deflection and time during the firing process is shown in Fig. (8).
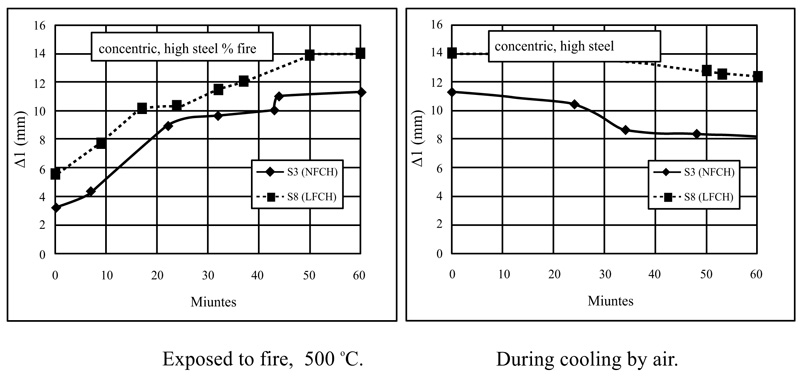
Comparison of the change in the deflection during firing and cooling for lightweight and normal-weight RC flat slabs.
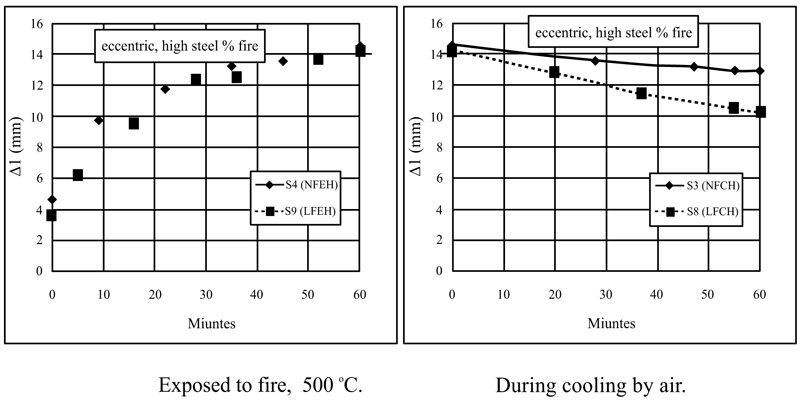
Comparison of the change in the deflection during firing and cooling for lightweight and normal-weight RC flat slabs.
For a concentric load, as shown in Fig. (8a) and Table 4, with a steel ratio equal to 0.7%, the deflection Δ1 of the structural lightweight polystyrene foam concrete increased by approximately 3.70% compared to normal-weight concrete. The deflection value Δ2 of the structural lightweight polystyrene foam concrete decreased by 50% compared to normal-weight concrete. The residual deflection of structural lightweight polystyrene foam concrete increased by approximately 38.7% from that of normal-weight concrete.
Condition | Type of Load | RFT% | Specimen | Δ1 | % | Δ2 | % | Δr | % |
---|---|---|---|---|---|---|---|---|---|
Fire | Concentric | High% | S3 (NFCH) | 8.1 | 3.7 | 3.2 | - 50 |
4.9 | 38.7 |
S8 (LFCH) | 8.4 | 1.6 | 6.8 | ||||||
Eccentric | High% | S4 (NFEH) | 9.9 | 7.1 | 1.6 | 143 | 8.3 | -19.3 | |
S9 (LFEH) | 10.6 | 3.9 | 6.7 |
For a concentric load, as shown in Fig. (8b) and Table 4, with a steel ratio equal to 0.7%, the deflection Δ1 of the structural lightweight polystyrene foam concrete increased by approximately 7.10% compared to normal-weight concrete. The deflection value Δ2 of the structural lightweight polystyrene foam concrete increased by 143% compared to normal-weight concrete. The residual deflection of structural lightweight polystyrene foam concrete decreased by approximately 13.7% from that of normal-weight concrete.
From this, we concluded that the stiffness of structural lightweight polystyrene foam concrete decreased and the remaining deformation after fire is be more than that in normal-weight concrete, depending on the ratio of the main steel reinforcement. Analysis of the deformation of the lightweight foam concrete slab shows that the increase in the void and decrease in the weight are the most important parameters.
4. THEORETICAL STUDY
In this section, the experimental and theoretical results using ACI-318 and BS-8110 are compared to evaluate the proposal modification factors in polystyrene foam concrete. Finally, the proposed equation considering the effect of foam concrete is developed.
4.1. Evaluation the Experimental Results According to Different Codes
By comparing the experimental results and analytical maximum forces due to punching for slabs without shear reinforcement calculated by ACI-318 [19] and BS-8110 [20] and codes, equations (1) and (2) are as follows.
![]() |
(1) |
![]() |
(2) |
where
f'c: Concrete cylinder compressive strength in MPa = (0.8 fcu) for cube strength.
λ: Modification factor, equal to 0.75 for lightweight concrete and unity for normal-weight concrete.
ϕ : Modification factor, equal to 0.80 for lightweight concrete and unity for normal-weight concrete.
![]() |
(3) |
![]() |
(4) |
For slabs loaded by an eccentric vertical load without shear reinforcement, the capacities are calculated according to equations (3) for (4) for ACI-318 and BS-8110, respectively.
Table 5 shows the comparison of the experimental and analytical values of the tested slab by ACI-318 and BS-8110 values. The ratio between the experimental an analytical results in the normal and foam concrete shows that the ratios decreased in lightweight foam concrete and increased when exposed to fire. From this, we concluded that correlation factors greater than unity are required for the modification factor of foam concrete. Moreover, the reduction factor of compressive strength during fire must be less than unity for the tested specimens.
Group | Specimens | Specimens Code | Type of Concrete | Heating Temp (°C). |
Eccentricity(e\t) | Flexure Reinforcement Ratio% |
Ultimate Load (PTest) (kN) |
PACI-318 (kN) | PBS8110 (kN) | PTest / PACI-318 | PTest / PBS-8110 |
---|---|---|---|---|---|---|---|---|---|---|---|
G1 | S1 | NACH | N | Non | No | 0.70% | 462 | 279.5 | 316.5 | 1.65 | 1.46 |
S2 | NAEH | N | Non | 0.5 | 0.70% | 382 | 157.2 | 237.0 | 2.43 | 1.61 | |
S5 | NACU | N | Non | No | 0.40% | 383 | 279.5 | 251.2 | 1.37 | 1.52 | |
G2 | S3 | NFCH | N | 500° | No | 0.70% | 444 | 253.1 | 281.0 | 1.75 | 1.58 |
S4 | NFEH | N | 500° | 0.5 | 0.70% | 298.7 | 142.4 | 210.4 | 2.1 | 1.42 | |
G3 | S6 | LACH | L | Non | No | 0.70% | 430 | 209.6 | 253.2 | 2.05 | 1.7 |
S7 | LAEH | L | Non | 0.5 | 0.70% | 367 | 117.9 | 189.6 | 3.11 | 1.94 | |
S11 | LACU | L | Non | No | 0.40% | 343 | 209.6 | 200.9 | 1.64 | 1.71 | |
G4 | S8 | LFCH | L | 500° | No | 0.70% | 332 | 204.3 | 253.2 | 1.63 | 1.31 |
S9 | LFEH | L | 500° | 0.5 | 0.70% | 238 | 114.9 | 189.6 | 2.07 | 1.26 | |
S10 | LFCU | L | 500° | No | 0.40% | 278 | 204.3 | 200.9 | 1.36 | 1.38 |
4.2. Correction Factors Required for the Lightweight Foam Concrete: Evaluation of the Experimental Results According to Different Codes
Table 6 shows the ratio between (Ptest/Ptheor) for normal concrete and (Ptest/Ptheor) for lightweight foam concrete. From this, we find that the correction factors are 1.24 for ACI-318 codes and 1.16 for BS-8110.
Condition | Type of Load | RFT% | Specimens | PTest (kN) | PACI318 (kN) | PTest / PACI-318 | Correction Factor | PBS8110 (kN) | PTest / PBS-8110 | Correction Factor |
---|---|---|---|---|---|---|---|---|---|---|
No-fire | Concentric | High% | S1(NACH) | 462 | 279.5 | 1.65 | 1.242 | 316.5 | 1.46 | 1.164 |
S6(LACH) | 430 | 209.6 | 2.05 | 253.2 | 1.7 | |||||
Low% | S5(NACU) | 383 | 279.5 | 1.37 | 1.197 | 251.2 | 1.52 | 1.125 | ||
S11(LACU) | 343 | 209.6 | 1.64 | 200.9 | 1.71 | |||||
Eccentric | High% | S2(NAEH) | 382 | 157.2 | 2.43 | 1.28 | 237 | 1.61 | 1.2 | |
S7(LAEH) | 367 | 117.9 | 3.11 | 189.6 | 1.94 |
For ACI-318, the modification factor (λ) can be equal to 0.93 = (0.75 × 1.24) for foam concrete. In addition, for BS-8110, the modification factor (ϕ) equal to 0.93 = (0.80 × 1.163) for lightweight concrete and unity for normal-weight concrete
4.3. Proposed Reduction Factors for Concrete Compressive Strength Due to Fire
In this part, reduction factors of concrete compressive strength in foam concrete depending on the reduction factors in normal concrete strength are proposed. The ratio between (Ptest/Ptheor) for normal concrete to (Ptest/Ptheor) for lightweight foam concrete in Table 7 demonstrate that the reduction factors of concrete strength in normal-weight concrete during firing at 500 °C could be decreased by approximately 17%.
Condition | Type of Load | Specimens | PTest (kN) | PACI318 (kN) | PTest / PACI-318 | Correction Factor | PBS8110 (kN) | PTest / PBS-8110 | Correction Factor |
---|---|---|---|---|---|---|---|---|---|
LWC factor | Concentric | S3 (NFCH) | 444 | 253.1 | 1.75 | 0.931 | 281 | 1.58 | 0.829 |
S8 (LFCH) | 332 | 204.3 | 1.63 | 253.2 | 1.31 | ||||
Eccentric | S4 (NFEH) | 298.7 | 142.4 | 2.1 | 0.986 | 210.4 | 1.42 | 0.887 | |
S9 (LFEH) | 238 | 114.9 | 2.07 | 189.6 | 1.26 | ||||
Proposal factor | Concentric | S3 (NFCH) | 444 | 253.1 | 1.75 | 0.81 | 281 | 1.58 | 0.81 |
S8 (LFCH) | 332 | 235.4 | 1.41 | 261.3 | 1.27 | ||||
Eccentric | S4 (NFEH) | 298.7 | 142.4 | 2.1 | 0.85 | 210.4 | 1.42 | 0.85 | |
S9 (LFEH) | 238 | 132.4 | 1.79 | 195.67 | 1.22 |
The reduction factors in concrete compressive strength exposed to 500 °C fire, as shown in Table 8, can be changed from 0.82 and 0.7, according to ACI318 and BS8110 codes in normal weight-concrete, respectively, to 0.68 = [0.82 × 0.83] and 0.58 = [0.7 × 0.83] in foam concrete.
Reduction Factor | NWC | LWC | Proposal factor For Foam Concrete |
|||
---|---|---|---|---|---|---|
ACI-318 | BS-8110 | ACI-318 | BS-8110 | ACI-318 | BS-8110 | |
Compressive strength of concrete | 0.82 | 0.7 | 0.95 | 1.0 | 0.68 | 0.58 |
Yield strength of reinforcement steel | 0.6 | 0.6 | 0.6 | 0.6 | 0.6 | 0.6 |
CONCLUSION
By studying the behavior of structural lightweight foam concrete flat slabs when exposed to fire, we found that:
- In the tested specimens, by using the fibers and admixtures, the density of structural lightweight-foam concrete reached 1820 kg/m3, and the concrete compressive strength reached 30.0 MPa.
- By comparing the performance of structural lightweight polystyrene foam concrete flat slabs and normal-weight concrete flat slabs, we find that:
- The ultimate load decreased in the foam concrete flat slab by approximately 7.0% for concentric load and 4% for eccentric load compared with those of normal-weight concrete.
- The number of cracks decreased and the crack width increased in foam concrete.
- When calculating the theoretical punching shear force in ACI-318 and BS-8110 codes, the proposed modification factors of foam concrete can be equal to 1.24 and 1.163, respectively.
- By comparing the behavior of the structural lightweight polystyrene foam concrete flat slab and normal-weight concrete flat slab exposed to fire, we find that:
- The ultimate load decreased by 25% in polystyrene foam concrete and decreased by 13% in normal-weight concrete under the same conditions.
- The recommended reduction factors in compressive strength according to ACI-318 and BS-8110 codes are 0.68 and 0.56 instead to 0.82 and 0.70, respectively.
- Further experimental and theoretical studies are required for the application of structural foam concrete in the construction field.
CONSENT FOR PUBLICATION
Not applicable.
CONFLICT OF INTEREST
The authors declare no conflict of interest, financial or otherwise.
ACKNOWLEDGEMENTS
Declared none.