All published articles of this journal are available on ScienceDirect.
Improving Water Resistance of Compressed Earth Blocks Enhanced with Different Natural Fibres
Abstract
Background:
Studies have shown a great potential for the use of Compressed Earth Blocks (CEBs) as a sustainable building material due to its economic, environmental and social benefits.
Objective:
This study investigates the water resistance characteristics of CEBs reinforced with different natural fibres.
Methods:
The fibres were sourced from coconut husk, sugarcane bagasse and oil palm fruit at 1 wt% added to two soil samples. The CEB specimen size of 290 × 140 × 100 mm was made at a constant pressure of 10 MPa and dried in the sun for 21 days. Accelerated erosion test was conducted to determine the resistance of the specimen to continuous rainfall condition.
Results:
It was discovered that the fibres helped in reducing the erodibility rate of the blocks, though there were some degrees of damage. The difference between the water resistance of the unreinforced and fibre reinforced CEBs were found to be statistically significant. Furthermore, the surface of the fibre reinforced blocks eroded rapidly in depth than the internal part, and there was reduction in the depth difference of the erosion with increase time of water spraying on the specimens.
Conclusion:
The study concludes that though the addition of fibres in soil blocks does not completely prevent the block from erosion, the impact of the fibres on the blocks significantly reduces the erosion.
1. INTRODUCTION
Compressed Earth Blocks (CEBs) are building units made of damp soil and compacted at a high pressure for constructing walls of earthen structures. They are sometimes stabilized with: (1) binders such as cement and lime, and (2) fibres (natural and artificial) to improve their performance properties. This is necessitated by the weakness of the blocks when subjected to greater load and rain/water. The later has a devastating effect on the blocks especially in high rainfall areas, and the strength problem also limits the number of storeys used in buildings.
The benefits of the use of CEBs for earthen structures such as affordability, environmentally friendly, easy to work with and availability has generated a renewed interest over the past decade [1-4]. Recent studies have investigated the properties of various units used for earthen structures [5-11]. Their findings have shown a great potential for the use of CEBs as a sustainable building material. Most studies focused on the physico-mechanical properties of the blocks without considering the durability properties.
Measuring the durability properties of CEBs is important because blocks may easily erode under water (rainfall) and also the particles wear off under abrasion [5, 17]. Durability of CEBs is usually measured by the use of erosion and wearing tests. The main erosion tests available are (1) drip test, and (2) water spray test. A study by Heathcote [17] identified and developed three types of drip test and eight types of water spray test. The wearing test is normally conducted using wetting and drying (wire brush) method which is described in details by American Society for Testing and Materials ASTM D559-03 [20].
Danso [12] identified that there are limited studies on the durability properties of CEBs though one of the critical problems of earthen structures is erosion. Eires, et al. [11] studied the water resistance of earthen buildings enhanced with binders. They tested the water resistance properties of earth blocks enhanced with lime and oil. There is the also the need to study the water resistance properties of earth blocks reinforced with fibres. This study therefore investigates the water resistance properties of CEBs reinforced with natural fibres. To achieve this, the study determined the failure mode of the fibre reinforced blocks, the depth of erosion and the depth difference of erosion of the fibre reinforced blocks.
2. MATERIALS AND METHODS
2.1. Soil
Two soil samples were used for the experimental work, they are (1) Red soil and (2) Brown soil which were obtained from Ghana. These soil types have different properties and characteristics and therefore were appropriate to determine if soil type has an effect on the erosion properties of soil blocks for constructing houses. The general properties of the soils are shown in Table 1.
Soil Type | Grain Sizes (%) | Atterberg Limits (%) | Compaction | ||||||
---|---|---|---|---|---|---|---|---|---|
Gravel (>2 mm) | Sand (2 - 0.063 mm) | Silt (0.063 - 0.002 mm) | Clay (<0.002 mm) | wL | wP | PI | OMC (%) | MDD (Mg/m3) | |
Red | 15 | 39 | 16 | 30 | 51.2 | 27.3 | 23.9 | 19 | 1.79 |
Brown | 12 | 46 | 28 | 14 | 13.3 | 17.2 | 13.9 | 18 | 1.78 |
2.2. Fibres
Reinforcement of the compressed earth blocks was achieved by using three types of fibres from (1) coconut husk, (2) sugarcane bagasse and (3) oil palm fruit fibres. The coconut fibres were obtained from the husk of coconut fruit from coconut vending points. Sugarcane Bagasse fibres were obtained from sugarcane residue at a local sugarcane alcohol distillery mill. The palm oil fibres were also obtained from a palm oil extraction plant in Ghana. These were by-products from agricultural products, they were soaked in water for two days, mechanically beaten, the fibres extracted manually and dried in the sun. The lengths of the fibres used are 125, 80 and 38 mm, respectively for coconut, bagasse and oil palm fibres. These fibre lengths were used as a result of the lengths that produced optimum strength in the previous study by Danso, et al. [6]. Photos of the fibres can be found in previous studies [7, 21].
2.3. Specimen Preparation
The compressed earth blocks size of 290 × 140 × 100 mm were made with soil and 1 wt.% fibre content as recommended by previous study [7]. The soil was first measured and spread on a platform. The fibres were measured and spread on the soil and mixed together until a uniform mixture was obtained. The quantity of water used was equal to the optimum moisture content of 19 and 18% for red soil and brown soil, respectively, and was sprinkled on the soil-fibre mixture and mixed together to obtain a homogenous mixture. The fibres were soaked in water for 2 days to saturation before being added to the mix. The blocks were made with BREPAC block making machine with a constant pressure of 10 MPa [13]. The blocks were then dried in the sun (Fig. 1) at an average temperature of 27 °C and relative humidity of 72% for 21 days. To ensure uniform drying, the blocks were turned each day. After drying, the blocks were packed and the surfaces cleaned with soft duster before testing.
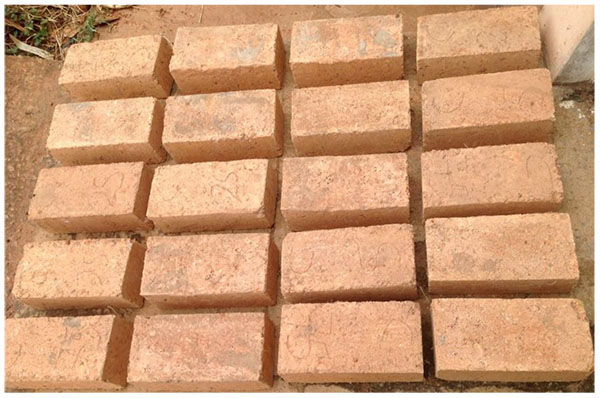
2.4. Testing of Blocks
A pressure spray test (accelerated erosion test) was conducted to determine the resistance of the specimen to continuous rainfall condition. This method was used instead of drip (Geelong) method because it is more representative of the field conditions, such as rainfall that causes erosion to earthen structures. The test is an empirical one developed by Commonwealth, Scientific and Industrial Research Organisation (CSIRO) according to Australian Standard [14] to simulate rain action. The purpose of performing this test was to determine the ability of the blocks to resist erosion which may be caused by continuous rainfall.
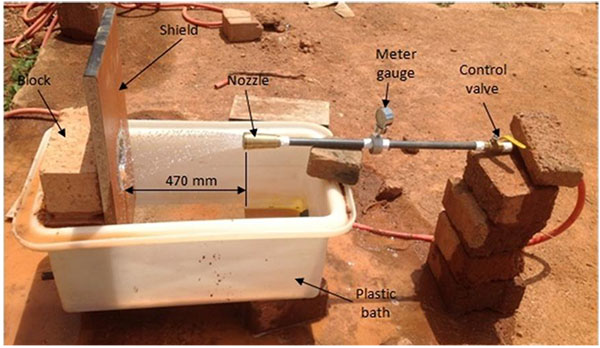
The test was conducted in accordance with Section D of New Zealand Standard [15]. The test rig (Fig. 2) was set up with shield board positioned in the plastic bath and the pressure spray nozzle set on the bath at a distance of 470 mm from the shield. Each block was mounted behind a thin shield and was exposed to spray through a 100 mm diameter hole. The shield ensured that only limited area of the block face was subjected to water spray. Tap water was connected to the pressure spray nozzle and then opened at pressure 50 kPa through the nozzle onto the block. The water was sprayed onto the block exposed surface and run out through the outlet of the plastic bath. The spray was interrupted at every 15 min to allow for assessment for a total of 60 min. The depth of erosion was measured using a 10 mm diameter flat ended rod. Three blocks (replicates) were used for each test.
2.5. Statistical Analysis
Correlations were carried-out to establish relationships between unreinforced compressed earth blocks and fibre reinforced compressed earth blocks. Paired t-test (Two-tailed p-value) with SigmaPlot Version 13.0 were used to test for significant difference between the mean values of unreinforced block specimens and fibre reinforced block specimens, after conducting Shapiro-Wilk normality test.
3. RESULTS AND DISCUSSION
3.1. Failure Mode
Fig. (3) shows the failure mode of unreinforced compressed earth blocks (Brown specimen). The front surface that had direct contact with the spraying water created a bigger indent which narrowed through the block thickness and appeared smaller at the back of the block. This is expected as the front (in the normal sense the outer surface of the wall) surface always has direct contact with water/rainfall, and therefore is prone to excessive damage. The Brown block specimens could not resist the erosion for the entire 60 min water spraying. All the five specimens tested failed between 54 to 58 min. However, the Red specimens survived the 60 min water spray test but eroded deeply from between 81 to 86 mm for the three specimens tested. This result suggests that unreinforced compressed earth blocks have poor resistance to erosion, hence the need for stabilization to improve its durability property.
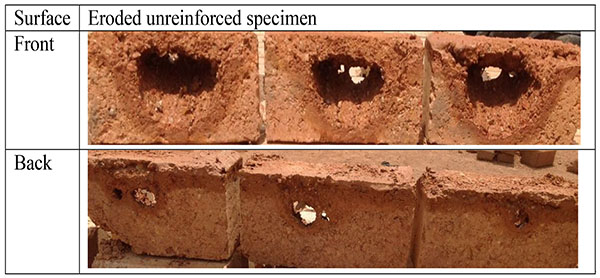
As can be seen in Fig. (4), the compressed earth block specimens that were reinforced with natural fibres improved the blocks resistance to the water spray. For all the specimen tested, the water failed to penetrate through the blocks. The inclusion of the fibres in the blocks helped in reducing the erodability rate of the blocks, though there were some degrees of damage. This means the addition of fibres in soil blocks does not completely prevent the block from erosion but reduces the impact of the erosion on the blocks. Similar result in the study by Balila, et al. [16] shows that all the specimens for the unstabilized Sudanese bricks were completely eroded in less than 60 min, while bovine stabilized specimen recorded a decreased erosion rate. Another study by Eires, et al. [11] indicated that the untreated soil recorded the highest erosion as compared to lime, oil and cement stabilized soil specimens. According to Heathcote [17], the measurements carried out indicate a discharge of 29.6 l/min for the test which yields a total volume of water in the 60 min to approximately 85 years rainfall in Sydney, Australia. This indicates that the degree of damage observed in Figs. (3 and 4) is a simulated result of a continuous erosion of the blocks over eight decades when the block surface is exposed to rainfall.
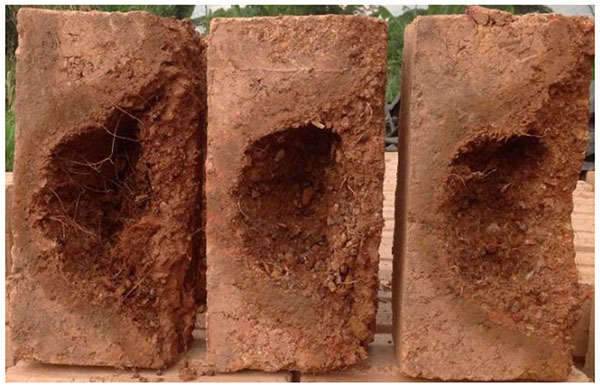
The mean values of unreinforced and fibre reinforced compressed earth blocks were subjected to paired t-test to determine whether there is statistically significant difference between the unreinforced and fibre reinforced with p-value at ≤ 0.05. according to the t-test, all treatments differed from each other, with the highest p-value of 0.042. This indicates that there is a statistically significant difference between the mean values of erosion depth of the unreinforced and fibre reinforced compressed earth blocks. This means that the inclusion of fibres in the compressed earth block is significant in improving the erosion resistance of the blocks.
3.2. Depth of Erosion
The trend of the erosion of the reinforced soil block specimens is shown in Fig. (5) for both red and brown soils. As clearly seen, the erosion of the blocks increased with increase time of water spraying on the specimens for all the two soil types and the fibre types. In both soil types, the bagasse fibre reinforced compressed earth blocks recorded the highest erosion while the coconut reinforced compressed earth blocks obtained the lowest. The erosion depth for the red soil specimens is between 15.2 to 43.2 mm, while for brown soil it is between 15.2 to 75.4 mm all within 60 min. This implies that red soil samples performed better in the erosion resistance than the brown soil. The result could be attributed to the higher plasticity index and the smaller particle sizes of the red soil samples as shown in Table (1). A study by Danso, et al. [13] suggests that soil with higher plasticity index usually perform better than those with lower plasticity index. This is because the smaller soil particles are able to bond together and improve their plasticity, thereby improving their bond properties which resist the ease of water peculating through and wash the individual particle away.
As the erosion measurements were taken at intervals by which the test was interrupted, that is between 1-15, 16-30, 31-45 and 46-60 min. This categorized the depth difference into four quartiles (1st, 2nd, 3rd and 4th). This then places the depth of erosion in quartiles, the 1st quartile (1-15 min) recorded the highest erosion depth for all the soil and fibre types. The 2nd to 4th quartiles (16-30 to 46-60 min) were on the average half each of that of the 1st quartile. This depicts that the surface of the blocks erodes more rapidly than the internal part. This is because when the erosion starts on the surface of the blocks, there are few fibre encounters, as the erosion moves internally a number of fibres are encountered which cluster together and therefore protect the particles of the soil from been washed away. The behavior of the fibres protecting the soil from been washed away is similar to tree roots protecting earth from erosion [18, 19].
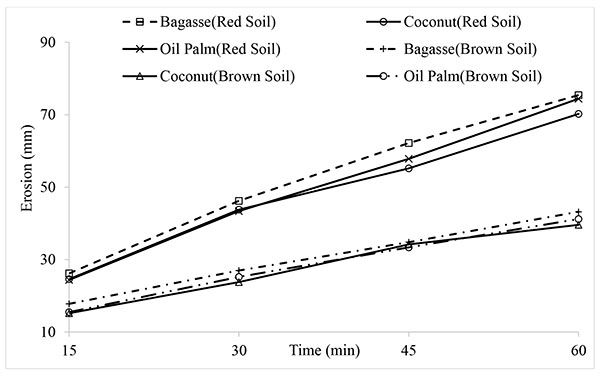
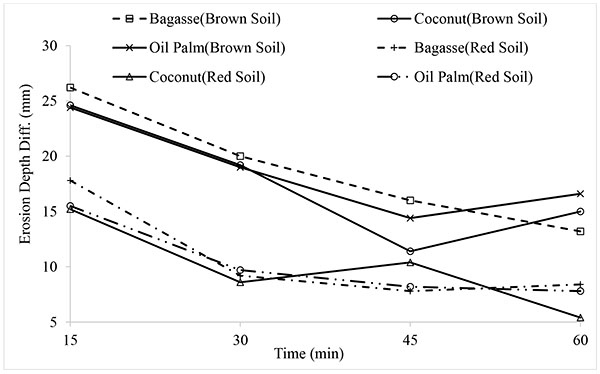
3.3. Depth Difference of Erosion
Depth difference is the difference in erosion recorded between the intervals by which the test was interrupted for taken the measurement, that is the four quartiles (1st, 2nd, 3rd and 4th). The 1st quartile is from the beginning to fifteen (15) minutes of the test, the 2nd quartile is from the sixteen (16) to the thirty (30) minutes, 3rd quartile is from the thirty-first (31) to the forty-fifth (45) minutes, and the 4th quartile is from forty-sixth (46) to sixtieth (60) minutes of the test. The difference in depth of erosion of the fibre reinforced compressed earth blocks are presented in Fig. (6) for both red soil and brown soil specimens. It can be observed that for both soil types and fibre types there is reduction in the depth difference with increase time of water spraying on the specimens. The reduction in erosion depths recorded from 1st quartile to 2nd quartile is between 51.7 – 62.6% and 76.3 – 78.1% for red soil and brown soil samples, respectively for all the fibre types. Between the 2nd and 3rd quartiles are 43.8 – 68.4% and 46.3 – 61.1%, respectively for red soil and brown soil, and between the 3rd and 4th quartiles are 35.5 – 50.3% and 49.6 – 68% for red and brown soil samples, respectively. The result shows that for both soil samples, there was continuous reduction from the 1st to the 4th quartiles. This means that the amount of erosion in the compressed earth blocks kept reducing through the period of testing, implying that the rate at which the erosion occurred at the beginning, slowed down quartile way to the end. This means from the outer surface of the blocks, there was a speedy erosion, but as the water reaches the internal of the blocks, the rate of erosion reduces. This can be linked to the accumulation of the fibres within the block, shielding and protecting the soil particles from been easily wash away [12]. It can also be observed that the depth of erosion reduction for red soil was less than brown soil, implying that the red soil blocks have better resistance to erosion.
4. SUMMARY AND CONCLUSION
This study investigated the water resistance properties of CEBs reinforced with natural fibres. From the results obtained, the following concluding summary can be drawn:
- The unreinforced block specimens (Brown) could not resist the erosion for the entire 60 min water spraying, suggesting that the raw earthen structures have poor resistance to erosion. However, the fibres helped in reducing the erodibility rate of the blocks, though there were some degrees of damage to the fibre reinforced blocks. This means that the addition of fibres in soil blocks does not completely prevent the block from erosion but reduces the impact of the erosion on the blocks.
- The difference between the water resistance of the unreinforced and fibre reinforced compressed earth blocks were found to be statistically significant. This means that the inclusion of fibres in the compressed earth block is significant in improving the erosion resistance of the blocks.
- The surface of the fibre reinforced blocks eroded rapidly in depth than the internal part. This is because when the erosion starts on the surface of the blocks, there are few fibres encountered, but as the erosion moves internally, a number of fibres are encountered which cluster together and therefore protect the particles of the soil from being washed away.
- There was a reduction in the depth difference of the erosion with increased time of water spraying on the specimens. This means that the amount of erosion occurs in the compressed earth blocks reducing through the period of testing, implying that the rate at which the erosion occurred at the beginning, slowed down the quartile-way to the end.
The paper therefore concludes that though the addition of fibres in soil blocks does not completely prevent the block from erosion, the impact of the fibres on the blocks significantly reduces the erosion. In addition, the effect of fibres inclusion in the blocks is greatly felt at the internal of the blocks than on the surface.
CONSENT FOR PUBLICATION
Not applicable.
CONFLICT OF INTEREST
The author declares no conflict of interest, financial or otherwise.
ACKNOWLEDGEMENTS
Declared none.