All published articles of this journal are available on ScienceDirect.
Potential Utilization of Spent Coffee Waste in Permeable Concrete
Abstract
Introduction
Concrete is widely used in the construction industry. A vast array of applications of concrete popularized permeable concrete due to its ability for sustainable climate resilient cities. In 2015, 17 Sustainable Development Goals were introduced by the United Nations. Among the 17 goals, goal 12: Responsible Consumption and Production, aimed at reducing reliance on natural resources to combat climate change, biodiversity loss, and pollution. Cement, being the most important material to cast permeable concrete, depletes natural resources while polluting the environment. Recent studies have utilized waste materials as permeable concrete materials to promote sustainable construction. With the increased consumption of coffee annually, this research investigates the use of Spent Coffee (SC) as partial cement replacement by weight in permeable concrete to reduce the environmental impact of cement production. This paper presents the chemical properties of SC wastes produced under different drying conditions through X-ray Fluorescence (XRF). Compressive strength and percolation rate of permeable concrete containing SC wastes as cement replacement at 0%, 1%, 3%, 5%, and 10% by weight are investigated at water-cement ratios of 0.3, 0.35, and 0.4. From the study, SC wastes are found possible to replace 1% by weight of cement with an optimum mix design of 0.35 w/c ratio.
Aims
Permeable concretes are becoming increasingly used in the construction industry for the construction of climate-resilient cities. These concrete with permeable properties allow for use in open-air areas to improve percolation into the ground. However, casting requires the use of cement. Cement is one of the most destructive materials on earth. It is estimated that one pound of cement produces 0.93 pounds of carbon emissions, making up 7% of the world’s carbon emissions. To reduce this impact, coffee is aimed at reducing the use of cement in the permeable concrete mix. Spent coffee waste, is a waste that tends to be discarded as general waste into landfills. Nevertheless, studies on the use of spent coffee wastes as cement replacement in permeable concrete are scarce. Other than that, the effect of the different processing methods on the properties of spent coffee wastes was also not fully investigated. Hence, this study aims to identify the most optimum processing methods of spent coffee wastes to study its potential use as cementitious materials in permeable concrete to fill in this gap of knowledge and propose a lesser cement future.
Background
Permeable concretes are popularized for their ability in the construction of climate-resilient cities. With the increased coffee consumption annually, this research investigated the use of spent coffee as partial cement replacement in permeable concrete to reduce the environmental impact of cement production, aligned with achieving the United Nations Sustainable Development Goals.
Objective
The objective of this study is to first identify the potential of the spent coffee (SC) wastes as cement replacement. Then, to identify the best proportion of SC wastes as cement replacement by weight and the suitable water-cement (w/c) ratio for the permeable concrete mixes.
Methods
First, SC wastes are processed with 4 different processes and examined through X-ray fluorescence analysis. SC permeable concretes are being casted at varying percentages and w/c ratio. A compressive strength test is then conducted. The percolation rate of the samples is obtained according to the falling head permeability test in the ACI 522R-10 report.
Results
SC wastes were found to have the potential to be used as cement replacement. The findings revealed that SC at 1% by weight of cement replacement with a w/c ratio of 0.35, the permeable concrete demonstrated strength improvements with acceptable permeability properties compared to conventional mixes.
Conclusion
From the study, it is concluded that SC wastes are possible to be used as cement replacement. The mechanical strength of the permeable concrete benefited from the incorporation of SC wastes while presenting acceptable permeability properties.
1. INTRODUCTION
Permeable concrete, also known as pervious concrete or no-fines concrete, is concrete cast through the use of cement and water as binders with the use of coarse aggregates and little to no fine aggregates [1]. These concretes, though presenting lowered density and strength, are porous, allowing water to permeate easily through the internal structure of the concrete [2]. This makes permeable concrete becoming increasingly used in the construction industry as it allows paved surfaces the ability for rainwater to percolate easily into the soil underneath [3]. However, the lowered strength of permeable concrete resulted in the need for altered mix design, such as the use of waste materials as cement replacement [4].
Today, there have been numerous studies that have been conducted on the use of various wastes as cement replacements to improve permeable concrete properties [5]. Other than being able to improve the typical concrete properties, the use of wastes can also promote sustainable production aligned with the United Nations Sustainable Development Goals [6]. From the 17 goals, goal 12: Responsible Consumption and Production was aimed at reducing reliance on natural resources to combat climate change, biodiversity loss and pollution. Cement, being the most important material to cast permeable concrete, depletes natural resources while polluting the environment [7]. To promote sustainable construction, research studies have used waste materials generated from human activities as permeable concrete materials.
While there are many studies conducted concerning the use of spent coffee wastes in concrete, there have been limited works conducted on using spent coffee wastes being applied to the permeable concrete mix [8]. Therefore, this research looks to fill in the gap by studying the application of spent coffee wastes into the permeable concrete mix.
Previous studies have also investigated the use of spent coffee wastes into the concrete, the methods used involved the use of oven drying at 50°C - 60°C [9, 10]. Through this process, the spent coffee presented a high potassium oxide composition, making it less effective when used as concrete materials [11]. With that, alternative methods of processing the spent coffee wastes were required to be studied. Reviewing some previous studies investigating the use of sugarcane bagasse ash processed at different temperatures, it was found that the chemical composition greatly differs at different process temperatures [12]. Another study by Lerna et al. [13] investigating PET wastes found that different treatment methods of the PET waste result in different properties of the material, ultimately influencing the concrete formed, reporting decreased strength using PET wastes with chemical treatment method but increasing strength when using PET wastes undergoing mechanical treatment method. Eggshell powder is one of the examples of possessing the required chemical composition to be used as a cement replacement when dried through the use of sun drying methods [14]. With that, spent coffee wastes in this study were investigated through the drying of the wastes under sun-dried methods and oven-dried methods at different temperatures. The chemical composition of the dried waste is then investigated through the use of X-ray fluorescence.
Understanding the chemical composition of the spent coffee wastes, the study proceeds to identify the effect of the permeable concrete containing the spent coffee wastes at varying percentages of 0%, 1%, 3%, 5%, and 10%. To identify the most optimum mix design for permeable concrete containing spent coffee wastes, the relationship between the proportions of cement replaced with spent coffee wastes in the permeable concrete mix and the optimum water-cement (w/c) ratio is then investigated through 3 different w/c ratios of 0.3, 0.35 and 0.40 as w/c ratio may affect the strength and properties of the concrete produced [15]. According to the ACI 522R-10 report, typical permeable concrete should have a w/c ratio of a maximum of 0.40 [16]. The study investigated a range of 0.3 to 0.4 w/c ratio, as it has been reported that a lower w/c ratio can increase the density of the concrete form, allowing for an increase in strength. Hence, the range of values 0.3, 0.35, and 0.40 w/c ratio are selected to be studied.
A compressive strength test was conducted to evaluate the mechanical performance of permeable concrete at varying w/c ratios and percentages of spent coffee wastes as cement replacement [17]. The test was conducted at 7 days, 14 days, and 28 days of water curing. For each percentage of spent coffee replacing cement by weight and each of the w/c ratios at each curing period, a total of 3 sample cubes were cast, totaling 135 permeable concrete specimens prepared for compressive strength test. This is to ensure the repeatability and accuracy of the data obtained from the compressive strength test.
Concrete strength is usually associated closely with the density of the concrete internal structure. It is often hypothesized that increasing the air content of a concrete sample may lead to deteriorating strength performance [18]. Though this remained true in many cases, Coviello et al. [19] reported that at the expense of PET wastes in self-leveling underlayment screed, the material produced illustrated positive strength increment while increasing air content, allowing for lightening of the structural element. Thus, the percolation rate performance of the permeable concrete becomes a crucial aspect to be investigated. This could help identify if the spent coffee wastes have the potential to increase the permeability of the concrete while increasing the strength performance simultaneously.
According to the standards set by the ACI 522R-10 report, another 30 permeable concrete samples from different percentages of replacement and w/c ratio were also prepared for the percolation rate test to gauge the percolation rate performance of the permeable concrete. Hence, the objective of this study is formed that is to first identify the suitable methods of processing spent coffee waste. Secondly, to identify the mechanical performance of the permeable concrete containing spent coffee waste at different percentages of cement by weight replacement and water-cement ratio. Third, the percolation rate performance of the permeable concrete at the varying percentages of cement replacement and water-cement ratio.
2. MATERIALS AND METHODS
2.1. Introduction
In terms of the experimental program carried out, can be generally separated into two different phases. The first phase is to identify the most suitable methods of drying the spent coffee waste. The second phase is to understand the performance of permeable concrete containing spent coffee waste and identify the most optimum proportions of materials in the permeable concrete. The following chapter discusses the methods involved in the study, from the preparation of materials to data collection.
2.2. Materials and Preparation Methods
This study focuses on the use of spent coffee wastes as partial cement replacement. The main materials involved include coarse aggregates, cement, spent coffee wastes as partial cement, and water to cast the permeable concrete mix. Cement is then studied to replace by weight with spent coffee wastes at 0%, 1%, 3%, 5%, and 10%, whereas the w/c ratio to be studied are 0.30, 0.35, and 0.40. The following sub-section discusses the preparations involved in all the materials used in the study.
2.2.1. Cement
For this study, the cement used is Ordinary Portland Cement (OPC) supplied by YTL Corporation Berhad. The cement used is kept away from moisture and stored in a cool and dry place.
2.2.2. Spent Coffee Wastes
Spent coffee wastes used in this study were sourced from Malaysian coffee shops. The spent coffee wastes were collected and washed to clean off impurities. Once washed, the spent coffee wastes are then dried through 4 different methods. The first method is sun-drying the spent coffee wastes for 2 weeks until fully dried. The other methods involved the use of oven drying at 3 different temperatures of 100°C for 1 day (24 hours), 120°C for 2 hours, and 130°C for 2 hours. This is to identify the effect of the drying process on the properties of the spent coffee wastes. With the 4 different drying methods of spent coffee wastes, the spent coffee wastes are then ground into fine sizes through the use of the LA-abrasion machine. The grinding process uses a total of 4500 cycles to fine grind the 4 different dried spent coffee wastes into fine sizes [20]. To ensure that the spent coffee wastes are finely grounded, a sieve pan of size 200 microns passing is then used to ensure that all spent coffee wastes fulfill the fineness to be used as a cement replacement. The finely grounded and sieved spent coffee wastes of 4 different drying processes are then sent for an X-ray fluorescence test to identify the chemical composition of the spent coffee wastes. The spent coffee waste processing method that produces the highest calcium oxide (CaO) composition is then selected to be used as partial cement replacement.
2.2.3. Water
Potable tap water is used for this study. To investigate the effects of the w/c ratio on the performance of permeable concrete through varying percentages of spent coffee wastes as cement replacement, water is calculated and prepared according to 3 different w/c ratios, which are 0.30, 0.35, and 0.40. Water will also be used for curing the permeable concrete specimens as per the BS EN 12390-2 standards [21]. The casted samples are soaked into a polyethylene round-type water tank for the water curing process. The water tank is placed under a shade, away from direct sunlight, to keep the water in the water tank temperature around 25°C±5°C. The water tank used is shown in Fig. (1).
2.2.4. Coarse Aggregates
The coarse aggregates used in this study are gravels. According to the ACI 522R-10 report, the sizes of the coarse aggregates to be used in permeable concrete casting must be within 9.5mm to 19mm while avoiding flaky or elongated particles [16]. Hence, aggregate selection and sieving were conducted to ensure that coarse aggregates are fit to the standards as set. The sizes of the coarse aggregates are crucial as they determine the permeability properties of the permeable concrete.
2.3. Permeable Concrete Mix Design
All the proportions of the test materials prepared and studied are listed in Table 1. The proportions of the mix design vary according to the w/c ratio and the percentage of cement replaced with spent coffee wastes.
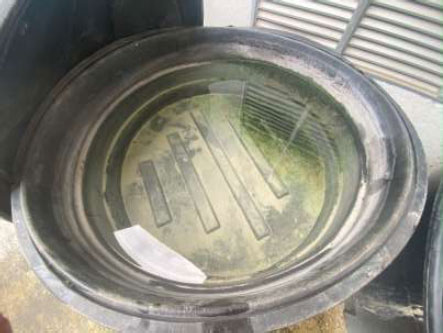
- | w/c ratio | Coarse Aggregate (kg/m3) | Water (kg/m3) | Cement (kg/m3) | Spent Coffee (kg/m3) |
---|---|---|---|---|---|
0% | 0.30 | 1750 | 210 | 700 | 0 |
1% | 1750 | 210 | 693 | 7 | |
3% | 1750 | 210 | 679 | 21 | |
5% | 1750 | 210 | 665 | 35 | |
10% | 1750 | 210 | 630 | 70 | |
0% | 0.35 | 1750 | 245 | 700 | 0 |
1% | 1750 | 245 | 693 | 7 | |
3% | 1750 | 245 | 679 | 21 | |
5% | 1750 | 245 | 665 | 35 | |
10% | 1750 | 245 | 630 | 70 | |
0% | 0.40 | 1750 | 280 | 700 | 0 |
1% | 1750 | 280 | 693 | 7 | |
3% | 1750 | 280 | 679 | 21 | |
5% | 1750 | 280 | 665 | 35 | |
10% | 1750 | 280 | 630 | 70 |
2.4. Test Equipment and Procedures
The following sub-section discusses the test equipment and procedures involved in the study.
2.4.1. Los Angeles Abrasion Machine
Los Angeles abrasion machine (LA machine) is the equipment used to grind the spent coffee wastes into fine sizes. A total of 21 metal balls were used in crushing the spent coffee wastes with a crushing cycle of 4500 cycles to grind the sizes of the spent coffee wastes into fine powder form [20]. The same procedures were used for all 4 different drying processed spent coffee wastes. Upon collection of crushed samples from the LA machine, the powdered spent coffee wastes were sieved through the use of a 200-micron sieve and packeted into resealable bags to be sent for an X-ray fluorescence test.
2.4.2. X-ray Fluorescence (XRF) Test
The X-ray fluorescence (XRF) test involved the use of XRF spectroscopy. The XRF spectrometer used is a Rigaku / ZSX Primus II test machine, as shown in Fig. (2). The spent coffee wastes that have been dried through all 4 different processes were packed in separate resealable bags. The spent coffee wastes were then tested to identify their chemical composition. XRF analyses the oxide composition of the spent coffee wastes, and from there, a selection was conducted to select the spent coffee with the highest CaO content to be used as cement replacement.
2.4.3. Compressive Strength Test
After selecting the chemical composition of spent coffee wastes with the highest CaO content to identify its effectiveness in permeable concrete, permeable concrete cube samples of (100 mm x 100 mm x 100 mm) on each side were cast according to the BS EN 12390-1 standards [22]. A concrete mixer is used to cast the permeable concrete samples. In the beginning, the aggregates, binder, and spent coffee wastes were first added into the concrete mixer and dry-mixed for 1 minute until it was mixed homogeneously. Once all materials were mixed well, water portions were then added into the concrete mixer at 2 batches with each batch having a mixing time of 1 minute. Once the materials are homogenous and a gel-like liquid is observed, the concrete mix is then poured into the cube molds.
The water-cement ratios adopted in this study are 0.30, 0.35 and 0.40. Cement was replaced by weight with spent coffee wastes at 0%, 1%, 3%, 5% and 10%. The casted cubes were then sent for a compressive strength test following the BS EN 12390-3 standards [23]. The compressive strength test machine used for the study is the MATEST 2000kN Compression Testing Machine, as shown in Fig. (3). Initially, when the permeable concrete is still fresh, after being cast into the cube molds, the permeable concrete is allowed to set and harden for 24 hours before being soaked into water. The permeable concrete samples were kept on a metal shelf away from moisture and heat to avoid excessive water and water loss to heat. After 24 hours of setting time, the permeable concrete is molded with the use of a pressurized air gun. The permeable concrete was then allowed for water curing, and the compressive strength test took place during 7 days, 14 days, and 28 days of water curing. For each of the w/c ratios and different percentages at each curing period, 3 samples were prepared and tested to obtain the mean compressive strength to reduce error. For that, a total of 135 permeable concrete samples were prepared for the compressive strength test.
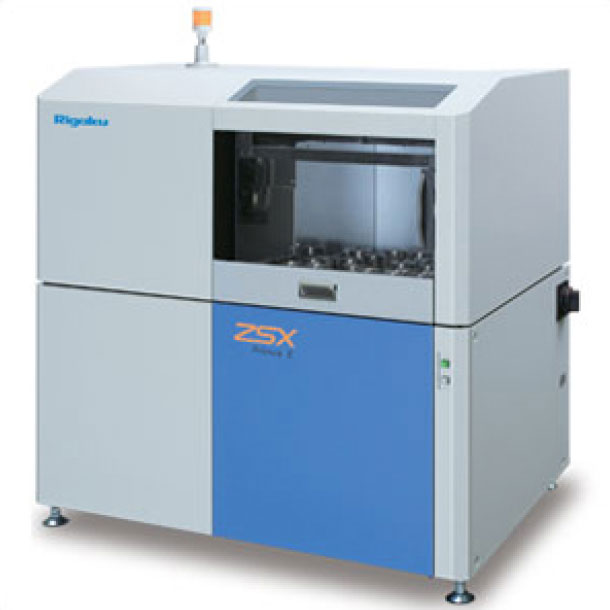
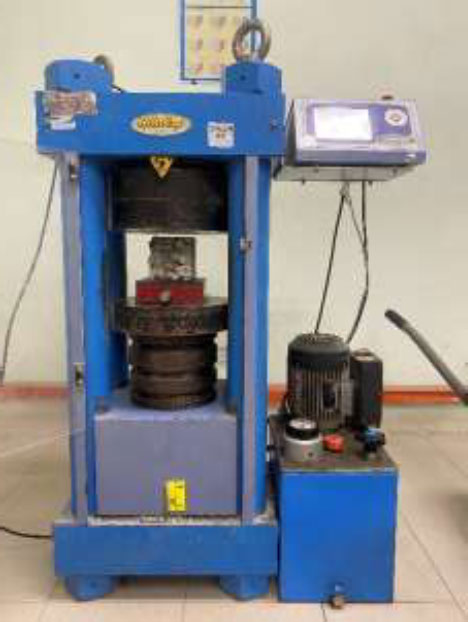
2.4.4. Percolation Rate Test
Besides studying for the mechanical performance, the test for the percolation rate performance of all the permeable concrete samples was also conducted to identify the permeability performance of the permeable concrete containing spent coffee wastes at different w/c ratios. The percolation rate test set-up is per the ACI 522R-10 report, as shown in Fig. (4) [16]. To begin, a cylindrical pipe of 150mm in length and 95mm inner diameter is used as a mold to cast the permeable concrete samples of different void ratios. Without removing from the cylindrical pipe mold, the permeable concrete in the pipe was soaked into the water tank for 28 days of water curing. After the permeable concrete had gained ultimate strength upon 28 days of curing, the pipe was attached to the percolation rate test equipment. Water is then poured into the inlet of the water system to test for leakages around the pipe connections. All leakages were sealed off with PVC glue and rubber connectors. Ensuring that there are no more leakages in the piping system, water is then allowed to flow into the inlet of the system until the water overflows out from the outlet. Once overflow at the outlet, the valve is turned off. This is a pre-wetting process to ensure that all parts of the system are filled. Once filled with water, the stop valve is turned on for the water to flow from the inlet height of the water system to the height of the outlet of the system. A stopwatch is used at this stage to record the time taken for the water to flow from the height of the inlet of the system until it reaches the constant head to the outlet of the pipe, in which water stops flowing out from the system. The time taken was recorded, and the calculations for the percolation rate performance of the permeable concrete are calculated according to Darcy’s law as shown in Eq. (1). The equation is then summarized into Eq. (2), with A being a constant [24].
![]() |
(1) |
![]() |
(2) |
where
K = Permeability, mm/s
A1 = Area of the cross-section of the sample, mm
A2 = Area of the cross-section of the tube, mm
l = Thickness of a specimen, mm
h1 = Initial head of water, mm
h2 = Final head of water, mm
A = A constant with the value of 192mm
t = Time required for water to fall from initial head to final head, seconds
3. RESULTS AND DISCUSSION
3.1. Chemical Composition of the Spent Coffee Wastes
Running the oxide analysis of the spent coffee wastes, it was found that the different drying processes of the spent coffee wastes have caused the spent coffee wastes to possess very different properties. Other than the drying processes, the duration of drying may result in differences in chemical properties. The differences in the chemical composition of the spent coffee wastes due to the different drying processes and periods of exposure are similar to the study on rice husk ash waste, where different drying processes and periods of exposure cause different chemical compositions present in the rice husk ash waste [25].
The study begins with running XRF analysis for spent coffee wastes that have been obtained through sun drying methods for a duration of 2 weeks and oven drying at 100°C for a duration of 1 day. The excerpt of the results is shown in Table 2. For the spent coffee wastes that have been dried through sun drying methods, the highest composition is calcium oxide at 32.4%. With calcium oxide being the highest chemical composition in spent coffee wastes, this makes spent coffee wastes that have been dried through sun drying methods to be used as cement replacement as cement is known to be the highest in calcium oxide content [26]. However, when spent coffee wastes were sent for oven drying at 100°C for a 1-day period, the highest chemical composition is carbon at 53.3%. This makes spent coffee wastes oven dried at 100°C being not suitable to be used as cement replacement at a high percentage due to its high carbon content. This is seen in the case of biochar as cement replacement, where biochar can only be used as 1% cement replacement mainly due to the carbon-absorbing a high amount of water in the concrete [27].
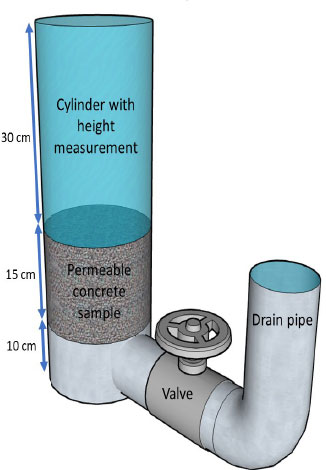
Noting the results obtained, the study proceeds to alter the oven drying temperatures and oven drying periods to reduce the carbon content of the spent coffee wastes. Hence, by altering the oven drying temperatures to 120°C and 150°C but decreasing the drying period from 1 day to 2 hours, the excerpt of the XRF analysis result is summarized in Table 2. The spent coffee wastes tested with XRF indicated that the highest composition in the spent coffee wastes is potassium oxide at 36.4% and 35.8%, respectively. Calcium oxide content was reported as second highest in both 120°C and 150°C oven drying spent coffee samples at 26.9% and 27.9%, respectively.
Comparing the overall data as summarized in Fig. (5), it can be seen that calcium oxide could be found highest in the sun-dried samples at 32.4% compared to the oven-dried samples at all temperatures with different drying periods. Calcium oxides are composed in limestone which makes cement because the reaction with water forms a binder known as calcium silicate hydrate (C-S-H) gel [28, 29]. The C-S-H gel is crucial in concrete formation as a reaction with water forms a liquid paste substance to hold the concrete constituents together and, when allowed to dry and cure, hardens into a solid [30].
- | Chemical Composition (%) | |||
---|---|---|---|---|
Sun Dry for 2 Weeks | Oven Dry at 100°C for 1 Day | Oven Dry at 120°C for 2 Hours | Oven Dry at 150°C for 2 Hours | |
CaO | 32.4 | 0.600 | 26.9 | 27.9 |
Fe2O3 | 4.09 | 0.452 | 3.37 | 3.55 |
Al2O3 | 0.855 | 0.147 | 0.351 | 0.452 |
SiO2 | 2.09 | 1.01 | 1.14 | 1.29 |
K2O | 27.2 | 0.711 | 36.4 | 35.8 |
P2O5 | 12.8 | 0.552 | 12.7 | 12.7 |
SO3 | 10.6 | 0.441 | 10.9 | 10.7 |
Cl | 3.89 | 0.13 | 2.52 | 2.53 |
C | - | 53.3 | - | - |
O2 | - | 42.2 | - | - |
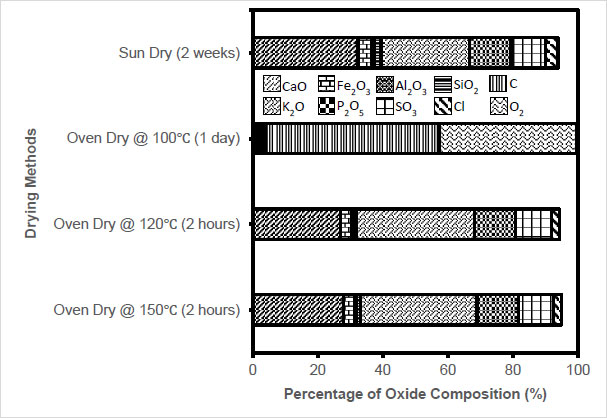
According to the ASTM C618-19 standards [31], a material would need to have 70% SiO2, Al2O3, and Fe2O3 to be classified as pozzolan to be used as cement replacement, which, from the summary illustrated in Fig. (5), shows that spent coffee wastes does not contain the necessary composition to be classified as pozzolanic properties. Other than having the highest calcium oxide composition in the sun-dried samples, sun-dried samples also presented higher SiO2, Al2O3, and Fe2O3 composition compared to the oven-dried samples. Hence, to proceed to the next phase of the study, spent coffee wastes that have been processed through sun drying methods are most suited as material to replace cement in permeable concretes of this study due to its higher CaO, SiO2, Al2O3, and Fe2O3 composition.
3.2. Compressive Strength of the Spent Coffee Permeable Concrete
From the results obtained from the XRF analysis, sundried spent coffee wastes were then used to cast permeable concretes to investigate for its applicability as cement replacement at w/c ratio of 0.3, 0.35, and 0.4 as well as percentages of 0%, 1%, 3%, 5% and 10% by weight replacement. For all the 5 percentages studied and the 3 w/c ratios, the permeable concrete cast was set to undergo a water curing of 7 days, 14 days, and 28 days. The compressive strength test was then conducted on 3 samples of permeable concrete from 5 different percentages of cement weight replacement at 3 different w/c ratios and 3 different days of water curing.
From the compressive strength test results, as summarized in Fig. (6), it can be seen that the best performing permeable concrete are those that contain 1% spent coffee wastes as partial cement replacement by weight with a w/c ratio of 0.35. Observing the 1% cement replacement data, it can be seen that at a w/c ratio of 0.3 and 0.4, the compressive strength performance is generally weaker compared to the 0.35 w/c ratio mixes. Initially, at 7 days of curing, the 0.35 w/c ratio mixes containing 1% cement replaced with spent coffee wastes perform slightly lower strength compared to the 0% mixes at a w/c ratio of 0.35 with a minor difference of only about 0.009%. However, the 1% mixes at 0.35 w/c ratio outperform all control mixes of 0.35 w/c ratio at 14 days and 28 days curing. This result presents a similarity to the study on biochar pervious concrete, where 1% cement replacement shows better compressive strength than the conventional permeable concrete mixes [32]. The ultimate compressive strength of the 1% mixes of 0.35 w/c ratio is superior to all other mixes except the control mix at 0.4 w/c ratios.
Observing the control mixes, however, throughout all w/c ratios, the compressive strength increases with the increasing period of water curing. The compressive strength also increases with the increasing w/c ratio. The results obtained from the control mixes are similar to a research study conducted by Claudino et al. [33], where the conventional pervious oncrete mixes increase in strength with the rising w/c ratio. This trend, however, is not observed in all spent coffee waste cement replaced mixes. The 0.4 w/c ratio spent coffee permeable concrete mixes indicated lowered compressive strength, which may be a result of too much water present in the permeable concrete matrix. When a concrete mix contains too high a w/c ratio, the bond strength of the concrete constituents may be decreased [34]. This is because, at a high w/c ratio, the hydration kinetics is slower, resulting in a longer setting time needed for the concrete mix [35]. The delay in hydration kinetics of the cement paste can result in the evaporation of excess water and the formation of pores in the concrete matrix, which lowers the compressive strength of the concrete produced [36]. For the spent coffee, permeable concrete samples of 0.3 w/c ratio also indicated lowered mechanical strength, which may be a result of insufficient water needed for the permeable concrete sample to harden, causing pores to form within the permeable concrete matrix. This data is similar to a study conducted by Das et al. [37], where the low w/c ratio caused a high porous pervious concrete, leading to lowered mechanical strength. Hence, the 0.35 w/c ratio can be concluded as the most optimum proportion of water and cement for a strong yet permeable spent coffee permeable concrete.
The 3% data presented a maximum strength gain of not over 8 MPa at 0.35 w/c ratio, making all 3% mixes generally unsuitable to be used as cement replacement. For all 5% and 10% cement replaced samples, the strength gain is too low, rendering both mixes unsuitable. The 10% cement replacement samples, in fact, despite being cured for a period of up to 28 days, still presented strength too low to be reported from the compressive strength test equipment. This shows that the increasing percentage of cement replacement resulted in lowered mechanical strength, mainly due to the coffee wastes having high calcium oxides but not enough to be classified as a pozzolan. This data is similar to the compressive strength data of concrete containing wood ash wastes where the increasing cement replacement decreases the compressive strength, due to the wood ash wastes containing high calcium oxide but insufficient to be classified as a pozzolan [38].
Thus, as a closure of the results of the compressive strength performance of the permeable concrete, it can be said that the best performance mix of the spent coffee permeable concrete would be at 1% mixes with a w/c ratio of 0.35 with its performance outperforming the control mix of w/c ratio of 0.35 by around 7.45%.
3.3. Percolation Rate of the Spent Coffee Permeable Concrete
The results of the percolation rate study of the spent coffee permeable concrete samples are presented in Fig. (7). Studying the percolation rate of the permeable concrete samples, it can be generally seen that the 3% cement-replaced permeable concrete samples contain the highest percolation rate throughout all the 3 different w/c ratios. The high percolation rate of the 3% permeable concrete mixes could be a result of the water being absorbed by the spent coffee wastes developing higher voids present in the permeable concrete. The results are similar to a study utilizing palm oil fuel ash (POFA) as cement replacement. It was found that the addition of POFA into the permeable concrete mix increased the percolation rate of the pervious concrete as water may be absorbed by the highly porous POFA particles in the permeable concrete matrix, causing the formation of pores [39].
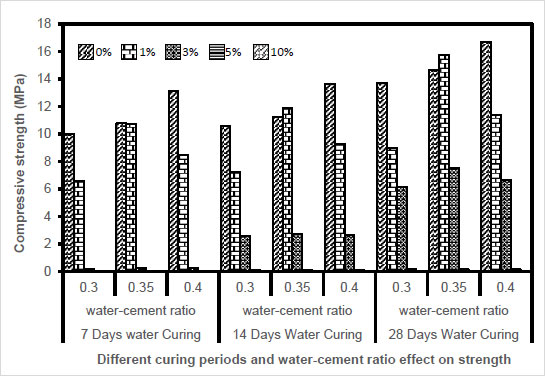
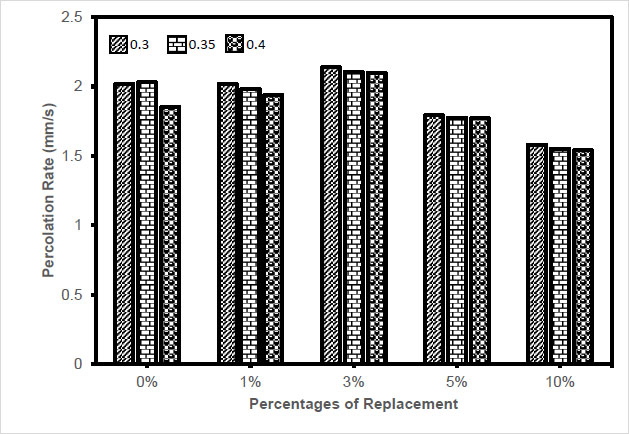
Comparing between control mix samples and 1% cement replacement samples, the percolation rate is similar at a w/c ratio of 0.3. However, at 0.35 w/c ratio, the control mix samples indicated a higher percolation rate compared to the 1% mixes. This phenomenon could be due to the spent coffee wastes being able to fill in the pores of the permeable concrete better, resulting in a decreased percolation rate. This also explained the increase in mechanical strength of the 1% mixes for the permeable concrete of 0.35 w/c ratio. According to Elango et al. [40], it was reported that permeable concretes have a tendency to increase the strength with decreased permeability as pores of the permeable concrete are being filled, giving it a more compacted permeable concrete matrix. Even though the 1% spent coffee permeable concrete samples present a decrease in permeability properties compared to the control mix, the percolation rate of the spent coffee permeable concrete samples generally still has acceptable values at 1.982 mm/s as typical permeable concrete only contains roughly 1 mm/s to 2 mm/s [41, 42].
For the 1%, 5% and 10% spent coffee waste permeable concrete samples, the higher amount of spent coffee waste as cement replacement in the permeable concrete matrix resulted in a decrease in percolation rate. However, at 3%, there is an improvement in the percolation rate in the spent coffee permeable concrete. This could be largely due to the wastes filling up the internal pores of the permeable concrete matrix, but at the right amount, the wastes may help develop higher pores in the permeable concrete. The findings of a study by Moura et al. [43] illustrated that the use of glass powder waste at a higher percentage has also caused a decrease in the percolation rate of the pervious concrete, but at a certain percentage, the percolation rate increased as well. Nevertheless, the improvement of the percolation rate could also mean that higher voids are present in the permeable concrete, eventually leading to decreased compressive strength properties [44].
Generally, all permeable concrete samples containing spent coffee wastes at 0.3 w/c ratios have higher percolation rates compared to the w/c ratio at 0.35 and 0.4 w/c ratios. The spent coffee permeable concrete samples at w/c ratio present the lowest percolation rate values. This is similar to the study conducted by Cai et al. [45], where it was found that the high w/c ratio would cause excessive cement flowability, resulting in cement paste flowing downwards, blocking the pores of the pervious concrete.
3.4. Summary of Test Results
From the XRF analysis, the spent coffee waste undergoing sun dry methods shows the highest chemical composition of calcium oxide. When oven-dried at 100°C for 1 day (24 hours), the spent coffee wastes show a high carbon content, making it less preferable to be used as cement replacement. Altering the temperature of oven drying to 120°C and 150°C with a drying period of 2 hours, the spent coffee wastes show the highest chemical composition of potassium oxide, with calcium oxide coming in second. In terms of the compressive strength performance, spent coffee wastes could only be used as cement replacement at a maximum of 1% by weight of cement; at 3%, 5%, and 10% replacement, the compressive strength proceeds to drop drastically. Nevertheless, at 1%, the w/c ratio suitable is 0.35, where the strength outperforms control mixes of w/c ratios of 0.3 and 0.35. In terms of the percolation rate, at 1% mixes, the percolation rate decreases with the increasing w/c ratio. Noting the 0.35 w/c ratio of 1% mixes, only a small drop of percolation was observed compared to the control mix at the same w/c ratio. This could be due to the spent coffee wastes being able to fill up more pores in the concrete resulting in an increased strength but decreased percolation rate permeable concrete. The summary of the test results for the compressive strength and percolation rate performance of the 0% and 1% mixes over 3 different w/c ratios are summarized in Fig (8).
From the summary, it is indicated that the 1% spent coffee permeable concrete samples generally have higher pores in 0.30 w/c ratio samples, resulting in lowered strength. Whereas in 0.35 w/c ratio samples, the number of pores decreases, resulting in increased strength with acceptable percolation properties. The 0.40 w/c ratio samples indicated the lowest number of pores, with decreased percolation rate and decreased strength mainly due to the excess water present in the permeable concrete matrix. These findings are similar to the casted samples as shown in Fig. (9) where at 0.30 w/c ratio, large pores could be seen, and at 0.35 w/c ratio, the pore size reduces; whereas at 0.40 w/c ratio, the cement paste has high flowability resulting in blockage at the bottom of the permeable concrete sample.
In conclusion, the most optimum proportion of spent coffee waste as cement replacement in permeable concrete is 1% by weight of cement with a water-cement ratio of 0.35 for the best performance. While the 1% replacement may be low in numbers, the impact of the research is significant.
3.5. Implications of Research Finding
In scientific knowledge and research, this study paves an alternative method of processing the spent coffee wastes that contain high CaO content. This allows future research works to capitalize on this knowledge and can potentially use other waste materials that could complement the chemical composition of the sundried spent coffee wastes which may allow for higher percentages of spent coffee waste application in the concrete. This can be seen in studies utilizing rice husk ash (RHA) in which alone the percentage of cement replacement could be effective up to only 10%, but when paired with the incorporation of ground granulated blast furnace slag (GGBFS) as a coarse aggregate replacement, it was found that the strength is observed to increase upon incorporation of 20% RHA and 25% GGBFS [46, 47].
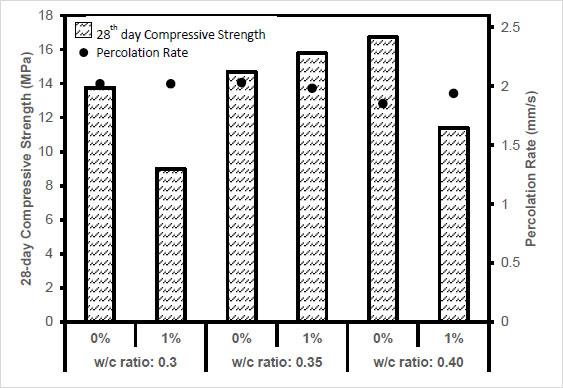
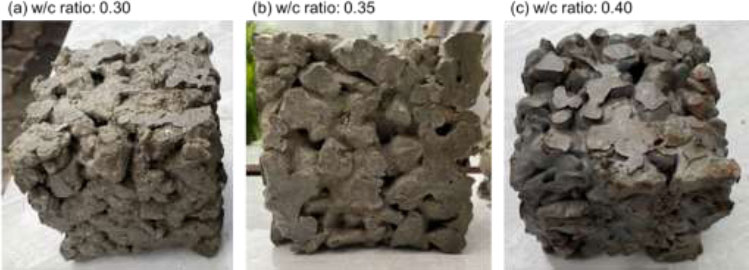
Another impact of the research is the reduction of cement in concrete production. It is important to acknowledge that cement production uses natural resources that may take a long time to replenish [48]. Hence, the use of spent coffee wastes, even at low percentages as cement replacement could potentially lower the demand for depletable natural resources with wastes that are produced daily and increasing in volume. This could promote sustainable values in both the coffee-drinking industry and also the construction industry.
Other than that, one of the crucial impacts of the research is the high availability of spent coffee waste around the world. Unlike certain wastes such as rice husk ash and palm oil fuel ash that are harder to obtain in certain regions of the world, spent coffee wastes are largely accessible around the world due to their high production and consumption rate around the world [49-51]. This makes the spent coffee waste more accessible to be reused as a material in concrete. Thus, this research can promote the use of waste materials that are easily collected as supplementary material for concrete production.
Another impact of the research includes promoting better practices in managing spent coffee waste. Being classified as organic wastes, spent coffee wastes experience rotting in landfills, which can cause major environmental issues [52]. Also, being treated as general waste in most cities around the world spent coffee wastes are often disposed of without care. However, improper disposal methods of spent coffee can lead to contamination of groundwater, affecting the ecosystem [53]. Hence, reutilization of these wastes gives a completely sustainable coffee-drinking cycle while reducing the greenhouse gases that are released during cement production.
CONCLUSION
Based on the results obtained, the following conclusion can be drawn:
• XRF analysis indicates that spent coffee wastes have the potential to be used as cement replacement in concrete.
• In this study, spent coffee wastes are suitable to be used as a cement replacement in permeable concrete with up to 1% by weight of cement and a w/c ratio of 0.35.
• Permeable concrete containing cement replaced by weight of spent coffee wastes at 1% with a w/c ratio of 0.35 presents acceptable percolation rate properties.
LIMITATIONS
From the study, there may be a few limitations involved:
• Spent coffee waste being studied originates from a local coffee shop in Malaysia. Hence, it may not be suitable to represent the universal spent coffee waste properties. However, the study conducted at this stage is suitable for future research works to use as a reference.
RECOMMENDATIONS
As a recommendation for future studies:
• Durability tests can take place in the future to identify the effect of spent coffee wastes as cement replacement in permeable concrete.
• To investigate the use of spent coffee wastes at higher proportions in the permeable concrete, adjustments should be made to the water-cement ratio.
HIGHLIGHTS
- Study the chemical composition of spent coffee wastes through X-ray fluorescence.
- Identify the strength of spent coffee permeable concrete at varying water-cement ratios.
- Evaluate the strength of permeable concrete at replacement proportions of spent coffee.
- Investigate the percolation rate of spent coffee permeable concrete.
LIST OF ABBREVIATIONS
ACI | = American Concrete Institute |
Al2O3 | = Aluminium Oxide |
ASTM | = American Society for Testing and Materials |
BS EN | = British Standard incorporating European Standard |
C | = Carbon |
CaO | = Calcium Oxide |
Cl | = Chloride |
CSH | = Calcium Silicate Hydrate |
Fe2O3 | = Ferrous Oxide |
K2O | = Potassium Oxide |
LA | = Los Angeles |
OPC | = Ordinary Portland Cement |
O2 | = Dioxygen |
POFA | = Palm Oil Fuel Ash |
P2O5 | = Phosphorus Pentoxide |
SC | = Spent Coffee |
SDG | = Sustainable Development Goals |
SiO2 | = Silicon Dioxide |
SO3 | = Sulphur Trioxide |
UN | = United Nations |
w/c | = water-cement ratio |
XRF | = X-Ray Fluorescence |
CONSENT FOR PUBLICATION
Not applicable.
AVAILABILITY OF DATA AND MATERIAL
The data supporting the findings of the article is available in the Mendeley Data at https://dx.doi.org/10.176 32/k4s8sf49bg.1, reference number doi: 10.17632/k4s8s f49bg.1.
FUNDING
This study was funded by Universiti Malaysia Pahang Al-Sultan Abdullah, Funder ID: Postgraduate Research Grant Scheme (PGRS), Awards/Grant number: PGRS2303 123.
CONFLICT OF INTEREST
The authors declare no conflict of interest, financial or otherwise.
ACKNOWLEDGEMENTS
The authors would like to acknowledge the financial support from Universiti Malaysia Pahang Al-Sultan Abdullah (UMPSA) Postgraduate Research Grant with grant number, PGRS2303123.