All published articles of this journal are available on ScienceDirect.
Enhancement of Straw Bale Performance Using Gum Arabic
Abstract
Background:
The negative impacts of the construction industry are compelling arguments for embracing technology that contributes to carbon footprint reduction and resources conservation. Toward the achievement of objective 9 of the Sustainable Development Goals, the development of new building’s materials like straw bale has advanced in the construction industry. As demonstrated in the literature, straw bale is an eco-friendly material that presents many advantages, like its contribution towards a circular economy. However, it has low compressive strength and displays high displacement under compression load. So far, no attempt has been made in order to enhance the strength of straw bales.
Objective:
This study aimed to develop alternative material to straw bale using chopped straw stems mixed with a binder (gum Arabic) and determine its stress-strain characteristic.
Methods:
The manufacturing process of the new material involved the use of chopped straw and gum Arabic to form straw blocks.
Results:
Results obtained show that the compressive strength of straw block (1.25MPa) is greater than the strength of straw bale (0.02MPa). Also, the average displacement recorded during compression load on straw blocks (29mm) was 2.8 times smaller than the displacement in straw bale (80mm). In terms of shape and size, straw blocks match with conventional materials like cement or compressed block. This will facilitate their use in construction compared to straw bales that require skilled laborers for pre-compression and plastering.
Conclusion:
The use of gum arabic helps in holding straw stems together and forms a compact material with improved strength compared to straw bale. Performance improvement of the characteristics of load-bearing straw bale walls can be addressed by using straw blocks.
1. INTRODUCTION
The rate at which the population is growing is an indicator that more houses are to be built. To protect the environment, it is evident that we cannot rely on concrete material for the construction of new homes. In general, it has been estimated that buildings account for about 40% of world GHG emissions [1]. Cement is the second-highest industrial source of carbondioxide on earth [2]. To provide a clean environment, the concept of sustainable construction or green buildings has evolved in order to mitigate the negative impacts of constructions. One of the foremost actions of this arena is to shift technology and develop infrastructures that can respond and adapt to the climate. Over the last decades, attempts to minimize the environmental burden of buildings, to reduce construction cost and provide acceptable thermal comfort have been made by the use of natural construction materials such as straw bale.
Straw bale is made of residue material from the agricultural crop (rice, wheat). The method of baling consists of compressing straw stems and tiyng them with two or three strings. Handbooks on straw bale construction are published by Corum, Hodge, Nails and Walker et al. [3-6]. These books served as a guide to those who are interested in building straw bale houses. It is known that straw stems are biodegradable; therefore, straw bales can deteriorate with time. Studies reports show that buildings made of the straw bale are water, fire and rot resistant when techniques of good practices are used [7], [8]. Among such techniques, we have roof overhangs and a moisture barrier at the bottom course of straw bale. Moreover, previous studies on straw bale recorded low strength and high deflection of straw bale. The average compressive strength of straw bales is around 0.02 MPa [9, 10], while the displacement in straw bales is in the range of 32 – 90 mm [11, 12]. The displacement in straw bales depends on their density. The compressive strength of plastered straw bale assemblies depends on the plaster [13, 14] because plastered straw bale assemblies form a composite structure that works like a sandwich panel. The relationship between plaster and straw bale is the same as in the web to flange in a steel I-beam [15]. Therefore straw bales and plasterwork together to create a composite structural system similar in concept and performance to the structural insulated panel [16]. However, the relatively small load-carrying capacity of plastered straw bale assemblies limits straw bale construction to single-story buildings. The enduring interest and continued development of straw bale houses result from the fact that straw bale is a bio material that contributes greatly to carbon footprint reduction and to resources conservation [14, 17]. For instance, straw bale is an environmental friendly material; it provides significant benefit in term of cost and human health [18]. Straw bale walls offer excellent thermal insulation; their thermal property is around 0.06W/mK [19]. Straw bale home construction is shown to be achieved at a lower cost, with lower embodied energy compared to conventional materials [20].
To improve quality and structural performance of straw bale houses, some methods are used. These methods consist of pre-compressing straw bale assemblies before plastering them. For instance, to pre-compress straw bale assemblies, King [15] used a threaded rod through the bales at intervals of 1.8m. Lecompte and Le Duigou [21] used tensioning cable to tie the top plate to the foundation and push down straw bale assemblies. Also, in order to provide stability during construction, steel or wood rebar is used to pin straw bales [7]. These techniques enhance only the stability of straw bale assemblies and not the strength of the bales. In addition, the pre-compression process is complex, and its application may be limited if no qualified labor is available. However, from the compression test conducted on straw bale and modelled straw bale, it was observed that straw bales do not withstand the load applied on them; they displayed an elastic behavior. Under compression load, for instance, there is high displacement in the bale. Strawbale height shifts from
Gum Arabic is a natural binder from the hardened sap of acacia trees. Gum Arabic is found in the Middle East and North Africa [23, 24]. It is called Gum Arabic because it is exported from Arabia countries [24]. Gum Arabic is not harmful; it is a normal branched-chain multi-functional hydrocolloid with a complex of calcium, magnesium and potassium [25]. Its chemical properties and features are being used in a wide range of industrial sectors such as textiles, ceramics, lithography, cosmetics and pharmaceuticals, encapsulation, food, etc [24]. For example, it is used worldwide as a stabilizer in wine, soft drink, candies, cosmetics, postage stamps, envelopes, paint and traditional treatment of diverse diseases [23]. Gum Arabic has great potential in the construction industry. Studies have shown that the addition of gum Arabic in concrete and mortar increases the setting time and thus, can be used as a super plasticizer in concrete and mortar [26-28]. Moreover, gum Arabic is used as a binder in the production of eco-friendly particleboard because it increases the stiffness of particleboard [29].
The aim of this research was to develop alternative straw blocks from chopped straw stems mixed with a binder (gum Arabic) to determine the stress-strain characteristic of manufactured straw blocks and compare the results with the strength of straw bales. Straw block (Table 1) is made of chopped straw stems mixed with a binder, while straw bale (Fig. 1) is made of straw stems tied down with two or three strings [17].
2. MATERIALS AND METHODS
In this work, wheat straw bale (Fig. 1), sawdust (used in order to provide fine particles in the block) and gum Arabic from local suppliers in Kenya were used. Gum Arabic looks like stone (Fig. 2) and thus requires to be crushed before use. To form a binder, gum Arabic is mixed with water. The size of powder gum Arabic does not matter because it will dissolve in water to form a viscous solution. Wheat straw and gum Arabic are locally available and environmentally friendly materials. In Kenya, for example, it is estimated that annually, about 800 000 metric tons of wheat straw residue are generated [30]. Also, Kenya is the 3rd largest exporter of gum Arabic and its annual production is estimated to be 10 000 tons [31]. If gum Arabic and straw are used to manufacture masonry units, the cost of purchasing and transporting commercialized materials will reduce.
2.1. Straw Block Design and Manufacturing Process
Binder preparation consisted of producing homogenous glue from the mixture of hot water and gum Arabic. Four ratios (1:0.5, 1:0.75, 1:1 and 1:1.25) per volume were investigated. To determine the ratio that has good bonding with straw, each of these ratios was mixed with chopped straw. Binder formed from ratio 1:1 satisfied the desirable attribute of the straw binder. Compared to the 3 others ratios, the ratio 1:1 forms a binder that flew easily in straw, that is not absorbed by straw, and that binds straw stems well. We used this ratio for the production of straw blocks. Straw stems were chopped into small length (1 to 9 cm). A bucket of 10 liters was used to measure chopped straw and the weight was recorded. In order to determine the quantities that fit well in the blocks manufacturing machine, three mixtures were made with water to gum ratio of 1:1. The weight of chopped straw per mixture was 0.658kg for mixture A, 0.823kg for mixture B and 0.987kg for mixture C. Mixture B fits well in the blocks manufacturing machine.
2.2. Straw Block Manufacturing and Testing Procedure
A cubic meter for mixture B requires 215 liter of water, 244 kg of gum Arabic, and 89 kg of chopped straw. As shown in Table 1, three types of block were manufactured using hand compression machine (Fig. 3). For each type of straw block, 3 blocks were cast. After one month of curing in the open air, straw blocks were tested under compression load using AMSLER’S compression testing apparatus. Other equipments were: load cell type CLP-50B, with capacity of 50tf and sensitivity 2mV/V; 2 dial gauge displacement transducers type DDP-30AS2 of capacity 30mm to measure transversal and longitudinal displacement in the blocks. The equipment was connected to a data logger, and test results were printed out after every 5 seconds. Two methods were used to record displacement in the blocks. The first recording was automatic with the displacement transducers. When the transducer reached its maximum (30mm), further displacements were recorded manually at 3 different loads: 20KN, 50KN and 100KN. Compression test was conducted as per BS 1881 part 166: 1983. Fig. (4) shows the test set up.
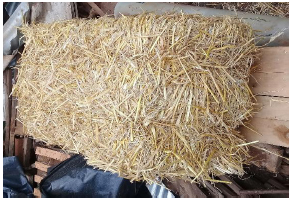
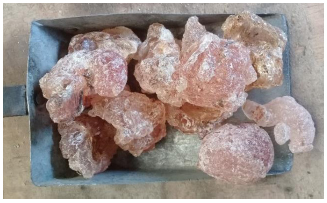
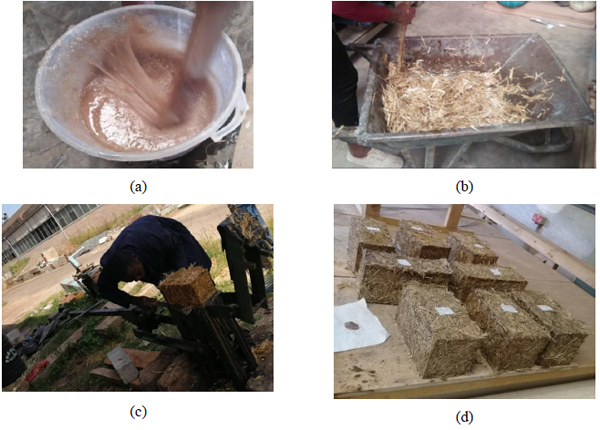
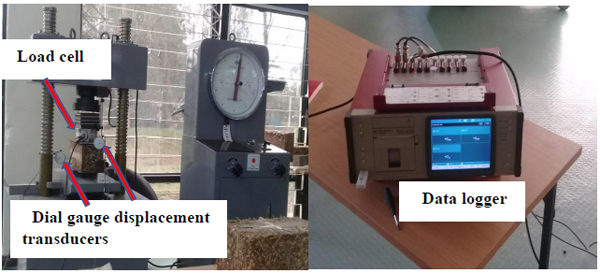
Block Sample | Block Label | Different Type of Straw Block |
---|---|---|
Block Type 1: Cast using chopped straw of length less than 2 cm mixed with binder |
WSB_1 | ![]() |
Block Type 2: Cast using chopped straw of length less than 9 cm mixed with a binder |
WSB_2 | ![]() |
Block Type 3: Cast using chopped straw of length less than 9 cm and sawdust mixed with a binder |
WSB_SD | ![]() |
3. RESULTS AND DISCUSSION
Table 2 below shows the compressive strength of straw blocks. It also shows the longitudinal and transverse displacement measured at maximum load in the block during the compression test.
It is important to determine the compressive strength of straw blocks and deflection that may occur in the loaded straw blocks because in load-bearing wall, straw blocks are permanently under compression. Generally, standards are used to control the minimum compressive strength for blocks and the maximum displacement that we can allow in masonry. For straw bale construction, Appendix R and appendix S of the International Residential Code (IRC) regulate the load-bearing capacity of straw bale assemblies
3.1. Compressive Strength
The characteristic that determines if a material can be used for load-bearing wall is its compressive strength. Results obtained from the compression test show that the compressive strength of straw blocks at maximum load is 1.25 Mpa (Table 2). A similar study to this research was conducted by Colsom et al. [32]. In this work, chopped straw was mixed with a bio binder to manufacture straw cubes. After testing, the straw cube had a compressive strength of 1 MPa. Currently, straw bale used for the construction of straw bale houses is around 0.02 MPa. Based on this , the compressive strength of straw block is greater than the strength of straw bale and that of straw cubes. Therefore, straw blocks can support more load compared to straw bale and straw cubes. Standards are not yet established for the minimum strength of straw bale. However, the allowable compressive load for cement plastered load-bearing straw bale walls is 800 pounds per linear foot; about 11.675KN/m as per Appendix S of the International Residential Code [33]. Because load-carrying capacity of straw bale wall is small, the construction of straw bale houses is limited to one storey buildings [33]. A study conducted by Njike et al. [17] shows that straw block assemblies can support at least 286 KN/m2, which is higher than the minimum slab load (18.25KN/m2) for a residential house. Thus straw blocks can be used for the construction of single-story buildings.
Furthermore, under compression load, straw block deformation curves (Fig. 5) go upward parallel to the vertical axis; the same behavior was observed in a straw bale. Three stages are identified in the behavior of straw bale [14, 34]. Stage 1 is identified as the stage where there is high displacement in the block with low compressive strength. Stage 2 is the stage where a linear elastic behavior, comparable to that of concrete and timber is observed. The last stage corresponds to the hardening behavior where straw block became compact. In this stage, stress increases while there is small displacement in the block.
3.2. Displacement
The load-displacement curve represents the relationship between applied load and deformations for the three types of straw blocks. Two methods were used to record displacement in the blocks. The first recording was automatic with the displacement transducers. When the transducer reached its maximum (30mm), further displacements were recorded manually at 3 different loads: 20KN, 50KN and 100KN. The longitudinal and transverse displacement was measured for each type of straw block. At maximum applied load (100KN), the longitudinal displacement in the straw block is around 60mm, 50mm and 30 mm for blocks type 2, type 3 and type 1, respectively. This result implies that when the length of chopped straw becomes small and when fine aggregates are added, straw blocks become more compact. In addition, as shown in Fig. (6), there is high displacement in straw bale compared to the displacement in different type of straw blocks.
The transverse displacement was minimal in all three types of blocks. At maximum load, the maximum horizontal displacement recorded was 3 mm, 4mm and 3 mm for blocks type1, block type 2 and block type 3, respectively.
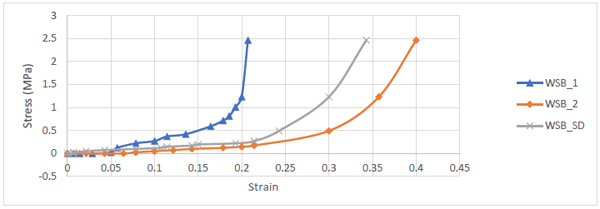
Block Sample | Block Label | Average Bale/Block Dimensions (mm) | Average Wight (Kg) | Density (kg/m3) | Longitudinal Displacement (mm) | Transverse Displacement (mm) | Average Compressive Strength at Maximum Load (MPa) |
---|---|---|---|---|---|---|---|
Type 1 | WSB_1 | 290 x 140 x 140 | 5.37 | 944.76 | 29 | 3 | 1.25 |
Type 2 | WSB_2 | 3.08 | 541.87 | 56 | 4 | ||
Type 3 | WSB_SD | 3.445 | 606.09 | 48 | 3 |
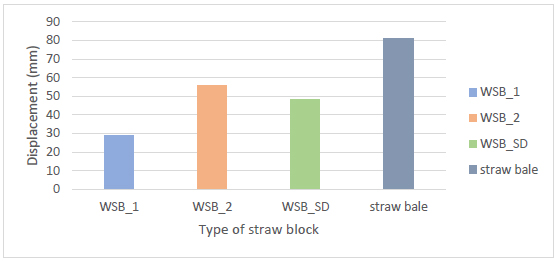
CONCLUSION
The manufactured straw blocks have a compressive strength of 1.25 MPa at maximum applied load. This value is greater than the strength of straw bale (0.02MPa). Since load carrying capacity of masonry depends on the strength of its constituent materials, plastered load-bearing straw block walls will support more load compared to plastered straw bale panels. Also, in response to the applied load, displacement in the straw block is smaller than the displacement in a straw bale. Displacement in straw blocks was about half of the displacement in a straw bale. The use of gum arabic helps in holding straw stems together and forms a compact material with improved strength compared to straw bale. Improvement of the performance characteristics of load bearing straw bale walls can be made by using straw blocks. In addition, straw blocks have a regular form similar to that of cement or compressed block. This will facilitate their use in construction compared to straw bale that requires skilled laborers for pre-compression and plastering.
However, the straw block should be used for the construction of single-story houses as recommended in Appendix S of the International Residential Code. Also, the straw block is a biodegradable material and its durability will be influenced by the presence of water. It is recommended that during construction, engineers or practitioners should follow the established good practices guideline for masonry. The good practices (roof overhangs, increasing the height of slab beam from the floor, use of a moisture barrier at the bottom course of straw block) help in minimizing problems such as moisture in straw block masonry.
AUTHORS' CONTRIBUTIONS
Conceptualization, M.N.; W.O.O. and S.O.A.; methodology, M.N. and W.O.O.; formal analysis, M.N., W.O.O. and S.O.A.; data curation, M.N.; writing—original draft preparation, M.N.; writing—review and editing, M.N., W.O.O. and S.O.A.; visualization, M.N.; supervision, W.O.O. and S.O.A.; funding acquisition, M.N.; W.O.O. and S.O.A.; All authors have read and agreed to the published version of the manuscript.
CONSENT FOR PUBLICATION
Not applicable.
AVAILABILITY OF DATA AND MATERIALS
The data supporting the findings of the article will be available in the Jomo Kenyatta University of Agriculture and Technology, Kenya repository at: http://ir.jkuat.ac.ke/handle/123456789/1154.
FUNDING
This research was funded by the African Union Commission (AUC) as contribution to high education in Africa through the Pan African University.
CONFLICT OF INTEREST
The authors declare no conflict of interest, financial or otherwise.
ACKNOWLEDGEMENTS
The first author wants to appreciate the African Union Commission and the Pan African University for making fund available for this study.