All published articles of this journal are available on ScienceDirect.
A Comprehensive Review of the Factors and Strategies to Mitigate Construction Projects Delays in Saudi Arabia
Abstract
Background
The construction industry in Saudi Arabia faces numerous challenges that hinder its progress due to frequent and prolonged project delays.
Objectives
The specific objectives of this study are (1) To analyze the factors contributing to construction project delays in Saudi Arabia, (2) To identify the risk of factors contributing to construction project delays, and (3) To propose strategies to mitigate construction project delays in Saudi Arabia.
Methods
The study reviewed 16 articles to identify and suggest solutions for construction project delays in Saudi Arabia.
Results
There are 140 factors of delay found and seven pose unacceptable risks including delays due to material delivery, delays in approval of submittals, design drawings, shop drawings, and sample materials (making decisions), delays related to subcontractors work, inflation and escalation of material prices (changes in price), lack of coordination with contractors, shortage of construction materials (non-availability of material), and equipment shortages. The risk assessment can be conducted using the Bowtie diagram, scenario analysis, MRM, and MCS separately or collectively to get a new and improved model.
Conclusion
This review will contribute to the development of strategies to enhance the performance of ongoing and future construction projects in the region. Additionally, decision-makers can utilize the outcomes to strategically allocate resources and improve construction project success.
1. INTRODUCTION
The construction sector is constantly expanding, exerting a significant influence on the national economy and numerous other industries [1, 2]. Construction projects hold paramount importance, serving as crucial instruments for translating strategic aspirations and objectives from theoretical plans into tangible realities [2]. A project's success acts as a benchmark for gauging its operational efficiency and its ability to deliver on its developmental goals. However, construction projects often encounter challenges and obstacles [3].
A project’s success can be measured by its performance indicators. A project is considered successful if it delivers the building or structure within the established parameters of time, cost, and quality, ultimately achieving client satisfaction [4, 5]. However, various unforeseen events can impact construction performance. Additionally, factors like party performance, resource availability, environmental conditions, and contractual agreements all influence project outcomes [6].
A report by Arcadis Contract Solutions [7] identified several key factors contributing to construction delays in 2019. These include poorly drafted or incomplete claims lacking proper evidence, a lack of interim awards regarding time extensions and compensation, and failures by owners, contractors, and subcontractors to understand or fulfill their contractual obligations.
The Middle Eastern countries suffered approximately 62 million USD in 2019, the highest amount of average dispute value globally, compared to North America (18.8 million USD), the United Kingdom (17.8 million USD), and Continental Europe (24.5 million USD).
The Royal Institute of Chartered Surveyors [8] reports that a global construction survey indicates a marginal improvement in construction activity globally. The global construction industry is gradually increasing, with positive growth observed in most regions. This is the fourth consecutive quarter of progress. The rise is driven by the Asia Pacific (APAC) and Middle East/Africa (MEA) regions, where workloads are increasing significantly across all sectors. Signs of improvement are also emerging from the Americas. Certain nations, including the United Arab Emirates, Saudi Arabia, and India, are prospering, and progress is evident in every sector of the building industry. There are also indications of a recovery in China. Sri Lanka and Qatar are having trouble in the building sector. Europe is the only continent experiencing negative growth, mostly due to a decline in the building of individual homes and mortgage rates. Notwithstanding the progress, expensive materials, cash flow problems, and a shortage of competent labor remain problems for construction firms. They might result in delays.
Construction management delays are among the leading factors in the economic slowdown in developing and emerging nations [9]. A delay in the construction project has an impact on several elements, including project cost, timeline, job quality, and others [10]. In the past few years, Saudi Arabia has seen a significant rise in construction projects, driven by its vision of economic diversification and regional leadership. The Ministry of Municipal and Rural Affairs (MOMRA) has addressed the issue of the estimated 75% of public construction projects taking longer than anticipated and running into delays [11]. The complexity and difficulty of current projects expose Saudi Arabian construction stakeholders to a multitude of unforeseen challenges.
Despite extensive research on critical success factors, construction professionals lack definitive data on the leading causes of project delays and their subsequent impact on success. Identifying and ranking these delay factors would significantly benefit the construction industry [12]. Also, due to the uniqueness of the Saudi Arabian construction industry, a one-size-fits-all solution may be inefficient. The unique challenges faced in this region, such as the complex structure of projects, strict deadlines, and intense competition in the market, call for a more comprehensive understanding of delay factors. Previous studies also frequently rely on qualitative data or concentrate on a small number of initiatives. This highlights the need to conduct a systematic analysis of the factors that particularly affect construction project delays in Saudi Arabia. As the nation sets out on a transformative journey, ensuring the efficient and successful execution of modern construction projects is crucial to achieving its goals.
Hence, this study aims to review the factors and recommend strategies for construction project delays in Saudi Arabia. Specifically, it will (1) analyze the factors contributing to construction project delays in Saudi Arabia, (2) identify the high-risk factors contributing to construction project delays, and (3) propose strategies to mitigate construction project delays in Saudi Arabia. This review will contribute to improved performance in current and future construction projects by examining factors causing delays and exploring potential solutions within the region. Decision-makers can leverage these findings to strategically allocate resources and enhance project success rates.
2. METHODS
2.1. Samples
The article sampling started by specifying the eligible studies. Multiple online resources were used to identify relevant articles on construction project delays in Saudi Arabia. Search terms include ‘delays,’ ‘construction delays,’ ‘delay factors,’ ‘factors of delay,’ and ‘Saudi Arabia.’ The initial search yielded a total of 59 articles. Subsequently, the article’s title and abstract were screened, and 38 articles were excluded (Fig. 1). The remaining articles were reviewed, and six articles were excluded. The exclusion criteria were articles 15 years and older, studies not specific to construction project delay factors in Saudi Arabia, and the non-availability of relevant data for frequency, severity, and importance analysis. A total of 16 articles were included in the final review, inclusive of a diverse array of studies relating to factors and potential strategies to mitigate construction project delays in the Saudi Arabian construction industry. The selected articles were reviewed and confirmed by all authors before being analyzed.
2.2. Analysis of Data
The variables collected from the studies are specific delay factors, the number of projects affected, and delay durations. There are three effect measures used, namely, frequency (percentages to represent frequency of delay factors), severity (mean number of delay durations), and importance analysis (importance index of each factor gathered from each study). Three methods to assess the risk of bias were employed, including assessment by two independent reviewers, disagreement resolution, and reporting of risk-of-bias assessment results.
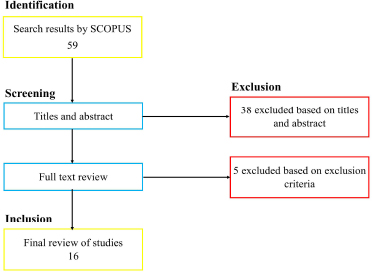
Methodology framework.
The data were extracted and categorized according to the degree of emphasis placed on the frequency, severity, or significance of delay factors. Relevant analysis includes articles that cover multiple aspects. Then, the data were screened for missing information. Alternative measures (medians, ranges) or standards were used to resolve missing data or inconsistencies. The results were added up and plotted for each outcome (frequency, severity, and importance). A description of the findings examines similarities, differences, and potential causes of variation using subgroup analysis. Lastly, sensitivity analyses were performed to evaluate the conclusions' robustness based on the availability of data and bias.
The data were analyzed using three types of indices, namely, the frequency or significance index (FI), relative importance or severity (RI) and importance index (RII), following the methods shown by Ibrahim and Nabil [13] and Rajgor et al. [14]. The FI value is used to rate the factor of construction delays according to how frequently they occur or how common a factor is [15]. The RI is a method to determine how important a factor is in contributing to construction delays. When a factor has a higher RI than factors with lower RI values, it indicates that it has a more significant negative effect on project deadlines. Finally, the RII builds upon the concepts of RI and FI to provide a broader perspective on the factors contributing to delays. A factor with a high RII indicates that it is frequently cited as a cause of delays (high FI) and is expected to have a major detrimental impact on project timelines (high RI).
These indices were selected due to their widespread use in identifying the most significant causes of construction delays. It is important to note that some studies did not directly report FI, RI, or RII values, necessitating their calculation using the following formulas:
![]() |
(1) |
![]() |
(2) |
![]() |
(3) |
Where ai represents the constant weight assigned to i (ranges from 1 to 5/ 1=unknown, 2=never, 3=low, 4=middle, and 5=high); xi represents the variable the frequency assigned to i (ranges from 1 to 5); and N represents the total number of participants in the study.
The calculation of FI includes the number of projects affected by the factor in that study and the frequency of the factor reported in that study. The RI is the average of the FI multiplied by the weight, which ranges from one to five. The RII is derived from the multiplication of FI and RI by the total number of participants involved in the studies.
After that, the frequency of the factor is recalculated by combining data from all participants across the articles. The following equation shows how the new frequency is determined:
![]() |
(4) |
Where FI’ represents the new frequency calculated over NT, FIx represents the frequency of factors gathered from each study, Nx participants of each study, and NT total number of participants from all articles.
Next, the severity of each factor is reassessed by incorporating data from a larger participant pool, encompassing all participants from the articles. Thus, the new severity is given by the following equation:
![]() |
(5) |
Where RI’ represents the new severity calculated over NT, RIx represents the severity of the factor gathered from each study, Nx participants of each study, and NT is the total number of participants from the articles.
Next, the importance index of the factors is recalculated by considering a larger group of participants and adding all participants from all articles. The new importance index is then determined by the following equation:
![]() |
(6) |
Where RII’ represents the new importance index calculated over NT, RIIx represents the importance index of each factor gathered from each study, Nx participants of each study, and NT total number of participants from all articles.
The standard risk matrix is used to determine the risk zone for the identified delay factor. There are seven scales used to identify the frequency and impact of the factors (Table 1). The frequency ranges from nearly impossible (< 14.29) to very often (> 85.74). The impact then ranges from minor to extreme. The risk matrix is 7*7, with impact ranging from minor to extreme on the horizontal axis and frequency ranging from very often to nearly impossible on the vertical axis (Fig. 2). The frequency and impact were differentiated by colors. The green box indicates the lowest level of risk, suggesting it can be ignored. The light green indicates a low-level risk, not a top priority level, but it is advisable to be monitored periodically. Yellow indicates a medium-level risk, where it is recommended to actively reduce the effect of these factors. Orange indicates a high level where risks should be monitored, and actions should be implemented. Finally, red indicates an unacceptable level of risk, demanding top priority and intensive efforts. If the risk is medium or higher, mitigation is necessary [16].
Scale | Frequency | Impact of severity is differentiated by colors as shown in Figure 2 |
---|---|---|
> 85.74 | Very often | Extreme |
71.45 - 85.74 | Often | Serious |
57.16 - 71.45 | Frequent | Significant |
42.87 - 57.16 | Probable | Moderate |
28.58 - 42.87 | Possible | Small |
14.29 - 28.58 | Improbable | Very small |
< 14.29 | Nearly impossible | Minor |
3. RESULTS AND DISCUSSION
3.1. Factors of Construction Project Delay in Saudi Arabia
Over 88% of the selected studies used qualitative questionnaires as their research methodology. By answering the questionnaire, Saudi Arabian experts in the construction industry provided several justifications for their perspectives on the various issues that building projects encounter. Most of the questions on the questionnaire dealt with elements of past studies. However, the analysis did not consider several factors that could potentially impact the results, such as the data source, the number of projects studied, the project execution duration, and the project types and sizes [17]. Therefore, future studies should realistically collect data from actual construction projects in Saudi Arabia. This would involve defining delay factors by analyzing the final reports of recently completed projects.
A total of 140 delay factors were identified across the reviewed articles (Table 2). Some of the factors were mentioned several times in different articles. One of the earliest studies on construction delays in Saudi Arabia, conducted by Albogamy et al. [18], identified 62 factors. Subsequent studies by Mahamid [19], and Elawi [20], found 31 and 7 factors, respectively. In 2016, Elawi et al. [20], and Mahamid [21], discussed 20 and 56 factors, respectively, while Al-Emad et al. [22], and Mahamid [23], identified 10 and 33 factors. Studies by Alotaibi [24], and Assaf et al. [1] contributed 20 and 25 factors, respectively. More recent studies by Mathar et al. [25], Gopang et al. [26], and Alharbi [27], identified 28, 34, and 47 factors, respectively. Other study by Abduljawwad & Almaktoom [28], found 13 factors, while Alshihri et al. [29] and Alshibani et al. [30], identified 76 and 11 factors, respectively. The most recent study, by Ahmad et al. [31], found 14 factors.
The factors are categorized into 11 groups. The groups are including;
(i) Owner / client related factors [15, 18, 21, 24, 26-28],
(ii) Consultant/supervisor related factors [15, 18, 21, 24, 26],
(iii) Designer related factors [24, 26, 28],
(iv) Contractor related factors [15, 18, 21, 24, 26-28],
(v) Material related factors [24, 26],
(vi) Equipment related factors [24, 26],
(vii) Labor related factors [24, 26],
(viii) Construction site or work environment related factors [31],
(ix) Government related factors [20],
(x) Force majeure risk related factors [29], and
(xi) Other external related factors [15, 21, 24]
The frequency of the delay factor can be categorized into two main categories i.e., internal, and external factors. The internal factors are factors that come from within the project. The internal factors with a frequency of more than 50.00% found in the review are contractor-related and designer-related factors. In contrast, the external factors stem from outside influences, including owner/client-related, government-related, and other external-related factors. The recalculated frequency of delay factor (Table 3) found that the internal factors related to contractor for instance, the difficulties in financing the project by contractor (cash flow problems), have the highest frequency of 72.16%. Within the owner/client related category, “delay of financing and payments by owner” (50.47%) is ranked as the second most common cause of delay, with a frequency of 60.44%. In general, these factors contribute to more delays than any other external factor.
The severity of the delay factor is also categorized into internal and external factors. The internal factors, with more than 50.00%, include contractor-related, consultant/supervisor-related, and labor-related factors. The external factors are force majeure risk-related, equipment-related, owner/client-related, and other external-related factors. The recalculated severity for the delay factor (Table 4) found that other external-related factors, such as poor communication and coordination with other parties, have the highest severity of 58.97%. Force majeure risk-related factors, such as the weather (heat, food, etc.), have a severity of 57.06%. The shortage of labor (inadequate crew size) has the lowest severity of only 52.72%.
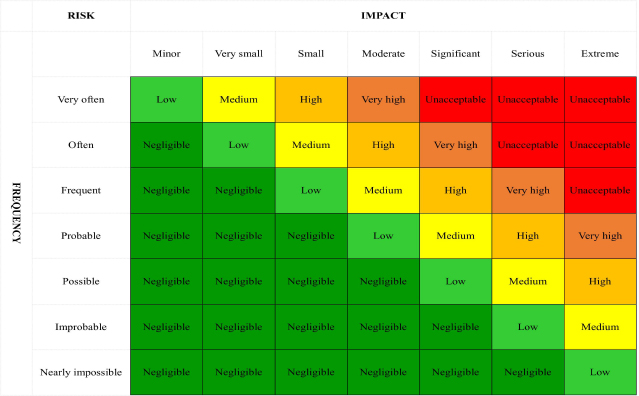
Risk matrix [16].
Author (Year)/Refs | Number of Factors | Type of Construction | Point of View |
---|---|---|---|
Abduljawwad & Almaktoom (2021) [28] | 13 | General study includes all types of projects* | Contractors |
Ahmad et al. (2023) [31] | 14 | General study* | Project engineers, project staff, project managers, construction managers, construction directors, and of project directors |
Albogamy et al. (2012) [18] | 62 | General study* | Owners, contractors, and consultants |
Al-Emad et al. (2017) [22] | 10 | General study* | Manager, Engineer, Technical Staff |
Alharbi (2020) [27] | 47 | Housing construction projects | Client, consultants and contractors |
Alotaibi (2018) [24] | 20 | Public construction | Project Manager, Engineering Consultant, Engineering Supervisor, Site Engineer, Others |
Alshibani et al. (2022) [30] | 11 | Oil and gas pipeline construction | Experts |
Alshihri et al. (2022) [29] | 76 | Building projects | Owner/ government agency, Designer, Consultant, Contractor, Others |
Assaf et al. (2019) [1] | 25 | General study* | Professionals |
Elawi (2016) [20] | 7 | Road and bridge project | Owners |
Elawi et al. (2016) [20] | 20 | Road and bridge project | Owners |
Gopang et al. (2020) [26] | 34 | Railway/ metro construction projects | Experts |
Mahamid (2013) [19] | 31 | Public construction | Owners |
Mahamid (2016) [21] | 56 | Residential building projects | Contractors |
Mahamid (2017) [23] | 33 | Road construction projects | Contractors |
Mathar et al. (2020) [25] | 28 | Large building construction projects | Experts |
There are two internal factors with an importance value of more than 50.00%, i.e., consultant/supervisor-related and contractor-related factors. The external factors include equipment-related and owner- or client-related factors. The recalculated importance index for the delay factor (Table 5) then found that the equipment-related factors, i.e., equipment shortages, have the highest importance value of 55.06%. On the other hand, the shortage of labor (inadequate crew size) has the lowest importance (50.10%).
The difficulties in financing the project by the contractor (cash flow problems) were found to have the highest frequency of delay. This highlights the significant impact of financial challenges on construction projects in Saudi Arabia, leading directly to delays. Similar findings emerged in a Nigerian study by Omopariola et al. [32], where financial constraints were identified as the primary cause of construction delays. Cash flow issues during construction projects often stem from inadequate budgetary control, difficulty securing funding, and payment delays, hindering contractors' ability to complete their work on time. Another study by Androod and Bamdad [33] proposed a finance-based scheduling model that can lower financing costs. The model considers various funding options like credit cards, long-term loans, and short-term loans. The model will also decrease the project duration, which will lower the risk of delays or abandonment.
The high frequency of “changes to the project by the owner” (Table 3) indicates a significant impact of frequent owner-initiated modifications on project timelines. Similar findings were reported by Hatmoko et al. [34], in Indonesia, who identified five key owner-related delay factors: site acquisition issues, design and work instruction modifications, payment problems, and ambiguous contract drawings. These factors resulted in financial losses for contractors, with an average claim success rate of only 53% despite attempts to recoup these losses. Another study by Das and Emuze [35], in India also found client-owner related factors contributing to delays, including slow decision-making, mid-construction order changes, poor communication and coordination, late design and document revisions, and delays in site handover. They emphasized the importance of prompt decision-making supported by readily available data and clear communication to ensure timely payments and minimize delay risks.
Categories | Factors | Frequency (%) |
---|---|---|
Contractor-related factors | Difficulties in financing the project by contractor (cash flow problems) | 72.16 |
Owner/client-related factors | Changes to the project by owner | 60.45 |
Government-related factors | Low performance of the lowest bidder contractor in the Government Tendering System | 56.88 |
Designer-related factors | Unclear and inadequate drawings, specifications, bills of quantities (BOQ) | 52.87 |
Other external-related factors | Poor communication and coordination with other parties | 51.00 |
Owner/client-related factors | Delay of financing and payments by owner | 50.47 |
However, poor communication and coordination with other parties has the highest severity rating, indicating a need for immediate attention and actions to improve communication and coordination among the industry players. Similar results were also found in a Jordanian construction industry study by Akram et al. (2023) [36], which identified poor communication as a major contributor to cost overruns, stakeholder misunderstandings, and frequent design and schedule changes. Factors contributing to poor communication often include varying educational backgrounds among stakeholders, the absence of a communication plan, and information delays. Another study by Yaser et al. [37] also found that poor communication significantly impacts project time and cost overruns. Their study further showed that implementing advanced communication systems and information communication technologies can mitigate the severity of these overruns.
Categories | Factors | Severity (%) |
---|---|---|
Other external-related factors | Poor communication and coordination with other parties | 58.97 |
Force majeure risk-related factors | Weather factor (heat, food, etc.) | 57.06 |
Equipment-related factors | Equipment shortages | 55.06 |
Contractor-related factors | Deficiency in planning and scheduling of project | 54.31 |
Consultant/supervisor-related factors | Lack of supervisor consultant experience and wrong approval | 54.26 |
Owner/client-related factors | Lack of coordination with contractors | 53.36 |
Labor-related factors | Shortage of labors (Inadequate crew size) | 52.72 |
Categories | Factors | Importance value (%) |
---|---|---|
Equipment-related factors | The equipment shortages factor | 55.06 |
Contractor-related factors | Deficiency in planning and scheduling of project | 54.00 |
Consultant/supervisor-related factors | Lack of supervisor consultant experience and wrong approval | 54.00 |
Owner/client-related factors | Changes to the project by owner | 51.58 |
Owner/client-related factors | Lack of coordination with contractors | 50.40 |
Equipment-related factors | Shortage of labors (Inadequate crew size) | 50.10 |
Following “poor communication and coordination with other parties” as the most severe factor (Table 4), force majeure risks related to weather also exhibit a high severity rating. This highlights the significant contribution of weather events to construction delays. A review by Schuldt et al. [38] on weather-related delays in a changing climate confirms this finding. Their analysis, spanning 1972 to October 2020, identified extreme temperatures, precipitation, and high winds as the most impactful weather factors. These changing weather conditions not only disrupt construction progress but also affect the properties of construction materials like concrete, asphalt, brick, steel, and soil.
The current study identifies “shortage of equipment” as the factor with the highest importance, highlighting the critical need for proper equipment maintenance and sufficient allocation to prevent construction delays in Saudi Arabia. Equipment shortages are not unique to Saudi Arabia, as evidenced by a study in Nepal by Bhattarai [39]. This study identified equipment shortages as one of the top three critical factors leading to construction delays, alongside material and labor shortages. These delays can have significant negative impacts on a country's economic growth and development, hindering access to essential services, obstructing trade and commerce, and driving up costs. Similar findings were reported by El Sayed et al. [40] in Bosnia and Herzegovina, where equipment shortages were identified as one of eight critical delay factors. They proposed to use different approaches to project planning and scheduling to mitigate these issues. These combined findings emphasize the need to address equipment shortages not only in Saudi Arabia but also in other regions to ensure sustainable development and economic growth.
3.2. The High-Risk Factors Contributing to Construction Project Delay
The risk assessment identified seven factors categorized as “unacceptable risk” (Table 6). These factors include delays due to material delivery, approval of submittals (design drawings, shop drawings, and sample materials), subcontractor work, inflation and material price escalation, lack of coordination with contractors, construction material shortages, and equipment shortages. Their placement in the red zone of the risk matrix signifies an extremely high impact and frequency, demanding top priority and intensive mitigation efforts.
Table 6.
Categories | Factors | Risk |
---|---|---|
Construction site or work environment related factors | Disputes on site | High |
Problems with neighbors | Medium | |
Consultant/ supervisor-related factors |
Absence of consultant's site staff | High |
Insufficient data collection, work preparation and drawing details | Medium | |
Mistakes or discrepancies in documents or specifications issued by consultants | High | |
Poor estimate of task duration and scheduling | Medium | |
Poor management of the site and lack of distribution of tasks | Medium | |
Contractor-related factors | Delay in the preparation of contractor document submissions | Medium |
Delay related to sub-contractors’ work | Unacceptable | |
Poor controlling of subcontractors by contractors (relationships, payments) | High | |
Rework due to errors during construction by contractors | High | |
Designer-related factors | Complexity of design | High |
Delay in approval of submittals, design drawings, shop drawings, and sample materials (making decisions) | Unacceptable | |
Design errors | High | |
Designing delay | Medium | |
Equipment-related factors | Equipment availability and failure | High |
Inadequate equipment on site | High | |
Equipment shortages | Unacceptable | |
Force majeure risk-related factors | Weather factor (heat, food, etc.) | Medium |
Labor-related factors | Lack of motivation (Low payment for labor force) | Medium |
Poor manpower productivity (Workers used for longer hours) | Medium | |
Strike | Medium | |
Unqualified and unskilled workforce | High | |
Material related factors | Delay due to material delivery | Unacceptable |
Delay in test samples of material | Medium | |
Shortage of construction materials (non-availability of material) | Unacceptable | |
Other external-related factors | High fluctuation in cost (e.g., money exchange rate; taxes and burdens; and interest rates charged by bankers on loan) | High |
Inflation and escalation of material prices (Changes in prices) | Unacceptable | |
Owner / client related factors | Changes in the scope of the project (additional work) | High |
Lack of coordination with contractors | Unacceptable | |
Poor communication and coordination with other parties | Medium | |
Short contract duration | High |
An additional thirteen factors were classified as “high-risk,” including the absence of the consultant's site staff, changes in the scope of the project, complexity of design, design errors, disputes on site, equipment availability and failure, high fluctuation in cost, inadequate equipment on site, mistakes or discrepancies in documents or specifications issued by consultants, poor control of subcontractors by contractors, rework due to errors during construction by contractors, short contract duration, and an unqualified and unskilled workforce. These factors indicate the need for monitoring and mitigating actions.
The risk assessment identified several factors demanding immediate attention due to their “unacceptable risk” categorization (Table 6). These include delays in material delivery, submittal approvals (design drawings, shop drawings, and samples), subcontractor work, and a lack of coordination with contractors. Additionally, inflation, material price escalation, construction material shortages, and equipment shortages all contribute to this high-risk category. A study by Kurniawan and Anggraeni [41] in Indonesia supports these findings, identifying late material delivery as the riskiest factor in regional construction projects. Similarly, Rachmawati et al. [42] found that power plant projects in Indonesia face critical risks from inexperienced labor, material and equipment logistics delays, inadequate communication, local material shortages, and incomplete material deliveries. It was recommended that all industry players improve the requirements for open positions, hold frequent training or informational meetings prior to project implementation, and keep an emergency supply of spare components to minimize the risks.
Conversely, high-risk factors such as construction site or work environment, consultant/supervisor, contractor, designer, equipment, labor, owner/client, and other externally related factors warrant close monitoring. A study by Hayati et al. [43]. supports this view, identifying labor, resources, and design/technology as the top three risks plaguing the construction industry. Similarly, Nga and Tuan [44]. found that Vietnamese construction projects face significant risks from flawed design, payment delays, funding issues, poor contractor performance, inadequate materials, slow site clearance, unverified contractor finances, and safety concerns. They emphasize the importance of implementing effective risk management strategies to minimize the impact of these factors on ongoing projects.
3.3. Strategies to Mitigate the Construction Project Delays
Critical factors that can cause delays in construction projects include unskilled or inexperienced labor, delays in the logistics of materials and equipment, poor coordination and communication, a shortage of materials in the local market, and incomplete deliveries of materials. These can be mitigated by implementing stricter recruitment procedures to ensure qualified labor, holding frequent meetings or training sessions, and keeping an emergency supply of spare parts to minimize disruptions [42].
The risk assessment can be effectively conducted using the Bowtie diagram and scenario analysis [43]. These practical tools serve to guide the risk management and decision-making processes. The Bowtie diagram offers a visual representation of the interrelationships between potential hazards, their causes, and resulting consequences. This clear illustration of risks and potential outcomes facilitates informed decision-making regarding mitigation strategies. Concurrent application of scenario analysis further aids in understanding and evaluating the risks and repercussions associated with potential situations, such as fluctuations in market conditions, regulatory changes, and project variable deviations.
Risky conduct is a labor-related factor contributing to industrial accidents and subsequent construction project delays. A study by Guo et al. [45], in China highlights the limitations of traditional risk matrix methods in quantifying risky conduct within the construction industry. They propose a Modified Risk Matrix (MRM) that facilitates quantitative analysis for identifying risks associated with different accident types. This method enables the prediction of potential accidents stemming from identified risky behaviors, allowing for the implementation of preventative measures.
Another study by Rajendra and Aher [46], in India focused on the application of Monte Carlo simulation (MCS) to evaluate the impact of risks on construction schedules. This technique utilizes random sampling to perform multiple simulations, generating a range of potential outcomes based on various input factors and their associated probability distributions. The study further employed sensitivity analysis to evaluate the influence of uncertain activities on the overall project timeline. The findings confirmed that MCS can accommodate diverse distribution forms within individual actions. Additionally, the study revealed that using larger sample sizes in MCS can yield less optimistic (i.e., more realistic) results.
Various risk assessment tools can be integrated into a structured approach to implement mitigation strategies for Saudi Arabian construction projects. This five-step approach involves five steps, including identifying and assessing risk, developing a mitigation strategy, selecting and prioritizing a strategy, implementing and monitoring, and continuous improvement. The first steps to identify and assess risk can be conducted through workshops with key stakeholders. The MRM methodology, suggested by Guo et al. [45], can be used to identify potential risks. Based on the identified risks, specific mitigation strategies should be developed for each one. Mitigation strategies are then evaluated based on factors like cost, feasibility, and alignment with project objectives. Strategies addressing high-severity and high-likelihood risks should be prioritized. An implementation plan needs to be developed for each prioritized strategy. This plan should consider all stakeholders involved, timelines, and resource allocation. The mitigation strategies can then be integrated into existing project management processes. Regular monitoring of each implemented strategy is crucial throughout the project lifecycle. The MCS methodology, as suggested by Rajendra and Aher [46], can be a valuable tool for this purpose. The progress and effectiveness of each mitigation strategy need to be documented. Lessons learned throughout the project can then be used to continuously improve future risk identification and mitigation processes.
CONCLUSION
A review of 16 articles identified 140 factors contributing to delays in the Saudi Arabian construction projects. The findings showed that seven factors are considered unacceptable, whereas ten factors are considered high-risk factors. The unacceptable factors were delay due to material delivery, delay in approval of submittals, design drawings, shop drawings, and sample materials (making decisions), delay related to sub-contractors’ work, inflation and escalation of material prices (changes in prices), lack of coordination with contractors, shortage of construction materials (non-availability of material), and equipment shortages. Material and equipment shortages are identified as one of the most critical factors in the Saudi Arabian construction industry. There is a need to improve or promote a reliable and efficient supply chain in the nation. Communication and coordination issues among stakeholders also have a significant impact on the construction industry. There is a need for policies and regulations to promote communication tools among stakeholders. The findings also identify a need for a skilled workforce. This suggests a need for vocational training and upskilling within the industry.
The findings highlight the need for future studies to define the construction delay factors in the recently completed projects in the region. The inconsistent methods used in past studies make it challenging to collect data. Ideally, the significance of delay factors needs to be determined through actual construction projects instead of being extracted from articles. Nonetheless, the literature review offers an area to start while attempting to understand how experts interpret the delay factors. It helps to identify the common delay factors, establish a baseline for the factor’s importance, and highlight areas for future research. This necessitates standardized data collection across construction projects in Saudi Arabia. With sufficient data, policymakers can develop an effective mitigation plan.
Furthermore, efforts should focus on creating a risk management model or framework specifically tailored to address the issues of construction delays in Saudi Arabia. These will lessen the effects of the delay factors connected to building projects in Saudi Arabia and lead to reduced project costs, improved completion time, and increased success rates. The risk assessment can be conducted using the Bowtie diagram, scenario analysis, MRM, and MCS separately or collectively to get a new and improved model. The model should undergo case study trials and be validated by specialists in the Saudi Arabian building industry. Policymakers could also introduce several training programs or certifications to better equip industry players with risk management skills.
The current study also identified several gaps, such as collecting and analyzing various project types and sizes under one study. Future studies should investigate significant differences in delay factors between project types and sizes. The current study also suggested a risk management model or framework to address the issues of construction delays in Saudi Arabia. However, there is potential for future studies to delve more into this subject and develop a new framework that can be tailored to the current needs of Saudi Arabia.
AUTHORS' CONTRIBUTIONS
It is hereby acknowledged that all authors have accepted responsibility for the manuscript's content and consented to its submission. They have meticulously reviewed all results and unanimously approved the final version of the manuscript.
LIST OF ABBREVIATIONS
APAC | = Asia Pacific |
MEA | = Middle East/Africa |
MCS | = Monte Carlo simulation |
AVAILABILITY OF DATA AND MATERIALS
The data supporting the findings of this article are not currently publicly available due to privacy concerns. However, the data will be made available upon reasonable request from the corresponding author.
ACKNOWLEDGEMENTS
The authors would like to acknowledge the School of Civil Engineering, Universiti Sains Malaysia (Engineering Campus), for their support in producing and publishing this review study. We would also like to extend our gratitude to the Editor(s) and anonymous reviewers, whose comments and feedback significantly contributed to this work.