All published articles of this journal are available on ScienceDirect.
Evaluation of the Performance of Concrete Reinforced with Bamboo and Incorporating Cassava Peel Ash
Abstract
Introduction
The main materials utilized in the production of reinforced concrete are aggregates, cement, and steel. The production of steel and cement contributes to the generation of carbon dioxide emissions, which is a main cause of global warming.
Methods
To further enhance sustainability in the construction industry, this study focuses on utilizing alternative sustainable materials in bamboo-reinforced concrete containing cassava peel ash (BRC-CPA) by fully replacing steel with bamboo strips and partially replacing cement with cassava peel ash. The experimental phase includes material characterization for the cassava peel ash (CPA) and bamboo reinforcements. Eighty-nine samples of BRC-CPA beams with dimensions 100×150×500 mm were produced, and bamboo strips of three different sizes, 12, 14, and 16 mm, were prepared and used as reinforcement in the BRC-CPA beams to evaluate their flexural strength and flexural strain. In addition, 12 samples of 150 mm cassava peel ash-blended concrete (CPAC) cubes without bamboo strips were produced. The cassava peel ash was used to partially replace cement at three levels, 0, 10, and 20%, to evaluate their influence on the compressive strength and water absorption of concrete cube samples.
Results
The addition of CPA slightly reduced the compressive strength of CPAC cubes, with values of 23.4 N/mm², 22.2 N/mm², and 21.4 N/mm² observed for 0%, 10%, and 20% CPA replacement levels, respectively. However, incorporating CPA had a positive effect by reducing water absorption and narrowing the flexural crack width in BRC-CPA beams. The flexural strength of BRC-CPA beams increased as the concrete aged, but decreased as the bamboo reinforcement size increased. Notably, at 20% CPA replacement, the flexural strength was less influenced by the bamboo strip size compared to beams with 0% CPA.
Conclusion
Based on experimental results obtained for compressive strength, flexural strength, and flexural crack width, cassava peel ash at 10% replacement and bamboo strips of size 14 mm were recommended for use in BRC-CPA for concrete structural elements such as beams, columns, and slabs.
1. INTRODUCTION
Concrete can be defined as a combination of constituent materials, including coarse aggregate, fine aggregate, cement and water. Concrete possesses excellent compressive strength, while its brittle nature makes it weak under tension. To overcome this weakness, a reinforcement is to increase its tensile, and flexural strengths, as well as its toughness. Since concrete is a widely spread material for construction due to the availability of raw materials, it has evolved through centuries and it keeps evolving as long as innovations and inventions are made. This evolution is needed to accompany the revolution the building sector is undergoing to achieve good mechanical and durability properties. The need for sustainability in concrete production has been on the rise, it is, therefore, important to focus on the changes in constituent materials used in concrete production to make it more sustainable [1]. Various types of waste have been introduced into concrete mix to ensure sustainability [2-4]. These waste materials, including blast furnace slag (BFS), fly ash (FA), silica fume and agro-based ash, are usually used as supplementary cementitious materials (SCM) and they result in alteration of concrete durability and mechanical properties when compared to that of conventional concrete. In addition, the adoption of bamboo strips as reinforcement in concrete has been advocated based on research findings. To ensure that concrete structures with these materials (bamboo strips and CPA) are safe and meet design standards, there is a need to carry out performance evaluations on the concrete produced with them.
Ash from Agro-based products, including rice husk ash (RHA), sugarcane straw ash (SSA), and groundnut husk ash (GHA), have been used by some notable researchers as pozzolans in concrete [5-7]. The use of these ashes has been observed to improve the workability of green concrete [8]. Recently, cassava peel ash (CPA) attracted the attention of both engineers and researchers due to its availability in Southeast Asia and the Western part of Africa, with 296 million tons produced in 2020 [9]. Peeling cassava tubers yields cassava peels, constituting a significant portion, typically ranging from twenty to thirty-five percent, especially when removed manually [10]. The production of cassava peels surged to around twelve million tons in 2020, with Nigeria alone generating over 14 million tons annually [11]. Unfortunately, the improper disposal of cassava peels, resulting from their under-exploitation and the absence of sufficient means to handle them, poses a challenge, leading to substantial environmental pollution. This situation underscores the critical need to find improved management approaches. Notably, a study by Salau [12] found that when cassava peels are subjected to calcination at 700 °C for ninety minutes, they exhibit notable pozzolanic potential, meeting the minimum requirements of 70% combination of silicon, aluminium and iron oxides. According to Maddalena et al. [13], the use of alternative environmentally friendly materials in producing concrete will help reduce CO2 emission into the atmosphere and consequently lessen the effect of global warming that endangers the environment.
Moreover, concrete has little or no tensile strength, which informs the introduction of steel to reinforce it. The ever-increasing cost of steel and the need for sustainability has led to the search for alternatives and bamboo fits into this category due to its high tensile strength and renewable nature [14, 15]. The tensile strength of bamboo has been investigated and was found to be as high as 370 N/mm2 [16], and it also has tensile strength to unit weight ratio that is six times higher than that of steel [17]. With this, bamboo has become a viable replacement for steel in tensile loading applications [18]. The incorporation of bamboo, a locally made material as steel replacement in concrete is likely to solve the problem of housing, especially in developing countries with more low-cost residential buildings. Falade and Akeju [19] discovered that bamboo is a better and cheaper substitute for steel in beams and columns in low-cost houses due to its comparative advantages over steel reinforcement in terms of economy and weight. It’s cheaper and locally sourced, not susceptible to corrosion, and its inclusion in plain concrete beams increases the load-carrying capacity of the beam. It was identified that the use of bamboo would reduce the cost of reinforcement by 30 percent depending on the design, location of the site and other variables [20]. Similarly, Agarwal et al. [21] and Kumar et al. [22] have all proved the need to provide at least minimal bamboo reinforcement as well as an adequate surface treatment to improve binding. Kumar et al. [22] discovered that beams reinforced with 3% split bamboo had four times the ultimate capacity of equivalent unreinforced concrete beams. Bamboo can be used as a steel reinforcement substitute in concrete when subjected to irregular cycle loads [23]. According to Alade et al. [24], the typical strength of bamboo is between 204 and 250 N/mm2, which is equal to that of mild steel. Another study by Siddika et al. [25] observed an average tensile strength of 105 MPa, while Qaiser et al. [26] observed tensile strength varied between 76 MPa and 90 MPa. The variability in strength can be largely attributed to the different bamboo species and maturity [27]. Bhagat et al. [28] investigated various designs for fibre reinforced bamboo composites (FRBC) in different structural elements such as columns, beams, portal frames, and joints tested under varying stresses. The FRBC demonstrated appropriate behaviour and weight-carrying capacity.
After a thorough review of literature, it was observed that there is no information on using CPA as a supple- mentary cementitious material in bamboo-reinforced concrete. It is, therefore, worthwhile for this study to investigate the performance of this novel concrete containing a blend of bamboo strips and cassava peel ash to understand its mechanical and durability properties. The output of this research will help to find a good alternative to steel with the use of bamboo as reinforcement and partially replace cement with agro-based materials such as CPA, thereby achieving sustainability in the construction industry, reducing environmental pollution and overall, producing a green concrete with similar conventional concrete’s mechanical strength properties. This study is in concordance with numerous published works that delve into the examination of the structural, dynamic, and fracture behaviour of bamboo [29, 30], as well as the employment of bamboo in bio-composite laminates [31].
2. METHOD
2.1. Material and Testing Methods
2.1.1. Binder Material
The study employed the Dangote brand of Portland limestone cement with a grade of 42.5 MPa alongside cassava peel ash as binding agents. The cassava peel ash was obtained through a systematic process, commencing with the collection of cassava peels from the agricultural holdings of Landmark University in Kwara state, Nigeria. Subsequently, these peels underwent sun-drying and were subjected to calcination at 800 °C for a duration of two hours, utilizing a Thermolyne furnace. The resulting ash was meticulously sieved and further refined using a ball milling machine to achieve the requisite particle size, finer than sieve number 200 (75 µm).
The chemical composition and morphology of the CPA were determined through XRF and SEM analysis tests. It can be seen that CaO and SiO2 are the primary oxides in CPA, and the combination of the percentage weight of SiO2, Fe2O3, and Al2O3 is more than 70%, thereby meeting the specified criteria by ACI 211 standard [32] for pozzolanic material. The chemical composition of CPA is presented in Table 1. Furthermore, the SEM images of CPA in Fig. (1) show that CPA has irregular particles with a smooth surface and fibrous cavities (or pores) at the magnification of × 2000. The pore diameter of these cavities varied between 41 μm and 57 μm and these cavities generally did not intersect each other. The pore opening sizes could affect the workability of fresh concrete since it would mean a tendency to absorb water.
2.1.2. Aggregates
River sand with particle sizes ranging between 0.15 - 1.18 millimetres was used as the fine aggregate in this study. The fine aggregate was sundried, cleaned, and free of any silt or clay impurities. The coarse aggregates (NCA) have a diameter greater than 4.75 mm but generally range between 4.75 mm to 18.5 mm. It is angular shaped with fine stone dust sparingly scattered in it and sourced from a quarry site in Omu-Aran, Nigeria. The sieve analysis of the aggregate is presented in Fig. (2).
Chemical Composition (%) | SiO2 | Al2O3 | Fe2O3 | K2O | CaO | SO2 | P2O5 | Ag2O | MgO | Y2O3 | Nb2O5 | Cl | TiO2 | Na2O | V2O5 |
---|---|---|---|---|---|---|---|---|---|---|---|---|---|---|---|
CPA | 39.26 | 16.98 | 14.76 | 4.36 | 5.03 | 4.54 | 4.88 | 1.58 | 2.42 | 1.57 | 1.58 | 1.05 | 1.39 | 0.3 | 0.29 |
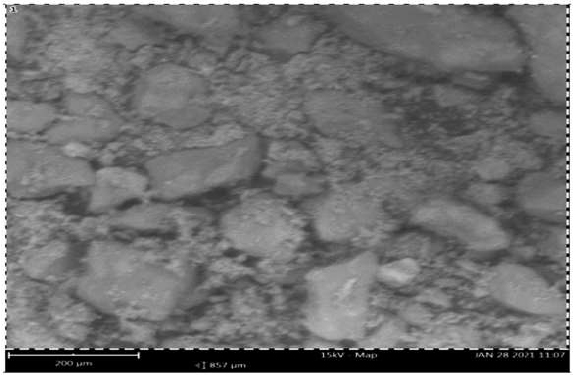
SEM Image of cassava peel ash showing its microporous nature. Magnification of 2000×.
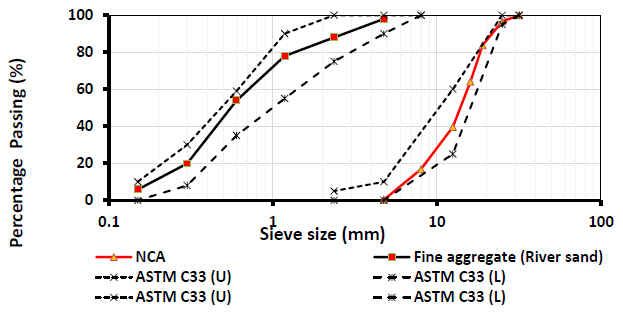
Particle size distribution of fine and coarse aggregate.
2.1.3. Bamboo Reinforcement
The bamboo strips that were used as replacements for steel reinforcement were processed into strips with widths of 12 mm, 14 mm and 16 mm sizes. The thickness of the bamboo strip was about 4 ± 0.2 mm. The bamboo strips were coated with bitumen to ensure proper bonding with concrete and to prevent moisture penetration (Fig. 3). The tensile strength test conducted on the bamboo strips showed that 12mm, 14mm and 16 mm size has tensile strengths of 145.73 N/mm2, 181.25 N/mm2 and 158.60 N/mm2, respectively. From these results, it could be inferred that bamboo can be a viable alternative for steel reinforcement in sustainable construction since the tensile strength values obtained were close to that of mild steel reinforcement. Fig. (4) shows the load versus elongation curve recorded for the tensile strength test for different bamboo sizes; the obtained tensile strength values are presented in Table 2. The average modulus of elasticity of bamboo strip determined based on the secant modulus from the bamboo stress strain curve was 27000 MPa.
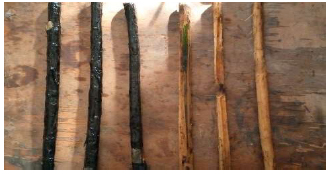
Samples of coated and un-coated processed bamboo strips used as reinforcement.
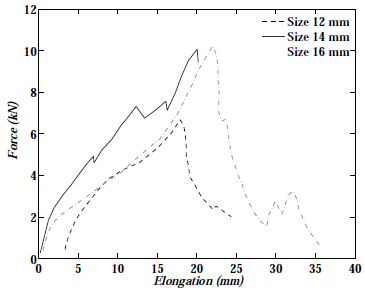
Load and elongation curve for different bamboo sizes (a) 12 mm (b) 14 mm (c) 16 mm.
Width of Bamboo (mm) | Bamboo Thickness | Area (mm2) | Maximum Force (N) | Elongation at Break Point (mm) | Tensile Strength (N/mm2) |
---|---|---|---|---|---|
12 | 4 | 48 | 6995 | 24.525 | 145.73 |
14 | 4 | 56 | 10150 | 20.294 | 181.25 |
16 | 4 | 64 | 10150 | 35.852 | 158.60 |
Mix ID | % Ash | Bamboo Size (mm) | Cement (kg/m3) | CPA (kg/m3) | Fine AggregateSharp Sand (kg/m3) | Coarse Aggregate (kg/m3) |
---|---|---|---|---|---|---|
CPA Beams | ||||||
C0-12 | 0 | 12 | 750 | 0 | 990 | 660 |
C0-14 | 0 | 14 | 750 | 0 | 990 | 660 |
C0-16 | 0 | 16 | 750 | 0 | 990 | 660 |
C10-12 | 10 | 12 | 675 | 75 | 990 | 660 |
C10-14 | 10 | 14 | 675 | 75 | 990 | 660 |
C10-16 | 10 | 16 | 675 | 75 | 990 | 660 |
C20-12 | 20 | 12 | 600 | 150 | 990 | 660 |
C20-14 | 20 | 14 | 600 | 150 | 990 | 660 |
C20-16 | 20 | 16 | 600 | 150 | 990 | 660 |
CPA Cubes | ||||||
CPA -0 | 0 | - | 750 | 0 | 990 | 660 |
CPA -10 | 10 | - | 675 | 75 | 990 | 660 |
CPA -20 | 10 | - | 660 | 150 | 990 | 660 |
2.2. Mix Proportions for Bamboo Reinforced Concrete Containing CPA
The mix design of the concrete was carried out following ACI 211.1 standard [32], and the proportion of each constituent material in the mix was estimated as presented in Table 3. The concrete mixture was prepared at a constant w/c ratio of 0.55 and the CPA was used to partially replace cement at 0, 10 and 20% replacement levels. Aggregates and cement were first batched into the rotating concrete mixer before water was added. The mixer continued for about 3 minutes to allow for proper mixing. The concrete mixture blended with CPA was then cast into the rectangular moulds of size 100×150×500 and bamboo strips of different sizes, 10, 12 and 16 mm were placed as reinforcement at 75 mm spacing to produce the BRC-CPA beams. Also, the concrete mixture blended with CPA was used to cast concrete cubes of 100 mm without any bamboo strips to produce the CPAC cubes. All the samples were allowed to remain in the moulds for 24 hours before being de-moulded and cured in water by immersion for 28 days. Fig. (5) shows the schematic section view of the cast bamboo reinforced concrete beam. This Figure clearly illustrates the spacing of reinforcement in the longitudinal or transverse directions and Fig. (6) shows samples of concrete cubes and bamboo reinforced concrete beams used for compressive strength and flexural strength tests, respectively. For each Mix ID a minimum of nine samples were prepared to cater for the three test ages of 28, 56 and 90 days considered. For the compressive strength test at 28 days, a minimum of three samples was prepared.
2.3. Test Methods
The workability of the fresh concrete was evaluated using the cone slump test according to ASTM C143 [33]. The difference in height between the cone and the deformed concrete is the measured slump value of the concrete mixture. Water absorption test was carried out on coated and non-coated bamboo strips to evaluate the efficiency of the bitumen coating on the bamboo strips. The compressive strength of each CPAC cube specimen was determined through a compression test by loading the specimen to failure; the maximum axial load at failure of CPAC specimens was divided by the total surface area to estimate the ultimate compressive strength. The ultimate flexural strength, referred to as the modulus of rupture, was determined for the BRC-CPA rectangular beam specimens utilizing the center point loading method in accordance with the British standard EN BS 12390-5: 2009 [34] standard. Fig. (7) illustrates the flexural test method adopted in the study. Throughout the testing process, careful observation was conducted to monitor the initiation of the first fracture and subsequent crack propagation, leading to failure. Upon specimen failure, the maximum load displayed was recorded. Additionally, the distance between the crack line and the nearest support was measured and documented. The modulus of rupture was subsequently calculated using Eq. (1).
![]() |
(1) |
Where:
MR= Modulus of Rupture (N/mm2),
P = maximum load (N),
L = distance between supporting rollers (mm),
b = width of beam (mm),
d = depth of beam (mm).
3. RESULTS AND DISCUSSION
3.1. Slump Test
Table 4 shows the slump values obtained at different CPA replacement levels in the concrete mixture. It can be observed that the slump value reduces as CPA increases, indicating reduced workability. This can be attributed to the porous structure of CPA which absorbs more water during concrete mixing.
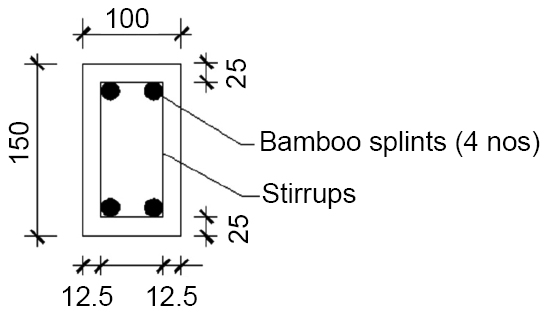
The schematic section view of the concrete with bamboo reinforcements. Note: All dimensions in (mm).
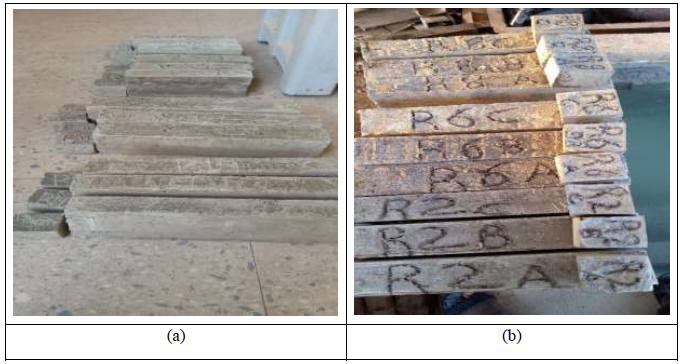
Samples of 100 mm concrete cubes and bamboo reinforced beams of 100×150×500 mm.
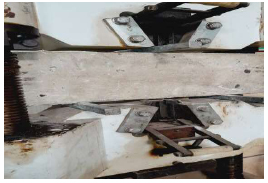
Beam under flexural loading.
Sample ID | CPA-0 | CPA-10 | CPA-20 |
---|---|---|---|
Weight of fully compacted concrete (kg) | 16.5 | 17.0 | 18.1 |
Slump Value (mm) | 60 | 40 | 32 |
% CPA | Bulk Density (kg/m3) |
---|---|
0 | 2300 |
10 | 2266 |
20 | 2219 |
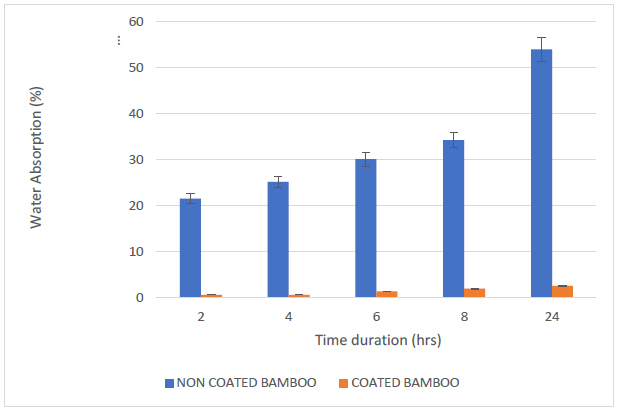
Water absorption test on bamboo strips.
3.2. Water Absorption
Fig. (8) shows the results of the water absorption test on coated and non-coated bamboo strips in order to validate the functionality of the bitumen coating. From the result obtained, the bitumen coating was found to be very effective in preventing moisture penetration into the bamboo as the rate of water absorption by the bamboo strips reduces drastically after bitumen coating. The water absorption for non-coated bamboo increased from 21.56% and 54.03% for 2hrs and 24hrs soaking, respectively while that of coated bamboo strips increased from 0.59% and 2.53% for the same time duration.
3.3. Density of Hardened Concrete
Table 5 shows the variation in bulk density of CPA blended concrete at different cassava peel ash content levels. The bulk density of CPA blended concrete reduces as the percentage of CPA increases in the mix. However, all the values obtained still fall within the range of 2000 – 2400 kg/m3 as specified by BS 8110 [35] for concrete.
3.4. Compressive Strength
The result of the 28 days compressive strength of CPA is presented in Fig. (9) and it shows the compressive strength of 23.4, 22.2 and 21.4 N/mm2 at CPA replacement levels of 0, 10 and 20%, respectively. Although a decreasing trend was observed, the values obtained still meet the required strength for grade 20 concrete at all tested CPA replacement levels, indicating that the addition of CPA at 10 and 20% replacement levels did not have a significant negative effect on concrete compressive strength.
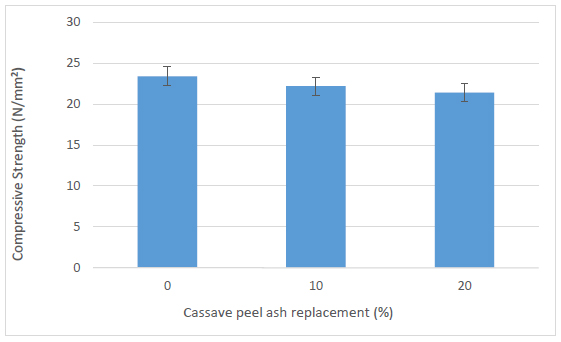
Compressive strength of CPA blended concrete.
3.5. Flexural Strength
The values of flexural strength for the BRC-CPA beams at 28-, 56-, and 90-days’ strength are presented in Table 6 and plotted in Fig. (10). The flexural strength of BRC-CPA samples generally increased with curing age. However, the rate of increase in flexural strength of BRC-CPA samples with 10 and 20% CPA content from 28 to 90 days is higher when compared to those without CPA. An average increase in flexural strength of 10, 43, and 37% was observed in bamboo reinforced concrete containing 0, 10, and 20% CPA replacements, respectively, from 28 to 90 days, indicating better flexural strength gain with curing age with the addition of CPA. This can be attributed to the pozzolanic properties of CPA. CPA reaction with cement yielded more CaO hydrated product which enhances strength development and improves the interfacial transition zone (ITZ) in bamboo reinforced concrete containing CPA. Also, from Fig. (11), the flexural strength of BRC-CPA with 0% CPA addition slightly decreased as the bamboo reinforcement size increased. The average flexural strength values for C0-12, C0-14, and C0-16 samples were 11.8, 10.5 and 10.0 N/mm2 for bamboo sizes of 12, 14, and 16 mm, respectively at 90 days’ concrete age. Whereas, for BRC-CPA with 10 and 20% CPA levels, the observed reduction in flexural strength with increased Bamboo size diminished as CPA content increased. C20-12, C20-14, and C20-16 samples have a relatively close flexural strength of 7.1, 6.9, and 6.8 MPa with 12 mm, 14 mm, and 16 mm Bamboo reinforcement sizes, respectively at 90 days’ concrete age. This shows that the flexural strength of BRC-CPA beams at 20% CPA levels is not significantly affected by bamboo size compared to that of 0 and 10% CPA content. A similar result was obtained in the study of Cao et al., [36] where they concluded that the flexural strength of high-performance steel reinforced concrete is not affected by changes in steel reinforcement size.
Mix ID | Cassava Peel Ash (%) | Bamboo Size (mm) | Average Flexural Strength (MPa) | ||
---|---|---|---|---|---|
28 days | 56 days | 90 days | |||
C0-12 | 0 | 12 | 11 | 11.5 | 11.8 |
C0-14 | 0 | 14 | 9.5 | 10.1 | 10.5 |
C0-16 | 0 | 16 | 9 | 9.8 | 10 |
C10-12 | 10 | 12 | 5.9 | 7.1 | 8.4 |
C10-14 | 10 | 14 | 5.7 | 6.7 | 8.1 |
C10-16 | 10 | 16 | 5 | 5.8 | 7.3 |
C20-12 | 20 | 12 | 5.4 | 6.6 | 7.1 |
C20-14 | 20 | 14 | 5 | 6.5 | 6.9 |
C20-16 | 20 | 16 | 4.8 | 6 | 6.8 |
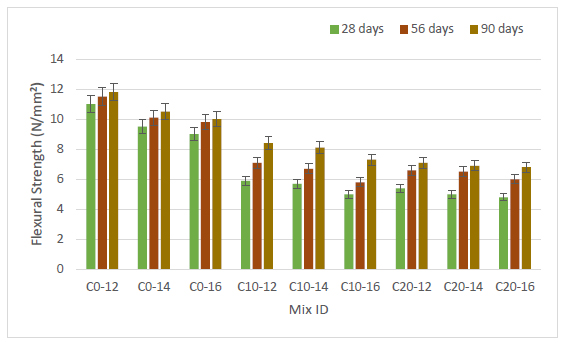
Flexural strength of CPA blended bamboo reinforced concrete beam.
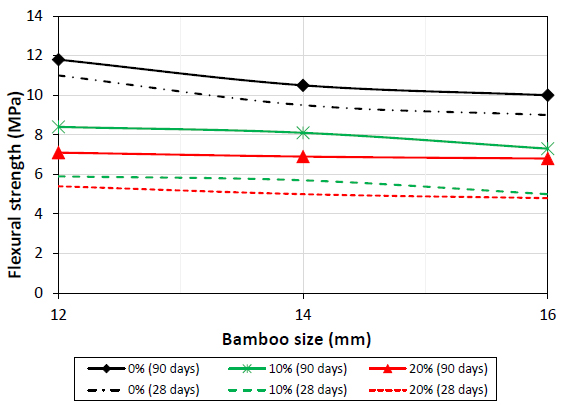
Comparison of flexural strength of cassava peel ash blended bamboo reinforced concrete at 28 and 90 days.
3.6. Flexural Crack Width
The first flexural cracks on all tested specimens were observed at an average of 0.25 of the ultimate load, crack width of 0.3 mm limit is specified in BS 8110 standard [35]. The obtained crack width for beams subjected to flexural loading at 28, 56, and 90 days is presented in Table 7. It can be noticed that the BRC beams with 0% CPA for all bamboo strip sizes did not satisfy the 0.3 mm specified in British Standard BS 8110 [35] for maximum crack width limit, but those incorporating CPA marginally meet the 0.3 crack width requirement at all tested curing age. Crack width also tends to reduce with increased diameter of bamboo strip reinforcement. This can be attributed to the increased surface area of bamboo strip reinforcements, which enhance bond transfer capacity and reduce concrete strain. For BRC-CPA beams containing 10% and 20%, the crack width values at 12, 14, and 16 mm satisfy the requirement of the code [35] as they all fall within the 0.3 mm crack width limit. This outcome shows a positive contribution of the cassava peel ash in improving the ITZ of concrete, thereby increasing the bonding between aggregate and cement paste and mitigating crack formation in concrete under flexural loading. Overall, crack width reduces with concrete curing age due to strength development; higher strength contributes to better resistance to tensile strength, thereby reducing crack width. Fig. (12) shows the crack width measured on concrete specimens at 0, 10, and 20% CPA replacement.
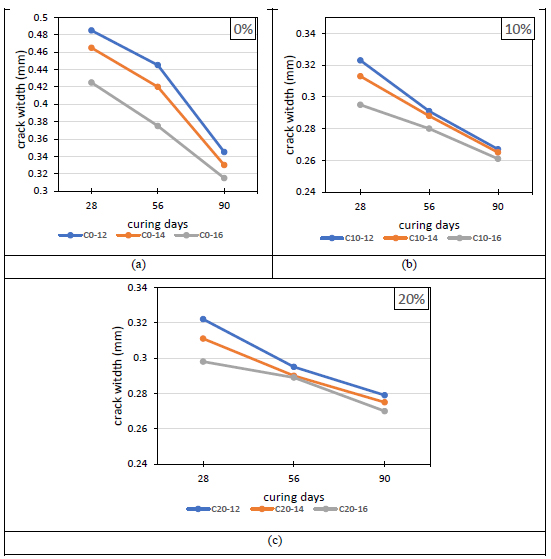
Flexural crack width of bamboo reinforced concrete beams at different CPA replacement.
Mix ID | Cassava Peel Ash (%) | Bamboo Size(mm) | Crack Width (mm) | ||
---|---|---|---|---|---|
28 | 56 | 90 | |||
C0-12 | 0 | 12 | 0.485 | 0.445 | 0.345 |
C0-14 | 0 | 14 | 0.465 | 0.420 | 0.330 |
C0-16 | 0 | 16 | 0.425 | 0.375 | 0.315 |
C10-12 | 10 | 12 | 0.323 | 0.291 | 0.267 |
C10-14 | 10 | 14 | 0.313 | 0.288 | 0.265 |
C10-16 | 10 | 16 | 0.295 | 0.280 | 0.261 |
C20-12 | 20 | 12 | 0.322 | 0.295 | 0.279 |
C20-14 | 20 | 14 | 0.311 | 0.290 | 0.275 |
C20-16 | 20 | 16 | 0.298 | 0.289 | 0.270 |
CONCLUSION
The following conclusions were drawn from this study:
i. The result of the chemical composition test carried out established that Cassava peel ash is a good pozzolanic material having high siliceous and aluminous materials composition.
ii. The tensile strength of the bamboo used ranged from 145.75 to 181.23 N/mm2 for 12 to 16 mm size.
iii. At constant w/c of 0.55, the slump value of fresh concrete reduces from 60 to 32 mm as the percentage of CPA increases indicating reduced workability. Also, the bulk density of hardened CPA blended concrete decreases as the CPA content increases.
iv. Compressive strength of CPA concrete decrease as the percentage of CPA increases which is in line with previous research. The compressive values obtained are 23.4 N/mm2, 22.2 N/mm2 and 21.4 N/mm2 for 0%, 10% and 20% CPA content respectively. However, CPA addition in concrete up to 20% still meets the minimum strength requirement for grade 20 concrete.
v. The flexural strength gains in CPA blended bamboo reinforced concrete at 90 days is higher compared to equivalent samples without CPA. This is due to the pozzolanic property of CPA that enhances better strength gain with concrete age.
vi. The flexural strength of bamboo reinforced concrete beams containing CPA at 20% is not significantly affected by variation in bamboo size when compared to that of 0 and 10% CPA content where increase in bamboo size led to reduced flexural strength.
vii. The addition of CPA significantly reduced flexural crack width as observed on concrete specimens and most CPA blended bamboo reinforced concrete meets the minimum crack width of 0.3 mm according to BS8110 specification. Crack width was also found to reduce with increasing Bamboo strip size.
In general, it can be deduced from the results obtained from a test conducted on hardened concrete that CPA causes a slightly downward trend in the compressive strength, which is a negative contribution but reduces the flexural crack width of bamboo reinforced concrete beams containing CPA. The addition of CPA can be considered to have a positive influence on the performance of beam reinforced beams.
RECOMMENDATION
The study recommends further research work to be carried out on computing the energy required for the calcination of CPA.
AUTHORS’ CONTRIBUTION
A., B., A., A., and A.: Original draft, Writing - review & editing;
A. and A.: Methodology;
A., A., B. and G.: Formal analysis;
A., A., A., A. and A.; Data curation;
A. and A.: Conceptualization & Supervision;
LIST OF ABBREVIATIONS
BRC-CPA | = bamboo-reinforced concrete containing cassava peel ash |
CPAC | = Cassava peel ash-blended concrete |
CPA | = Cassava peel ash |
BFS | = Blast furnace slag |
SSA | = Sugarcane straw ash |