All published articles of this journal are available on ScienceDirect.
Fire Resistance of Lightweight Aggregate Concrete Containing Spent Garnet as Partial Fine Aggregate Replacement
Abstract
Introduction
The escalating demand for concrete, driven by global infrastructure development, poses significant challenges to environmental sustainability due to the depletion of natural resources and the accumulation of waste materials. This paper explores the potential of utilizing waste materials, particularly palm oil clinker (POC) and spent garnets, as sustainable alternatives in concrete production. The depletion of natural aggregates, such as river sand, coupled with the environmental hazards associated with waste disposal, underscores the urgent need for eco-friendly solutions in construction materials. POC, derived from palm oil production waste, and spent garnets from abrasive industries offer promising avenues for reducing environmental impact and enhancing sustainability in concrete production. By addressing the dual challenges of resource depletion and waste management, this research aims to contribute to developing greener construction practices and mitigating environmental degradation.
Aims
This study aims to investigate the effects of incorporating spent garnet as a partial fine aggregate replacement on the fire resistance of POC LWAC. By examining the interplay between spent garnet inclusion and fire resistance, the research contributes to developing more sustainable concrete formulations and aids in industrial waste management practices, addressing critical societal and environmental challenges.
Methods
This study investigates the effects of elevated temperatures on the compressive strength and durability of POC LWAC specimens. Concrete specimens were demoulded after 24 hours of curing and submerged in water for 28 days. Compressive strength and water absorption tests were conducted at the end of the curing period. Subsequently, specimens were subjected to temperatures of 300 °C, 500 °C, and 700 °C for 1 hour in a furnace. After cooling naturally for 24 hours, visual inspection, mass reduction analysis, and evaluation of residual compressive strength were performed.
Results
Results indicate that 20% garnet replacement yields the highest compressive strength due to pore filling and denser structure. Higher garnet levels lead to reduced strength and increased water absorption. Visual assessment post-heating shows surface alterations, with 20% garnet exhibiting the lowest mass loss and strength reduction at elevated temperatures.
Conclusion
Notably, specimens containing 20% spent garnet in POC LWAC performed better in a fire than others, enhancing their fire-resistant properties. In summary, this research introduces a hopeful approach to improve the sustainability of concrete and mitigate the environmental repercussions of industrial waste.
1. INTRODUCTION
Concrete is the most commonly utilized building material, experiencing a rise in demand with the progress of global infrastructure construction. Its versatility extends across diverse applications, including construction, pavement, and marine infrastructure. According to Hemavathi et al. [1], coarse and fine aggregates, constituting about 70% of concrete's total volume, are fundamental ingredients. However, the extensive exploitation of natural resources like river sand and gravel due to the escalating need for construction materials is causing ecological imbalances and potential scarcity [2]. Hence, the necessity arises to identify alternative materials capable of entirely or partially replacing fine aggregates, aligning with sustainability goals and specific applications. Currently, lightweight aggregate is gradually gaining traction in practical construction projects. This is particularly significant for buildings in fire-prone areas and regions with prolonged exposure to high temperatures, where the elevated thermal environment substantially threatens building usage and human safety [3]. Therefore, an in-depth investigation of the mechanical performance of lightweight aggregate concrete (LWAC) under high temperatures is vital, establishing a robust foundation for efficient fire prevention and rehabilitation efforts after disasters. This paper comprehensively summarizes the damage mechanism of concrete under high temperatures and thoroughly reviews the mechanical properties of LWAC in such conditions.
Malaysia and Indonesia are the two biggest producers of oil palm plants worldwide [4, 5]. The worldwide palm oil production for the 2016-2017 amounted to roughly 64.5 million tons [6]. The substantial growth of approximately 6.1 million tons of waste materials, including empty fruit bunches, fibers, and kernels in palm oil plantations, caused a significant increase in the amount of solid trash produced [7]. This surge in waste has subsequently caused environmental problems [8-10]. Waste management offers economic benefits but brings environmental challenges, including greenhouse gas emissions. Unregulated disposal practices lead to significant heavy metal pollution in water, soil, and vegetation [11]. Open burning contributes to emissions of CO, CO2, SO, NO, PM10, and other pollutants, impacting the atmosphere [12]. Individuals involved in waste picking at open dump sites face severe health risks. The discharge of solid waste into water bodies exacerbates global marine litter and environmental contamination [13]. Hence, making sustainable waste management decisions is of utmost importance to address these issues [14]. Shells and fibers from palm oil are commonly co-combusted in mills due to their high fuel value, generating additional waste materials like palm oil clinker (POC). POC manifests as a sizable gray mass resembling a porous stone characterized by its irregular and flaky structure [15]. These waste materials are often disposed of improperly and haphazardly in landfills and open spaces. This careless and indiscriminate disposal leads to air, water, and land pollution, causing detrimental environmental impacts. Transforming this by-product for product manufacturing would reduce waste disposed and save landfill use.
Considering environmental sustainability, researchers have explored the possible utilization of POC as a component in concrete mixing. The search for eco-friendly alternatives becomes vital as the natural aggregate sources deplete and high artificial aggregate costs. POC has been proven as a viable option for recycled aggregates, substituting the need for natural stone. This substitution leads to the creation of lightweight aggregate concrete with reduced density and improved sustainability [4, 5, 16, 17]. Following this, the pressing issues of sand exhaustion and river degradation owing to excessive sand mining have inspired researchers to integrate sand replacement material originating from industrial waste such as coal bottom ash [4, 18-20] and POC [21, 22] to form greener POC LWAC. The existence of ample industrial surplus opens for further exploration of the potential of these materials as sand replacements in this concrete. The existence of spent garnet waste is a significant concern within various industries, particularly those involving abrasive blasting and waterjet cutting processes. The Malaysian shipbuilding industry imports thousands of tonnes of garnet annually, producing substantial material waste [23]. Garnets possess angular fractures and robust toughness properties, making them suitable for diverse abrasive applications. Garnet blasting waste is a mixture of old paint flakes, oil, and other residues extracted during blasting [24]. Unfortunately, this waste is typically disposed of in landfills, contributing to diminishing land availability and heightening environmental concerns [25]. When these substances enter rivers through flooding or runoff, garnet waste becomes a significant environmental and health hazard, causing water pollution. Therefore, the presence of spent garnets threatens ecological equilibrium and biodiversity. Repurposing this waste for alternative uses can mitigate the accumulation of environmentally harmful waste, thus addressing this environmental challenge.
A few researchers have investigated the potential use of spent garnet in an alkali-activated mortar [24], self-compacting geopolymer concrete [25], high-strength concrete [26], mortar [27], and lightweight aggregate concrete [28]. However, the above researchers only investigated the effect of spent garnet as a fine aggregate replacement on concrete's mechanical and durability properties. In terms of fire resistance, research that has been investigated by Ab Kadir et al. [29] is limited to findings on the performance of spent garnet as fine aggregate replacement in physical change and residual compressive strength after being exposed to elevated temperatures (200 °C, 400 °C, 600 °C, and 800 °C) in high-strength concrete. The effect of spent garnet as a fine aggregate replacement on fire resistance in POC LWAC has yet to be adequately covered and has not been investigated. The study examines how incorporating spent garnet as a partial fine aggregate affects the fire resistance of lightweight aggregate concrete (LWAC). It considers visual observation, mass loss, and residual strength and utilizes response surface methodology (RSM) for analysis. The use of spent garnet in POC LWAC results in more sustainable concrete and aids industrial waste management matters for the well-being of society.
2. MATERIALS AND METHODS
2.1. Materials
The concrete specimens comprised ordinary Portland cement (OPC), river sand, POC, spent garnet, water, and superplasticizer (SP). The river sand used in this study was air-dried and had a maximum particle size of 2.36 mm after passing through a sieve. POC was a lightweight coarse aggregate from a palm oil mill plant's dumpsite. Initially, the large POC chunks were crushed to the required size using a jaw crusher, resulting in POC coarse aggregate ranging from 5 mm to 10 mm. The spent garnet waste was sourced from an East Coast Peninsular Malaysia facility associated with brownfield services for the oil, gas, and petrochemical industries. Since the collected spent garnet was damp, it was oven-dried at 105 °C ± 5 °C for 24 hours to eliminate moisture content. After removing impurities, the garnet was screened through a 600 µm sieve to replace fine aggregate (river sand) partially. The visual representations and particle dispersion of POC and the spent garnet utilized in this research can be found in Figs. (1 and 2), respectively. The physical characteristics of POC, river sand, and spent garnet were assessed and are provided in detail in Table 1. Clean tap water was used for both concrete specimen preparation and curing. A 1% addition of SP by cement was incorporated as a water reducer to enhance the workability of the concrete. The SP used in this research is classified as Type F according to ASTM C494/C494M-19 [30].
Physical Properties | POC | River Sand | Spent Garnet |
---|---|---|---|
Bulk density (kg/m3) | 945.22 | 1541 | - |
Water absorption (24h) (%) | 10.19 | 2.85 | 6.12 |
Specific gravity | - | 2.77 | 3.75 |
Moisture content (%) | 1.87 | - | - |
Fineness modulus | - | 3.85 | 1.68 |
Aggregate abrasion value (%) | 58.70 | - | - |
Aggregates impact value (%) | 48.39 | - | - |
Aggregate crushing value (%) | 45.54 | - | - |
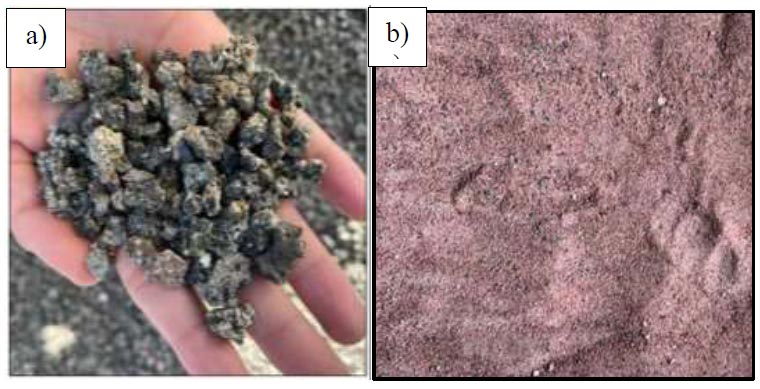
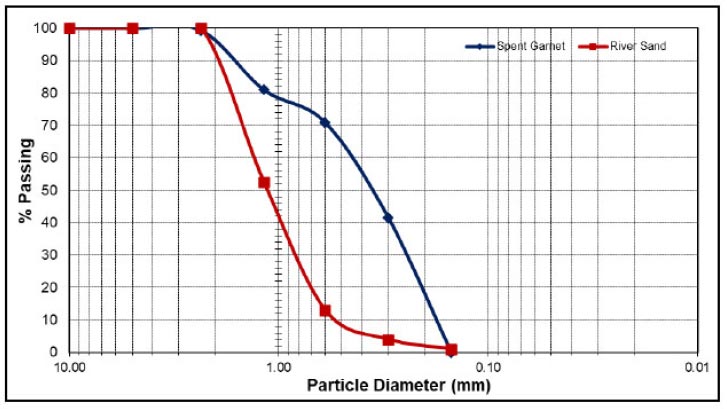
2.2. Mix Proportion and Testing Method
Ordinary Portland Cement, fine aggregate (natural river sand), and POC were used for the mix design in the trial mix method. The fine aggregate was partially replaced with spent garnet. The replacement percentages were mixed in several batches, with the control sample being normal concrete without spent garnet. For a series of POC LWAC mixes, the range for percentage replacement of spent garnet was 10%, 20%, 30%, 40%, and 50% (based on the fine aggregate weight), as tabulated in Table 2. The concrete mixes were designed to achieve a target compressive strength of 45 MPa. The interactions between cement, aggregates, and additives like spent garnet and POC can influence concrete strength. The optimal dosage of these additives may vary depending on the specific combination of materials used in the mix. Once the concrete had been thoroughly mixed, it was poured into the steel mold, which measured 100 mm x 100 mm x 100 mm. All the hardened concrete specimens were demoulded after 24 hours and placed in the curing water tank for 28 days. After 28 days of curing, the specimens underwent compressive strength and water absorption tests. Then, after exposure to elevated temperatures of 300 °C, 500 °C, and 700 °C for 1 hour in a furnace, compression tests were conducted on the POC LWAC specimens. The testing procedure was based on the approach used by Abdul Rahim Zai and Salhotra [31]. The furnace switch was shut down at the end, and the vent hole opened. This process helps them cool naturally for 24 hours. Afterwards, an evaluation was conducted on visual inspection, mass reduction, and decrease in residual compressive strength. Fig. (3) shows the specimen's preparation and testing process. The mass loss and reduction in compressive strength values of specimens exposed to elevated temperatures were evaluated using Eqs. (1 and 2), respectively.
![]() |
(1) |
where:
Mi = mass of the specimen before exposed to elevated temperature, g
Mt = mass of the specimen after exposed to elevated temperature, g
![]() |
(2) |
where:
fc(28 days) = 28 days compressive strength of the concrete mixture, MPa
fc (t days) = compressive strength at (t) days after being exposed to elevated temperature, MPa
Mix Designation | River Sand | Spent Garnet | POC | OPC | Water | SP |
---|---|---|---|---|---|---|
0% | 625 | - | 345 | 375 | 158 | 3.75 |
10% | 563 | 63 | 345 | 375 | 158 | 3.75 |
20% | 500 | 125 | 345 | 375 | 158 | 3.75 |
30% | 438 | 188 | 345 | 375 | 158 | 3.75 |
40% | 375 | 250 | 345 | 375 | 158 | 3.75 |
50% | 313 | 313 | 345 | 375 | 158 | 3.75 |
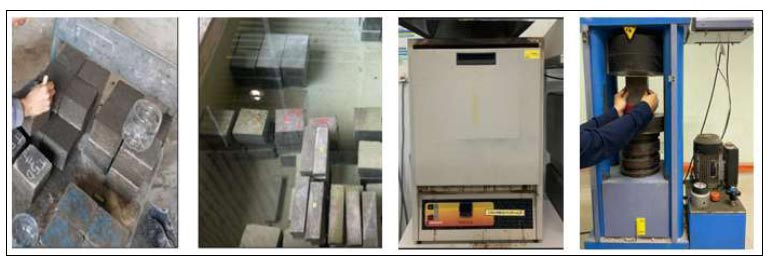
2.3. Respond Surface Methodology
The effect of different elevated temperatures and levels of spent garnet replacement on POC LWAC properties, exploiting mass loss and strength reduction, was also analyzed statistically using Design Expert 13 software. The analysis aimed to establish the possible relationship between factors (spent garnet content and elevated temperatures) and responses (mass loss and strength reduction). The response surface methodology (RSM) model produced a surface response graph and generated the possible equation. The regression equation derived from the analysis establishes the correlation between the factors and the response. Once the model was validated, the best model to fit the correlation was verified and discussed. The analysis provided insights into how variations in spent garnet content and exposure to elevated temperatures affect the mass loss and strength reduction of POC LWAC specimens.
3. RESULTS AND DISCUSSION
3.1. Compressive Strength
Fig. (4) displays compressive strength variations in LWAC made from POC with varying proportions of spent garnet replacing sand. Following a 28-day curing period, the lightweight aggregate concrete (LWAC) incorporating 20% spent garnet exhibited the highest compressive strength, reaching 53.7 MPa. This surpassed the compressive strength of the control specimen, which was at 51.0 MPa. Strength gradually declined as the spent garnet percentage increased: 52.4 MPa at 30%, 48.6 MPa at 40%, and 44.6 MPa at 50% garnet replacement. The 20% garnet mixture achieved the highest strength by filling pores and creating a denser concrete structure. The rough, angular texture of spent garnets also contributed to increased strength. Research by Muttashar et al. [32] emphasized the benefit of this texture in enhancing particle grip and reducing strength loss, resulting in higher strength in self-compacting geopolymer concrete. However, caution is needed to avoid excessive use of spent garnet, as 30%, 40%, and 50% levels led to reduced compressive strength in POC LWAC. The reduction in the compressive strength was mainly due to lesser integrity between the cement paste and the aggregate, as mentioned by previous researchers [33]. Table 3 comprehensively compares compressive strength results from multiple studies, each investigating the impact of different substitution percentages of spent garnet or expanded perlite on lightweight aggregate concrete. The table encompasses findings from the present research, highlighting the variations in compressive strength across different substitution levels and the additional insights provided by each study.
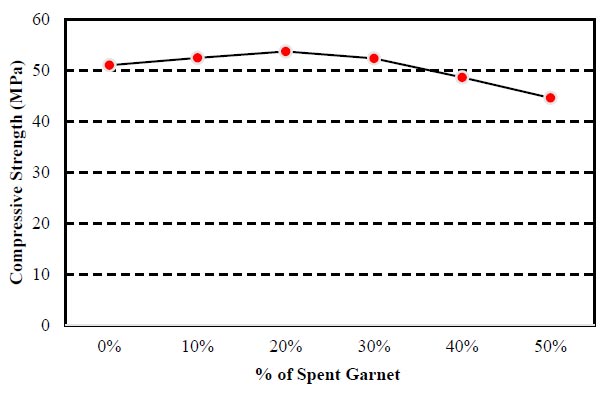
Reference | % Substitution | Compressive Strength (MPa) | Additional Findings |
---|---|---|---|
Present research | 0%, 10%, 20%, 30%, 40% and 50% of spent garnet | 53.7 (20%) | The highest strength is achieved in lightweight aggregate concrete due to pore filling and denser structure. |
Muttashar et al. [32] | 0%, 25%, 50%, 75%, and 100% of spent garnet | 79.84 (0%) | The study highlights the benefit of angular texture in enhancing particle grip and reducing strength loss. |
Present Research | 0%, 10%, 20%, 30%, 40% and 50% of spent garnet | 44.6 (50%) | Further decline in strength was noted at a 50% garnet substitution level. |
Top et al. [33] | 0% - 5% of expanded perlite | Varies | Integrity between cement paste and aggregate is a crucial factor in compressive strength. |
3.2. Water Absorption
The impact of incorporating spent garnet as a partial replacement for fine aggregate on the water absorption of POC LWAC is illustrated in Fig. (5.) After 28 days of curing, the water absorption rates are as follows: 2.8%, 2.7%, 2.0%, 2.5%, 2.6%, and 3.5% for 0%, 10%, 20%, 30%, 40%, and 50% substitution of spent garnet in POC LWAC, respectively. Notably, the water absorption values for all POC concrete mixes with varying proportions of spent garnet are below 4%. As per Neville [34], since the water absorption remains below 10% for all specimens, they appear to be of high-quality concrete. Incorporating 20% spent garnet leads to a lower water absorption rate than other substitution levels, possibly because the fine particles of spent garnet act as fillers, filling the internal voids/ pores and resulting in a more compact structure. However, when garnet is substituted at 50%, it exhibits the highest water absorption, consistent with Abdul Shukor Lim et al. [27], who investigated the effect of excess spent garnet in mortar. Zhang et al. [35] attribute the reduction in water absorption primarily to the gradual densification of the inner structure. However, in cases where spent garnet is utilized, the packing level of the aggregate may be inadequate, leading to voids within the POC LWAC. These unfilled voids facilitate water infiltration, exacerbating the absorption. Table 4 presents a comparative analysis of water absorption percentages from various studies investigating the substitution of garnet or iron ore in concrete mixtures. The studies include the present research, Abdul Shukor Lim et al. [27], and Zhang et al. [35]. The table highlights the impact of different substitution levels on water absorption rates and offers additional insights into the structural densification effects observed in the concrete mixtures.
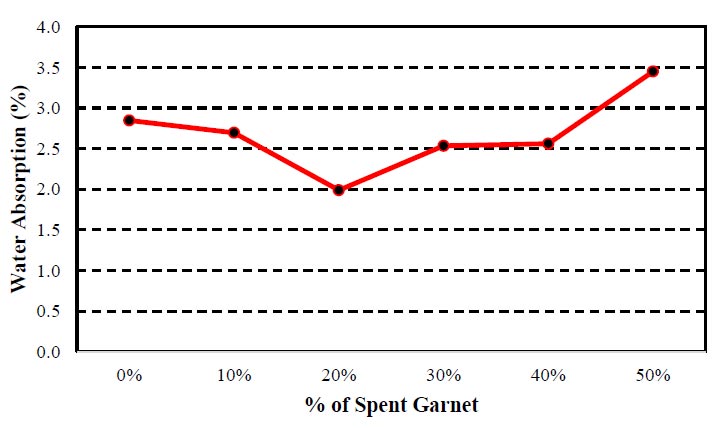
Reference | % Substitution | Water Absorption (%) | Additional Findings |
---|---|---|---|
Present research | 0%, 10%, 20%, 30%, 40% and 50% of spent garnet | 1.989 (20%) 3.450 (50%) |
Using spent garnet up to 20% reduces water absorption of lightweight aggregate concrete, but too much increases water absorption. |
Abdul Shukor Lim et al. [27] | 0%, 25%, 50%, 75%, and 100% of spent garnet | 4% (100%) | Excess spent garnet leads to higher water absorption of mortar |
Zhang et al. [35] | 0%, 20%, 40%, 60%, 80%, and 100% of iron ore | 0.76 (100%) | Reduction in water absorption in ultra-high performance concrete attributed to gradual densification of inner structure |
3.3. Visual Assessment
Figs. (6 to 8) illustrate the visible cracking and altered surface color of POC LWAC specimens with varying proportions of spent garnet following a 1-hour exposure at 300 °C, 500 °C, and 700 °C. The heated POC LWAC containing 0%, 20%, and 50% of spent garnet was chosen for visual assessment. At 300 °C, all the surfaces of the heated concrete specimens remained unchanged. When the temperature increases to 500 °C and 700 °C, fractures in the concrete begin to appear. This is due to the effect of heat stress caused by water evaporation [36]. No explosive spalling was witnessed in specimens subjected to heating up to 700 °C; however, crack formations were observed in all samples. Notably, POC LWAC, with a 50% spent garnet replacement, exhibited a more pronounced occurrence of surface cracking at higher temperatures. Upon visual evaluation, it was observed that upon heating to 500 °C, the specimen's color transitioned from light grey to reddish and brownish. Furthermore, at 700 °C, the surface of POC LWAC took on a pinkish hue. In the case of 50% spent garnet replacement, the POC LWAC appeared white with evident surface cracks. Ahsan et al. [37] reported similar findings when using excessive seashell powder in concrete.
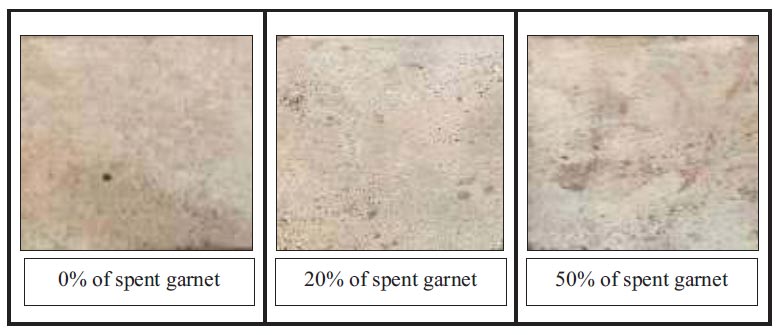
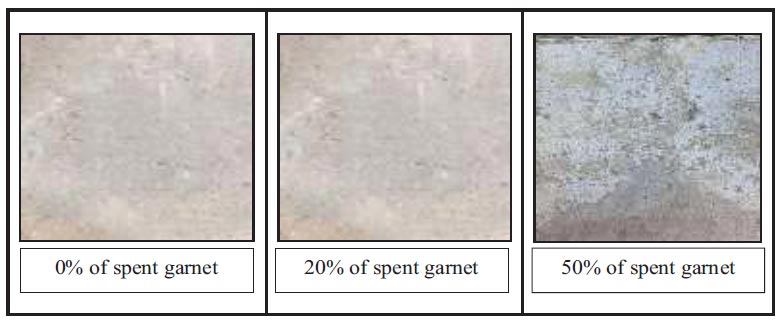
3.4. Mass Loss
The mass loss of POC LWAC is shown in Fig. (9). The mass loss of the concrete increased as the temperature increased from 300 °C, 500 °C and 700 °C. The mass loss of exposed specimens was found to be 6.76% to 7.59% (300 °C), 7.31% to 9.30% (500 °C), and 8.42% to 10.62% (700 °C). Moreover, the weight loss of the exposed specimens increased with increasing concrete porosity. When the temperature does not exceed 400 °C, the initial mass loss could be attributed to the evaporation of capillary water. Shukri, Mohamed, and Ishak [38] state that when specimens are subjected to temperatures between 600 °C and 800 °C, the moisture content will be lost from the tiny pores of cement pastes and aggregates, which would result in mass loss of the samples. Table 5 provides a comparative analysis of mass loss percentages observed in concrete specimens exposed to varying temperatures, as reported by the present research and Shukri, Mohamed, and Ishak [38]. The amount of utilized spent garnet generally impacts the mass loss. Concrete containing 20% of spent garnet has the lowest mass loss rate compared to other specimens. It is attributed to reducing concrete voids due to the incorporation of spent garnet as it fills all pores, making the concrete denser. Furthermore, excessive use of spent garnet will lead to a higher mass loss. It could be explained by the fact that the concrete specimen's void becomes larger as the amount of spent garnet increases at 50% replacement. As the void of the concrete matrix increases, it indicates that concrete is becoming less dense. Wang, Huang, and Xie [39] showed a similar pattern in terms of the mass reduction of concrete with the temperature rise.
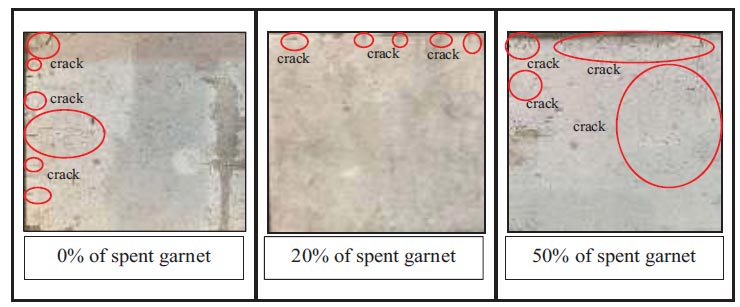
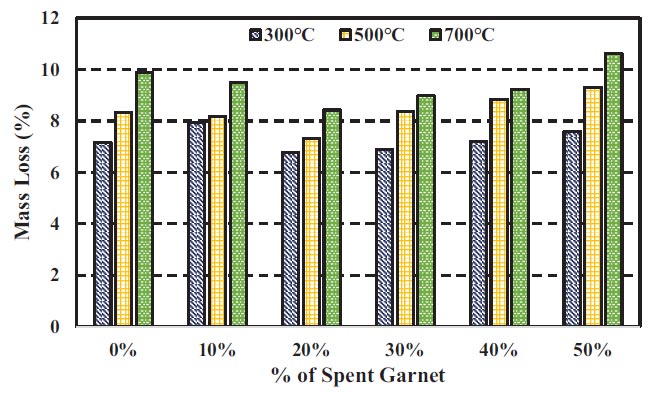
Reference | Temperature (°C) | Mass Loss (%) | Additional Findings |
---|---|---|---|
Present research | 300 | 6.76 to 7.59 | Mass loss in lightweight aggregate concrete increases with temperature; higher porosity correlates with higher mass loss. |
Present research | 500 | 7.31 to 9.30 | Mass loss in lightweight aggregate concrete increases with temperature; porosity influences mass loss. |
Present Research | 700 | 8.42 to 10.62 | The highest mass loss is observed in lightweight aggregate concrete; porosity and temperature contribute to increased mass loss. |
Shukri, Mohamed, and Ishak [38] | 600-800 | 6.61 to 7.48 | Moisture loss from pores at elevated temperatures contributes to mass loss. |
The validation of the proposed work is meticulously depicted in Fig. (10), where the correlation between spent garnet content and varying elevated temperatures concerning mass loss in POC LWAC is analyzed using RSM. Fig. (10a) illustrates a 3D surface response plot, offering insights into this relationship. The plot distinctly reveals that an increased proportion of spent garnet correlates with a corresponding rise in mass loss in POC LWAC, particularly evident with the temperature escalation up to 700 °C. This trend highlights a proportional relationship between spent garnet content, elevated temperatures, and mass loss. Furthermore, the surface response plot emphasizes that incorporating 20% spent garnet in POC LWAC improves mass loss performance compared to plain POC and other variants containing 10%, 30%, 40%, and 50% spent garnet. Fig. (10b) supplements this analysis with a perturbation plot, facilitating a comparison of the individual effects of these factors on the response. Curve A (spent garnet content) exhibits a more pronounced curvature, indicating higher sensitivity than Curve B (elevated temperature). This underscores the varied content of spent garnet in POC LWAC significantly influences and dominates, resulting in mass loss. The ANOVA analysis further solidifies the strength of the quadratic regression, unveiling a robust relationship between mass loss and these factors, as evidenced by an R-squared value (R2) of 0.8743. Eq. (3) encapsulates the empirical relationship between mass loss and the multiple factors, denoted by the spent garnet content (A) and elevated temperatures (B).
![]() |
(3) |
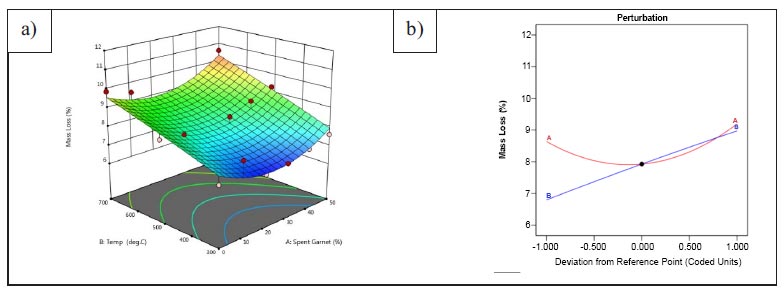
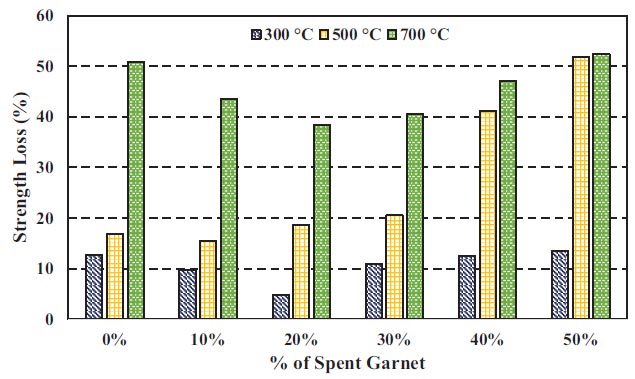
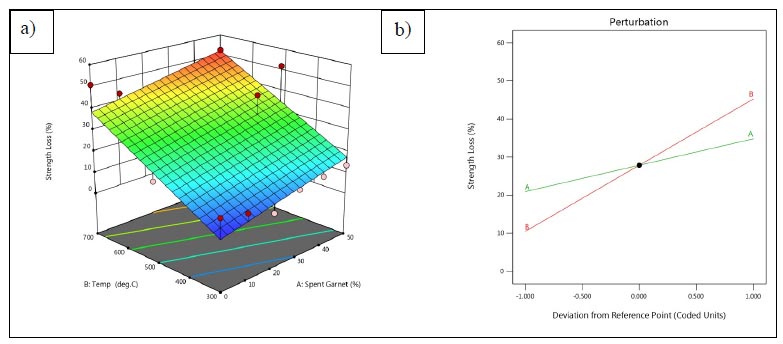
3.5. Strength Loss
As illustrated in Fig. (11), the compressive strength of the samples noticeably decreases when exposed to higher temperatures, reaching up to 700 °C. This pattern is consistent and significant, indicating that higher temperatures lead to a uniform reduction in compressive strength across all test series. The principal factor contributing to this decline in compressive strength of POC LWAC under elevated temperatures is concrete dehydration, stemming from the elimination of free water. According to prior studies by Heap et al. [40], the hydrothermal influence makes strength loss inevitable, resulting in free and adsorbed water loss. Furthermore, exposure to elevated temperatures induces various physical and chemical alterations in concrete, affecting its matrix. These alterations encompass cement drying, resulting in voids, cracks, and paste shrinkage. Using a suitable percentage enhances the performance of POC LWAC upon exposure to elevated temperatures. Using 20% of the spent garnet resulted in the lowest percentage of strength reduction of concrete. Less void in POC LWAC can be attributed to its denser matrix, making it less vulnerable to damage when subjected to elevated temperatures than the 50% POC LWAC with a porous matrix.
The surface response plots presented in Fig. (12) were instrumental in examining the relationship between spent garnet content, elevated temperature, and strength loss in POC LWAC. In Fig. (12a), the surface response plot illustrates how variations in spent garnet content and temperature impact strength loss in POC LWAC. It becomes apparent that as both spent garnet content and temperature increase, a corresponding rise in strength loss, highlighting a clear connection between strength loss and elevated temperature. Fig. (12b) further elucidates this relationship through a perturbation plot, visually comparing the effects. Notably, Line A, representing spent garnet content, displays a steeper slope than Line B, suggesting that changes in spent garnet content as a fine aggregate replacement exert a more significant influence on enhancing strength loss in POC LWAC than variations in temperature levels. Using RSM, a linear regression model was established to capture this relationship accurately. The subsequent analysis employing ANOVA demonstrated a robust fit with an R-squared value (R2) of 0.8068, indicating a significant correlation. Eq. (4) expressed the relationship between strength loss of POC LWAC, spent garnet content (A), and elevated temperatures (B).
![]() |
(4) |
CONCLUSION
The article examined the effect of substituting sand with spent garnet on the performance of POC LWAC upon exposure to high temperatures. Based on the findings, the following conclusions are presented:
1. The visual inspection showed that POC LWAC samples had surface cracks when exposed to temperatures above 500 °C. The specimen's color changed to reddish and brownish at 500 °C and turned pinkish at 700 °C.
2. Among the specified percentages (0%, 10%, 30%, 40%, and 50%) utilized in POC LWAC specimens, incorporating 20% garnet demonstrated the least mass loss, especially under elevated temperatures such as 700 °C. The reduction in mass of the concrete samples displayed a notable fluctuation across all percentages as the temperature rose.
3. The compressive strengths of POC LWAC samples, incorporating 20% spent garnet, displayed a notable upward trend with increasing exposure temperatures, particularly up to 700 °C. These specimens consistently exhibited superior performance compared to counterparts with varying garnet percentages. This enhanced performance can be attributed to the denser matrix of POC LWAC with 20% spent garnet, resulting in reduced voids and greater resilience against damage at elevated temperatures compared to POC LWAC with a 50% porous matrix. This observation aligns with the water absorption results, which indicated that the POC LWAC with 50% garnet substitution displayed higher water absorption, suggesting higher porosity.
4. The coefficient of regression by RSM associated different level percentages of spent garnet and elevated temperature to the responses (mass loss and strength loss) of POC LWAC indicated a strong relationship among the tested factors.
5. Using spent garnet in POC LWAC production could potentially reduce fine aggregate consumption, promote environmental friendliness in the shipbuilding industry, and provide a substitute building material for the regional construction sector.
HIGHLIGHTS
• Utilizing spent garnet and palm oil clinker reduces reliance on river sand, promoting sustainable concrete production.
• Investigating POC lightweight concrete at elevated temperatures (300 °C, 500 °C, 700 °C) showcases mass loss and strength reduction, which is vital for assessing fire-resistant properties.
• Specimens with 20% spent garnet demonstrate improved fire resistance, indicating an optimal garnet content for enhancing concrete durability in high temperature conditions.
LIST OF ABBREVIATIONS
POC LWAC | = Palm Oil Clinker Lightweight Aggregate Concrete |
LWAC | = Lightweight Aggregate Concrete |
POC | = Palm Oil Clinker |
LWA | = Lightweight Aggregate |
RSM | = Response Surface Methodology |
OPC | = Ordinary Portland Cement |
SP | = Superplasticizer |
AVAILABILITY OF DATA AND MATERIAL
The data necessary to comprehend the study's findings is presented within the article.