All published articles of this journal are available on ScienceDirect.
A Review Study of the Mechanical Characteristics of Nano Concrete Reinforced with Hybrid Fiber
Abstract
Due to poor strength and hardness, low tensile strength, and inadequate cracking resistance, conventional concrete has recently posed a significant barrier to the modernization of the structural sector. To solve these issues, researchers investigated and found ways of implementing nanotechnology in concrete production. Nano concrete can be produced by incorporating nanomaterials in the concrete mix. This concrete type can also be reinforced by incorporating hybrid fibers and nanofibers. This review paper conducted an in-depth study on two types of nanomaterials that could be used in the production of nano concrete. Additionally, hybrid fibers were used to strengthen nano concrete. The objective of this paper was to identify some nanomaterials used in the production of nano concrete. Even though this unique hybrid material has been the subject of several investigations, there have only been a few reviews on its production procedures, effectiveness, and performance of this type of concrete. To identify these nanomaterials, their potential, and their properties, a review method was used to study previous works of some researchers and scientists on related and similar works. Some properties of these nanomaterials were discussed in this paper. Summarizing and concluding the research works of previous authors and this current study, it was found that nano concrete has better properties compared to normal conventional concrete. However, there are some limitations associated with the uses and applications of these nanomaterials in concrete for mass production. By tracking the beginning and spread of cracks, it was discovered that mixing various fiber types into a concrete mix enhances the cementitious matrix's strength qualities. The mechanical and toughness characteristics of fiber-reinforced concrete mixtures may be significantly improved by incorporating composites hybrid fiber composites that utilize the synergistic impact of nano- and micro-additives.
1. INTRODUCTION
Among the most crucial concerns for structural engineering in both present and future projects, structural safety against loads is one of them. The current legislation clearly outlines the construction and design processes for new structures, but there are several challenges in assuring the safety of old structures, along with unspecified characteristics, significant uncertainties, various construction techniques, and economics.
The most common material used in structural construction is concrete. It is a highly homogenous substance made of water, finely ground cement, and a range of sized particles, and it also has inherent chemical, mechanical, and physical qualities. Calcium silicate hydrate, which gives concrete its strength and other mechanical qualities, and other byproducts, such as calcium hydroxide, are created by adding cement and water. Due to the widespread availability and benefits in terms of the cost of normal concrete (NC), it has been utilized extensively in civil engineering constructions. Low elongation, brittle behavior, and vulnerability to crack opening and propagation are only a few of NC's drawbacks. Thus, this gap severely constrains the range of its applicability. Structural components with superior mechanical qualities and longer service lives are needed for today's concrete constructions. This may be accomplished by giving the concrete better mechanical qualities by adding nanostructured components. The present trend in concrete technology development emphasizes the endurance of the severe environment as well as the characteristics, destructive capabilities, and intensity [1-3].
The construction industry is facing several significant challenges, including one of the most important ones, which is sustainability. Nanotechnology is developed because of the high demand for the use of materials that have a lower negative impact on the environment [4]. Compared with traditional materials, nanotechnology has the potential to result in the production of materials that feature a significantly larger and more extensive specific area as well as superior mechanical and durability properties [5-7].
Two types of classifications can be applied to nanomaterials: pozzolanic nanomaterials, which include nano alumina, nano silica, and nano clay [8], and fibrous nanomaterials, which include carbon nanofibers and carbon nanotubes [9]. When combined with calcium hydroxide, all pozzolanic materials are considered to be capable of producing high pozzolanic reactions, which leads to the formation of further hydrated calcium silicate gel. Due to this, the technical properties of the concrete have the potential to be enhanced [10].
The introduction of nanotechnology to concrete construction has the potential to increase tensile stability, mechanical strength, and durability while lowering maintenance costs and obviating the need for immediate replacement. Sooner or later, better methods for developing novel materials and enhancing living conditions will be identified with the aid of a better understanding of the properties of nanomaterials.
Since the turn of the millennium, there has been an increase in demand for ultra-high strength concrete (UHPC), which has necessitated the creation of cement nanocomposites or nano-concrete. Nanomaterials have the potential to alter the cement matrix's nanostructure and enhance bulk properties at the nanoscale because of their incredibly small size. By sharpening the intersection zone in the concrete and densifying the structure, nanoparticles can have a filling effect. Furthermore, the advantages of concrete materials, such as low tensile strength, modulus of elasticity and significant shrinkage, can be addressed by the superior mechanical properties of nanomaterials. However, the use of nanomaterials in the construction industry is still constrained by their high cost and handling challenges.
In the building sector, the use of nanomaterials in concrete is becoming more popular. Due to the pore-filling properties of nanomaterials, studies have shown that concrete containing nanoparticles exhibits increased strength, durability, and pore reduction in concrete. Additionally, the steel reinforcement's resistance to corrosion is increased as a result. Therefore, nanomaterials help extend a building's lifespan. Large-scale cement usage raises CO2 emissions, which, in turn, increases the greenhouse effect. To lower the cement content of the concrete mix, nanomaterials are used. One of the most amazing developments in concrete technology over the past ten years is the use of nanomaterials. Nanomaterials' unique qualities can significantly increase the level of concrete structure quality and expand the material's potential uses. There are numerous applications for nanomaterials worldwide, and this number is constantly growing. Nanomaterials are purposefully created and designed with specific shapes, sizes, and surface finish characteristics.
Nano cements are made with Portland cement particles that are not greater than 100 nanometers. The voids in the concrete are filled with these tiny particles, which strengthen the concrete. By reducing the void space between the cement and the aggregate in the hardened concrete, superfine particles in Portland cement paste that are added to a concrete mix using the top-down approach to nanotechnology alter the material properties and performance of the concrete.
In this article, we examined some nanomaterials that could be used to make nano-concrete. The nanomaterials that were investigated are nanosilica (Fig. 1) and carbon nanotubes (CNTs) (Fig. 2). The properties of these nanomaterials are listed in Table 1. These nano-concrete materials have the potential to improve the thermal and mechanical properties of buildings, which will ultimately result in increasing the buildings' tensile strength, durability, shrinkage, and adhesion to reinforcing materials. Due to this, the concrete industry may be able to reduce its overall costs and its rate of energy consumption. Concrete composites with superior properties can be produced by incorporating nanomaterials into the mixture [12].
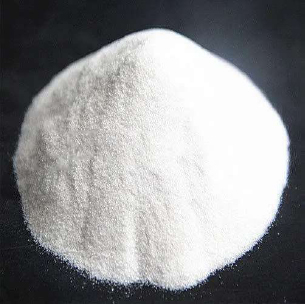
Nanomaterials | Properties |
---|---|
Nano silica (nano-SiO2) | |
![]() |
To increase compressive strength, nano-silica granules are crushed and added to the concrete. The fine size fills the spaces between the aggregate particles and cement. Second, as pozzolanic acid and CH combine to form CSH gel, the bond quality is enhanced, and the capillary porosity of the concrete is decreased. High-purity amorphous silica powder makes up nano-SiO2, a white, fluffy powder. Nano-SiO2 has the benefits of a large specific surface area, strong surface adsorption, large surface energy, high chemical purity, and good dispersion due to its small particle size. Nano-SiO2 can be divided into hydrophilic and hydrophobic varieties based on their varying hydrophilicity. The nano SiO2 used in the concrete is primarily hydrophilic and has good dispersion [12]. |
Carbon nanotube (CNT) | |
![]() |
i. CNT aspect ratio. ii. CNTs have a very high tensile strength. iii. CNTs are very flexible: they can be bent significantly without damage. iv. CNTs have a low coefficient of thermal expansion. v. CNTs are good electronic field emitters. vi. CNTs are as rigid as a diamond (the hardest natural material in nature). vii. The gravitational weight of the nanotube is very low. viii. The density of CNTs is a quarter of that of steel. ix. CNTs are stronger than steel. They have exceptional mechanical properties. CNTs are ten times stronger than steel. x. CNTs have a high heat capacity. In general, they are twenty times stronger than steel. Therefore, when heated, they do not expand like steel. Therefore, CNTs are used in making bridges and aircraft equipment. xi. In CNTs, each carbon atom is surrounded by three other carbon atoms through covalent bonds. These carbon-carbon covalent bonds form lattices in the shape of hexagons. xii. The crystalline structure of CNTs exists in the form of regular hexagons. xiii. CNTs are elastic with ~18% elongation at break. xiv. CNTs are good conductors of heat. xv. CNTs have good electrical conductivity. xvi. The modulus of elasticity is high. The modulus of elasticity of CNTs is about 1 terapascal, which makes them ten times stronger than steel. xvii. CNTs are chemically neutral. So, they are chemically stable. Therefore, CNTs are resistant to corrosion. |
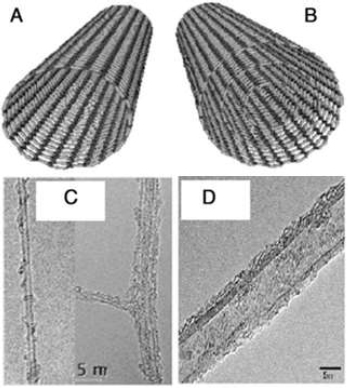
Concrete has a reputation for being a brittle material. To find a solution to this issue, a significant amount of research has been carried out. Many researchers have suggested the use of dispersed fiber reinforcement as a solution to the problem of brittleness in concrete. However, additional research has shown that the implementation of nanotechnology in the production of concrete would be a significant step forward in improving the mechanical properties of concrete and resolving the issues that are currently plaguing the material. In some countries, the concept of nano concrete has not yet been introduced. Therefore, the purpose of this paper is to review the previous works that have been done on nano concrete to identify the positive impacts as well as the challenges posed by the materials that are used in the production of nano concrete, which is also known as nanomaterials. The individual effects of these nanomaterials in nano concrete needed to be analysed for a better understanding so that people from all over the world could comprehend the reasons why nano concrete is distinct from regular conventional concrete.
2. NANO MATERIALS FOR NANO CONCRETE
2.1. Carbon Nanotubes (CNTs)
Due to their distinctive mechanical, electrical, and thermal properties, carbon nanotubes (CNTs) are one of the most popular nanomaterials used as fiber reinforcements to create multifunctional composites with different novel characteristics [16, 17]. In comparison to nanocarbon fibers, it has also been claimed that nano cement and CNTs can enhance the properties of concrete. CNTs have high yield strength, tensile strength, and modulus of elasticity. These characteristics make CNTs an intriguing concrete reinforcement material. The development of reinforced structural concrete using CNTs is an excellent opportunity provided by the special properties of CNTs [18]. The literature has investigated the addition of CNTs to concrete mixes and repair mixes [19, 20]. Due to their capacity to stop the development of microcracks in the cementitious matrix, CNTs enhance cementitious composites under tension [21]. The strongest fibers of any material to date, CNTs are an intriguing candidate for the upcoming wave of high-performance structural composites [22]. First, compared to other fibers, CNTs are much stronger, which increases the overall strength of concrete. Second, compared to other fibers, CNTs have a significantly higher aspect ratio, necessitating more energy for crack propagation. Third, because of their nanoscale size, CNTs can be widely distributed in the cementitious matrix with much closer spacing than conventional fibers because they are the same thickness as the layers of hydrated calcium silicate in hydrated cement. In cement-CNT composites, crack bridging has been observed in laboratory tests [23]. A study [23] employed finite element modeling to assess the modulus of elasticity of composites made of single-wall CNT reinforcement. Pressure-sensitive characteristics and microstructure of cement composites were reinforced with CNTs [22].
When using CNTs in cement-based materials, a uniform CNT distribution is essential [24]. The high van der Waals force, large surface area, and easy agglomeration of CNT make uniform dispersion in cement-based materials challenging. To achieve uniform distribution in the cementitious matrix, CNT dispersion is defined as the separation of a single multi-walled CNT from its backfill body and the maintenance of the separated multi-walled CNT [25]. There are two main types of diffusion techniques that researchers have proposed. Physical techniques, such as ultrasound, mechanical stirring, and ball milling, are examples of the first strategy. To overcome the van der Waals interaction, ultrasound provides energy. Ball milling, which includes manual and magnetic stirring and is typically combined with the ultrasonic method [26], can disperse the van der Waals-induced agglomeration of carbon nanotubes, but it will decrease CNT proportions and diminish their contribution to the matrix. The second type involves a chemical process that increases the wettability of the CNT surface by typically adding covalent or non-covalent bonds as well as hydroxyl and carboxyl functional groups [27]. Fig. (3) depicts a schematic process for dry mixing and ball milling.
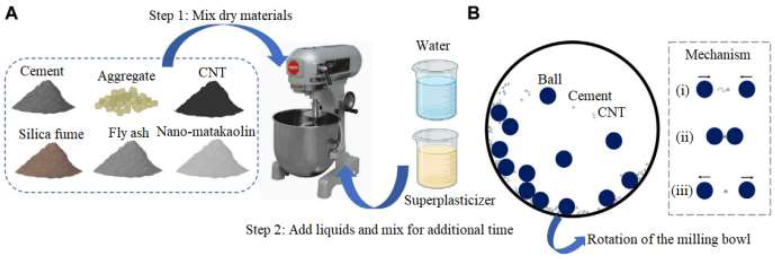
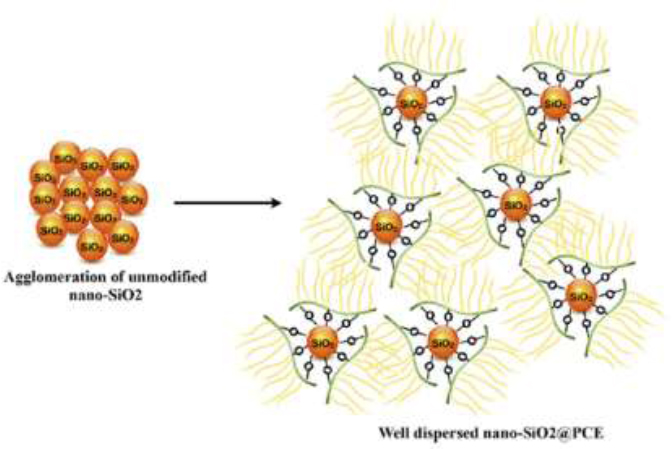
2.2. Nano Silica (Nano-SiO2)
The spherical particles in nano-SiO2 are man-made and range in size from 1 to 50 nm. Their strong pozzolanic reactivity and filling and seeding effects have drawn a lot of attention. Nano-SiO2 is superior to all other nanomaterials that can be used in cementitious materials [29]. A non-toxic, flavorless, and inorganic chemical substance is nano-SiO2. It has a spherical, flaky, net-like quasiparticle structure. Both the structural and molecular formulas are SiO2, and they are both insoluble in water [30]. A core-shell structure is created by stable chemical bonds being formed with the hydrocarbon groups on the nano-SiO2 surface (Fig. 4) [31].
When using nano-silica, it is important to understand that the material has a high surface area and, as a result, a high surface energy, which leads to particle agglomeration. The two most common forms of nano-silica are solid (powder) and suspension (nano-silica hydrolat). Since nano-silica powder agglomerates naturally, nano-silica hydrolates are typically preferred [32, 33]. However, several authors have claimed that silica sols lose their stability and coagulate at high pH values, such as in cementitious media (due to van der Waals's attractive forces) [34, 35]. As a result, when it comes to nano silica in cementitious materials, the main effects of the nanomaterial on the fresh and solidified properties of the concrete, such as pozzolanic activity, filling, and nucleation effects, are controlled by the behavior of the final silica agglomerate [36].
Fresh and hardened concrete's properties are enhanced using nano-silica. The cement is more effectively hydrated when nano-silica is added to concrete and mortar [37]. Additional calcium silicate hydrates are formed because of the pozzolanic activity to produce more force and lower free calcium hydroxide [38, 39]. The nano-silica improves the microstructure and lowers the water permeability of the concrete, increasing its durability and assisting in the reduction of the need for cement [40-42]. It is possible to produce concretes with strengths up to 100 MPa, high workability, anti-bleeding characteristics, and quick demolding times. The addition of nano-silica to eco-concrete mixtures is possible. Numerous studies have been conducted on the use of nano-silica in cementitious materials [43, 44]. According to the study [45, 46], nano-silica particles increased the stiffness and strength of an epoxy resin.
2.3. Hybrid Fiber
The failure of cementitious materials at relatively low loads is a common multiscale process that affects the long-term durability of structures because cementitious materials are typically very brittle and have low tensile strength and stress capacity [47].
Wide attention has been given to fiber reinforcement, which is now recognized as a common technique for strengthening concrete [48, 49]. The need for new concrete with excellent performance has increased with the advancement of construction technology. Therefore, finding a method to enhance the mechanical properties of concrete is crucial.
Concrete is a dense material with a low degree of elongation. Concrete's brittleness and short crack retention time are two issues that could be resolved by reinforcing the concrete with small, randomly placed fibers. Utilizing fibers with various sizes and moduli has improved the mechanical properties of cementitious composites. Additionally, it has been demonstrated that the use of hybridization enhances the mechanical performance of high-performance, fiber-reinforced, extruded cement composites.
The addition of two or more different types of fibers used as secondary reinforcement in the concrete matrix is known as hybrid fiber concrete (HFRC). Due to the ability to utilize the potential properties of the other fiber more effectively due to the presence of one fiber, these hybrid fiber composites can offer more intriguing technical characteristics. The final performance of the system typically depends on these bindings because numerous experimental studies have demonstrated that improper binding between FRP and concrete is the primary reason for the failure of FRP-reinforced concrete structures [50].
The most cost-effective way to reduce the total volume of concrete and the quantity of steel needed for a confined structural member is to use natural hybrid fiber-reinforced concrete (NHRFC). By reducing crack growth and boosting flexural strength, ductility, and energy absorption capacity, hybrid fibers help concrete achieve better tensile properties. Various fibers, including synthetic, metallic, glass, lathe, polymeric, mineral, and naturally occurring fibers, have been used in concrete. Of these, natural fibers (coir and human hair) are the most affordable and widely accessible. The hybrid composite can offer more desirable engineering properties because the presence of one fiber enables the more effective utilization of the potential properties of the other fiber, as has recently been demonstrated by numerous researchers who investigated the mechanical properties of the hybrid concept with two different fibers incorporated in a common cement matrix.
Studies have emphasized the significance of increasing concrete strength [51]. It was reported that using fiber in concrete will be a successful method of filling the void and fortifying the concrete.
Due to its extremely low tensile strength, nano concrete is like NC [52, 53]. However, by limiting crack propagation, microscale strengthening of cementitious composites can significantly increase the material's toughness [54, 55]. Steel fibers (SF) are added to nano concrete to enhance some of its properties and help promote the advantages of SF concrete [56, 57]. The characteristics of SF nano concrete are based on the interaction between SF and concrete. Understanding this interaction will allow us to assess the concrete's quality, consider the contribution of SF, and forecast the steel SF nano concrete's mechanical properties [58].
A brand-new field of study in concrete has been developed due to the development of nanoscale fibers. Recently, there has been a lot of interest in the creation of hybrid fiber systems, which combine two or more types of fibers, in the field of fiber-reinforced concrete (FRC). The efficient use of fibers to impart the best performance qualities of each constituent of fiber to the composite material is made possible by hybrid fiber systems [59]. The benefits of using hybrid systems of micro- and macro-fibers or various types of microfibers have also been highlighted by recent developments in fiber-reinforced composites [60, 61]. The advantages of using hybrid fibers are due to the multiscale structure of concrete, which includes micron and submicron scale hydration products, millimeter-scale sand, non-hydrated cement granules, and (if gravel is used as aggregate) centimeter scale temperature variations. At both micro and macro levels, the addition of fibers of various sizes enhances the properties of the composites. At the micro level, the fibers prevent cracks from forming and spreading [62, 63]. Using a single type or size of fiber may slow the spread of microcracks, but it does not prevent their emergence [64, 65].
To provide nanoscale reinforcement and successfully bridge nano cracks during loading and load transfer, several attempts have been made to incorporate nanoscale fibers into cementitious composites [66, 67]. As higher stresses are needed to form a crack when nanoscale fibers are present, the cementitious matrix's low
Cracks in cementitious materials begin at the nanoscale, and microfibers are unable to stop cracking at this level [69]. Carbon nanofilaments can inhibit cracking and delay the process of fracture. It was demonstrated by Yu et al. [21] that the mechanical strength of cementitious composites could be significantly improved by combining cementitious materials with carbon-based nano additives [70, 71].
Peled et al. [72] and Cyr [73] investigated the effect of combining low-modulus polypropylene (PP) microfibers with high-strength, high-modulus glass microfibers or polyvinyl alcohol (PVA) in extruded composites. They discovered that by incorporating PVA microfibers into the glass/PP hybrid composite, both the composite's strength and its toughness were significantly increased [74, 75]. Researchers reinforced concrete and mortar with steel microfibers and PVA. As they increased the composite's ductility, the microfibers improved the post-peak performance of the material. The microfibers added to the composite material made them more robust. The hybrid reinforced composite was stronger than both the single reinforced composite as well as any other hybrid reinforced composite. So far, all efforts have been concentrated on the use of microfibers combined with other microfibers.
3. CHARACTERISTICS AND PROPERTIES OF THE CONCRETE
Researchers from the United States and other countries typically use the Vicat method needle to determine the setting time of their experiments. Depending on the type of concrete, the initial setting time was approximately 4-7 hours, and the final setting time was approximately 6-10 hours. In comparison, the incorporation of nano-SiO2 into the concrete resulted in a reduction in the amount of time required for it to set [76]. Ltifi et al. also discovered a similar rule [77]. The deterioration of concrete that is caused by calcium leaching into the water can be stopped by adding nano-silica to the concrete [78].
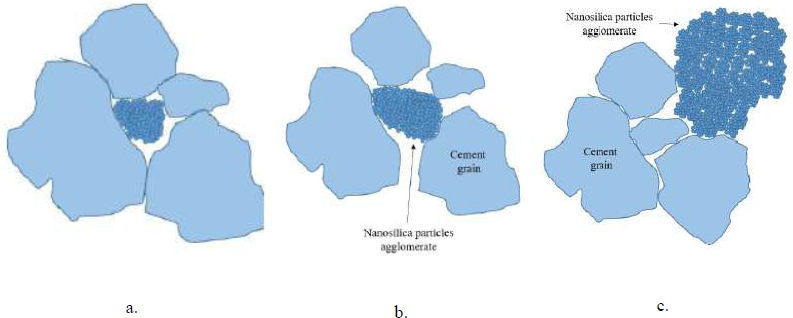
It has been suggested by several authors that the addition of nano-silica to cement-based materials results in an appreciable rise in the quantity of water that is essential to produce asphalt mixes [79, 80]. The high specific surface area of silica nanoparticles, which leads to agglomeration, is thought to be the cause of this phenomenon. If all the agglomerates are small and act as fillers to fill the space between the cement particles, then it is possible that nano-silica could theoretically improve the fluidity of the paste. However, this outcome is dependent on the size of the agglomerate. However, the number of large nano-silica agglomerates is typically indicative, as this characteristic tends to repel cement particles around it and increase the amount of void space [36, 81]. Very large nano-silica agglomerates can soak up some of the free water that is initially contributing to the fluidity of the dough [34, 36, 82]. This water does not contribute to the flowability because it is unable to escape the pores of the agglomerates where it is trapped [83]. As a direct consequence of this, the mixture's torque and viscosity both increase and the cement paste's workability suffer significantly [84, 85]. These three possible outcomes are depicted in Fig. (5).
The reduction in paste fluidity that results from the incorporation of nano-silica into cementitious materials can be quantified using the concept of the slump value [63, 80, 86]. According to Berra et al. [86], using a relatively low percentage of superplasticizers can bring the slump to a level that is more manageable and acceptable. The quantity of flow agent that must be used is determined by the number of nano-silicas that have been incorporated [87, 88] as well as their surface areas [89].
Slump is one of the important indices used to measure the liquefaction performance of concrete [90]. It is the average diameter of the concrete after the standard slump cone has been loosened. According to research [79, 91], the slump value of nano silica-modified concrete is between 80 mm and 100 mm, which is between 40 and 60 percent lower than the value of conventional concrete. Throughout the setting test, it was noticed that the freshly mixed concrete exuded trace amounts of moisture [92, 93]. When the cement was removed and replaced with nano-SiO2, the nano-SiO2 demonstrated a very high reaction capacity because of its large specific surface area and many unsaturated bonds. This makes it easier for water molecules in the surrounding area to be attracted to it and form chemical bonds. Due to this, no water segregation and no apparent exudation coming from the mixture containing the nano-SiO2 were reported [94, 95].
As a result of the loss of water, cement joints frequently experience a phenomenon known as shrinkage. The formation of cracks is a direct consequence of shrinkage, which also weakens the aggregates' ability to adhere to one another. The incorporation of nano-SiO2 was found to improve the shrinkage of lightweight aggregate concrete (LWAC), particularly the subsequent shrinkage of LWAC, according to the research conducted by Wang et al. [96]. Li et al. [76] investigated the degree to which different cement pastes shrank and discovered that the degree to which the cement shrank increased as the setting time of the cement increased. After 28 days, the cement paste experienced a shrinkage of between 0.28% to 0.70%. The progression of damage in a woven carbon fiber/epoxy composite was investigated throughout the work [97]. The most important discovery was that CNTs have an inhibiting effect on the formation of transverse cracks.
Said et al. [10] used colorimetry to determine the depth of chloride ion penetration in concrete and found that the depth of chloride ion penetration in concrete containing 6% nano-SiO2 was less than the depth of chloride ion penetration in concrete that did not contain nano-SiO2. As another point of interest, the charge, and the physical penetration depth both decreased as the silica content increased. The penetration depth of concrete that had a nano-SiO2 content of 3.8% was less than 5 millimeters when subjected to a pressure of 0.5 megapascals. The total porosity of the concrete did not change significantly, but nano-SiO2 reduced the size of the larger pores in the concrete, which resulted in a significant increase in the permeability of the concrete. This suggests that nano-silica-modified concrete has a significant amount of untapped potential in terms of enhancing permeability resistance [98]. After a short period of curing time, the pore size in the concrete reduced, resulting in a decrease in the concrete's porosity. It occurred when nano-SiO2 and fly ash were mixed into fresh concrete at the same time. One of the reasons could be the high activity and nucleation of nano-SiO2 promoted by fly ash, as well as secondary hydration. The filling effect of nano-SiO2 and fly ash could be another reason. In addition, research has shown that as the curing time for concrete samples increases, the pore size of all types of concrete samples decreases [99]. It was discovered through testing the durability of concrete with nano-SiO2 content of 0.3% and 0.9% and found that low-dose nano-SiO2 could also provide excellent waterproofing. This is because small doses of nano-SiO2 are easier to disperse [100]. Researchers [101] found that nano-silica in its colloidal state improved the durability of concrete more effectively than micron-silica.
Less amount of CNT in concrete improves mechanical and durability properties [102, 103]. CNTs strongly reinforce the cementitious matrix and hydration products and fill nanopores [104, 105]. This leads to an improvement in the impermeability of concrete and controls the propagation of cracks in concrete [106, 107]. CNTs are useful in resisting crack propagation, where they act at the nanoscale at micro and nano levels [108, 109]. They are used as fillers of pores and voids, resulting in denser reinforcement, in addition to a strong bridging effect that helps inhibit crack propagation and delay crack formation [110].
As a cementitious composite, concrete possesses a sophisticated binding system that is scientifically referred to as hydrated calcium silicate (C-S-H). There is a lot of untapped potential in cement-based concrete-CNT composites, and there is currently research being done to investigate the mechanical performance of cement-CNT composites. According to the research [111], the utilization of CNTs results in an improvement in the mechanical properties of concrete. The mechanical properties of CNTs have sparked significant interest in the possibility of utilizing them as a structural material, and it is anticipated that this will lead to significant advancements in the fields of construction design and materials [112, 113]. The mechanical properties of multi-walled carbon nanotubes (MWCNTs) were investigated in the study [114], which led to an increase in Young's modulus, tensile strength, and elongation at break. According to the findings of the study [115], rigid nanoparticles were found to have apparent enhancing effects on the responses of compression and bending.
The impact of utilizing modified CNTs to lessen the occurrence of bond slippage has been investigated [116, 117]. The results of the experiments showed that the use of CNT-modified epoxy resin improved bond strength and ultimate slip, as well as affected epoxy type, fiberboard type, the bond length of fiber-reinforced polymer (FRP), and FRP bond width. In addition, the results showed that the use of CNT-modified epoxy resin affected the epoxy type.
In concrete, the incorporation of nano-silica densifies the interface transition zone (ITZ) between aggregates and bulk cement paste. This leads to an improvement in both compressive strength and tensile strength [10, 118-121]. The ITZ scheme is depicted in both conventional concrete (Fig. 6) and nanotechnologically produced concretes (Fig. 6). Particularly noteworthy is the fact that the nano concrete possesses a denser ITZ along with a greater number of hydration products.
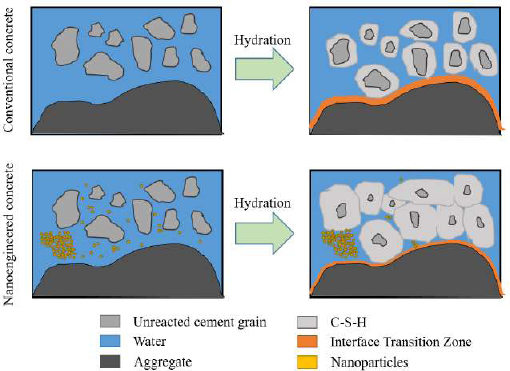
The use of nano-silica in a mixture of paste, mortar, and concrete significantly improves the mechanical properties and durability of concrete [96, 123] and reduces the porosity between cement particles. Nano-silica can improve the compressive strength, flexural strength, and durability of cementitious materials. The effect of the addition of nano-silica on the mechanical properties of cementitious materials depends on many factors, such as the dosage and the specific surface of the nanomaterial [124] as well as the water/binder ratio (w/ b) ratio, curing conditions, curing age and superplasticizer content [125].
Research [126] reported that cementitious foam concrete reinforced with single wall CNTs demonstrated up to 70% increase in compressive strength. It was also reported that when CNTs are present in the matrix, the thermal expansion coefficient decreases by 32%, and the mode 1 fracture toughness also increases significantly by more than 80% [127].
The introduction of nano-silica into FRC contributes to the compressive strength development of the composite. In this case, the use of fibers, such as polypropylene fiber, macropolymer fiber, steel fiber, glass fiber, basalt fiber, and mineral fibers, is reported [82, 128-131]. Atewi et al. [129] reported that improvements in compressive strength and split tensile strength were found in up to 4% of nano silica and 1.5% of glass fibers in self-compacting concrete. A 34% improvement in split tensile strength was observed by the authors within 90 days, compared to that of normal concrete. According to Mobini et al. [87], the addition of nano-silica with a specific surface area of 200 m2/g in a high-performance fiber-reinforced concrete (FRHPC) with 1% steel fiber led to the development of a denser ITZ between the matrix and the fibers and thus a tight bond was achieved between them. As a result, both the tensile strength and flexural strength of FRHPC were increased.
4. DISCUSSION ON THE OVERALL TOPIC FOR SCIENTIFIC VIEW
The incorporation of CNTs into conventional cement-based concrete is still in the preliminary exploration and basic research phase. Nevertheless, the potential of CNTs to improve the mechanical properties of conventional concrete is promising. Most published research has focused on cement composites reinforced with single-wall CNTs (SWNTs). The synthesis process of SWNTs is much more complex than that of multi-walled CNTs (MWNTs), and hence the cost of SWNTs is much higher than that of MWNTs. Moreover, the dispersion of SWNTs is more difficult to achieve than that of MWNTs. However, the mechanical properties of MWNT, such as compressive and tensile strength, are almost the same as those of SWNT. Therefore, MWNT has more potential than SWNT in the construction industry due to its lower cost and simpler manufacturing process.
Nano-silica is the most abundant material that makes up the earth. It has the chemical composition of SiO2, which resembles a diamond structure. It is a white, crystalline material. Nano-silica is one of the most used nanoparticles in concrete. It is a new pozzolanic material that exists in water in solid or liquid form. In the concrete industry, nano-silica is one of the best-known materials that determine the viscosity and fill level of the concrete.
4.1. Limitations of CNTs Application in Cementitious Materials
CNTs do not have the same level of widespread adoption in the construction industry as other polymer composites even though they have the potential to improve a variety of properties of cement-based materials. It is speculated that this is due to the high cost as well as the difficulty of achieving a non-homogeneous distribution within the cement matrix. As was discussed earlier in this article, proper dispersion is essential to the functioning of cement nanocomposites, whereas improper dispersion can be detrimental to the mechanical properties of the material by causing the formation of unwarranted voids. In addition, the alkaline environment that is present in the cementitious matrix has the potential to bring about secondary agglomeration of CNTs, which will make dispersion even more challenging. The prohibitively expensive nature of nanomaterials is yet another barrier that prevents their widespread implementation in the building industry. The insight gained from the efficient utilization of microfiber reinforcements serves as the inspiration for the preliminary plan to incorporate CNTs into cement-based material. Furthermore, the number of carbon nanotubes used is equivalent to between 0.5 and 1.5% of the total [132, 133].
4.2. Limitations of Nano Silica Application in Cementitious Materials
Nano silica is carcinogenic. As some nations import nano-silica to use in the concrete industry [134], the disadvantages of high cost and scarcity in certain regions of the world are unrelated to the demand for the material. One of the most obvious disadvantages of the nano-silica that is currently in the market is that it comes at a relatively high cost. Therefore, even though it has a very positive influence on the properties of concrete, its use in bulk concrete products is severely restricted due to economic factors.
5. IMPACT OF NANOMATERIAL-MODIFIED CONCRETE ON SUSTAINABLE DEVELOPMENT
Only the transportation and agricultural industries have higher annual greenhouse gas emissions, making construction a very large global industry with a high environmental impact. With the adoption of new materials and methods, many influential players in the construction sector are promoting a more sustainable future.
The sustainable construction movement presents a number of opportunities for nanotechnology, and numerous businesses are starting to use the cutting-edge properties of nanomaterials to create a construction that is cleaner and more energy efficient. However, nanotechnology has not yet had a big impact on the construction industry.
Fly ash, slags, and other industrial waste products have long been used as fillers in the manufacture of cement. These materials have frequently shown improved mechanical properties, better abrasion resistance, and other advantages, in addition to offering a good way to reuse this high-volume waste.
Application | Area | Nanoparticle Type | Major Applications |
---|---|---|---|
Construction | Concrete | Silica nanoparticles | • Reinforcement in mechanical strength • Rapid hydration |
Concrete | Titania nanoparticles | • Increased degree of hydration • Self-cleaning |
|
Concrete | Carbon nanotubes | • Mechanical durability • Crack prevention |
|
Asphalt concrete and Timber | Aluminium oxide nanoparticles | • Increased serviceability | |
Bricks mortar | Clay nanoparticles | • Increased compressive strength • Increased surface roughness |
|
Concrete | Iron oxide nanoparticles | • Increased compressive strength • Abrasion-resistant |
|
Steel | Copper nanoparticles | • Weldability • Corrosion resistance; Formability |
|
Asphalt concrete | Zycosoil | • Increased fatigue life • Higher compaction |
In particular, the dependence on particle size that comes into play with nanomaterials can have a significant impact on the bulk properties of the material. These properties are at least in part attributable to the nanoscale nature of the particles in the ash and slag. According to research, it is possible to create materials with useful properties by carefully regulating the composition and particle size of nanoadditives for cement. Table 2 lists a few uses for nanoparticles in the building industry.
During the manufacturing process for cement, numerous toxic and harmful gases are released into the atmosphere. Some examples of these gases include carbon dioxide, nitrogen oxides, and sulfur oxides. Carbon dioxide is the primary contributor to the phenomenon known as the greenhouse effect. Considering this, sustainable development in the cement industry has emerged as an emerging topic of study in the recent few years. Shen et al. [136] noted that more environmentally friendly production, recycling, and the use of alternatives to cement are effective ways to address the issues that exist today. The first two are primarily concerned with enhancing production process technology, fully recovering a variety of waste materials, increasing resource and energy utilization efficiency, and reducing emissions of greenhouse gases. Cement replacement primarily refers to the practice of reducing cement consumption through the utilization of a wide variety of industrial wastes as well as newly developed materials that are friendly to the environment.
In recent years, nanomaterials have emerged as a credible alternative to cement, which has led to their increased use. There are a wide variety of nanomaterials, each of which is produced using a distinctive approach. The manufacturing processes that are currently in use for nanomaterials have not contributed significantly to carbon emissions. For instance, the methods used in the production of nano-silica include the solid phase method, which is prepared by the physical method, the liquid phase method, which includes the chemical precipitation method and the solution gel method, and the gas phase method, which includes the chemical vapor deposition method [137]. When the chemicals are manufactured, there is no release of carbon dioxide into the atmosphere.
The initial and final setting times of cement mortar containing nano-silica were found to decrease with an increase in the replacement percentage. The use of nano-silica in concrete reduces CO2 emission.
CONCLUSION
From the literature review carried out in this work, the following conclusions can be drawn:
1. Nano-SiO2 has a large specific surface area due to its small particle size. During the mixing of concrete, many unsaturated bonds promote nano-SiO2 to absorb more water molecules, leading to a decrease in concrete collapse.
2. When nano-SiO2 is used to replace part of the cement, the high activity of nano-SiO2 helps promote the hydration reaction of concrete, which shortens the setting time of nano-SiO2.
3. When used correctly, adding nano-silica to cementitious materials helps refine the pores, which, in turn, reduces water absorption and porosity. Therefore, it improves the resistance to the penetration of aggressive ions into the concrete, such as sulfate and chloride ions, which ultimately contributes to an increase in the composite's durability.
4. On the one hand, nano-SiO2 promotes the hydration degree of concrete, causing the concrete matrix to produce more C-S-H gel, which fills the pores in the concrete matrix. On the other hand, the inactive nano-SiO2 plays a filling role. By these two aspects, the nano-SiO2 makes it possible to reduce the porous volume and make the concrete more compact. Therefore, nano-SiO2-modified concrete has excellent durability.
5. The mechanical properties of nano-silica cement materials directly depend on the amount of nanomaterial used and its specific surface area.
6. Using natural hybrid fibers in concrete as a source of material can be economical, environmentally friendly, and recyclable. Natural hybrid fibers have the highest cellulose content. The properties are suitable for their application to building and construction materials.
7. Adding nano-silica and CNT in concrete improves the performance of durability characteristics.
8. The water absorption and absorption results show that the decrease in permeability is due to the filling effect of nano silica and CNT.
Nanoconcrete is the solution to many of the difficulties that are encountered when constructing with concrete. The components that are required to make this variety of concrete can be manufactured in substantial quantities so that it is simple to acquire them. It has been observed that the use of nano-basalt fiber in a hybrid format for the reinforcement of nano concrete has not been investigated or the investigation is scarce; consequently, this aspect of hybrid fiber reinforced nano concrete should be investigated appropriately. As the construction industry transitions to a more sustainable future, nanotechnology has much to offer.
LIST OF ABBREVIATIONS
NC | = Normal Concrete |
UHPC | = Ultra-high Strength Concrete |
MWNTs | = Multi-walled CNTs |
CONSENT FOR PUBLICATION
Not applicable.
AVAILABILITY OF DATA AND MATERIALS
The data supporting the findings of the article is available in the body of the manuscript.
FUNDING
None.
CONFLICT OF INTEREST
The authors declare no conflict of interest, financial or otherwise.
ACKNOWLEDGEMENTS
Declared none.