All published articles of this journal are available on ScienceDirect.
Sustainable Construction Materials: Recycled Aggregate Concrete from Known Concrete Strength Debris
Abstract
Background:
Landfills receive construction and demolition wastes (CDW) that are the debris generated during the construction, renovation, and demolition of buildings, roads, and bridges. CDW are resources that could be used in new construction projects, thus eliminating the need for virgin materials to be mined and processed.
Objective:
The main objective of this study is to develop a novel investigation of the mechanical behavior of concrete mix design incorporating recycled aggregate concrete (RAC) from casted concrete debris of known compressive strength while meticulously monitoring the effective water-to-cement ratio.
Methods:
The following four variables were monitored while performing the concrete mix design: the percentage of recycled coarse aggregates (RCA), the percentage of recycled fine aggregates (RFA), the gradation of the recycled material used, and the original compressive strength of the casted concrete debris. The initial strength and size of the debris versus the quantity of usable recycled materials obtained were investigated. The consequence of the utilization of each variable in the final concrete mix was determined. The mechanical properties investigated were the compressive strength, flexural strength, and modulus of elasticity of concrete made with different percentages of recycled materials.
Results:
The result of this study is achieving an optimum concrete mix design that also results in minimizing the negative impact on the environment by reducing the amount of CDW being dumped in landfills.
Conclusion:
The combination of both recycled coarse and recycled fine aggregates resulted in an increase in mechanical performance of the concrete while enhancing the environmental value of the final material.
1. INTRODUCTION
Recycling of casted concrete debris to yield new concrete safeguards natural resources, diminishes the impact on declining landfill space, decreases dumping costs, and may decrease overall project cost. Thus, the construction industry has been undertaking numerous actions to diminish waste generation and improve the management of construction and demolition waste [1]. Because of the growing level of demolition, it is becoming crucial to efficiently reclaim demolition rubbles in order to preserve natural resources. Dwindling natural aggregate sources as well as increasing difficulties with waste management have strengthened the concept of utilizing recycled waste as aggregate for RAC [2].
RAC is, by definition, concrete produced by the utilization of recycled aggregate. Kou et al. [3] concluded that RAC will achieve the following requirements of green materials:
i) The material of recycled aggregates will reduce the depletion of natural resources and energy consumption.
ii) The material will be environmentally friendly.
iii) The material will lead to the realization of the concept of sustainable development.
Despite the fact that there are recognizable benefits of utilizing RAC, there are some technical impediments restricting its utilization in concrete production. RCA is actually a minor piece of concrete composed of adhered mortar (AM) attached to natural coarse aggregate (NCA) [4]. Recycled coarse aggregates (RCA) are angular with irregular surfaces, processing a higher water absorption capability, lower specific gravity, and higher LA abrasion loss; they typically fail the sulfate soundness investigation, but normally pass the magnesium soundness investigation. For a perfect comprehension of the RCA matrix, the individual parts must be identified independently [5]. Thus, freshly casted concrete composed of RCA tends to be very rough due to the angular shape and irregular surface of the aggregate. Additionally, it is more susceptible to diminishing slump rate and requires an increase in water contents because of the increase in the absorption of the mortar adhered to the aggregate and higher air contents due to the greater porosity of the recycled aggregate and the entrained air in the adhered mortar.
Li et al. [6] observed that the quality of RAC should correlate to the properties of the source of the waste concrete, the current concrete mix design and method, and the dwindling state of the recycled aggregates, and they conducted preliminary studies of RAC on the durability and mechanical properties. Although the utilization of RCA was feasible, a reduction in the behavior of the RAC was detected and should only be viewed as a normal outcome. In addition, Nagataki et al. [5] observed that the quality of the RCA is not necessarily dependent upon the properties of the attached mortar.
Padmini et al. [2] conducted experiments to investigate the effects of the original concrete properties on the RCA and the RAC. Natural aggregates (NA) of 3 different gradations with differing maximum aggregate sizes were utilized to cast concrete with 3 different compressive strengths. In addition, for those nine mixes, 3 different workabilities were investigated to cast 27 mixes. Employing a jaw crusher and modifying its opening dimensions to match the maximum size of the aggregate utilized in the original concrete, recycled aggregates were obtained to be utilized in casting the RAC samples. The results of this study indicated an increase in the compressive strength and specific gravity, and higher water absorption rate in the recycled aggregates concrete compared to the original concrete.
Hoffmann et al. [7] observed that a comparatively high quantity of water is required in concrete production to reach good workability due to high water absorption of the RCA if the aggregate is not pre-soaked. Domingo et al. [8] observed that increasing the quantity of RCA in the mix decreased the workability of the concrete, which correlated to the absorption, shape, and texture of the RCA. Thus, it might be advisable to use pre-saturated RCA or a larger amount of super-plasticizing additives to maintain the same level of workability. Nevertheless, Sagoe et al. [9] observed that mechanically processed RCA produced comparatively smoother spherical particles, which resulted in enhanced concrete workability when compared to NA.
Etxeberria et al. [10] observed that concrete produced by a full substitution of NCA with RCA caused a 20 to 25% decline in compressive strength for the same w/c ratio and cement. Additionally, it was observed that a full substitution of the coarse aggregate mandated a high quantity of cement to obtain high compressive strength and it was consequently not cost-effective. They observed that when producing medium-strength concretes, a maximum of 25% substitution was efficient. Other researchers, including Domingo et al. [8] and Sim and Park [11], observed that concrete strengths increased with the increase in RCA replacement percentages.
Kou et al. [3] reported that irrespective of the type of recycled aggregate utilized, the splitting tensile strength of the samples prior to the age of 28 days declined as a function of increasing the RCA substitution ratio. Nevertheless, it was also reported that for some types of RCA utilized, an increase in the splitting tensile strength at the age of 90 days was detected. Xiao et al. [12] also observed diminishing splitting tensile strength with increasing RCA substitution ratios but did not observe any trend of increases.
Hoffmann et al. [7] observed that the modulus of elasticity usually diminishes with an increase in recycled aggregate content and the content of crushed bricks, concrete, and tiles. Pereira et al. [13] reported that despite the increase in the RCA substitution ratio, a reduction in the modulus of elasticity of the RAC resulted; thusd, using the proper type and quantity of superplasticizer could increase the modulus of elasticity to higher values than those of referenced concrete specimens with no superplasticizer. Normally, there is a reduction in the modulus of elasticity with an increase in the RCA substitution percentages. The reason is related to the high volume of mortar with a relatively low modulus of elasticity that is attached to the natural aggregate in the RCA [12].
Knaack and Kurama [14] employed the direct volume replacement (DVR) method for casting normal-strength concrete mixtures with RCA. The DVR method assumes that the RCA is a single-phase material. An equal volume of coarse RCA substitutes for a predetermined volume of natural aggregates (NA). The mix proportioning is comparable to the method referred to in ACI 211 [15] for proportioning normal, mass, and heavyweight concrete. They concluded that the workability of fresh concrete casted by utilizing the DVR method is comparable to that of the NA concrete.
Due to the disagreements in the published literature with respect to the issue of compressive strength, incomprehensible deductions could be reached. Consequently, using RAC could be effective if careful consideration is devoted to the physical characteristics and properties of the aggregate, the physical properties of the fresh and cured concrete, and the mechanical performance. Thus, in this study, careful considerations were made to investigate those factors and to eliminate some of those disagreements.
2. MATERIALS
2.1. Source of Materials
Blended Portland cement type CEM II/A-L 42.5 R conforming to EN-197/1 [16] was used. This cement has a Blaine fineness of 0.42 m2 /g, and its relative specific gravity is 3.05. This cement is manufactured by blending or intergrinding 6-20% of ground limestone with Portland cement. It is also feasible to produce this material in the concrete mixer by mixing 6-20% of limestone fines, according to BS 7979 [17], with Portland cement. This cement is normally used for general construction work in the absence of the requirements of other special properties.
The natural aggregates (NA) consisted of deposited siliceous sand (quartz) as fine aggregates (FA) and crushed limestone as coarse aggregates (CA). Conventional potable tap water, which is free from impurities and chemicals, was used. As for recycled materials, debris resulting from tested concrete cylinder samples of known compressive strength were collected from concrete testing laboratories and divided into 5 Kg after manually pre-crushing them; these batches were then placed in the LA abrasion machine [18] for 500 revolutions and sieved for 10 minutes. The collected materials were separated into RFA and RCA. Fig. (1) displays samples of the aggregates used in the study.
Because all the recycled materials underwent the same process of acquisition, the only two factors distinguishing their quality were the initial strength of the specimens and the size (after pre-crushing). Fig. (2) displays charts of recycled materials size comparisons before and after placing them in the LA abrasion machine and comparing different samples of the same compressive strength with either a random selection of the concrete debris or only big-size debris particles. The figures clearly indicate that the smaller the pieces of debris, the more the adequacy of the obtained recycled material in terms of usable materials for the concrete mix.
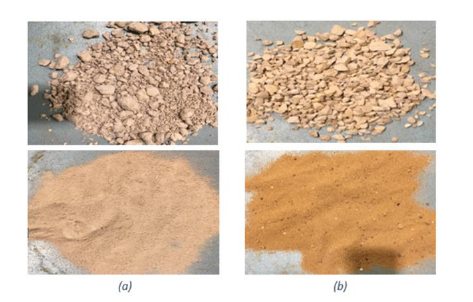
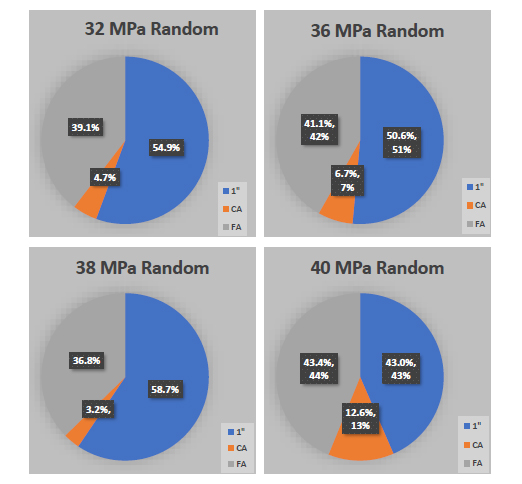

Fig. (3) displays the assessment of several samples with the same size collection process with either a big or random selection of debris but with different initial compressive strength. It could be deduced that as the initial strength of concrete increased so did the efficiency in terms of obtained usable materials.
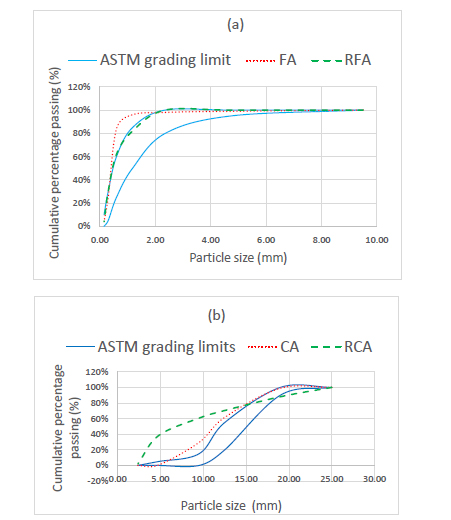
3. EXPERIMENTAL BASICS
3.1. Physical Properties of Materials
The determined physical properties of both natural and recycled materials included fineness modulus [19], nominal max aggregate size, specific gravity, and water absorption [20-22] these are presented in Table 1. Fig. (4) displays both the natural and recycled material gradation curves. It should be indicated that for the RCA grading curve, there was observed a jump because #8 sieve retained material size of 2.36 mm when added to the batch. The water absorption of RA was also confirmed to be higher than that of NA, although the specific gravity was lower, which is attributed to the existence of residue of adhered mortar with the RA, as discussed earlier.
Properties | CA | RCA | FA | RFA |
---|---|---|---|---|
Fineness modulus | 6.60 | 6.20 | 1.94 | 2.23 |
SG (ssd) | 2.54 | 2.50 | 2.71 | 2.42 |
Water absorption | 7.81 | 8.92 | 0.57 | 9.11 |
Max aggregate size | 19.05 | 19.05 | 1.18 | 2.36 |
3.2. Mixture Proportioning and Specimen Molding
A customary concrete (CC) mix was realized using natural aggregates. The recycled concretes were casted, maintaining constant the mixture proportions of CC. In two samples, natural sand was replaced by 20% and 50% of RFA (F20 and F50), and in one sample, natural aggregates were replaced by 20% RCA (C20). The aggregates were used in an air-dry state. The mixture proportions of different concrete are presented in Tables 2 and 3. The effective water was calculated by deducting from the total water amount the water amount needed for the complete aggregates saturation (SSD), estimated on the basis of water absorption values of different aggregates presented in Table 1.
Proportions | CC | F20 | F50 | C20 | |
---|---|---|---|---|---|
C (kg) | 1 | 6.62 | 6.62 | 6.62 | 6.62 |
FA (kg) | 2 | 13.26 | 2.65(RFA) / 10.61 | 6.63 (RFA) / 6.63 | 13.26 |
CA(kg) | 3 | 19.88 | 19.88 | 19.88 | 3.98(RCA) / 15.9 |
w/c (Water L) Design |
0.6 (4) | 0.6 (4) | 0.6 (4) | 0.6 (4) | 0.6 (4) |
w/c (Water L) Effective |
- | 0.36(2.38) | 0.33(2.15) | 0.28(1.80) | 0.35(2.33) |
The mixing procedure was performed in compliance with ASTM C192 Standard Practice for Making and Curing Concrete Test Specimens in the Laboratory [23]. Concrete was mixed in a rotating drum mixer. First, the required coarse aggregates were placed in the mixer with 20% of the required water quantity and mixed for 1 minute, while progressively adding the fine aggregates, cement, and the rest of the water quantity. The mixer continued to rotate for 3 minutes, followed by 3 minutes rest, and finally, 2 minutes mixing. Subsequently, the slump test was performed according to the ASTM C143 Standard Test Method for Slump of Hydraulic-Cement Concrete [24]. Cylindrical specimens of dimensions 150 mm by 300 mm were casted for compressive strength testing [25] and elastic modulus testing [26], whereas beams of size 450x150x150mm were utilized to determine the flexural strength [27]. All samples were un-molded after 24 hours and immersed in a water tub for curing at a room temperature of 22 ± 2 °C [23]. Moreover, the whole process was conducted twice to ensure the consistency of the results.
Material (kg/m3) | CC | F20 | F50 | C20 |
---|---|---|---|---|
Water | 251 | 251 | 251 | 251 |
Cement | 416 | 416 | 416 | 416 |
Natural sand (FA) | 834 | 667 | 417 | 834 |
Recycled fine aggregates (RFA) | - | 167 | 417 | - |
Natural coarse aggregates (CA) | 1250 | 1250 | 1250 | 1000 |
Recycled coarse aggregates (RCA) | - | - | - | 250 |
Water (total) | 251 | 251 | 251 | 251 |
Water (effective) | 150 | 135 | 113 | 147 |
Water/cement (total) | 0.6 | 0.6 | 0.6 | 0.6 |
Water/cement (effective) | 0.36 | 0.33 | 0.28 | 0.35 |
4. RESULTS AND DISCUSSION
4.1. Concrete Testing Results
4.1.1. Slump Test
The concrete slump test is an indication of the consistency of fresh concrete prior to curing. Its purpose is to verify the workability of freshly mixed concrete, and consequently, the ease with which concrete flows. It can also be used as an indicator of an inadequately mixed batch. The slump test was conducted according to the ASTM C143 Standard Test Method for Slump of Hydraulic-Cement Concrete [28], and the results for the different concrete mixes are presented in Table 4. The slump for F20 and F50 mixes was found irrelevant due to the higher water absorption of RFA compared to natural FA. As for the C20 mix, the slump was slightly different, and this is due to the slight difference in water absorption between RCA and CA.
Concrete Mix Type | CC | F20 | F50 | C20 |
---|---|---|---|---|
Slump (mm) | 20 | ≈0 | ≈0 | 10 |
4.2. Compressive Strength
The results of the compressive strength obtained by crushing the concrete cylindrical specimens according to the ASTM C39 Standard Test Method for Compressive Strength of Cylindrical Specimens [25] are presented in Table 5. The test series was conducted twice to ensure the conformity of the results. The concrete cylinders were crushed according to the targeted ages of 7, 14, and 28 days. The compressive strength of RAC mixes was relatively higher than that of CC mix. The maximum increase in the compressive strength of the RAC versus the CC mix is presented in Table 6. The higher compressive strength achieved in all RAC can be credited to the lower actual water/cement ratio of recycled concrete compared to conventional concrete, and this is due to the higher water absorption of recycled materials (RFA, RCA) compared to natural material (FA, CA). This higher water absorption is evident in the calculated effective w/c mixes of concrete CC and C20, which have almost identical w/c effective values, and concrete C20 showed a 43.8% improvement in compressive strength, which is an indication that RCA results in an improved performance in concrete mixes compared to NA. Moreover, FA20 mix displayed an effective decrease in w/c of 8.3% compared to the CC mix, and yet realized an overall 41.1% increase in compressive strength. Similarly, FA50 mix displayed an effective decrease in w/c of 22.2% and an overall increase of 60.27% in compressive strength.
4.3. Modulus of Elasticity
The modulus of elasticity was obtained using ACI empirical equation and through an experimental study conducted according to ASTM C469 Standard Test Method for Static Modulus of Elasticity and Poisson’s Ratio of Concrete in Compression [29]. The ACI318 [30] empirical equation is as follows:
![]() |
(1) |
Where,
Ec is the modulus of elasticity of concrete (GPa);
Wc is the unit weight of concrete (Kg/m3);
The experimental results presented were the averages of three specimens for each reported value. The results are shown in Table 7 and clearly display a variance between the two methods that range between 2.5 to 25%. Moreover, RAC presents a modulus of elasticity that is always higher than the CC mix between 10 to less than 1%. This fact can be attributed to the higher compressive strength of recycled concretes (Fig. 5).
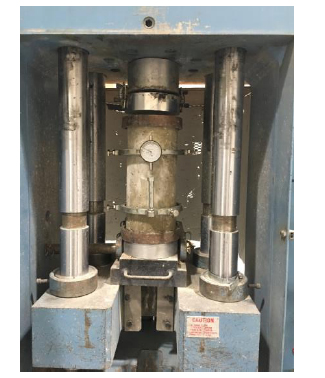
f’c (MPa) | CC | F20 | F50 | C20 | ||||||||
---|---|---|---|---|---|---|---|---|---|---|---|---|
Age | Test#1 | Test#2 | Average | Test#1 | Test#2 | Average | Test#1 | Test#2 | Average | Test#1 | Test#2 | Average |
7 days | 15.5 | 16.8 | 16.15 | 17.9 | 21.8 | 19.9 | 22.6 | 20.6 | 21.6 | 19.5 | 19.6 | 19.55 |
14 days | 19.5 | 18.7 | 19.10 | 22.9 | 28.3 | 25.6 | 28.0 | 26.9 | 27.5 | 26.4 | 22.8 | 24.60 |
28 days | 22.1 | 21.6 | 21.90 | 28.5 | 33.2 | 30.9 | 33.4 | 36.8 | 35.1 | 32.1 | 31.7 | 31.40 |
Modulus of elasticity (GPa) | CC | FA 20 | FA 50 | CA 20 |
---|---|---|---|---|
Ec (experimental) | 31.31 | 34.68 | 33.45 | 31.60 |
Ec (empirical) | 24.98 | 30.97 | 32.61 | 30.26 |
% Difference vs. empirical | 25.34 | 11.98 | 2.58 | 4.43 |
4.4. Flexural Strength
Six experimental beams specimens of 450x150x150mm were used to obtain the concrete modulus of rupture according to ASTM C78 Standard Test Method for Flexural Strength of Concrete [27], and the values were compared to ACI318 [30] empirical equation:
![]() |
(2) |
Where,
fr is the modulus of rupture of concrete (MPa);
The experimental results are the averages of three specimens for each reported value. The F20 modulus of rupture was 12.5% higher than that of the CC mix, reflective of the higher compressive strength of RAC. Once again, the experimental results are consistently higher than the empirical calculation values, as shown in Table 8.
5. OBSERVATIONS
Based on the experimental results, the following observations could be made:
(a) The aggregates produced from concrete cylinder debris had lower specific gravity and higher absorption than natural aggregates.
(b) The use of RAC imposed no problems with respect to workability. The workability issue did not affect the casting of the concrete cylinders and beam specimens.
Experimental Results | ACI Empirical* fr (MPa) |
||||
---|---|---|---|---|---|
ID# | Type | Load (N) | fr (MPa) | Average fr (MPa) | |
N1 | CC | 31076 | 4.143 | 4.00 | 2.90 |
N2 | 27698 | 3.693 | |||
N3 | 31251 | 4.167 | |||
R1 | RFA | 35878 | 4.784 | 4.50 | 3.45 |
R2 | 33862 | 4.515 | |||
R3 | 31500 | 4.200 |
(c) The compressive strength of the RAC mix was higher by a minimum of 9 MPa and as much as 14 MPa than that of the CC mix of the same water-cement ratio and similar NA.
(d) At 20% replacement of FA or CA, the increase in strength was around 40%, and at 50% replacement of FA, the increase in strength was around 60%.
(e) The grading of RFA produced by crushing concrete cylinder debris was the same as FA without modification. The existence of more RFA resulted in a much higher compressive strength, which is attributed to the existence of fine cement residue within the RFA.
(f) Fig. (2) indicates that random debris from the same original strength concrete does produce more useful recycled aggregates than big debris particles. Whereas, Fig. (3) indicates that the higher the concrete strength of the debris, the higher the percentage of useful recycled aggregates that could be obtained whether random or big debris particles were selected.
CONCLUSION
In the foregone investigation, recycled aggregates produced from crushed concrete cylinders debris were investigated to determine their influence on the mechanical properties of concrete. This study was conducted under the assumption that only conventional equipment could be used to process crushed concrete cylinders’ debris into recycled aggregates. Consequently, this limited laboratory research experience has shown that recycling concrete is feasible for producing structural concrete. While the cost of the crushing and sizing operation may be higher for recycling concrete into aggregates than for producing NA, all costs should be considered; it is believed that in many cases, there will be reduced transportation costs.
The laboratory data indicate that the recycled material is adequate for use as concrete aggregates. More specifically, a significant increase in RAC mix strength and mechanical properties compared to CC mix was detected, attributing to the cement residues. Bearing in mind the approval criteria for structural concrete in the prevailing structural concrete codes, it is only theoretically reasonable to cast concrete structures with RAC, but additional investigations on the serviceability of RAC structural components are essential and required.
Finally, based on the results obtained from this study, it appears that RAC would result in a stronger concrete than NA.
LIST OF ABBREVIATIONS
CDW | = Construction and Demolition Wastes |
RAC | = Recycled Aggregate Concrete |
NCA | = Natural Coarse Aggregate |
AM | = Adhered Mortar |
NA | = Natural Aggregates |
CA | = Coarse Aggregates |
FA | = Fine Aggregates |
CC | = Customary Concrete |
CONSENT FOR PUBLICATION
Not applicable.
AVAILABILITY OF DATA AND MATERIALS
The data supporting the findings of the article are available within the article.
FUNDING
None.
CONFLICT OF INTEREST
Dr. Camille Issa is on the Editorial Advisory Board of The Open Construction and Building Technology Journal.
ACKNOWLEDGEMENTS
The authors highly appreciate the support of the Civil Engineering Laboratory at the Lebanese American University and, more specifically, the assistance of the Lab Technician, Mr. George Shakour.