All published articles of this journal are available on ScienceDirect.
High-cycle Fatigue Behaviour of S460N Steel Grade Materials and Bolted Joints Processed by Laser Cutting
Abstract
Background:
Prompted by the EN 1090 standard, an important evolution has been observed in recent years about steel structures execution. Laser cutting is appealing for high machining speed and precision in implementation of details with complex geometry, but requires consideration for the effects of the inherent thermal process.
Objective:
The present study investigates the correlations between material properties altered by the laser cutting process and behaviour of the material and of structural joints subjected to high-cycle fatigue.
Method:
High-cycle fatigue tests on material samples and on structural bolted connections were carried out in order to correlate the structural response with material properties. For this purpose, hardness and residual stresses were analysed in depth, from the cutting surface inward and specimens processed using different laser cutting parameters and post-annealing treatments were investigated.
Results:
High-cycle fatigue tests on material samples and on structural bolted connections, processed by laser cutting, show a favourable fatigue behaviour of S460N steel, despite the high values of hardness on cut surface, in agreement with Eurocode 3 fatigue category FAT160 and FAT90, respectively for base material and drilled holes.
Conclusion:
Structural bolted connections made of S460N steel cut by laser exhibit a favourable fatigue behaviour. Local hardness is an important indicator, favourably complemented by the residual stress distribution to understand the effects of laser cutting and correlate them with the high-cycle fatigue behaviour.
1. INTRODUCTION
In the last years, the introduction of the harmonized standard EN 1090-1 [1] changed the execution of steel structures through the introduction of the new concept of execution class (EXC) and, consequently, the definition of new requirements for structural components and steel structures.
The EN 1090-2 standard [2] provides for the use of laser cutting technology both for edge cutting and for holes execution, thus allowing more streamlined solutions than possible by the traditional mechanical cutting, which often requires post-machining treatments. Laser cutting is particularly appealing to realize structural details with complex geometry and requiring high cutting precision, as in the case of tubular structures with circular hollow sections.
As with all thermal cutting processes, laser cutting introduces a Heat Affected Zone (HAZ) in the cutting edge region, which can influence - due to local embrittlement - the performance of structural details subjected to high-cycle fatigue loading. The complexity of the physical mechanisms governing the laser cutting process [3], such as the two-phase transition of melting and evaporation, the flow of the service gas, etc., plays a fundamental role altering the material properties in the HAZ and, consequently, the structural response of the machined elements.
Local HV10 hardness of the cutting surface, with limitations proposed by the standard EN 1090-2 [2], certainly provides important information, but needs to be complemented by phase composition and residual stresses data to explain the behaviour of structural elements and joints subjected to high-cycle fatigue loading. For these reasons, a study was accomplished to investigate: i) the effect of the laser cutting parameters on both mechanical properties of S460N steel grade material and elemental bolted joints; ii) possible correlations between relevant material properties altered by laser cutting and response both of material and of structural joints subjected to high-cycle fatigue loadings; iii) the effects of post-process annealing on the high-cycle fatigue performance of bolted joints.
2. MATERIAL PROPERTIES AND LASER CUTTING PARAMETERS
The study was carried out on a structural steel, S460N steel grade, supplied in rolled plates of 2500 mm x 12000 mm and 5 mm thickness for coupon specimens, in addition to 5 mm and 10 mm plates for the elemental bolted connections.
The main mechanical properties and chemical composition of S460N steel plates are summarized in Tables 1 and 2, respectively.
Thickness (mm) |
Aver. Yield Strength (MPa) |
Aver. Tensile Strength (MPa) |
A% Elongation (%) |
---|---|---|---|
5 | 506 | 655 | 25.7 |
10 | 516 | 647 | 23.4 |
Thickness (mm) |
C (%) |
Si (%) |
Mn (%) |
P (%) |
S (%) |
N (%) |
V (%) |
Mo (%) |
Ni (%) |
Cr (%) |
Cu (%) |
CEV (%) |
---|---|---|---|---|---|---|---|---|---|---|---|---|
5 | 0.19 | 0.25 | 1.54 | 0.011 | 0.002 | 0.001 | 0.074 | 0.01 | 0.42 | 0.05 | 0.04 | 0.50 |
10 | 0.17 | 0.21 | 1.54 | 0.012 | 0.003 | 0.006 | 0.071 | 0.00 | 0.42 | 0.04 | 0.04 | 0.48 |
Fiber lasers were used for their energy efficiency, appropriate to cut thick plates used in structural applications. Two sets of operating parameters were used, representing two limit conditions commonly adopted in the industrial practice. The two sets, VT1 and VT2, were adopted to cut both plates (5 mm and 10 mm), to produce both coupon specimens and bolted joint components, including cover and central plates. Details are summarized in Table 3.
Thickness (mm) |
Cutting Set-up | Cutting Speed (mm/min) |
Beam Power (W) |
Pressure (bar) |
Nozzle Diameter (mm) |
Stand Off (mm) |
Focus (mm) |
---|---|---|---|---|---|---|---|
5 | VT1-5mm | 3000 | 4000 | 0.8 | 1.0 | 1.5 | 2.7 |
5 | VT2-5mm | 1800 | 2000 | 0.8 | 1.0 | 0.7 | 2.7 |
10 | VT1-10mm | 2100 | 5000 | 0.7 | 1.5 | 1.5 | 1.7 |
10 | VT2-10mm | 1300 | 3000 | 0.5 | 1.5 | 1.5 | 1.7 |
The good quality of surfaces cut by the fiber laser is confirmed by the low roughness see Table 4: the mean height of the roughness profile (Rz5) is in agreement with the EN ISO 9013 standard [4], and fulfils the limit proposed by EN 1090-2 [2] for the more strict execution class EXC4, requiring not to exceed Range 3. For 10 mm thick elements cut using both sets of parameters, Table 4 reports Rz5 values measured at the following 3 sections: at the laser beam input (a); at mid specimen thickness (b); at laser beam output (c).
Setup | Section (a) | Section (b) | Section (c) | Range |
---|---|---|---|---|
VT1-10 | 4.45 μm | 3.67 μm | 7.25 μm | 1 |
VT2-10 | 8.85 μm | 6.27 μm | 21.28 μm | 2 |
3. ANALYSIS OF THE HEAT AFFECTED ZONE
This study has a twofold aim: i) to investigate the correlations among material properties of the steel processed by laser cutting and the high-cycle fatigue endurance; ii) to identify the most representative material properties/parameters and consequently the procedure to appropriately set the laser cutting process.
At present, in addition to the quality of the cutting surface, the EN 1090-2 standard [2] requires only checking the local HV10 hardness on the surface produced by the thermal cutting of elements subjected to high cycle fatigue, setting the limit to 380 HV10. This limit is important but is not sufficient to assess the actual response to mechanical fatigue. In this respect, microstructure, microhardness and the residual stress trend are all important indicators of the laser cutting effects on the HAZ. It is worth noting that the thickness of the HAZ increases approximately in a linear way along the direction of pulse penetration, from input toward output region of the laser beam, with a maximum value lower than 0.5 mm, as observed in other experimental campaigns [5]. The HAZ exhibits an increase of hardness on the cut surface, with values higher than the upper limit provided for by the standard. Corresponding HV1.0 values are summarized in Table 5; HV1.0 hardness is investigated to define the hardness profile along the depth from the cut surface. Despite the increase of hardness, tests made both on the material and on the bolted joint show that this increase is not directly correlated with the high cycle fatigue endurance. This aspect seems to support the importance of investigating hardness together with other parameters useful to estimate the fatigue behaviour of structural elements.
Thickness | Base Material | VT1 | VT2 |
---|---|---|---|
5 mm | 357 | 522 | 484 |
10 mm | 243 | 472 | 596 |
Another aspect of importance for high cycle fatigue response is the residual stress distribution resulting from the thermal process on the cut surface and region underneath. Fig. (1a) shows the residual stress distribution obtained in a previous experimental campaign [6], where critical values of tensile stress were observed along the laser cutting direction (ϕ=0°), whereas surface stress was compressive along other directions. This aspect is confirmed in the present study and showed in Fig. (1b), where residual stress was obtained by XRSA on the cut surface using the “sin2ψ method”, following specific SAE standards [7, 8]. Residual stress on the cut surface, corresponding to a depth equal to zero in Fig. (1a), is tensile or weakly compressive along the laser cutting direction (σ11); it is worth noting that the critical tensile stress is observed in the thinner plate (5mm) for VT1 laser cutting parameters, i.e., high cutting speed and power.
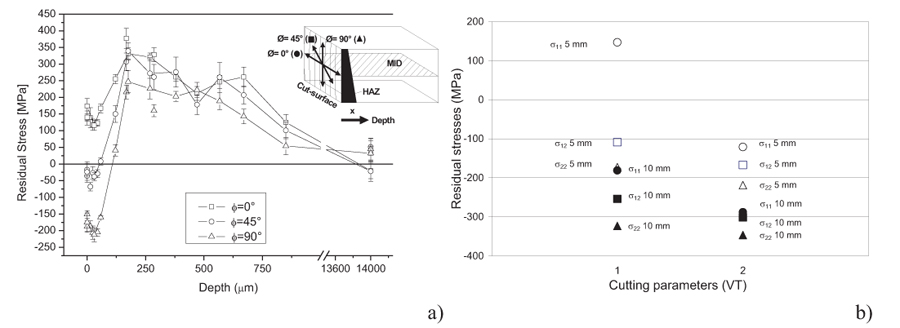
4. HIGH-CYCLE FATIGUE TESTS AND MAIN RESULTS
In order to investigate possible correlations of the altered material properties in the HAZ, tests were carried out according to Eurocode 3 Part 1-9 [9], both on the base material and on the elemental bolted joint. In detail, a campaign of high-cycle fatigue tests in reverse bending mode was made on 5 mm coupons processed by laser cutting, using both sets of parameters (VT1 and VT2). The geometry of the coupons and the S-N (Δσ-cycles) curves with the relevant code limits (line) are shown in Fig. (2). It is worth noting that the experimental results are well above the limits enforced by the Eurocode and that not evident effects are exhibited due to the cutting parameters in term high-cycle fatigue performance.
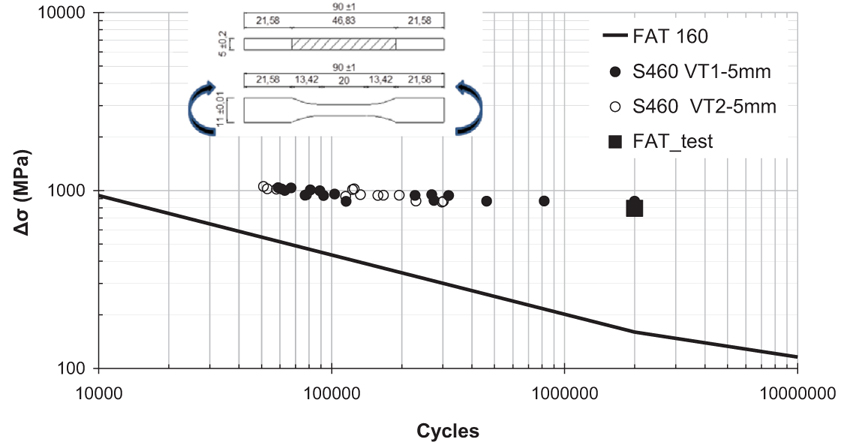
To study the response of structural joints to high-cycle fatigue, the bolted connections were tested in tension, with stress ratio R=0.05. The adopted test setup is shown in Fig. (3), tests were carried out using a servocontrolled electro-hydraulic actuator MOOG, characterized by a maximum stroke of ± 500 mm and a load cell with a maximum capacity of 500 kN. Geometry of the relevant elements of bolted connection joints is shown in Fig. (4a).
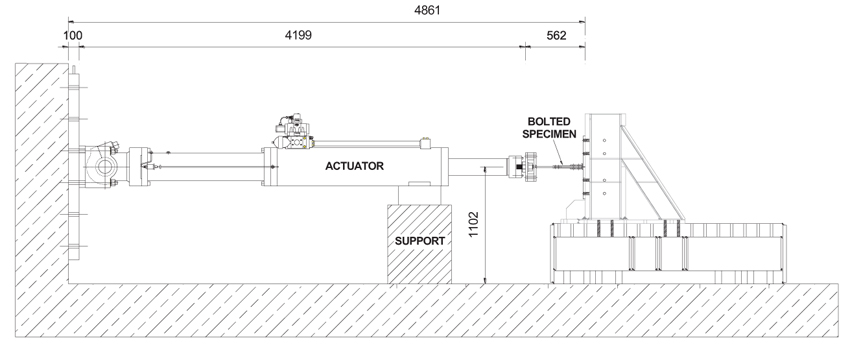
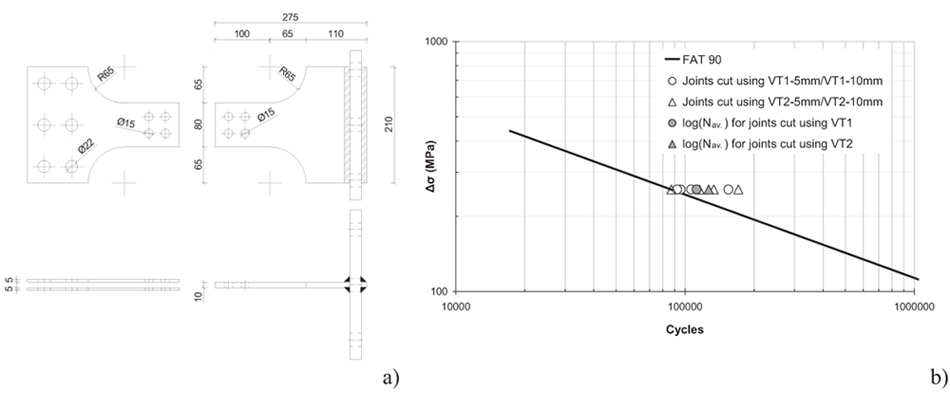
The bolted joints exhibit a favorable behaviour, in agreement with the Eurocode 3 Part 1-9 [9], characterized by fatigue surface cracks started in the cut hole of the plates and more frequently in the 5mm cover plates.
A careful observation of Fig. (4b) shows that the performance of the elemental bolted joints is affected by the laser cutting parameters, although not in a substantial way. This aspect is confirmed by the higher value of the average number of cycles to failure, log (Nav.), correlated to VT2 laser cutting parameters when compared with VT1 test results. In fact the reference fatigue strength Δσ correlated with the detail category C stated in the Eurocode 3 Part 1-9 [9] is directly related to the average value Nav. of test cycles to failure by the following relation:
![]() |
(1) |
It is worth noting the correlation between residual stress and the high-cycle fatigue endurance. In fact, the 5mm cover plate characterized by tensile stress or low compression along the laser cutting direction exhibit more frequently fracture events. This correlation is confirmed by the experimental results on bolted specimens tested after an annealing treatment. In detail, both coupon and bolted joints were subjected to an annealing of 3 hours at 360÷390°C, a process temperature chosen to allow relaxation of the residual stresses without modifying the HAZ neither in phase composition nor in grain size. High cycle fatigue tests on annealed specimens exhibit no significant effect in the case of base material, whereas a more favorable behaviour is observed for the bolted joints (Fig. 5).
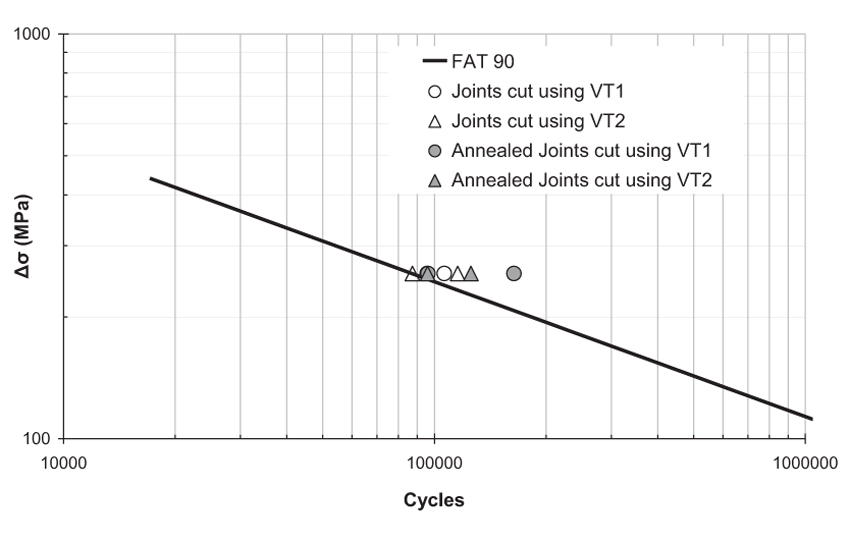
As expected an annealing process reduces local hardness on the cut surface, but the coupon specimens and bolted joints did not exhibit the same benefit in terms of high cycle fatigue performances. This result supports the conclusion that no direct correlation exists between hardness and high cycle fatigue endurance, pointing out the importance of investigating hardness together with other parameters, to correctly evaluate fatigue behaviour of structural elements.
In this context, residual stresses can play an important role in the high-cycle fatigue response when tension or low compression is observed along the laser cutting direction. This aspect is supported by the experimental results of annealed bolted joints where the critical elements are the 5mm cover plates, characterized by tension on the cut surface.
CONCLUSION
This work investigates the effects of laser cutting on the fatigue life of structural elements made of S460N steel grade. To estimate their performance, tests were carried out on both coupon and bolted connection specimens. Laser cutting was executed using different setups commonly used in industrial applications for straight/round shape and thickness of cut edges, to evaluate their effects on high-cycle fatigue endurance. Main parameters are laser power, cutting speed and workpiece thickness.
For this reason, the performance of laser cut specimens extracted from S460N structural steel plates was compared. Hardness and residual stress, were analyzed near the cut edges of both coupon and bolted connection specimens. The main results are listed herein:
- Coupons processed with both sets of cutting laser parameters meet the code requirements for high-cycle fatigue applications. In fact, the fatigue category proposed by Eurocode 3 for base material, FAT160, is adequate.
- Bolted connections made by laser cutting also meet the code requirements for high-cycle fatigue applications; the fatigue category proposed by Eurocode 3 for drilled holes, FAT90, is satisfied.
- Hardness values observed on the cut surface are higher than the value proposed by the EN1090-2 standard [2] as 380 HV10. In spite of this result, both coupon specimens and bolted joints exhibited a favourable behaviour.
- The residual stress distribution in the HAZ is an important parameter to predict high-cycle fatigue response.
- Setups of laser cutting parameters affect the high-cycle fatigue endurance of bolted joints.
- The annealing process which is finalized to remove residual stresses without modifying the phase composition and the grain size plays a favorable role in the high-cycle fatigue behaviour of bolted joints.
CONSENT FOR PUBLICATION
Not applicable.
CONFLICT OF INTEREST
The authors declare no conflict of interest, financial or otherwise.
ACKNOWLEDGMENTS
The present research was funded by a grant from the BLM-Group that is gratefully acknowledged. Nonetheless, conclusions reported here are those of the authors and may not reflect those of the sponsor.