All published articles of this journal are available on ScienceDirect.
Bio-Composites to Tackle UK Built Environment Carbon Emissions: Comparative Analysis on Load-Bearing Capacity, Hygroscopic and Thermal Performance of Compressed Earth Blocks with Addition of Industrial Hemp Waste
Abstract
Background:
The built environment contributes up to 47% of the UK’s CO2 emissions. Typically, building materials have an energy intensive life cycle. The UK construction industry generated 100 million tonnes of total waste in 2012. Only half of this was diverted from landfill. Facing this scenario, a mainstream transition towards biological materials in the building sector is encouraged to reduce embodied energy and carbon and to divert construction waste from landfill.
Objective:
This research aims to inform UK producers that there are available bio-composite materials for construction that can meet the mainstream requirements.
Method:
This paper analyses the effect of the addition of waste from industrial hemp agriculture to Earth Blocks on the performance of building products. To avoid potentially negative consequences of food displacement, an agricultural by-product from industrial hemp production was used. Hemp was also selected due to its known superior hygrothermal performance.
In the study, fine hemp shiv was added to Compressed Earth Blocks’ mix following three different Earth/Hemp ratios (75/25; 62.5/37.5; 50/50) also a control series. The compressive strength, conductivity and moisture performance were tested, analysed and then compared with the mainstream values.
Results:
The results revealed that blocks’ load-bearing capacity reduced and thermal conductivity also reduced, hence increasing its insulation capacity. The moisture performance also reduced as hemp ratio increased. In comparison with the mainstream products, the results comply with the standard requirements. Thermal capacity overperformed mainstream products.
Conclusion:
A closed loop approach for the construction industry is possible. Bio-composite materials offer the industry an option for the reduction of embodied energy, carbon emissions and construction waste, while meeting industry standards and building regulations.
1. INTRODUCTION
The main driver for this paper is the relevance that building sector has in the environmental disturbances leading to this climate change [1] [2] [3] [4]. It is this sector which accounts with more than half of UK’s greenhouse gases (GHG) basket [5] [6]. Over 80% of emissions from the building sector are derived from operational energy use. During construction, it is a common practice to use high embodied energy (EE) materials and it is very likely required aggressive methods to set them up. Although at present, there are only 15% of the whole sector emissions [5] as buildings energy efficiency is improving, the importance of EE and end of life waste become crucial to reduce emissions in the building sector; for instance, the principles set by cradle-to-cradle [7], One Living Planet [8], circular economy framework [9] and the 12th United Nations sustainable development goal [10]. These principles suggest a systemic closed loop approach to the economy, the environment and the society, and praise for a transition towards regenerative nature inspired systems with the main aim of retention and creation of capital, moving away from eco-efficiency and towards eco-effectiveness.
Through the Climate Change Act 2008, the UK has committed to cut down domestic CO2 emissions and it has developed its own decarbonisation plan for 2050 [11]. The 2050 decarbonisation plan proposes very significant policies and regulations involving the built environment. Most of them are focused on retrofitting the existing building stock in terms of energy performance and consumption behaviour [6]. The plan was to cut off many (80%) of the built environment’s emissions acting on the vital few (20%) factors involved, buildings energy performance and efficiency. Once these strategies are applied, home energy efficiency will improve thus lowering “In use” emissions. Then, the emissions related with manufacture grow significantly. It is represented in (Fig. 1).
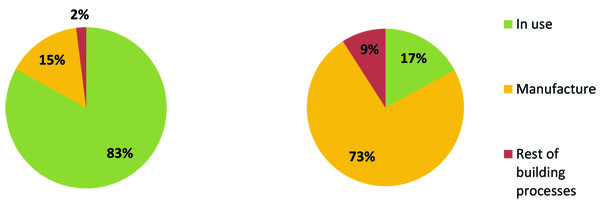
It is a common practice to utilise methods and products that use huge amount of energy at every stage of the process from production to installation, including transport and infrastructure. Additionally, some of those processes are high carbon emitters due to chemical reactions not involving fuel or electricity, thus releasing a very significant quantity of GHG, mainly CO2, to the atmosphere. Therefore, it is necessary to investigate building technologies and products to propose further approaches to institutions and industry and thus promoting a truly low carbon use not only for increasing efficiency in the sector but as well increasing resilience to energy shortages or price escalations.
The purpose of this study was to develop a bio-composite building product which could be integrated in the mainstream whilst it is truly sustainable and complying with building standards and regulations. To do so, fine hemp shiv has been added to earth according to three different Earth/Hemp ratios. Four series of samples of Compressed Earth Blocks (CEB) were produced. Their compressive strength, thermal conductivity and moisture performance were tested, analysed and discussed. Then a comparative analysis with other similar products was performed and their differences were also discussed .
2. LITERATURE REVIEW
The approach taken by the author to carry out this investigation entails a prior literature review to further understand the natural and building characteristics and environmental credential of the materials subject to this study. Following sections discuss both the materials and the building technology selected to develop an enhanced bio-composite and analyse its mechanical, hygroscopic and thermal characteristics in comparison to mainstream standards. Literature on CEB technology has demonstrated its potential to fulfil the purpose of the question proposed in this study. Earth blocks are already standardised and commercially available in EU. CEB technology provides a building material with less embodied energy than conventional masonry products (fire clay brick or concrete blocks) and it has a potential to lower the emissions of the UK built environment. At the same time, the addition of hemp shiv to the mix has the potential to improve insulation and moisture performance of the blocks, hence developing an enhanced bio-composite that can reach a closed loop cycle
2.1. Earth
Literature suggests that earth as a material for construction is extensive and broadly available [12] [13] [14] [15] [16] [17] [18] [19] [20]. It is found in the vernacular architecture all over the world [21]. Paul Jaquin [22] states that about one third of the world population lives in earthen buildings. Earth in construction is well-known for its high thermal inertia. It is on high diurnal temperature variation climates where traditional earth edification performs energetically better than modern ones, besides sustainability issues. So, earth is a building material which is already in a global mainstream with extensive knowledge available, it belongs to our heritage as humans and it has a high heat capacity. This makes earth an ideal material to be the host for an improved bio-composite building material.
2.2. Compressed Earth Block, CEB
CEB is evolved modular earth construction typology adobe that adds some great characteristics from the monolithic typology rammed earth [23]. It is CEB´s modular characteristic which makes masonry principles applicable and well spread around builders [12] [24]. Each block behaves as a monolithic earth element; high compaction levels, low water consumption and a better structural behaviour [25] [26]. Block production is described which promotes extensively formed basic brochures to very detailed manuals explaining history, technology, and methodology also giving a business plan promoting development [13] [27] [28] [24]. Machinery is the key stone of CEB technology. Depending on the machinery employed, production rate could be around 500 blocks/day [13]. Otherwise, using hydraulic or industrialised machinery, production rises considerably [29] demonstrating the capability of this technology to be industrialised. Most of the CEB normative is implied in earth codes or it has its own. Relevant for this study is the Spanish standard UNE 14410, specific for CEB. Earth blocks are treated as a masonry element for walls and partitions. Likewise, its specifications and test methods are repeatedly referenced to fire clay bricks or concrete blocks standards [30].
Compressed earth blocks, CEB, have been reported to be low embodied energy and low carbon emitter technology for construction as well as they are flourishing in different European countries as a mainstream option to meet regulations and standards. However, earth blocks stabilised or not are reported low thermal and hygric performance. These characteristics are very important in the UK built environment in order to meet regulation and standards.
2.3. Hemp Shiv
Aiming at this study for enhanced bio-composite material, hemp should act as an additive to earth. It is expected that hemp addition would ameliorate CEB hygro-thermic performance [31] [19]. Although is not a common material in construction, it is gaining credibility and support. It is an example of its use to create monolithic structures when mixed with lime. Whilst hemp and lime structure use a gross shiv of hemp hurds, fine hemp shiv is utilised to allow an adequate particle size distribution within the mix [32] [19]. However, besides just a few studies on plastering products and adobe [19], the influence of hemp addition to earth has not received enough attention in terms of building technologies research. Literature on industrial hemp as building material clearly suggests potential improvements in insulation and moisture performance on the addition of hemp to develop an enhanced bio-composite [19]. Moreover, hemp has the potential to meet environmental requirements as it can be produced and supplied in an environmental responsive manner [32].
2.4. Closed Loop Principles
Closed loop principles’ literature suggests that bio-composites can be both recovered through for soil regeneration or processing for fertilizers and biogas production at the end of their useful life, hence avoiding landfill and minimizing waste [7] [8] [9]. It is in the mainstream where strategies have to be demonstrated, resulting in a bigger contribution to a future free of Green House Gases, GHG, emissions from burning fuels or agriculture [10]. Facing this scenario, a mainstream transition towards biological materials in the building sector is encouraged as bio-composites materials are regenerative by nature having the ability to reach a closed loop life-cycle.
3. METHODOLOGY
This section outlines the methodology followed to answer the question proposed. An initial and preliminary research is carried out to determine the nature and suitability of the materials available as well as familiarization with these materials and the manually operated block-making machinery. To determine the characteristics of the object used in this study, the methodology follows Spanish standard UNE 14410 for the tests of compressive strength, density, thermal conductivity test and wet chamber test. It is intended to determine how the addition of hemp influences on earth blocks in terms of load-bearing capacity, thermal conductivity and hygric performance.
3.1. Preliminary Tests
Earth was supplied at the Research Centre on Traditional Architecture (Spanish acronym: CIAT). Two types of earth samples were considered and tested following the standard organoleptic tests [25] [27] [30] [20] and supported by experts Hormias, Bestraten and Vela advice. The samples were subjected to settlement test1 and standard field test to determine the particle size distribution, Fig. (2). A suitable loam contains a range of clay, 10% to 30%, silt, 15% to 20% and sand 50% to 75% [30] [19]. Both samples met the criteria. However, sample B had greater content of clay and a deficiency of sand whereas, sample A had an excess of sand particles. Therefore, B was selected as it would accommodate particles of hemp on the bigger fraction of the distribution. The earth mixture would be suitable and available in the UK context.
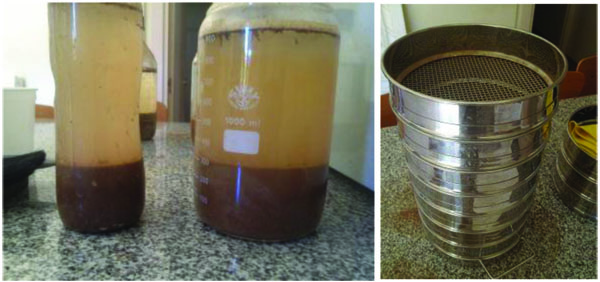
Hemp was provided by the Centre for Alternative Technology, CAT. The addition of hemp shiv was classified as ‘fine’; it has a fibre with size ranging between 1mm and 12mm. It is very likely to find hemp fibres mixed within the shiv as well as soil particles. The fibres were extracted to avoid disruption to the size distribution. A moisture meter equipment ‘TP-98D’ was used to determine hemp moisture content, which was15%. Nominal volumetric mass and bulk density of fine hemp shiv were 131 kg/m3 and 98 kg/m3, respectively. In this study, the bulk density of the shiv was defined by measuring the weight of a definite volume that is a 0.8 liter measuring cup. It resulted in 110 kg/m3
3.2. Test Block Series
Three different earth-hemp ratios were proposed as the aim of this paper was to investigate to what extent, fine hemp shiv influences earth blocks’ mechanical and thermo-hygric properties. They were set consciously aiming for an adequate ratio as per Table (1).
In total, 16 blocks were produced, 4 for each series. These entire blocks were then cut in half resulting in 32 samples. Each series of block was assigned a unique code; the system used ‘E’, ‘H’ indicates earth and hemp followed by ‘I’,’II’ and ‘III’ for the percentage of addition of fine shiv. Finally, letters from a-d were used to differentiate each individual series sample.
I | II | III | |
---|---|---|---|
Earth | 75% | 62.5% | 50% |
Hemp | 25% | 37.5% | 50% |
3.3. Block Making
Blocks were made by the author at the CIAT site in Segovia. The machinery utilised was a “BREPAK” block press shown in Fig. (3). Each series of blocks was mixed, compacted, retrieved from mould and placed to dry each at a time on earth blocks technology. Masonry principles were followed in every step of the production, as well as tools and other equipment characteristic of bricklaying [12] [25]. Blocks were left to dry 28 days following the standards. In the second round, half blocks were further dried in similar condition waiting for later testing.
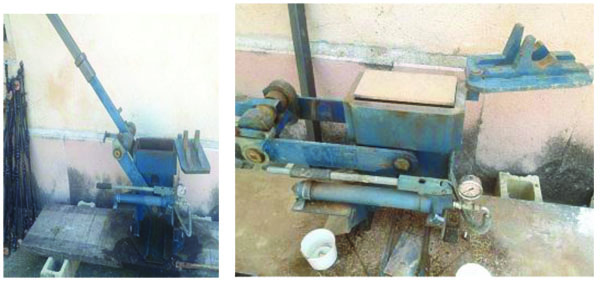
3.4. Testing
The tests were carried out in the laboratory facilities belonging to the Building Engineer School of the Polytechnic University of Madrid (Spanish acronym: ETSEM, UPM).
3.4.1. Compressive Strength
Earth Blocks Spanish standard [30] provides references for its determination procedure and calculations required to BS EN-772-1 [33] for masonry blocks. To measure the maximum compressive strength, a hydraulic press IBERTEST MIB-60Tn was utilised. For this specific strength test, it had two circular plates of 200mm diameter as shown in Fig. (4). The data logging was computerised and then it was analysed by WINTEST32 standardised testing software, including error corrections. Fig. (5) shows the software with extra data beyond the scope like the maximum load or deformation and thus young modulus. This equipment has been auto calibrated assuring precision and accuracy on the readings as per standard [34].
Complying with standard, the equipment used was a standard caliper (accuracy up to 0,1mm)with a scale (accuracy up to 0,1g and capacity of 6300g). The scales were calibrated before weighing [33].
As a custom, before strength tests, dry density of the samples was determined. To ensure an even dry state, all the samples were oven dried following the standard section 7.7.2 [33]. After this, the samples were placed between the plates as shown in Fig. (4) and broken at standard compaction pace. Then, experiments were carried out and the data was logged aided by the software. As required per standard, the results for compression strength were determined nearest to 0.1 N/mm2 accompanied by its coefficient of variation as per equation 1.

3.4.1. Conductivity Test
The test follows physics heat flow principles. Temperature data of a multilayer system subject to a steady state of heat transfer were gathered. After calculations, the conductivity was determined.
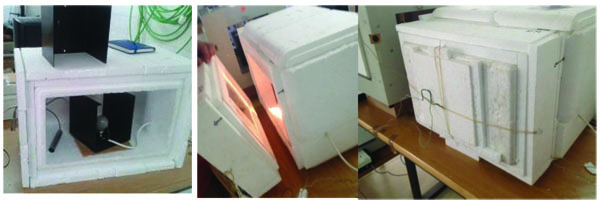
To determine the conductivity of the blocks, a specific apparatus was built as shown in Figs. (6) and 7). It was designed to fit with the standard equipment called “High insulation house” from PHYWE where samples did not fit. The equipment´s error and precision were analysed to amend if required. Due to time constraints, its accuracy was not investigated.
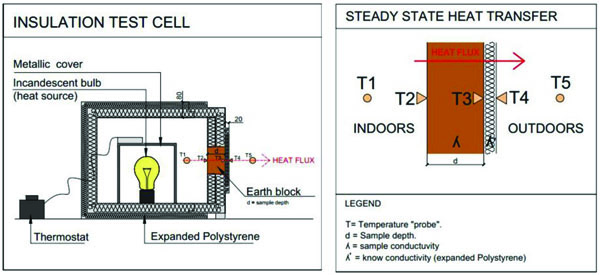
Other apparatus other than the original equipment were used. The instruments to measure the temperature, thermometers and thermocouples, were calibrated aiming at precise reading. However, their accuracy was not analysed because it was irrelevant for this experiment as it is based on a change of temperature between surfaces.
Each sample depth was first measured at the point where the thermocouples were expected to be measuring the temperature. Then it was adjusted in the “window” tailored on the opening of the test cell and thermocouples were connected to the thermometers logging the data into the software. Following this, the opening was engaged and the material with known conductivity was placed to complete the multi-layered system as shown in Fig. (7). Everything was then closed and secured avoiding leakages of heat from inside.
It is very important to assure a reasonable steady state of heat transfer through the sample and thus be able to apply the physics principles behind this test. When this steady state was reached2, the test was completed and data was logged for further calculations as per equation 2.

3.4.1. Wet Chamber Test
To determine the hygric performance, the samples were set in an enclosed environment with a saturated relative humidity3. Likewise, the samples were exposed to laboratory ambient conditions4 in the absence of ambient water5. Data of the weight of the samples were collected over time. This test is recommended for fired clay bricks and cement samples.
This method investigates the amount of moisture adsorpted and desorpted after saturation while samples reach balance with room conditions. The first step is to oven dry the samples assuring that they are completely dried. Their final dry-weight was determined as the initial dry-mass for the purpose of the test. Then, the samples were arranged in shelves inside the wet chamber. After saturation, samples were rearranged in similar shelves and exposed to lab conditions. Then, samples were oven dried for later exposition to lab conditions.
4. RESULTS
In this section, the author presents the results of the experiments described in this paper. Following, the compressive strength, the results are shown for the 28 days and 150 days periods. Lastly, thermal conductivity mean values and wet chamber test results are given. Results follow a colour scheme as a visual aid. The colours for this purpose have been chosen with regar to their resemblance to the materials involved. ‘CEHB control’, E in brown and those with the addition of hemp, CEHB6 in a range of green according to their hemp content – light green = low content; deep green = high content - easy identification when necessary, especially in correlations.
4.1. Physical Characteristics
Table (2) shows the results of physical characteristics of the samples including material compounds, mean dry density and moisture content. Mix composition is shown by percentage of volume of each material. Fig. (8) reveals the relationship between dry density and hemp content. The average dry density and moisture content7 for each series are shown together. Mean density values showed a high confidence. 2SD were observed to be less than 6% in the worst case scenario
Series Code | Earth (% of total Volume) | Hemp (% of total Volume) | Dry Density | Moisture Content % | |||
---|---|---|---|---|---|---|---|
Lab cond. | WC cond. | Saturated | |||||
µ | µ | µ | µ | ||||
E | 100% | 0% | 1745 | 0.32% | 1.62% | 5.91% | |
E-HI | 75% | 25% | 1404 | 033% | 1.82% | 6.16% | |
E-HII | 63% | 38% | 1162 | 0.38% | 2.01% | 6.32% | |
E-HIII | 50% | 50% | 962 | 0.44% | 2.38% | 6.85% |
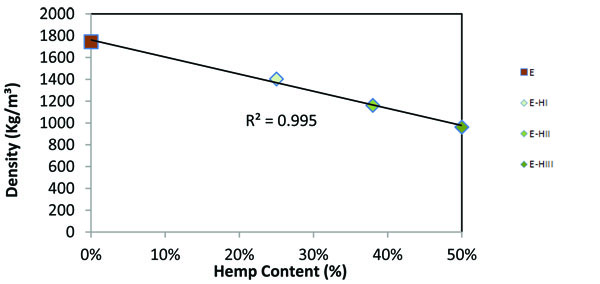
Fig. (8) shows the linear correlation between dry density and hemp content in a scatter graph for CEHB. The dry density is highly correlated to the quantity of hemp.
4.2. Compressive Strength Test
To calculate the maximum compressive strength, the BSI standard [33] has been followed. As required in the standard, the coefficient of variation is, in this section, used as an indicator of the dispersion of the mean data obtained by breaking the halved blocks samples in the press testing machine. Moreover, shape factor 0.96 was considered if the normalised (fb) value was intended.
4.2.1. At 28 Days
Although the samples broke due to the stress during the test, the author observed that the samples remained fresh. It may be the cause for discrepancies observed in the results. Fig. (9) plots the mean values of the results of the test in the form of a bar chart. The author found the mean value for the control series abnormally lower than the E-HI. The latter reached 3.1 N/mm2 while E was only 2.5 N/mm2.
The series with lower contents of hemp, E-HII and E-HIII (green), revealed similar compressive strength, 2.2 N/mm2 and 2 N/mm2 respectively. The author found the results unexpected. Once broken, the samples presented an excess of moisture. It is very likely that a more thorough dry out process would have provided results closer to the expected ones.
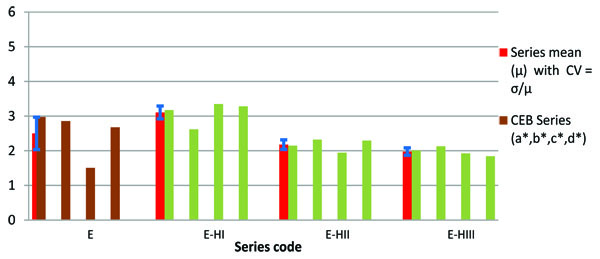
Fig. (10) reveals a weak correlation between the density and compressive strength on the test at 28 days. Such correlation encouraged the author to consider compressive strength at 28 days test results really poor to further discussion.
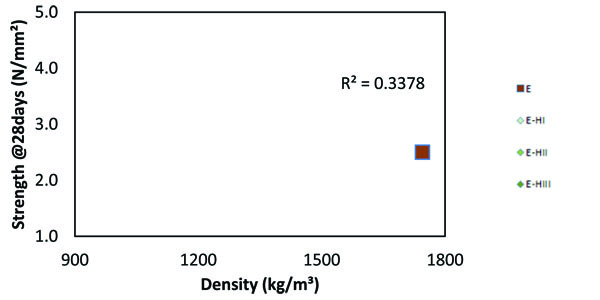
4.2.2. At 150 Days
The changes were proved to be in favour of more expected results correcting the anomalies of at 28 days strength test results. Fig. (11) plots the results for the second strength test; these were as expected in the articulated hypothesis. Control blocks reached larger mean strength values than any other series, being 5.3 N/mm2. And the rest of the series presented greater values than at 28 days. Again, the E-HII and E-HIII series showed similar results between them two – 2.6N/mm2 for E-HII and 2.2N/mm2 for E-HIII. The coefficient of variation indicated that the mean values for these series had a high confidence at 2SD.
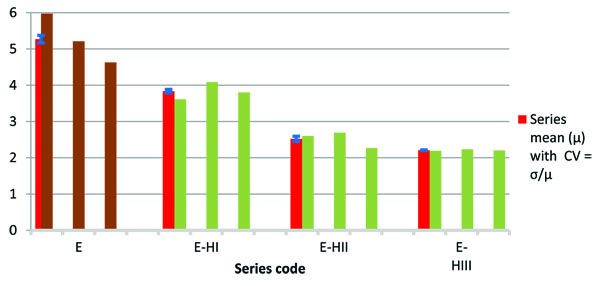
Fig. (12) shows the correlation of the mean strength values at 150 days with the mean dry density. A R2 value close to 1 corroborates the predictability of the results for the blocks commented in the previous section.
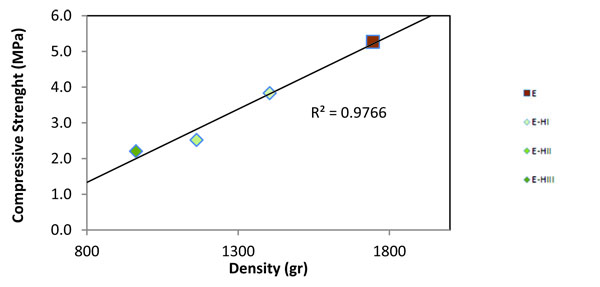
4.3. Thermal Conductivity Test
This section reveals the results obtained in the experiment carried out with a modified equipment to fit the blocks. The test reached a steady state of heat transfer with an average temperature of 60°C inside and 25°C outside. The average relative humidity outside the box was 45%. The error remained within the standard range of 5% in all measures. Fig. (13) shows a decrease similar to that of the dry densities in (Table 2 Fig. 13) also shows the strong correlation between conductivity and density. This demonstrates the correlation between density and conductivity.
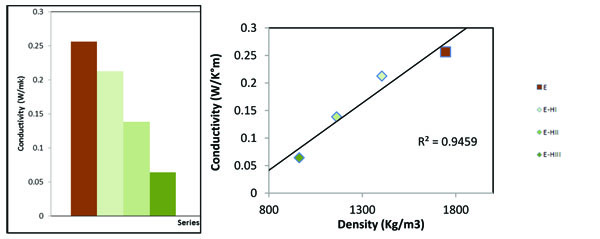
4.4. Wet Chamber Test
Table (3) shows the average moisture content expressed in percentages for each series in four different scenarios. In this test, the moisture content is determined by comparison of the dry weight with the weight of the samples for each scenario8. From left to right, moisture content of the samples at lab conditions9; wet chamber, WC; conditions after 24 hours; and until moisture saturation10; lastly mean values for lab conditions after saturation. The results showed a relatively high confidence.
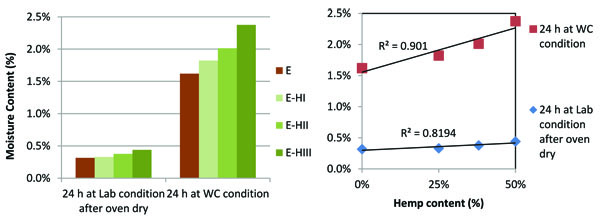
Series Code | 24h at Lab conditions after | 24h at WC condition | 25 days at WC condition | 24h at Lab condition after 25 | ||||
---|---|---|---|---|---|---|---|---|
µ | 2σ | µ | 2σ | µ | 2σ | µ | 2σ | |
E | 0.3% | 0.0% | 1.6% | 0.3% | 5.9% | 0.3% | 2% | 0.3% |
E-HI | 0.3% | 0.0% | 1.8% | 0.2% | 6.2% | 0.8% | 2% | 0.1% |
E-HII | 0.4% | 0.0% | 2.0% | 0.2% | 6.3% | 0.2% | 3% | 0.3% |
E-HIII | 0.4% | 0.0% | 2.4% | 0.1% | 6.8% | 0.5% | 3% | 0.1% |
4.4.1. Absorption at 24 Hours
Fig. (14) illustrates the moisture content for the scenarios lab conditions after oven dry and WC conditions. As expected, the samples with hemp addition absorbed more moisture, but it did not represent a big change between each other. The series E-HIII at WC conditions presented relatively greater moisture content than the rest. Fig. (14), right, shows a strong correlation between the capacity to store moisture and hemp content for the scenarios described. The linear trend, made clearer what was not perceptible in the previous section.
4.4.2. Saturation at 25 Days
Fig. (15) shows an absorption pattern that is similar to other scenarios. The saturated moisture content was observed to be very likely the maximum possible absorption for the samples as the difference between the last three readings was less than 0.01%.
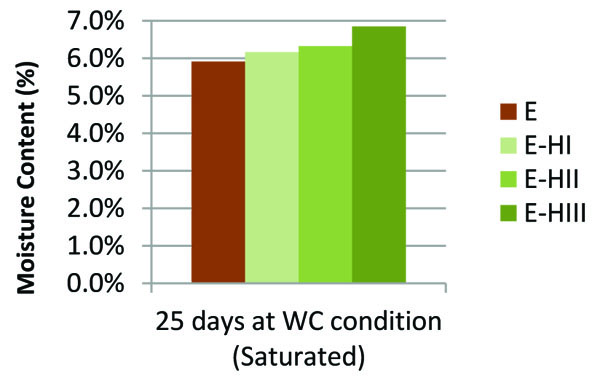
4.4.3. Desorption at 24 Hours
For clarity, this set of data was presented separately plotting the negative values. Fig. (16) shows the amount of moisture lost as a consequence of balance with the environment at lab conditions after saturation at 25 days under WC conditions. Results again follow the similar pattern between the series.
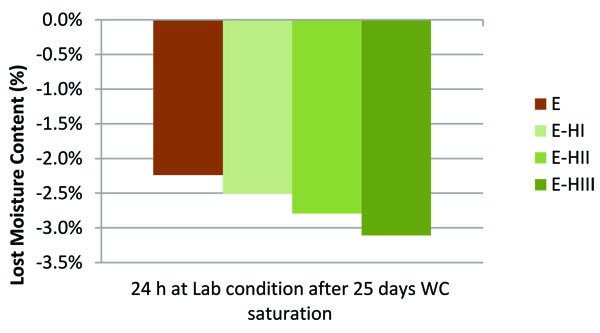
4.4.4. Moisture and Hemp Content: Saturation and Desorption
Fig. (17) shows the linear correlation of moisture content with hemp content for saturation at WC conditions and desorption 11 at 24 hours. It represents a strong linear correlation of both the conditions (R2 = 0.86 for saturation values and R2 = 0.95 for desorption) with hemp content.
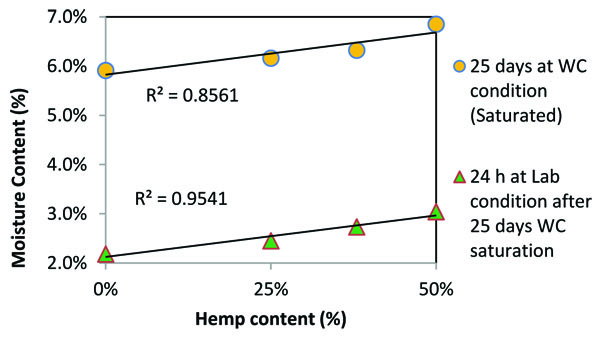
5. DISCUSSION OF RESULTS
In this section, the author discusses the results and their implications in-depth with regard to the effect that the addition of fine hemp shiv had on physical and mechanical properties; the thermal and hygroscopic performance of the earth blocks. Following this, a comparative analysis of the obtained results with the existing research was conducted where similar materials were involved since there is no published data on hemp and earth block technology and mainstream values available for the UK. The addition of fine hemp shiv produced, to a greater or lesser extent, an effect on all the block characteristics and standard parameters.
5.1. Density
Density is a feature of earth blocks which influences the structural capacity hence block’s compressive strength. The results show a strong influence on the samples’ density on the addition of fine hemp shiv. After calculation of the correlation coefficient squared (R2value = 0.995), it can be said with determination that if you add fine hemp shiv to earth blocks, density decreases directly related to the amount of fine hemp shiv.
The particle size distribution contained a suitable percentage of fine and clay particles. In the samples subject to study, there was 25% clay. Although material characterization is out of scope of this paper; it is worth mentioning that as the content of hemp increased, hence the percentage of earth decreased, and the overall percentage of clay reduced significantly - i.e. in E-HIII (50%hemp-50%earth), clay particles dropped till 12.5% or less -. Therefore, as clay particles reached close to the 10% minimum established in the standard [30], the cohesion of the E-HIII series blocks was greatly affected, with a small difference between the density values for series E-HII and E-HIII.
5.2. Compressive Strength
It is evident in the literature about earth blocks that density is the determinant of the final maximum compressive strength [35] [36]. However, values shown in Table (4) do not reveal a strong correlation as the author expected. This refrained the author to make a confident statement about the extent to which the addition of fine shiv influences the earth block´s compressive strength.
On the other hand, the results of this test show a significant mechanical performance at 150 days. It is very likely that the particle size distribution resulted in good results, as observed in the density. So the selection of the grains within this distribution has great significance in achieving better mechanical performance. Compressive strength is strongly related to density and particle size distribution. Therefore, it is this distribution of the particles which confers greater mechanical properties, regardless of the nature of the particle and strongly dependent on its size. It is worth mentioning the E-HI series. This series, with a 25% of hemp content, reveals great results. It surpasses the control block results at 28 days. It is probably because the 25% fine hemp shiv fits better with the particle size distribution of the earth used to manufacture the blocks.
Series Code | Fmax (N/mm2) @28 | Fmax (N/mm2) @150 | ||
---|---|---|---|---|
µ | 2σ | µ | 2σ | |
E | 2.50 | 1.17 | 5.27 | 1.10 |
E-HI | 3.11 | 0.57 | 3.83 | 0.39 |
E-HII | 2.18 | 0.30 | 2.52 | 0.36 |
E-HIII | 1.98 | 0.21 | 2.21 | 0.03 |
5.3. Thermal Conductivity
Thermal Conductivity of masonry products is a key parameter to determine energy efficiency of the building. As Table (5) shows, it is clear that the conductivity of the blocks decreases as long as hemp content increases. It decreased up to 0.065 W/K°m ±4% in the blocks with 50% of hemp.
These values have a great level of confidence. However, the sample size was not big enough to eliminate the variance and confirm these results as the actual influence of fine hemp shiv. However, it has been demonstrated and with a high confidence that the addition of fine shiv has influenced the thermal conductivity to a great extent.
Series Code | Conductivity λ (W/mk) | |
---|---|---|
Mean | 2σ | |
E | 0.2567 | 0.0335 |
E-HI | 0.2127 | 0.0307 |
E-HII | 0.1387 | 0.0111 |
E-HIII | 0.0643 | 0.0034 |
5.4. Moisture Adsorption
Although the mean values for moisture content showed an increased percentage on samples with hemp content than the control ones, different contents of hemp did not influence the moisture content. As hemp content increased, the capacity to store water within the mass body of the samples increased as well at a constant rate. By comparison of the two conditions, it became visible that at WC conditions under saturation, the absorption of moisture was observed to be greater as hemp content increased. Although the step between the series seemed proportional, it was the sample with 50% of hemp content that showed a greater difference. Every moisture set followed a similar pattern. Series E-HIII showed greater moisture absorption in all the scenarios.
5.5. Comparative Analysis with Mainstream Values
Table (6) shows public values of commercially available earth blocks Bioterre, Grupo La Plana (Spain); Ecoterre™, Ibstock (UK) [37]; Cannabric® (Spain) [38] and the UNESCO institution Auroville Earth Institute [24] used for emergencies after natural disasters against building standard and tests’ results.
The density of the commercial blocks is higher than the results revealed in this paper. Only Cannabric® hemp blocks’ density was the same as that of E-HII. However, the Canabric® block is made of hemp and lime.
Products in Mainstream | ||||||
---|---|---|---|---|---|---|
Company | Product | Size (mm) | Density (Kg/m3) | Compressive Strenght >12 | Conductivity (λ) | |
Grup. PLANA SL (Spain) | BTC BIOTERRE CSEB | 290x145x95 | 7.0 N/mm2 | 0.415 W/mKº 0 ºC | ||
0.546 W/mKº 35 ºC | ||||||
Ibstock (UK) (Ecoterre™ Earth Bricks) | Earth Brick Standard | 220x105x67 | 1940 | 3.8 N/mm2 | ||
Code EB3590 | ||||||
Earth Brick Large | 220x105x133 | 1940 | 2.9 N/mm2 | |||
Code EC3590 | ||||||
Cannabric® (Spain) | 300x145x105 | 1171 | 5.7 MPa | 0.1875 W/mK | ||
Auroville | Hollow interlocking block 245 | 5.85 | ||||
CSEB class A | - | 1900-2200 | 5-7 Mpa | 4.6 - 0.81 | ||
CSEB class B | - | 1700 -2000 | 2-5 Mpa | 0.81 -0.93 | ||
AENOR CEB Standard | ||||||
Compressive Strenght>13 | BTC 1 | 1.3 MPa | ||||
BTC 3 | 3 MPa | |||||
BTC 5 | 5 Mpa | |||||
Earth Blocks with Hemp shiv | ||||||
Compressed Earth-Hemp Blocks | E | 290x140x100 | 1745 | 5.27 MPa | 0.257 | |
E-HI | 290x140x100 | 1404 | 3.83 MPa | 0.213 | ||
E-HII | 290x140x100 | 1162 | 2.52 MPa | 0.139 | ||
E-HIII | 290x140x100 | 962 | 2.21 MPa | 0.064 |
The control and E-HI series reached similar load-bearing capacity at 150 days than commercial values. However, these values mostly refer to stabilised blocks with cement or lime. The results of the compressive strength revealed an acceptable mechanical performance at 150 days against the standard. Even those with a high content of hemp can be used in construction according to the Spanish standard.
Thermal conductivity values shown in the paper were half than most of the commercial values, when compared. Again Cannabric® blocks are a bit lower than the control blocks and E-HI. However, when the addition of hemp increased to more than 25% the values were observed to be considerably smaller.
Commercially available earth blocks and Auroville public values against building standard and mean values of tests’ results
Conductivity of E-HIII is close to high insulation mainstream materials like the polystyrene expanded foam used in the construction of the test cell used to measure thermal performance (0.037 W/K°m ±5%). Although thermal conductivity is a very relevant value for building materials, masonry units are used in conjunction with other materials like mortars and plasters. This combination of different materials, when building brick walls, affects to a large degree, the overall values of thermal conductivity required by regulations. Therefore, the results obtained for the enhanced bio-composite are comparable with other masonry products but these values have to be investigated combining mortar at least to be confident with regard to meet regulations and thus adoption by the mainstream UK built environment.
5.4. Comparative Analysis with Existing Research
The product Cannabric® seems the most suitable to further compare performance and composition for research. However, there is no published research besides on its features as a commercially available building product, discussed in the previous section. Besides Cannabric®, the author did not find published information regarding the addition of hemp or similar bio-composite like straw to compressed earth blocks. All the information found were from the vernacular typology ‘adobe’ and it cannot be compared due to fundamental differences such as a higher water and clay content.
The literature on the addition of hemp to pure clay slip, has been reviewed in the beginning of the paper. However, it is again not directly comparable as the clay content in earth blocks is very unlikely to surpass 25% within the particle size distribution. Literature was also reviewed for particle size distribution and its high influence on the mechanical properties of the earth blocks, but it is again not comparable as these investigations focused on different additions, which is beyond the scope of this paper [19]. In terms of enhanced bio-composites research, thermal conductivity of E-HIII is an exceptional value if compared to the data of a Chinese research on the development of insulating clay bricks using raw material extracted from urban river sediments - 0.35 ̴0.48 W/K°m - [39].
CONCLUSION
The aim of this paper was to study the influence that fine hemp shiv has on thermal conductivity, moisture performance and compressive strength of earth blocks. Different proportions of fine hemp shiv have been used to determine the different grades of influence. Within the scope, it also provides a comparative analysis of the results with the public values of similar building products and construction standards. The aim was to determine to what extent hemp content influences earth blocks characteristics and if the bio-composite developed, with the addition of fine hemp shiv has the potential to reach mainstream UK built environment and complies with the construction standards. Ultimately, the purpose of this investigation was to work on tackling the problem of further decarbonisation of the UK built environment by making improvements in building technologies with a closed loop approach. Based on the findings revealed in this paper, the following conclusions can be drawn:
- When fine hemp shiv has been mixed with earth to produce Compressed Earth Blocks, a reduction in the density of those blocks was observed. This decrease has been determined to have a strong linear correlation with the increasing quantity of fine hemp shiv addition. Although the load-bearing capacity of earth blocks is very highly correlated with their density, the series with 25% of hemp addition achieved compressive strength enough to meet the standards for structural purposes.
- Thermal conductivity of earth blocks has been largely reduced after the addition of fine hemp shiv. It has shown remarkable results of the series with 50% of hemp addition. This series has achieved results better than other commercially available products and the value is close to high insulation materials.
- The capacity to store water within the blocks analysed as moisture content, has been modestly increased after the addition of hemp. However, CEBs have been influenced by the addition of fine hemp shiv and that these variables have a strong linear correlation between them.
- Bio-composite building products can be developed that are suitable for the mainstream in the UK built environment while they are low embodied carbon with the potential of a closed loop life cycle. Construction industry would be better suited to meet the goals of UK’s de-carbonisation plan.
NOTES
1 Settlement tests were performed mixing water and soil samples inside a bottle in the following ratio, by volume: 2parts of water, 1 part of soil and 1 part of air. The bottle was vigorously shaken and then allowed to stand so that the various components, gravel, sands, silt and clays could sediment according to their weigh.
2 Settlement tests were performed mixing water and soil samples inside a bottle in the following ratio, by volume: 2parts of water, 1 part of soil and 1 part of air. The bottle was vigorously shaken and then allowed to stand so that the various components, gravel, sands, silt and clays could sediment according to their weigh.
3 Wet chamber conditions were monitored over a 25 days period whilst samples were exposed to them, with an average temperature of 24.8°C and an average relative humidity of 91.
4 Lab conditions were monitored over a 21 days period whilst samples were exposed to them, with an average temperature of 22.4°C and an average relative humidity of 40.5%.
5 Oven dry at 70°C during 24 hours or until constant weight as standard for Compressive Strength test [33].
6 Compressed Earth Hemp Blocks: Series E plus addition of hemp, HI, HII and HIII.
7 The results with regard to moisture content are commented later. However, these are illustrated in the table to compare them directly with density values.
8 Equation to work out the moisture content for all scenarios: ‘Scenario’ weight – oven dry weight = ‘scenario’ weight of moisture within the sample, ‘scenario’ weight of water/oven dry weight = % ‘scenario’ moisture content.
9 Lab conditions were monitored over a 21 days period whilst samples were exposed to them, with an average temperature of 22.4°C and an average relative humidity of 40.5%.
10 Oven dry at 70°C during 24 hours or until constant weight as standard for Compressive Strength test [33].
11 As a scatter graphs give the same linear correlation for negative or positive values, for the desorption one the results with positives values are presented. Therefore, to ease the presentation, this time these two scenarios are plotted together.
12 1N/mm2 = 1Mpa
13 AENOR Spanish standard for CEB [30]
CONSENT FOR PUBLICATION
Not applicable.
CONFLICT OF INTEREST
The author declares no conflict of interest, financial or otherwise.
ACKNOWLEDGEMENTS
The work presented in this paper was made possible due to the contribution of the following institutions and professionals
- Research Centre on Traditional Architecture (in Spanish CIAT, Centro de Investigación de Arquitectura Tradicional) while running a course on earth building techniques. The available materials, tools and machinery were utilized as well as the advice of those building professionals and earth experts . Special thanks to Antonio Vela and Jaime de Hoz for their support and work.
- The tests were carried out in the laboratory facilities belonging to the Building Engineer School of the Polytechnic University of Madrid (Spanish acronym: ETSEM, UPM). Special thanks to Mariano Gonzalez Cortina, Santiago Villa and Emilia for their support and experimental knowledge.
- Ranyl Rhydwen, the supervisor of the thesis, is acknowledged for his support and encouragement.