All published articles of this journal are available on ScienceDirect.
Characterization of Hot Bituminous-Asphalt Mixtures with Recycled Polyurethane Foam
Abstract
Introduction:
The use of polymer wastes in pavement as road is an increasing trend in the road construction sector. Those new pavements reduce the amount of solid waste disposed into landfills and provide more sustainable construction due to the use of in-situ materials. Polyurethane foam waste is a thermostable polymer being used in the form of a grey-coloured foam, a by-product of the automobile industry.
Aim:
The focus of this work centers on the exploitation of polyurethane foam waste in full or partial substitution of the fines and the mineral powder that form the bituminous mixtures to produce a sustainable alternative for bituminous asphalt used in pavement construction.
Methods:
A series of specimens were manufactured and tested for the Marshall test, with different percentages of polyurethane foam waste aggregates (50% and 100%), calculating their apparent densities.
Results:
The results show acceptable compatibility between the elements of bituminous concrete and the polyurethane waste, producing a reduction in both the apparent density and Marshall stability, as well as an increase in volume and an increase in deformation with higher volumes of waste in the mixture.
1. INTRODUCTION
Road transport is one of the most widely used means of mobility for people and goods. The construction and conservation of this type of infrastructure therefore involve very significant economic costs for various public administrations. Hot bituminous mixtures require large amount of aggregates and asphalt binders for road surfacing and for other sorts of bituminous surface courses. Hence, investigation into the use of recycled materials for the manufacture of bituminous surface courses is of great interest from an environmental point of view [1, 2].
Among the wide variety of waste products that may be used in the preparation of sustainable bituminous mixtures, the use of polymers as recycled raw materials is of great interest for the improvement of these types of waste products and their environmental management. There are numerous publications in which Polyethylene (PE) and Ethylene vinyl acetate (EVA) thermoplastic polymers from waste products are added to bitumens for their modification [3], or that replace the aggregates with other recycled waste products in bituminous mixtures, such as waste tire rubber which modified bitumen demonstrating the beneficial effect on fatigue life of the incorporation of (RCA) [4, 5].
Other types of wastes were used in hot mixed materials such as glass [6], crushed brick [7], steel slags in warm-modified asphalt concrete assuring equal or even enhanced performance than the corresponding traditional hot mixed materials, demonstrating promising field applicability [8, 9] and rice husk ash (RHA), as a waste byproduct of rice milling, in bituminous roadways providing valuable advantages such as reduction of environmental degradation, lowering construction costs and saving natural resources [10]. Previous literature on the use of recycled polyurethane foam reports good results for the use of polyurethane as a substitute for aggregates in different agglomerates, such as mortars [11] and lightweight plasters [12], and even other types of thermostable polymers used as lightweight aggregates [13].
This research work has analyzed the behaviour of bitumen-polyurethane mixtures [14], but based on the manufacture of the polymer in situ, rather than the use of the material as a pre-prepared waste product. In this work, asphaltic bituminous mixtures were prepared with the full or partial substitution of filler by polyurethane foam waste and their physical and mechanical properties were studied.
The research work not only covers the use of polyurethane waste to reduce its accumulation in landfill sites, and to reduce the consumption of natural resources, facts which by themselves are of great relevance, but it also attempts to find which of them imply improvements in the properties and applications of bitumen applications.
2. RAW MATERIALS
A thermostable polyurethane waste was used in the form of a grey-coloured foam, a by-product of the automobile industry. The waste is collected from the factory in the form of rigid polyurethane plates and then crushed, as may be seen in Fig. (1). The chemical composition was determined by CHNS elemental analysis with a LECO CHNS-932 analyzer and with X-ray diffraction (Table 1). The apparent density of the polyurethane foam, after being shredded to sizes of between 0 and 3 mm, weighed 68 kg/m3 and the polymer was examined with Scanning Electronic Microscopy (Fig. 2).
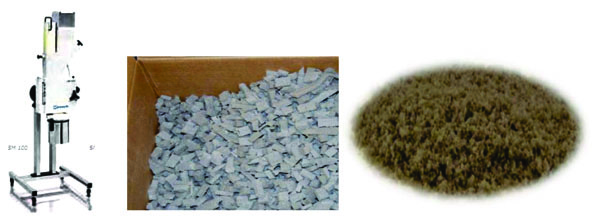
Element | C | O | N | H | Ca | Others |
---|---|---|---|---|---|---|
PU-Waste | 65.5 | 19.0 | 7.2 | 6.2 | 1.0 | 1.1 |
The reference bitumen used in this work was a standard 50/70 commercial type of asphalt bitumen. The bitumen was characterized by the degree of penetration at 25 ºC with a value of 66 in accordance with standard EN 1426 [15] and the softening point temperature, with the ring and ball method with a value of 49.8 according EN 1427 [16].
Siliceous aggregates were used in the study, with a specific weight of 2.65 g/cm3, an abrasion ratio of 20.7% and a Polished Stone Ratio of 52.
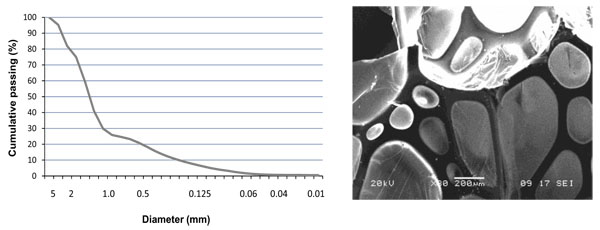
3. EXPERIMENTAL
3.1. Manufacture and Characterization of Hot Bituminous Mixtures
The type of hot bituminous mixture chosen for the preparation of the specimens was an AC 16 surf D for resurfacing. The hot bituminous mixtures corresponding to series were prepared with an specific aggregate granulometry (Fig. 3) that met the granulometric grading required for mixture AC16D, as established in table 542.9 of the PG-3 [Set of general technical specifications for road works and bridges]. Four series of specimens were prepared for this study:
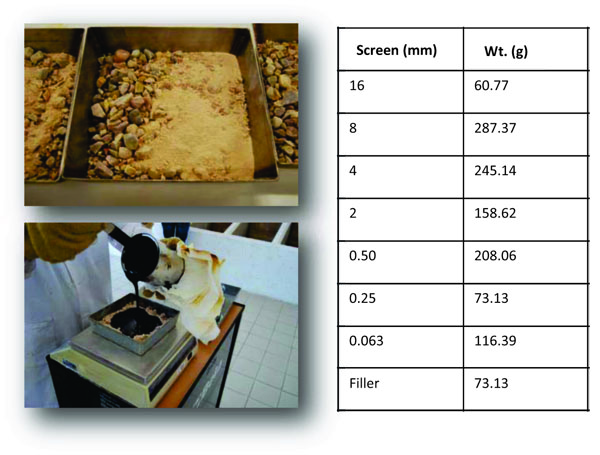
Series A: Reference mixture without polyurethane foam.
Series B: Mixture with a substitution of 50% by weight of filler for polyurethane waste incorporated cold in the hot mixture.
Series C: Mixture with a substitution of 100% by weight of filler for polyurethane waste incorporated cold in the hot mixture.
Series C’: Mixture with a substitution of 100% by weight of filler for polyurethane waste soaked for 2 hours before.
In all cases, the fines and the bitumen were previously heated over 10 hours at 160ºC. The specimens were manufactured at 160ºC and then compacted.
A series of similar specimens were manufactured and tested for the Marshall test, with different percentages of raw materials, calculating their relative densities and cavity content. On the basis of these results, the optimum content of the binder may be determined for a mixture of aggregates at a specific granulometry.
3.2. Apparent Density
The dry procedure specified in standard EN 12697-6 [17] was used, in order to determine the apparent density of each specimen.
3.3. Marshall Test
This test is used in the preparation of dense, semi-dense, and thick bituminous mixtures. The purpose of the Marshall test is to determine the optimum content of bitumen for a specific combination of aggregates. It is a mechanical test that consists of breaking previously prepared cylindrical test specimens, heated to a temperature of 60ºC, through the application of a vertical load by means of a perimetral clamp, at a constant speed of deformation of 50.8 mm/min to determine their stability and deformation. Stability is measured in terms of load (kp), while deformability is the reduction in diameter that the specimen undergoes between the start of loading and the breaking point, expressed in mm (ASTM D 1559-82) [18]. This method establishes optimum cavity densities and contents that have to be met for the construction of the surface.
4. RESULTS AND DISCUSSION OF HOT BITUMINOSUS MIXTURES
The properties that are obtained with the addition of polymers in bituminous materials depend on the nature of these organic materials and their chemical structures. In general, the long chains of these compounds give the mixtures greater elasticity, due to the presence of very long polymeric chains, which improve adherence, due to the short chains that exist in those same polymers. At the same time, a physical cross linking of the polymer chains occurs between the different phases that reinforce the cohesion of the mixtures, and which depend on the molecular weight and the viscosity of the added polymer.
4.1. Apparent Density
The first result was the physical appearance that the specimens presented. It was also observed that all the mixtures that incorporated polyurethane foams in their dosages presented an appreciable increase in volume, as represented in Fig. (4), and a slight wetting of the fines; particularly, in those mixtures in which the polymers had neither been heated nor previously soaked and in the compaction of the samples. In concrete, the increase in height of this type of specimen was 4.2 mm. A possible explanation of this effect is that if polymers are incorporated cold in the mixture, there is insufficient time to produce the interaction between the bitumen and polymer, making it acts as an elastic fine. Some authors consider that in these first stages of reaction, the polymer absorbs volatile particles of the bitumen resulting in its increased volume [19].
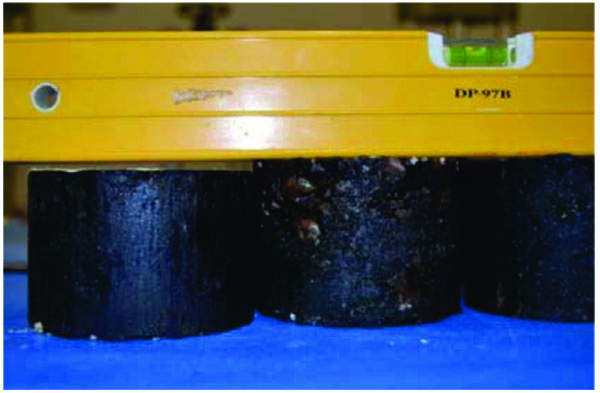
The density results (Fig. 5) indicate that the mixtures that contain polyurethane foam undergo a considerable drop in their density as opposed to those that do not incorporate this waste (Series A), the effect being greater in the mixtures that contain larger volumes of foam (Series C with 100% substitution of filler).
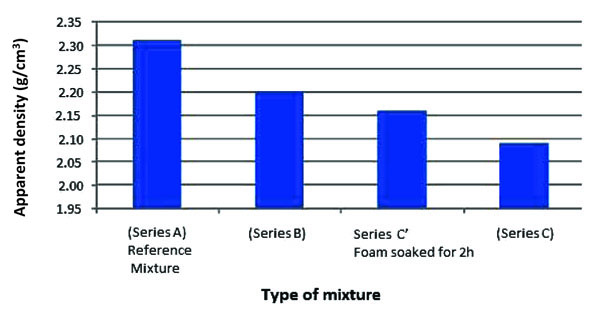
4.2. Stability and Marshall Deformation
As happens with the densities, the Marshall stabilities vary linearly with the increased amounts of polyurethane foam, producing a drop in those values, as shown in Fig. (6). As previously analyzed, this fact may be because the polymer has not interacted as a binder in the mixture. The polymer has to be previously heated to prevent this effect, so that it reacts with the bitumen and by doing so acquires a greater reinforcement effect. Part of his fact is observed in the Series C’ mixture in which the polyurethane foams are previously heated for two hours. In the graph, we may see that the drop in stability is lower than in the mixtures in which the foams are incorporated in a cold state. In previous studies, it was confirmed that the capacity of the binder that a polymer can give to a bituminous mixture is because the bitumen and polymer react to produce a homogenous mass that will contribute greater binding power to the mixture [20].
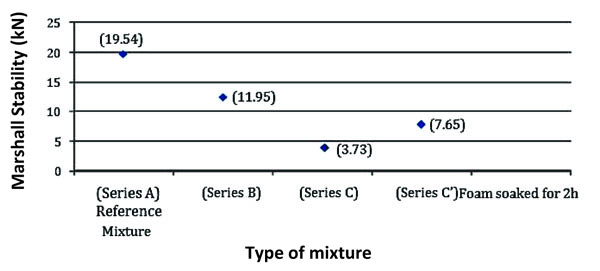
With reference to Marshall Deformation, it may be seen in Table 2 that high values in the content of polymers produce an increase in deformation. In the Series C’ mixtures, in which 100% filler was substituted for foam, the deformation was lower. It was also observed that previous soaking of the foam reduced deformation, so that once again it was confirmed that the polymer should not be incorporated in the mixture in a cold state. The highest deformations that were reached therefore reveal that the materials were not sufficiently well bound together. Moreover, an increase in the volume of cavities in the mixture was determined as well as a considerable reduction in the unfilled cavities.
A good workability of the mixture is confirmed with the percentage of the added polymer, such that it may be assumed that on-site laying and compaction will be acceptable, partly because of the lubricating action of the polymer. The possibility remains of studying the use of additives that could improve the workability of the mixture, for percentages of foam waste above those in this investigation.
Series | Plastic Deformation (mm) | Marshall ratio (Mean Average) |
---|---|---|
A | 3.59 | 5.44 |
B | 3.72 | 3.21 |
C | 4.55 | 0.82 |
C’ | 3.28 | 2.33 |
CONCLUSION
In view of the changes in volume, it may be concluded that soaking of the mixture at mixing temperature over a set period of time, before compaction might improve the resulting mixtures preventing increases of volume. This information underlines our understanding that the period of soaking prior to extension and compaction is fundamental and critical, as when performed incorrectly, not only would it provoke modification of the bitumen, but it would yield a product with a worse performance than a conventional binder.
The polymers to be incorporated in the mixture must be proportionate to the amount of bitumen to be added, to prevent processes of separation and disaggregation.
The possibility has been confirmed to reducing the density of bituminous mixtures through the incorporation of polyurethane foam wastes.
Likewise, the use of polymers could increase the resistance of the mixture to ageing, maintaining the bituminous asphalt in a better state, as the possible cavities are occupied by the polymer.
Further work will focus on the potential applications of these mixtures, with the aim of determining their durability through other forms of testing, in order to obtain materials with practical applications for roadway construction.
ETHICS APPROVAL AND CONSENT TO PARTICIPATE
Not applicable.
CONSENT FOR PUBLICATION
Not applicable.
CONFLICT OF INTEREST
The authors declare no conflict of interest, financial or otherwise.
ACKNOWLEDGEMENTS
Declared none.