All published articles of this journal are available on ScienceDirect.
Experimental Study on Properties of Steel-plastic Geogrids and their Application in Supporting Engineering
Abstract
Steel-plastic geogrid greatly improves the stability of surrounding rock in the supporting project due to the qualities, such as high strength, high toughness and less creep deformation. Through the geogrid mechanical properties analysis, tensile strength, deformation and creep test and field experiment and so on, we researched and analyzed steel-plastic geogrids’ characteristics and supporting effect, and concluded the influencing factors of steel-plastic geogrids’ characteristics, load-time curve and the steel-plastic geogrids’ variation under different temperature. We explained steel-plastic geogrids’ supporting effect through specific examples of projects. The results of the studies are listed as follows: (1) Steel-plastic geogrid has good resistance to deformation and node failure of roadway surrounding rock deformation, which has good tensile property, creep property and deflection performance; (2) It is feasible to support the surrounding rock by forming a whole combined joint support with steel- plastic geogrid and high-strength prestressed anchor rod.
1. INTRODUCTION
With the advantages of high strength, good durability, convenient construction, geogrid has been widely used in highway, railway, mine and other fields. When it is applied as supporting structure, geogrid mainly through its tensile strength to bear the load from the soil plays a role of the project. But as a kind of new material, research on the mechanical properties is still at the beginning stage. Similarly, steel grating in roadway support applied research is still blank.
A lot of people have studied the application of metal mesh as the anchor net in support. But almost no one is involved in the application of the steel plastic geogrid as anchor net support. In the 1960s, L.V. Rabcewic [1] summarized and put forward a new construction method for Austria tunnel with many years' experiences of tunnel engineering construction in Austria. The construction method of flexible support and active support method, the soft rock roadway has a certain guiding significance, has been widely used in the design and construction of underground engineering Based on the classical elastic-plastic theory of surrounding rock, many scholars have carried out a lot of research and improvement in the domestic and international [2, 3].
On the base of the experimental research, Tannant. D. D. [4, 5] studied the welding wire mesh reinforcement, and found that the net in the anti-deformation ability depended on the plate shape and plate relative to the nets in the direction, and the mesh number of the load transfer located in the pallet. Since the 90’s in twentieth century, the development of the domestic and international has been gradually developed with the support of the cable and the anchor net belt [6-9]. By using bolt support on the initial pressure of the surrounding rock to support the foundation, strength and stiffness of the two supporting measures increase to jointly support the surrounding rock stress, this by improving the supporting strength to maintain the long-term stability of the tunnel. Supporting measures were taken to the anchor, grouting and sealing metal bracket or concrete lining structure to form a different form of joint support [10-14].
In view of the metal mesh selection and network method in coal mine bolt mesh shotcrete support, Lin Jian and Sun Zhiyong [15] used laboratory test method to study the stress state, deformation condition and supporting function of the common metal mesh of the bolt support. According to the bolt fracture, appeared in Dongtan coal mine roof net local roadway deformation serious tear strip even collapse, Deng Xiaolin [16] optimizes the anchor net support technology in deep well. Therefore, combined with a variety of theories and methods, research on mechanical properties of steel grating and the supporting effect is very necessary.
From the above results, we know that there are almost no researches of the steel-plastic geogrids as the anchor of the supporting mechanism and method. Therefore, this paper introduced tests and analysis of steel-plastic geogrids’ tensile strength, deflection performance and creep performance. Steel-plastic geogrid was applied successfully in roadway, and it was verified that the steel-plastic geogrids could replace metal mesh to support in roadway.
2. OVERVIEW OF PLASTIC GEOGRID
2.1. Concept and Scope of Application
Based on plastic geogrid, the steel-plastic geogrid is made of high strength steel wires processed specially and PE or PP and other additives. Steel wires are wrapped by PE or PP by special fusing, then these form compound and high strength tensile bands with rough surface, and the followed procedure is that longitudinal and transverse bands experience a knitting procedure into a system at certain distance. A special welding technology is used to bond the junction points into the steel-plastic geogrid. Changing the diameters of steel wires and quantity improves the tensile strength of geogrid. The steel-plastic geogrid can enhance tensile strength of geogrid, and is more good at resisting creep properties, and prolong the service life of the grid, which is suitable for coal mine, highway, railway, airport, well irrigation, civil construction and so on [17-20].
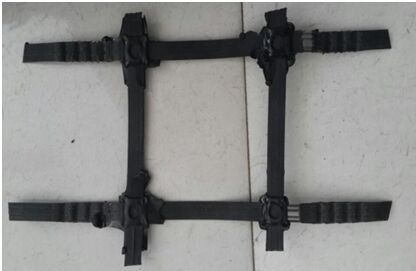
2.2. Mechanical Performance Index
In the design and construction process, due to the different load, the mechanical performance evaluation indexes of steel-plastic geogrids are also different. The mechanical properties of the steel-plastic geogrid (Fig. 1) include tensile strength, friction test intensity, tensile strength and the interaction between the fillers and so on [21]. The Mechanical performance indexes are shown in Tables 1 and 2.
Project | Type and Specification |
---|---|
Vertical (horizontal) to tensile strength (kN/m) | ≥ 128.0 |
The tensile strength of the 2% longitudinal strain(kN/m) | ≥ 30.4 |
The tensile strength of the 5% longitudinal strain(kN/m) | ≥ 61.2 |
Peak strain/% | ≤ 15.5 |
Creep ultimate strength at 20° (kN/m) | ≥ 45.3 |
3. TEST ANALYSES
Considering that the support effect is influenced by different temperatures, loads and fillers in engineering application, the tensile properties of geogrid are different. Therefore, the test of single and double geogrids pull out test of the above mentioned factors is carried out, and the strength of the steel-plastic geogrids is studied [22].
3.1. Tensile Strength
The steel-plastic geogrid is a flexible material, and the tensile strength is the main characteristic of the material of the synthetic material. The main parameters include that: the tensile strength of the longitudinal and transverse tensile strength is far greater than 50kN/m, the longitudinal and transverse elongation are no more than 13%, and the tensile strength of the elongation at 5% is much greater than 35kN/m.
In order to study the effect of different tensile rates on the tensile properties of steel-plastic geogrids, we selected three kinds of different specifications of the steel plastic geogrids in the uniform and different strain rates (50, 10, 1, 0.1, 0.05mm/min) of tensile in experiment research. Test equipment was used for the DR028J universal material testing machine. The experiment was carried out at (20 + 2)°C constant temperature and (60 + 5)% relative humidity conditions, and used the fixture to clamp the steel-plastic geogrid by the universal testing machine. The whole experiment process is controlled by universal testing machine.
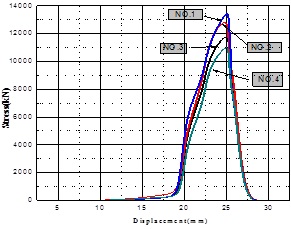
As we can see from Fig. (2), the four groups of steel-plastic geogrid stretching process can be roughly divided into three stages: low load and large deformation stage, stage of small high load deformation and fracture stage. At the beginning of loading process low load and large deformation stage: tensile load was small, the displacement of tensile deformation was large, and 4 groups had reached the final tensile testing of about 19 mm; and then had entered the second stage high load small deformation stage. In this stage, with the increase of loading, the displacement and deformation of geogrid were increasing gradually. It could be seen from the Fig. (2), the tensile curves increased, but at the same change of loading, the displacement of the second phase is smaller than the first stage, and tensile maximum length of the NO.1 group is only 6mm; when the loading exceeded 11kN, the four groups had entered the third stage fracture stage: in this stage, the wires were destroyed by root, the tensile curve decreased, and the tensile strength decreased rapidly until 0. It could be known from the analysis: the tensile strength of steel-plastic geogrid was influenced obviously by steel wires, and wires were destroyed, thereby decreasing the geogrid tensile strength.
Type |
Per meter tensile yield ≥(kN/m) |
Nominal elongation rate≤(%) | The tensile force at 2% elongation ≥(kN/m) | Width(m) | |||
---|---|---|---|---|---|---|---|
Longitudinal | Transverse | Longitudinal | Transverse | Longitudinal | Transverse | ||
GSZ60-60 | 60 | 60 | 3 | 3 | 54 | 54 | 6.0 |
3.2. Deflection Test
Due to the high flexibility of the steel-plastic geogrid, we could not measure the deflection of steel-plastic geogrid directly, so the geogrid was placed on a concrete slab, and the deflection tests were carried out. In order to guarantee the reliability of the test data, and take the influence factor into consideration, we made 4 plates for test. These plates were divided into 2 types, which were added to the steel-plastic geogrid, and phi 6-Q235 metal mesh. Concrete plate specifications were 1000mmx1000mmx100mm. The concrete slab is shown in Fig. (3).
The TLD-JG600 manhole cover press machine was used in the experiment, which was provided by LU DA of Shandong, and the machine consisted of a portal frame, cylinder, oil source and servo measurement control system. It is shown in Fig. (4). Oil source consists of three parts: Taiwan group pump motor, Italy Matsu Ki pump and Athos servo valve. Control system includes a spoke compound sensor, photoelectric encoder, temperature monitor, Lenovo machine operating procedures. This equipment has many advantages: design is reasonable, performance is reliable, structure is firm and the data are accurate. The maximum load was 600kN and the displacement can reach 400mm.
After the completion of the maintenance, the specimen is transported to the test device position. The hydraulics of the test machine were changed to the highest level. Specimen was placed on the supporting by forklift, and test operator fine-tuned the location of the specimen to ensure that the specimen was located in the middle, so the force became uniform. According to the experiment requirements, such as the adjusting of test equipment and the placement of test plate, and the sample was loaded by hydraulic lift. When the pressure plate contacted specimen and the stress started to change, all the dates were cleared. In order to reduce specimen surface roughness caused by stress concentration and obtain test data accurately, we chose a smaller load as a control load(1kN, 0.7kN and 0. 6 kN).
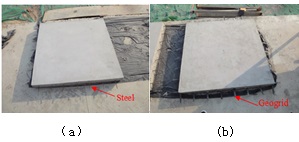
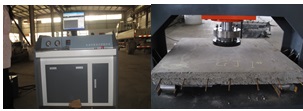
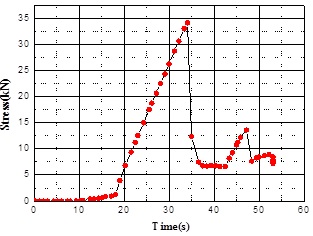
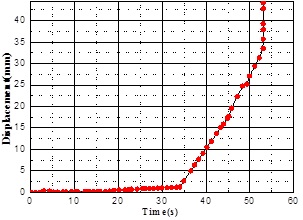
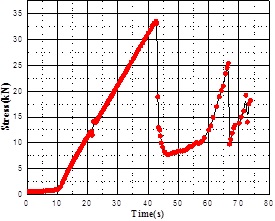
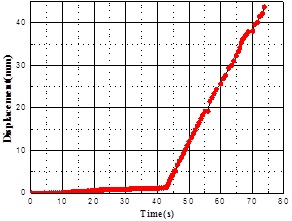
As we can see from Figs. (5-8).
- For GSW-1 and GSW-2, the two same steel-geogrids slab stress changes were similar. From the beginning of the applied loading to the load applied to the 10s, GSW-1 could withstand the pressure, and changes were slow and only grew to 1kN, the displacement almost no change. When the loading time reached 20s, stress began to increase and the plate began to crack. At the same time, stress decreased with the expansion of cracks. The steel geogrid began to play a role, and stress increased again. When the loading time reached 45s, stress reached the maximum, 34.1kN, and displacement reached the maximum 44.2mm.
- Due to the inclined plate, its stress was uneven. The stress of GSW-2 was rapidly grown in 10s, but there was no displacement changing. When the applied load time was up to 40s, GSW-2 appeared to crack and the withstand stress began to decline, and the displacement began to increase. As cracks continued to increase, the metal mesh began to play a role, letting the stress increase, but the stress only reached 27.5kN.
3.3. Creep Test
The so-called geogrid creep characteristic is the geogrid deformation with the continuation of time in the case of the external load. Geogrid is made of a series of complex processes and it has a grid structure, which has a direct effect on the long-term stability of reinforced earth structures [23]. The creep effect of the reinforced structure can lead to the change of stress state, and then cause the engineering loss of the whole stability. Therefore, the creep performance of the geogrid is the key to the stability of the geogrid tensile strength. In practical engineering application, due to the influences of different temperature and loading, the geogrids will be the creep deformation, so that the geogrid reinforcement function is greatly weakened or even the buildings lose its overall stability. For the steel-plastic geogrid, under the same tension (50kN/m), 20 DEG C, 40 DEG C two different environment temperature conditions, we obtained steel-plastic geogrids’ creep curve by test, as shown in Fig. (9).
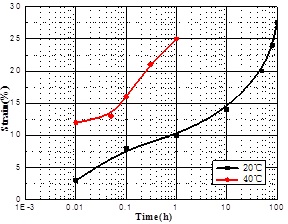
Through the analysis of Fig. (9), we could know that the strain spent 100 hours reaching 20 at 20 DEG C, but in 40 DEG C, only 0.5 hours is enough. The temperature had a great influence on steel-plastic geogrids’ creep, and the strain value increased with the increasing of temperature.
4. SUPPORT THEORIES
Anchor net support mainly use prestressed anchor (resin bolt, an end anchor head mechanical bolt) and anchor (metal), the selected anchoring force should be very strong, which can carry real time, after installation of surrounding rock prestressing [24].
In the broken soft rock roadway, bolt support is difficult to form a stable and effective load bearing structure, which is difficult to control the strong deformation of this kind of roadway, and it is not enough to ensure the overall stability of the roadway. Elastic-plastic theory analysis method is to study the deformation and failure of roadway surrounding rock, and is the most original and one of the most classical methods, which is the theoretical basis of the research on the deformation and failure mechanism of roadway surrounding rock [25-29].
The roadway surrounding rock is generally in a low confining pressure environment, and under this condition, the strain softening phenomenon generally occurs. The correlation test [30, 31] showed that the residual strength increased with the increase of confining pressure, and it showed a strong sensitivity to confining pressure.
Metal frame is the most commonly used method in soft rock tunnel. It is through the provision of passive radial support force, directly acting on the surface of the roadway surrounding rock, to balance the deformation of the surrounding rock, the surrounding rock deformation. Support technology is a common form of support in deep rock roadway [32-39].
The high quality of the anchor net can effectively control rock deformation, and boost to squeeze into the tunnel rock; it is an important measure to ensure the anchoring effect of bolts. And its main functions are as following:
preventing cataclysmic rock mass caving,
separating load from non-anchoring rock to the anchor,
anchor net cradling the broken rock. Although roadway surrounding rock has been broken, due to gravel bulking effect and transmit the force of the role of the media, the roadway deep surrounding rock remains a triaxial stress state, greatly improving the rock mass of residual strength (as shown in the Fig. 10) [40-43].
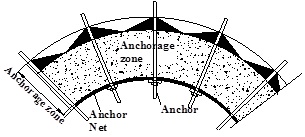
5. ENGINEERING EXAMPLES
5.1. Engineering Survey
Shandong Hualian mining is located in Yiyuan, Shandong Province. Most of the rock roadway lay in the complex geological conditions of rock. The tunnel buried is in more than 1000m, and tunnels are in great depth, rock with large deformation and high pressure conditions. The dip angle is from 25° to 30°. The uniaxial compressive strength is 2.2 MPa. The traditional support method is more and more difficult to control in the roadway support engineering so that many technical problems are encountered. Hualian ditch mine mainland layer can be divided into four engineering geological petro-fabric: Quaternary loose rock formation, Cambrian limestone shale rock group, Taishan Mountain Group metamorphic rock and igneous rock group, which is decided by the above characteristics. The Quaternary loose rock group stability is poor. Cambrian limestone shale rock hard to semi hard, but close to the Han Wang rupture, rock crushing rock quality classes VI to V level; metamorphic rock group and magmatic rock quality of grade III, ore produced for the Taishan Mountain Group wild goose Ling Guan formation, surrounding rock strength is higher.
5.2. Supporting Construction
5.2.1. Hang Network
According to the tunnel blasting footage and construction convenience, this section of the test steel grating linked to design the whole section hanging design of steel gratings method, from the top in turn laid on both sides, termination on the side of the rock to help foot. Geogrid width is arranged from 1.6m to 2.0m, and length is same as tunnel section perimeter. Geogrid lap width is 15cm~20cm, and nylon ties are used to fix geogrids reinforced with binding, as shown in Fig. (11).
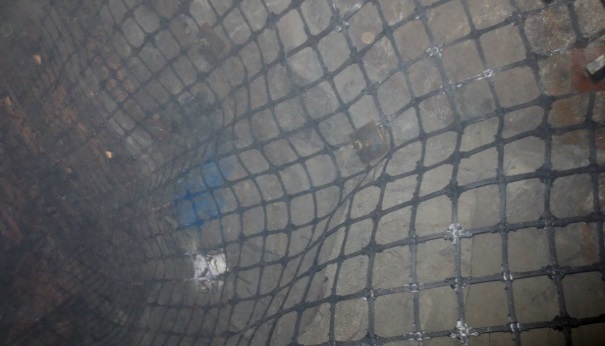
5.2.2. Mounting Bolt
Generally bolt installation is achieved by means of a drill. Preparations before the installation: first of all, we should clean rock debris and water in the anchor hole by using the blower to blow wind to the hole inside. In the stage, the operator cannot stand in the same position, and they must be on the side, so as to prevent the occurrence of danger. At the bottom of the hole, anchor was fastened through a special drill, and the operator ensured that the bolts were up to the resin anchoring agent. On the other end of anchor, the steel wire mesh and anchor plate was equipped. Then through the drilling rig setting bolt, the rig was used driven by the rotation, the anchoring agent was stirred evenly, during the period of about 20 seconds, the rig was closed, and then the rig continued pressure, two minutes later, and then the nut tightening torque of 150N·m, and finally the machine was discharged.
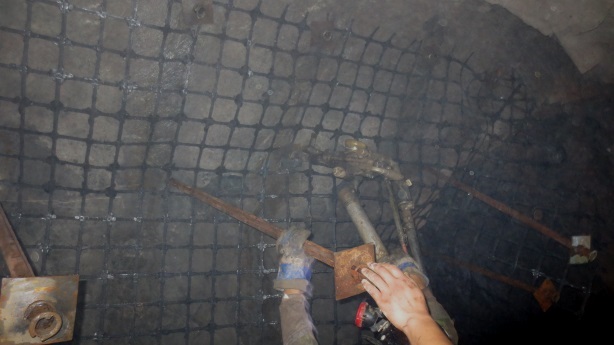
5.2.3. Jet Concrete
In the construction of secondary lining concrete, first of all, we should check whether the bolt hit and anchor Fig. (12) net meet the design objective, and give timely feedback and process to some existing problems. When the conditions are met, the secondary lining is poured. Pouring process is the same as the initial lining.
5.3. Analysis of Steel Grille Surrounding Rock Supporting Effect
For the scientific evaluation of the practical effect of the supporting scheme, the monitoring of the surrounding rock deformation of the test section is needed. Among them, the deformation monitoring of surrounding rock is mainly through the test of different depth of rock mass deformation in support and reinforcement in order to understand the weakening and failure scope of surrounding rock.
5.3.1. Multi-point Displacement Monitoring of Roof
After test section of roadway support, a drilling was fixed in the center of the roof and equipment of multi-point displacements was installed. There were six measuring points, which included 1.0m, 1.5m, 2.0m, 2.5m, 3.0m and 5.0m. Monitoring data with time change curves are shown in Fig. (13)
It can be seen that:
I. The accumulated displacement of the bottom wall was obvious. Thereafter, the deformation of surrounding rock was gradually attenuated. After 25 days, the deformation of the roadway floor tended to be stable.
II. After 50 days, the rock deformation and stability values were 16.0mm, 6.5mm, 5.5mm, 4.0 mm, 5.0 mm and 3.0mm at all intervals, which included 0~1.0m, 1.0~1.5m, 1.5~2.0m, 2.0~2.5, 2.5~3.0, and 3.0~5.0m. The total displacement on the roof surface of surrounding rock reduced from 78.5 mm to 40.0mm, and the maximum separation interface transfers from the front guard roof 2.5m deep to the surface of 1.0m.
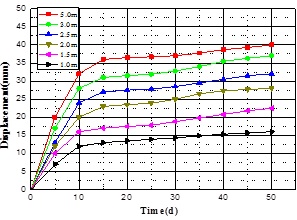
5.3.2. Multi-point Displacement Monitoring of Roadway Side
A drill hole was fixed in the test section of the roadway sides and equipment of multi-point displacements was installed. There were four measuring points, which included 1.0m, 1.5m, 2.0m, 2.5m, 3.0m and 5.0m. Monitoring data with time change curve are shown in Fig. (14).
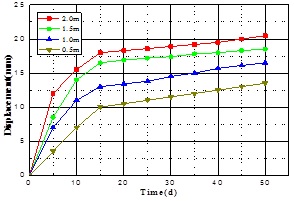
It can be seen that:
I. About 15 days after the reinforcement, the total displacement of the roadway sides increased significantly. After 15 days, the deformation of the measuring points gradually decreased and tended to be stable.
II. On the 50th day, the rock deformation and stability values were 13.5 mm, 3.0 mm and 2.5 mm and 1.6 mm at intervals, which included 0~0.5m, 0.5~1.0m, 1.0~1.5 m, 1.5~2.0m. The maximum separation interface changed to the surface of 0.5m, and opening of the roadway sides’ displacement was about 20.5mm. With the increasing surface distance, the displacement of surrounding rock was gradually reduced.
5.3.3. Multi-point Displacement Monitoring of Floor
After the test section of roadway supporting, we arranged a drill hole in central floor and installed multi-point displacement equipment. There were six measuring points, which included 1.0m, 1.5m, 2.0m, 2.5m, 3.0m and 5.0m. Monitoring data with time change curve is shown in Fig. (15).
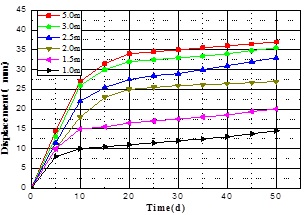
It can be seen that:
I. The total displacement of the bottom wall in the 25d increased obviously after the reinforcement. Thereafter, the deformation of surrounding rock was gradually attenuated. After 30 days, the floor of the roadway tended to be stable.
II. On the 50th day, less than 1.0m, in 1.0~1.5m, 1.5~2.0m, 2.0~2.5m, 2.5~3.0m, and 3.0~5.0m, the rock deformation and stability values were 14.5mm 5.5 mm and 7.0, 6.0mm and 2.5mm and 1.5mm. Maximum separation interface with a front protection plate deeply transferred to a surface of 1.0m.
The orifice of the surface of the base plate of the surrounding rock displacement was about 37.0mm. The distance from the surface of the bottom plate is gradually reduced, the deformation of the surrounding rock displacement which were less than 1.0 and 1.0~1.5m, accounting for 39.2% and 14.8% in total displacement. 1.5~2.0m, 2.0~2.5, 2.5~3.0m, 3.0~5.0m rock deformation accounted for the total displacement capacity of 19.0%, 16.2%, 6.8% and 4.0% respectively.
5.4. Effect Evaluation
Through above mine supporting analysis in Hualian, the data showed that the deformation tended to be stable in supporting 25 days. After supporting 50 days, the maximum displacement of the roof was 40mm, maximum displacement of the side was 20.5mm, the maximum displacement of the floor was 37mm, and the maximum deformation speed only was 0.8mm/d. The roadway is in a steady state, and the supporting effect was good.
CONCLUSION
- Steel-plastic geogrid has better deformation resistant structure, twisted nodes and possesses roadway surrounding rock deformation settlement ability, high flexibility, high elasticity, nodes are not easy to be torn to support a multi direction load, and have a great effect on disperse loading,which has good tensile property, creep property and deflection performance.
- Steel-plastic geogrid and high-strength prestresses anchor combined support apply enough pre tightening force to the rock, improving the stress state of surrounding rock, controlling the deformation of surrounding rock effectively, and reducing the cost of support. Steel-plastic geogrid plays an important role in roadway supporting.
CONFLICT OF INTEREST
The authors confirm that this article content has no conflict of interest.
ACKNOWLEDGEMENTS
This work was financially supported by:
(1) National Natural Science Foundation of China (NSFC) (41372289).
(2) SDUST Research Fund (2014TDJH103).