All published articles of this journal are available on ScienceDirect.
A Comprehensive Review on Effects of Material Composition, Mix Design, and Mixing Regimes on Rheology of 3D-Printed Geopolymer Concrete
Abstract
Recent years have witnessed a significant growth in the research and development of additive manufacturing methods involving concrete and cementitious materials, with technologies like three-dimensional (3D) printing becoming more widely used in the construction industry. Construction has the possibility to be revolutionized, not only in the context of cost savings but also in the context of increased sustainability and functionality. 3D printing of concrete is a cutting-edge technology that has the potential to speed up construction, reduce labor costs, give architects more creative freedom, improve precision, obviate requirements for formwork, and result in less construction wastes. In addition, 3D printing can be a long-term solution for both economy and environment. Even though 3D printing in concrete has made tremendous strides recently, developing an effective 3D-printable material that decreases material usage and enhances performance is critical for carbon dioxide reduction. Robust geopolymer formulations for 3D printing concrete technology in current construction applications have emerged as the subject of much research among scientists to find novel ways to circumvent this constraint. This study intends to highlight the current state of the art in developing 3D-Printed Geopolymer Concrete (3DPGC) with a comprehensive review related to the material composition, mix design, and mixing regimes on rheology of 3DPGC. The rheology of 3DPGC in terms of printability and buildability is discussed. The mixing regimes employed for the preparation of one-part and two-part 3DPGC are tabulated and commented on. Lastly, the research gaps are identified and summarized, and several research directions are also provided for future investigations to expedite the ubiquitous use of 3DPGC in versatile construction applications.
1. INTRODUCTION
In this new era of Industry 4.0, three-dimensional (3D) printing or additive manufacturing has attracted a lot of interest in recent years from both the building industry and the scientific community around the globe. [1]. This technique involves the deposition of materials in a layer-by-layer fashion to create the desired structure with a gantry-based 3D printer or an advanced robotic arm from a digitally designed model via a geometric code (G-code) generated from computer-aided design and slicing software [2]. Additive manufacturing technology, which is already used in the automobile [3], medical [4, 5], and aerospace [6] sectors, is yet in a stage of infancy in its contribution to the industrialization and digitalization of the construction sector [7, 8]. Many additive manufacturing technologies, including extrusion-based [9] and powder-bed-based [10-15], have been cultivated in the previous decade for 3D printing concrete. Building components with complicated geometry as per industry demand can be manufactured offsite utilizing powder-bed-based methods without costly formwork and assembled on-site. Hence, most of the research has focused on this method of 3D printing concrete [16]. 3D printing in concrete is a technologically advanced method holding potential benefits such as rapid construction, reduced labor expenditure, architectural freedom, high precision, formwork-free construction, and lesser construction waste generation [9, 17-24]. With technological advances like topology optimization, 3D printing can be a sustainable technology, providing economic and environmental benefits [25-28]. Due to its distinctive benefits, including enhanced production on demand and construction safety over traditional construction processes, 3D printing has recently expanded its application to the building and construction sectors. It appears to be the trend-setter, providing tremendous opportunities to revolutionize the construction industry in the coming years [29-35].
Extrusion-based concrete 3D printing is fundamentally characterized by the ingredients (raw materials) and ingredient properties and their design mix to fulfill the rheological essentials of printability, i.e., pumpability, extrudability, and buildability of the mixture [29, 36-43]. The mix design poses one of the major challenges for 3D printing in concrete [44]. When extruded, owing to the absence of formwork, the mixture must be able to hold itself and succeeding layers while still flowing freely throughout the pumping system [45]. Fast-setting yet adequate bonding mixtures are best suited for concrete 3D printing, which may be achieved by incorporating admixtures [46, 47]. The use of Ordinary Portland Cement (OPC) [48, 49] or Supplementary Cementitious Materials (SCMs) or industrial by-products [50, 51] such as Fly Ash (FA), Ground Granulated Blast-Furnace Slag (GGBS), metakaolin, Silica Fume (SF), etc., has been reported as a primary binder in the mix.
The continuous production of cement has led to massive carbon dioxide emissions in the atmosphere, resulting in global warming, which has a pernicious effect on the environment. Geopolymer is a promising long-term substitute for OPC binders. The formulation of the geopolymer mix contains aluminosilicate sources such as GGBS, FA, etc., which are industrial waste, thus beneficial in solving their storage and disposal issues [52, 53]. The utilization of geopolymers provides a sustainable solution to deal with this issue because cement is not required in its preparation, resulting in a cleaner environment by reducing carbon footprints [54-57]. Furthermore, geopolymers possess attractive rheological properties such as high thixotropy, which is demanded and desirable in the case of 3D printing of concrete [58, 59]. Studies comparing geopolymers to OPC for 3D printing of concrete have been limited despite the advantages noted above. Generally, a solid aluminosilicate precursor and a liquid alkaline activator (usually sodium (Na) or potassium (K) - based) make up the two-part geopolymer combination [60, 61]. For commercial and large-scale use, alkaline activator solutions that are viscous and corrosive are eventually difficult to manage [62]. Geopolymer’s rheological characteristics are also intricate and highly reliant on the amount and nature of alkaline activators and the alkali/silicate ratio, which is difficult to regulate in actuality [63]. Thus, the use of small doses of solid activators (known as “one-part geopolymer” or “just-add-water geopolymer”) [64] rather than huge amounts of liquid activators in 3D-Printed Geopolymer Concrete (3DPGC) should be investigated to utilize the benefits of one-part geopolymer, as very few attempts have been made in this area [65, 66].
Traditional methods of reinforcing concrete, on the other hand, either do not work with 3D printing or completely negate its advantages, and quite a few experiments have been carried out by experts in this direction [43, 47, 67-74]. Scientists have also examined the inclusion of fibers in the 3D printing ink to enhance ductility and flexural performance [75-77].
This article describes the rheology of 3DPGC related to the design mix and the effect of geopolymer formulation (one-part and two-part) in terms of material composition, mix design, and mixing regimes on the rheological and structural characteristics. In addition, the use of various reinforcing elements and their effects on the properties of 3DPGC are discussed, along with the research gaps for future investigations.
2. RHEOLOGY OF 3DPGC
Two fundamental metrics that characterize the rheological properties of fluids are yield stress and plastic viscosity. The yield stress is caused by the adherence and contact roughness between the particles in the slurry, which reflects the slurry's difficulty in surmounting frictional resistance and generating plastic flow [78]. The static yield stress denotes the greatest stress necessary for the substance to flow from its resting state, whereas the dynamic stress represents the minimum stress necessary to sustain flow [79]. The plastic viscosity is the attribute by which the slurry's internal structure impedes its flow. Plastic viscosity reflects slurry cohesiveness. Slurry will be more stable when sheared if its plastic viscosity is higher [78]. Plastic viscosity expresses shear stress growth with shear rate [79]. Viscosity recovery demonstrates the material's ability to recover across various shear rates. In contrast, the structural build-up rate serves as a guide for the material's stiffening rate before its final setting [80]. Due to the material's thixotropy, there is a distinction between static and dynamic stresses. Thixotropy refers to a reversible, isothermal, time-dependent decrease in viscosity when a fluid is subjected to increased shear stress or shear rate [61]. The material must be flowable and extrudable via a nozzle, adhere to the preceding layer, and keep its form under the growing stress induced by successive layer deposition to realize the acceptable quality of 3DPGC. The printability (pumpability and extrudability) and buildability of the printable ink characterize the quality of 3DPGC, thus relating them to the rheological properties of 3DPGC.
2.1. Printability (Pumpability and Extrudability)
In the printing process, pumpability refers to a print mix's ability to be pumped to the printing device under pressure and maintain its initial qualities. An easily transportable substance (typically by pumping) is required for 3D printing in concrete. Yet, an extruded material that is reasonably rigid is required to guarantee that the deposited filaments must preserve their shape. Print mix material's capacity to extrude smoothly as a continuous filament at the print head with an unimpeded material flow can be termed extrudability. Extrudability is dependent on several factors, including the nozzle design (size and shape), the mode of extrusion (such as screw or ram), the rate of extrusion, and, perhaps most intriguingly, the rheology of the material [21, 81-86].
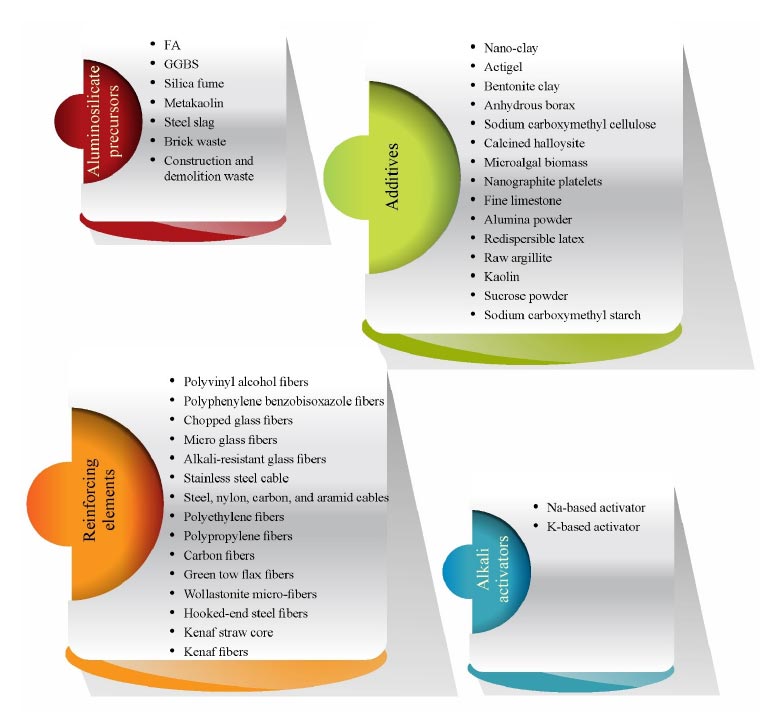
2.2. Buildability
It is possible to describe the print material's buildability as its ability to continue escaping from the nozzle through extrusion as bonded layers and withstand the overburdened weight of subsequent layers generated by the printing phenomenon. Stresses induced by gravity reach their peak in the bottom layer when the material has achieved the final object height. As a result, gravity-induced stresses in the bottom layer could cause printing failure due to yielding [81, 87, 88]. Even the print speed, path length, and layer thickness influence the printed material’s structuration rate since these parameters affect the growth of yield stress over time [89]. Because buildability is time-dependent, it can be determined utilizing the structural build-up rate through the change in the rate of yield stress with time [45, 87]. The chemical and physical mechanisms in the fresh paste affect the structural buildup rate [90]. The structural buildup must be more rapid to build up more swiftly within the permissible yield stress limit [91]. The static yield stress of printable cementitious materials is inextricably linked to their buildability and form preservation [81]. For the printed specimen to remain stable, the bottom layer's yield stress must constantly exceed the stress imposed by the weights of its above layers [87]. This stress is equal to ρgH/, where ρ, g, and H are the density of the fresh mixture, gravitational force, and final height of the printed object, respectively [81]. Green strength may be employed in 3D printing to show how many layers can be placed before the bottom layer deforms significantly. In contrast, hardened strength indicates where irreversible failure can be predicted [66, 85, 92]. Moreover, the interlayer bonding must be proper, as it is directly related to interlayer strength, and dramatically depends upon the print time interval. In contrast, the formation of cold joints at the interface would negatively influence the mechanical properties.
To improve the buildability, broader filaments should be printed, which can decrease the risk of buckling failure. The weight of the top layers causes strength-based failure below a specific critical height, while failure owing to buckling becomes critical beyond this height [45, 81, 93, 94]. Layer deformations may cause instabilities. Formwork supports concrete in traditional building practices; therefore, this is not an issue. But 3DPGC is a formwork-free technology, therefore, concrete that is printed should be self-supporting. There are two ways to enhance the buildability of 3DPGC: (1) initial concrete mixing additives and (2) intervention to improve buildability at the print head (set-on-demand). The former is the most studied, although it influences pumpability. The latter comprises heating, mixing accelerators, magneto rheological control, or ultrasonication at the print head to boost the material's yield strength before extrusion and prove to be more effective [95].
3. MATERIAL COMPOSITION AND MIX DESIGN OF 3DPGC
Fig. (1) presents the various aluminosilicate precursors, alkali activators, additives, and reinforcing elements employed in the preparation of geopolymers for 3D printing applications, as reported in the literature.
The geopolymer material composition and preparation, including types of aluminosilicate precursors, alkali activators and their molar ratios, aggregates, additives, reinforcing elements, and curing conditions, are summarized in Table 1. The rheological and physical properties, such as workability, yield stress, viscosity, setting time, thixotropy, shape retention, print quality, buildability, and porosity are discussed.
Ref. | Aluminosilicate Precursor | Activator | Ratio | Additive | Aggregate | Reinforcing Element | Curing Condition | Property Measured/Experimental Technique Adopted | |
---|---|---|---|---|---|---|---|---|---|
T (°C) | RH (%) | - | |||||||
[16] | FA | NaOH + Na 2 SiO 3 | SiO 2 /Na 2 O = 3.22, A = 2.5 | CMC powder | Silica sand (CS 330 μm and FS 172 μm) a | PVA, PP, and PBO fibers | 60 for 24 h | - | IBS, CST, FS |
[96] | FA, GGBS | NaOH + Na 2 SiO 3 , KOH + K 2 SiO 3 | SiO 2 /Na 2 O = 2.0, 3.22, SiO 2 /K 2 O = 2.02, A = 1.5, 3.0, B = 0.4 | CMC powder, Anhydrous borax | Sand (CS 898 μm and FS 172 μm) a | - | Ambient for 3 days | - | EX, OT, SRA, CST |
[97] | FA:GGBS:Microsilica (75:15:10) | NaOH + Na 2 SiO 3 | A = 2, 1.85, 1.6, B = 0.46, C = 1.5 | Nano-clay (2.5%) | Fine river sand (2 mm) b | - | - | - | Structuration rates, structural breakdown, and build-up rate, IBS |
[60] | FA, GGBS, Microsilica | KOH + K 2 SiO 3 | - |
Thixotropic additives
(Actigel and cellulose) |
Fine river sand | - | Ambient for 7, 14, 28 days | - | OT, DE, XRD, SEM, CST, FS, tensile bond strength |
[61] | FA (90-100%), GGBS (0-10%), Un-densified SF (0-10%) | NaOH + Na 2 SiO 3 | SiO 2 /Na 2 O = 1.8, B = 0.46, C = 1.5 | - | - | - | Room temperature (25 ± 2) for 7 days | - | FESEM, XRF, XRD, TB, VR, SBU, IC, CST |
[98] | FA, GGBS, Microsilica | Liquid K 2 SiO 3 (MR = 2) | - | HPMC (2%) | Fine river sand (1.18 mm) b | Chopped glass fibers | Lab temperature for 28 days | - | CST, FS, TS |
[99] | FA, GGBS, Microsilica | Liquid K 2 SiO 3 (MR = 2) | - | Thixotropic additives | Fine river sand (1.15 mm) b | - | Ambient for 28 days | - | SEM, XRD, YS, V, EX, OT, DE, CST, TS, FS, IBS |
[77] | FA | NaOH + Na 2 SiO 3 | A = 2.5, B = 0.38, 0.467 | CMC powder | Silica sand (CS 330 μm and FS 172 μm) a | PP fibers | 60 for 24 h | - | SRA, W, AP, IBS, CST, FS |
[100] | FA:GGBS:SF (60:35:5, 60:25:15, 70:15:15) | NaOH + Na 2 SiO 3 | A = 2, C = 0.55 | - | River sand (1 mm) b | - | 60 for 24 h + 20 (ambient) for 7 days | - | ST, OT, W, YS, PV, SRA, BU, CST, FS, SEM |
[76] | FA, GGBS, SF | K 2 SiO 3 solution + NaOH solution | SiO 2 /K 2 O = 1.8, C = 1.1, 1.3, 1.5, 1.7, 1.9 | Highly purified attapulgite clay | Fine river sand (2 mm) b | Micro glass fibers | 25 (ambient) | 45 | EX, BU, SRA, TB, OT |
[101] | FA, GGBS | KOH + K 2 SiO 3 | SiO 2 /K 2 O = 1.56, B = 0.35, 0.4, D = 0.30, 0.35 | Nano-clay (0.5%) | - | - | 23 ± 2 for 28 days | - | TB, CST, ST, initial strength evolution, IC, FESEM, SRA, SBU |
[79] | FA, GGBS, SF | KOH + K 2 SiO 3 | - | Actigel and bentonite clay | Sand (1 mm) b | Alkali resistant glass fibers | 21 ± 2 | 60 ± 5 | W, TB, V, CST, FS |
[67] | FA:GGBS:Microsilica (80:15:5) | K 2 SiO 3 | C = 1.5, D = 0.45 | Thixotropic additives (magnesium aluminum– silicate nano-clay) | Fine river sand (1.18 mm) b | Hybrid reinforcement – PVA fibers, stainless steel cable | Ambient for 7 days | - | SEM, statistical analysis, FS, TB |
[50] | FA, GGBS (10, 20, 30%), SF (10, 20, 30%) | Anhydrous Na 2 SiO 3 powder | SiO 2 /Na 2 O = 1.4 | Attagel-50 thixotropic thickener-magnesium aluminum silicate | Quartz sand (40-80 mesh) b | - | Ambient for 28 days | - | AV, TB, PV, YS, SEM |
[68] | FA, GGBS, SF | Penta sodium metasilicate powder | - | - | Sand (1 mm) b | Steel, nylon, carbon, aramid, and polyethylene micro-cables | Sealed and stored at room temperature for 24 h, then 20 ± 1 in a moist cabinet | 95 ± 5 | Bond behavior (pull-out), CST, shear test, direct tensile test, effect of print configuration on mechanical behavior |
[102] | FA, GGBS, SF | Penta sodium metasilicate powder | - | Hydroxyethyl cellulose | Sand (0.1 - 0.6 mm) | PP fibers, steel micro-cable | - | - | FS |
[75] | Gladstone FA | NaOH + Na 2 SiO 3 | A = 1, B = 0.26, SiO 2 /Al 2 O 3 = 2 | - | Sand (0.3 mm) b | Steel, PP fibers | Room temperature for 12 days + 70 for 2 h | - | W, FS |
[103] | FA | NaOH + Na 2 SiO 3 | A = 2.5, C = 2, D = 0.35 | - | - | Green tow flax, carbon fibers | 75 for 24 h + ambient for 7 and 28 days | - | DE, CST, FS |
[104] | GGBS:FA:SF (3:1:0.5) | Sodium meta-silicate powder | D = 0.31, 0.33, 0.35 | - | - | - | Sealed with a plastic bag, then 25 for 21 days | - | W, OT, CST, printing parameters such as pumping (extrusion) pressure and print head speed, effect of percentage of activator and water to solid ratio |
[105] | GGBS, steel slag | Sodium metasilicate + NaOH | Si/Na = 1.0, 0.9, 0.8, 0.7, 0.6, 0.5, D = 0.35 | Defoamer, superplasticizer, and re-dispersible latex | Sand | - | - | - | BU, EX, YS |
[106] | FA (60-70%), GGBS (15-35%), SF (5-15%) | NaOH + Na 2 SiO 3 | SiO 2 /Na 2 O = 3.23, A = 2, C = 0.55, D = 0.4 | Nano graphite platelets (0.1, 0.3, 0.5, 1 wt.%) | River sand (0 – 1 mm) | - | 60 for 24 h + 20 till testing | - | OT, SRA, ST, W, BU, DE, CST, FS, SEM, XRF, XRD |
[51] | Metakaolin, calcined argillite | Na 2 SiO 3 | - | Raw argillite, kaolin | Sand | Wollastonite, glass fibers | 20 for 7 days | 85 | W, IBS, FS |
[107] | Metakaolin | NaOH + Na 2 SiO 3 |
SiO
2
/Al
2
O
3
= 3.48, 3.31, 3.75, 2.83,
Na 2 O/SiO 2 = 0.25, 0.21, 0.19, 0.26, Na 2 O/Al 2 O 3 = 0.86, 0.69, 0.70, 0.73, D = 0.48, 0.40, 0.43, 0.46 |
- | - | - | - | - | Rheology and buildability by preheating process |
[66] | FA:GGBS (85:15, 70:30, 60:40) | KOH + K 2 SiO 3 | A = 1.5, C = 0.85, D = 0.35 | - | Fine river sand (2 mm) b | - | Ambient for 28 days | - | SYS, TB, VR, CST, SBU, XRD, FESEM, EA |
[108] | FA:GGBS (1:1) | Anhydrous sodium metasilicate powder | - | - | Sand (CS 898 μm and FS 172 μm) a | - | Sealed in container, 60 for 24 h + ambient (23 ± 3) | - | CST, FS, IBS |
[65] | FA:GGBS (1:1) | GD grade sodium silicate powder and anhydrous sodium metasilicate powder | GD grade sodium silicate powder (SiO 2 /Na 2 O = 2.0) and anhydrous sodium metasilicate powder (SiO 2 /Na 2 O = 0.9), GGBS to FA mass ratio = 1.0, C = 1.5 | Sucrose powder as a retarder | Sand (Fuller Thompson theory was used to determine proportions of silica sands) | - | 23 ± 3 for 28 days | - | EX, SRA, SYS, DYS, PV, TB, CST, FS, AP, EA |
[109] | FA:GGBS (70:30) | KOH + K 2 SiO 3 | A = 1.5, B = 0.1, C = 0.85, D = 0.35 | - | Fine river sand (1.18 mm) b | - | - | - | EX, BU, TB, YS, V, CST |
[110] | FA:GGBS (1:1) | Anhydrous sodium metasilicate powder | FA to GGBS mass ratio of 1.0, SiO 2 /Na 2 O = 0.9 | Sucrose powder (0.2% mass), CMC powder | Sand (D 50 of 176 μm and D 10 of 108 μm) | Oil-coated PVA fibers | Ambient (23 ± 3) for 24 h + 60 for 24 h | - | BD, AP, CST, FS, fiber orientation using a digital microscope |
[111] | FA (50 wt.%), GGBS (50 wt.%) |
Anhydrous sodium
metasilicate powder |
SiO 2 /Na 2 O = 0.9, B = 0.08:1.0, C = 1.5:1.0, D = 0.34:1.0 | - | CS D 50 = 896 μm, FS D 50 = 172 μm, mass ratio of CS to FS = 1.0:0.5 | - | 60 for 24 h, ambient (23 ± 3) for 7 and 28 days | - | ST, W, OT, SYS, IBS, CST, FS |
[112] | FA:GGBS (1:1) | Anhydrous sodium metasilicate powder + GD grade sodium silicate powder | - | Sucrose powder | Sand (CS D 50 of 840 μm, FS D 50 of 176 μm) | Wollastonite micro-fibers | Sealed in a container, then 60 for 24 h + ambient for 7 days | - | SRA, YS, CST, FS |
[113] | FA:GGBS (1:1) | Anhydrous sodium metasilicate | SiO 2 /Na 2 O = 0.92, Water/GGBS = 0.31, Water/FA = 0.05, CS/Binder = 1.0, FS/Binder = 0.5, SiO 2 /Al 2 O 3 = 4.2, 4.3, 4.41, 4.42, H 2 O/Na 2 O = 42.20, 29.24, 22.38 | Highly purified magnesium alumino silicate (0.75%), pure sucrose in solid form (0.5, 1, 1.5) | CS (D 50 and D 90 = 498 μm and 583 μm, respectively), FS (D 50 and D 90 = 172 μm and 271 μm, respectively) | - | 23.5 | 40 | SYS, VR, AV, elastic behavior of geopolymer while printing, polymerization reaction of geopolymer binders (DSC, FTIR) |
[114] | FA, GGBS | NaOH + Na 2 SiO 3 , KOH + K 2 SiO 3 | A = 1.5, 2.5, and 3.0, Mass ratio of FA to GGBS = 3.0, B = 0.4 | Anhydrous borax, CMC | Sand | - | 23 ± 3 for 3, 7, 28 days | - | W, EX, SRA, CST, FS, IBS |
[115] | FA:GGBS (1:1) | Anhydrous sodium metasilicate | SiO 2 /Na 2 O = 1 | - | Two grades of silica sand |
Micro PVA
fibers |
Microwave heating, then at 25 for 0, 5, 10, and 20 seconds | 50 | SYS, effect of microwave heating on IBS, BU, filament stiffness, surface moisture content, inter-layer temperature, total mass loss, VR and reaction kinetics |
[85] | FA | NaOH + Na 2 SiO 3 | B = 1.07-1.96, C = 1.5 | - | Quartz sand (125-150 μm) | - | - | - | Printability, SBU, ST, OT, XMT |
[78] | GGBS (50%) | NaOH + Na 2 SiO 3 | SiO 2 /Na 2 O = 1.7, D = 0.28 | Sodium carboxymethyl starch (CMS) (0%, 2%, 4%, 6%, 8%) | Calcium carbonate (50%) (0.25 mm) b | - | 23 | 90 | W, DYS, PV, ST, CST, FS, drying shrinkage, porosity, water retention rate, microstructure |
[116] | GGBS | Raw water glass + NaOH | D = 37.70% | Sodium carboxymethyl starch | - | - | - | - | ST, DSC (heat release), ATR/FTIR (reaction degree), TB, three interval thixotropy test (recoverability), Zeta potential analysis, YS, PV, VR |
[80] | FA:OPC:SF (80:20:0, 77.5:20:2.25, 75:20:5, 65:35:0, 60:35:5, 50:50:0, 47.5:50:2.5, 45:50:5) | Na 2 SO 4 powder | C = 1.35, D = 0.45 | - | Fine river sand (2 mm) b | - | - | - | SYS, SBU, TB, BU |
[117] | GGBS | Na 2 SiO 3 .5H 2 O | C = 0.83, D = 0.35, 0.40 | Attapulgite nano-clay (0, 0.2, 0.4, 0.6%), hydromagnesite seed (nucleation seed) (0, 1, 2%) | Sand (1.18 mm) b | - | - | - | SYS, SBU, TB, EX, BU, SEM, FESEM, XRD |
[118] | Metakaolin | NaOH + Na 2 SiO 3 | - |
Spirulina
platensis (0.6-2.8 wt.%), Tetraselmis suecica (0.6-2.8 wt.%), lignin (0.6-2.8 wt.%), bentonite (rheology modifier) |
- | - | Ambient for 7 or 28 days, then at 800 for 4 h in a muffle oven | - | YS, V, BU, CST, SEM |
[86] | Hollow brick (30%), red clay brick (30%), roof tile (30%), glass (10%) | Ca(OH) 2 , NaOH, Na 2 SiO 3 | A = 0, 0.5, 1, D = 0.33 | - | - | - | 23 ± 2 for 7 and 28 days | 50 ± 5 | W, EX, BU, SRA, CST |
[119] | Hollow brick (26.67%), red clay brick (26.67%), roof tile (26.67%), glass (10%), concrete rubble (10%) | Ca(OH) 2 , NaOH, Na 2 SiO 3 | A = 1, C = 0.35, D = 0.33 | - | Fine recycled concrete aggregates (2 mm) b | - | 23 ± 2 for 7 and 28 days | 50 ± 5 | W, BU, CST |
[120] | GGBS:FA:Steel slag (50:50:0, 50:40:10, 50:30:20, 50:20:30, 50:10:40) | Flue gas desulfurization gypsum (FGD), Na 2 SiO 3 | SiO 2 /Na 2 O = 1.4 | - | Quartz sand (40-80 mesh) | - | - | - | YS, V, W, ST, OT, BU, CST, FS, IC, SEM, XCT, FTIR, micromorphology, porosity |
[121] | GGBS:FA (1:1) | GD grade sodium silicate powder and anhydrous sodium metasilicate powder, mass ratio of silicate powder = 1.0 | GD grade sodium silicate powder (SiO 2 /Na 2 O = 2.0 and anhydrous sodium metasilicate powder (SiO 2 /Na 2 O = 0.9), C = 1.5 | Sucrose powder as a retarder | F-sand D 50 = 176 μm, M-sand D 50 = 498 μm, C-sand D 50 = 840 μm | Wollastonite microfiber (5%, 10%, 15%, 20%, 30% replacement of F-sand | 60 for 24 h, then 23 ± 2 for 28 days | - | ST, EX, BU, SYS, DYS, PV, CST, FS, micromorphology characterization, SEM |
[122] | GGBS:FA (1:1) | NaOH + Na 2 SiO 3 | SiO 2 /Na 2 O = 0.34, 0.54, 1.04, 1.72, 2.15, B = 0.35, C = 1.5 | - | CS (D 50 and D 90 = 498 μm and 583 μm, respectively), FS (D 50 and D 90 = 172 μm and 271 μm, respectively), CS:FS = 2:1 | - | - | - | YS, ST, ATR FT-IR, CST, non-destructive ultrasonic transmission, mixing process of activator, BU |
[123] | FA:GGBS (40:60) | N grade Na 2 SiO 3 | SiO 2 /Na 2 O = 0.50, C = 0.75, 1, 1.5, 2, D = 0.14, 0.16, 0.21, 0.24 | Nano-clay (rheology modifier), anhydrous borax (retarder) | F-sand D 50 = 176 μm, M-sand D 50 = 498 μm, C-sand D 50 = 840 μm, (0.45:0.21:0.35) | - | - | - | SYS, PV, TB, VR, SRA, SBU |
[124] | FA:Limestone:SF:OPC (70:30:0:0, 60:20:0:0, 50:20:0:30) | NaOH + Na 2 SiO 3 , Na 2 SO 4 | D = 0.60, 0.65, 0.25 | Lightcrete 02TM surfactant liquid as foaming agent and foam stabilizer (1, 2, 3%) | - | - | 70 for 24 h | - | YS, PV, W, VR, SRA, BU, CST, specific gravity, thermal conductivity, SEM, MIP |
[125] | Cement (CEM I 42.5R), FA, metakaolin | NaOH + Na 2 SiO 3 | A = 2.5, C (geopolymer (FA/metakaolin:sand) /hybrid (FA/metakaolin and cement:sand)) = 1:1, D = for FA (0.25, 0.28, 0.35), for metakaolin (0.35, 0.38, 0.40), D (hybrid (1:1) with FA base) = 0.28, D (hybrid (1:1) with metakaolin base) = 0.35, D (control sample (cement:sand = 1:1)) = 0.125 | - | Commercial quartz sand | - | 75 for 24 h, then at ambient | - | Raw material characterization by SEM, XRD, XRF, FTIR, thermal analysis, radioactivity test, CS, FS, abrasion resistance |
[126] | FA | NaOH + Na 2 SiO 3 | B = 0.66, C = 1.5 | Halloysite (less reactive)/meta-halloysite (calcined-highly reactive) (0-15 wt.% of FA) | Dust-free silica sand having high quartz content (90-250 μm) | - | 21 ± 1 | 50 | Characterization by XRD, TGA, ATR FT-IR, particle size and BET surface area analysis, dissolution reactivity, transmission electron microscopy (TEM), XCT, ST, BU, CST, FS |
[127] | FA:GGBS (80:20) | NaOH + Na 2 SiO 3 (20 wt.%), sodium gluconate (1 wt.%) | - | Kenaf straw core | - | Kenaf fiber | - | - | AV, DE, SRA, ST, EX, FS, SEM |
[128] | Hollow brick (26.67%), red clay brick (26.67%), roof tile (26.67%), glass waste (10%), concrete waste (10%) | Ca(OH) 2 (0, 4, 8 wt.%), NaOH (10M, 12.5M) | C = 0.35, D = 0.33 | - | Fine recycled concrete aggregates (2 mm) b | - | 23 ± 2 for 7, 28 and 90 days | 50 ± 5 | CST, FS, IBS, influence of alkaline activator |
[129] | GGBS:FA (100:0, 75:25, 50:50, 25:75, 0:100), GGBS:SF (95:5, 90:10) | Waterglass (sodium silicate aqueous) | B = 0.425, SiO 2 /Na 2 O = 1.6 | - | - | - | 20 ± 2 | 50 ± 5 | Apparent density, ST, SYS, TB, VR, IC |
[130] | FA:GGBS (1:1, 1.7:1, 2:1, 3:1) | NaOH + Na 2 SiO 3 | SiO 2 /Na 2 O = 0, 0.5, 1, C = 0.8, 1.0, 1.2, D = 0.35 | - | River sand (F.M. = 2.47) | - | 25 | 98 | SYS, DYS, EX, BU, W, IBS, drying shrinkage |
[131] | FA:GGBS:Brick waste (50:50:0, 40:50:10, 20:50:30, 0:50:50) | Anhydrous sodium metasilicate powder (Na 2 SiO 3 ) (10 wt.%) | SiO 2 /Na 2 O = 0.9, C = 1.5 | Sucrose powder as retarder (1 wt.%), nano-clay as a thixotropic modifier (0.5 wt.%) | F-sand D 50 = 172 μm, C-sand D 50 = 498 μm (1:2) | - | Covered with plastic film (24 h) + 60 for 24 h + ambient for 7, 28 days | - | SYS, DYS, W, V, ST, CST, IBS, BD, SEM |
[132] | GGBS:FA (50:50, 60:40, 70:30, 80:20, 90:10) | NaOH + Na 2 SiO 3 | SiO 2 /Na 2 O = 2.68, binder/aggregate = 1.5, B = 0.2, 0.3, 0.35, 0.4, D = 0.45 | - | C-sand (1.7 mm) b , M-sand (0.71 mm) b , F-sand (0.36 mm) b (1:1:1) | - |
Ambient
for 6 days sealed curing and then water bath curing |
- | SYS, UPV, BU, pumpability, CST, IBS |
[133] | GGBS:FA (100:0, 75:25, 50:50, 25:75) | NaOH + Na 2 SiO 3 | B = 1.65, D = 0.39 | Naphthalene based superplasticizer | River sand | - | 20 ± 3 | 70 ± 10 | EX, BU, CST, FS, split tensile strength, characterization of pore structure by XCT |
[134] | FA:GGBS (67:33) | Na 2 SiO 3 :NaOH = 2:1 | B = 0.4, C = 1.65 | Natural halloysite clay mineral (NH), calcined halloysite clay mineral (heating NH at 600°C for 1 h) | River sand (0-0.5 mm): (0.5-1.0 mm): quartz sand (0.06-0.3 mm) = (53:36:11) wt.% | - | 60 for 24 h, then at 20 ± 3 for 6 days | - | OT, EX, SRA, BU, CST, FS, material characterization using XRF, XRD, BET surface area, TGA/DTG, ATR FT-IR, SEM, |
a Average particle size, b Maximum particle size, D50 and D90 are defined as 50% and 90% of particles by weight are finer than respective diameters.
3.1. Aluminosilicate Precursors
As observed in Table 1, class-F low-calcium FA and GGBS are the most commonly chosen industrial wastes as the primary binder or precursor for 3DPGC due to their global availability. Since FA has adequate silica and alumina content and low water consumption, whereas GGBS is rich in CaO content, influencing setting time and strength, researchers have frequently used both in combination or as partial replacements for each other for 3DPGC. While in some studies, the replacement of FA from 5 to 15% with GGBS in the geopolymer mixture has a negative impact on the thixotropic open time of 3DPGC mixes [76], it was useful for setting up the time control important for 3D printing [68, 102]. The setting time increased, and flowability improved, but compressive strength was reduced by replacing GGBS with FA and SF [106]. GGBS has a minor impact on increasing the fresh property of the geopolymer pastes but a noticeable impact on the early-age compressive strength of 3DPGC [61].
In an investigation, the yield stress of 3DPGC was increased by 125% when 40% of FA was replaced with GGBS [66]. GGBS has revealed to reduce the setting time in the case of alkali-activated materials [135]. It can considerably affect the workability time (i.e., open time) by altering the flow characteristics.
Due to its higher thixotropy and poor activation reactivity, a rise in FA dosage led to enhanced mechanical anisotropy as a result of high pore content, worsened pore structure between printed layers, and lower mechanical strengths in a study on GGBS-FA-based 3DPGC [133]. To improve the 3D printing's associated rheology, the addition of FA (25 wt.%) or SF (10 wt.%) was found suitable and recommended for GGBS-based 3DPGC [129].
For optimum mix proportioning of extrusion-based 3DPGC mortars to fulfill the printability and hardened state essentials, a simple centroid design approach was devised by the authors [130], taking extrudability and buildability, interlayer bond strength, and drying shrinkage into account simultaneously. A study looked into a novel method for achieving an on-demand setting of 3DPGC through the mixing of precursor slurry with an activator at the print head, which enabled a longer pumping period since the non-activated mixture gets activated after it reaches the print head [132].
Researchers have also experimented with the addition of SF as a partial replacement to the 3DPGC blends and noticed that in the fresh stage, it successfully maximizes yield stress and enhances the thixotropic behavior and microstructure characteristics owing to its spherical shape and high surface area, which is desirable for 3D printing [80]. It allows for smooth extrusion of the blend, good shape preservation of the deposited filaments, and substantial recovery behavior. SF's smaller particle size causes increased particle packing in the 3DPGC mixes, lowering apparent viscosity and reducing extrudability [50].
Some research works have also examined the inclusion of metakaolin, steel slag, and brick waste as precursors for 3DPGC to study their influence on the rheological and structural properties of 3DPGC. The slump rate is not affected considerably by increasing the amount of reactive metakaolin and calcined argillite in metakaolin-based 3DPGC formulations [51]. In an investigation involving 3D printing of concrete-geopolymer hybrids [136], 95% concrete + 5% FA hybrids exhibited 20% greater compressive strength and 4% greater residual compressive strength (after fire resistance tests) than 95% concrete + 5% metakaolin specimens. Greater surface area, pore volume, and silica and alumina concentrations are identified in metakaolin, while FA has a greater pH, Si:Al ratio, calcium content, and water absorption [125].
The effect of steel slag [120] on 3DPGC’s flowability and setting time demonstrated a spread diameter of 197 mm for the control mortar mix (without steel slag), which increased from 218 mm to 235.5 mm with steel slag content (0-40%). Fresh geopolymer mortar with varying steel slag content was set faster than the control group. With the increase in steel slag content to 30%, both initial and final setting times increased and then dropped. Low specific surface area and large particle sizes reduced fluidity and water consumption. Steel slag's high CaO content increases alkalinity and speeds up raw material dissolution.
A group of researchers evaluated the effect of brick waste as a partial replacement of FA in 3DPGC and found that there was a 60-80% decrease, as compared to traditional OPC concrete, in the embodied energy and carbon footprint of the eco-friendly 3DPGC [131]. Increased setting time, higher loss of flowability, rise in static yield strength, and apparent viscosity were noticed with a rise in brick waste content owing to its less ball-bearing behavior and greater water absorptive nature in the 3DPGC mixture, which influences the extrusion-based 3D printing process [131]. Compressive and interlayer bond strengths increased up to 10% of optimum brick waste content and then decreased for content beyond optimum [131].
Thus, the selection of precursors and their proportions will evidently influence the printing process and final products.
3.2. Alkali Activators
As displayed in Table 1, sodium (Na) and potassium (K)-based alkaline activators are used in 3DPGC mixtures as they are easily available and economical. Comparing K-based activated 3DPGC to Na-based activated 3DPGC pointed out that the earlier had lower compressive strength [96, 114], a shorter open time, and a greater capacity to retain shape. The results of an optimization study on 3DPGC [114] revealed that the Na-based geopolymer combinations were more workable than K-based geopolymer mixtures, implying lower yield stresses. The yield stress rose when the K-activator concentration increased from 10% to 20% [66]. The viscosities of 3DPGC mortars were low under high shear forces, independent of activator and GGBS contents. A study [137] reported that yield stress of alkali-activated GGBS paste increases significantly with alkaline hydroxide activators, especially at larger doses, while yield stress of silicate-activated GGBS remains unaltered. The results provide a clear association between a faster reaction rate, solid product development, and increased yield stress. An improvement in strength occurred with a rise in activator concentration from 8 wt.% [108] to 10 wt.% [65], together with an acceptable setting time and workability, when anhydrous sodium metasilicate powder was used as an activator to 3D print a one-part geopolymer.
In a research on construction and demolition waste-based 3DPGC, a mixture with 6.25M NaOH and 10% was the best performing regarding rheology and compressive strength [86]. Na2SiO3 reduced viscosity and buildability but increased flowability and compressive strength [86]. While similar behavior was noticed in another study [119], the addition of Na2SiO3 induced quick hardening of less than 30 minutes, resulting in lowering of the open time for 3D printing. In contrast, the authors observed that for construction and demolition waste-based 3DPGC, there was a rise in compressive and flexural strengths while the bond strength reduced owing to a rise in viscosity when NaOH molarity and Ca(OH)2 utilization increased from 10 to 12.5M and beyond 4%, respectively [128].
3.3. Molar Compositions
The range of various molar compositions from Table 1 are: silicate to hydroxide ratio = 0-2.5; activator to binder ratio = 0.08-1.96; liquid to solid ratio = 0.14-0.65; SiO2/Na2O = 0.34-5.26; SiO2/K2O = 1.56-2.02; SiO2/Al2O3 = 2-4.42; Si/Na = 0.5-1.0; Na2O/Al2O3 = 0.69-0.86; and H2O/Na2O = 22.38-42.20.
A slower geo-polymerization process and longer setting time are caused by decreased SiO2/M2O (M = Na or K) ratios and greater silicate/activator ratios [96]. Additionally, compressive strength rises as the silicate/ activator ratio is raised [96, 114]. A lower molar ratio fastens the reaction with a binder, minimizes the setting time, and shortens the open time [97]. The higher activator/binder ratio leads to a longer setting time for FA-based 3DPGC [85]. Moreover, the increase in molar ratio results in a decrease in interface bond strength. The findings from a study on FA-GGBS-based 3DPGC [130] indicated expedited growth in buildability and a decline in extrudability, along with a reduction in shrinkage and interlayer bond strength, by employing a lesser silicate modulus of activator. As a result of the increased silicate viscosity at molar ratio 2, yield stress and geopolymer viscosity are also higher, leading to superior shape retention and an improved ability to recover (36% higher) in comparison to the paste made at molar ratio 1.8 at a constant solution-to-binder ratio [101].
In the 3DPGC sample with an 8 wt.% activator, increasing the w/s ratio from 0.31 to 0.35 decreased yield stress, but increasing the activator dose resulted in a quick reaction and a faster rate of yield stress rise [104]. For metakaolin-based 3DPGC formulations, the reduction in the liquid-to-solids ratio decreases the slump rate [51].
The authors used the rheology approach to examine the structure rebuilding and yield stress of 3DPGC pastes at various Si/Na alkali activator ratios [105]. Specific Rebuilding Energy (SRE) was employed to assess the rebuilding that happened in the fresh paste and to evaluate the ability and speed of structure rebuilding by printing concrete materials. The value of SRE steadily rose with rest time for 3DPGC.
Solid NaOH activators pre-mixed with dry components showed quick yield strength development even at lower activator dosages but inferior hardened mechanical characteristics than liquid activators [122].
Since the metakaolin particles have a lower capillary effect compared to FA particles, the setting time was prolonged by 25% and 40% as the liquid-to-solids ratio increased, as presented in Table 1, for metakaolin and FA-based 3DPGC mixtures, respectively [125].
3.4. Additives
Additives such as sodium carboxymethyl cellulose (CMC), anhydrous borax, nano-clay, actigel, bentonite clay, cellulose, nanographene platelets, fine limestone, alumina, defoamer, superplasticizer, re-dispersible latex, raw argillite, kaolin, sucrose powder, sodium carboxymethyl starch (CMS), and halloysite have been incorporated in 3DPGC, as listed in Table 1, to tailor its rheological and structural properties.
The ratio of silicate to hydroxide solutions increases the amount of CMC added to 3DPGC, regardless of the activator used [96]. This is consistent with the fact that a hydroxide solution is less viscous than a silicate solution. A reduction in the amount of CMC powder utilized as a Viscosity-Modifying Admixture (VMA) resulted in increased workability, decreased static yield stress, and a consequent reduction in shape retention ability [77, 137, 138]. No obstruction, ripping, segregation, or bleeding were seen during the extrusion of any of the combinations, indicating that the characteristics studied had no impact on extrudability of 3DPGC samples since the dosage of admixtures (CMC as a viscosity modifying agent and anhydrous borax as a retarder) was regulated in each combination to get beneficial rheological qualities [114]. Findings of a study [132] displayed that polycarboxylic ether-based super-plasticizer can be effectively employed to enhance rheological and mechanical properties of set-on-demand 3DPGC by influencing the apparent viscosity and static yield strength at lower water content.
Nano-clay (highly purified attapulgite clay) is used in 3DPGC to enhance thixotropy of the mix through colloidal interaction [76]. The flocculation feature of the clay particles increases rheological parameters such as yield stress [101]. Even in the presence of nano-clay, yield stress and viscosity decrease as the activator dosage increases. Nano-clay has a minor effect on the initial setting time, and it proves ineffective in speeding the rate of strength development.
A group of researchers conducted an investigation [139] on the influence of incorporating additives (attapulgite nano-clay with dosages of 0.5 wt.% and 1 wt.% and PVA fibers with dosages of 0.25 wt.% and 0.5 wt.%) in 3D printable alkali-activated mixtures containing 60, 25, and 15 wt.% of FA, GGBS, and SF content, respectively. As the nano-clay particles undergo good dispersion and due to the crack-bridging phenomenon exhibited by the fibers in the mixture, the 3DPGC's mechanical performance, shape preservation, and buildability improve immensely, as are also evident from the excellent microstructural characteristics and lowest pore anisotropy [139]. Adding 0.4% nano-clay to the mixes alleviated early yield stress owing to flocculation [117]. FA-based 3DPGC with GGBS and SF that was thickened by the addition of nanographene platelets was less workable when 0.3% and 1% nanographene platelets were added; however, the lubrication effect of nano graphite platelets overtook the thickening effect on adding 0.1% and 0.5% nanographene platelets, and the workability increased compared to the plain mix without nanographene platelets [106].
The material design was focused on assessing [140] a ternary blended 3DPGC containing FA, fine limestone, GGBS, or OPC, and alumina powder for extrusion-based 3D printing. Rheology modifiers such as actigel and bentonite clay were used to boost pumpability of 3DPGC [79]. Actigel and cellulose are also incorporated as thixotropic additives to achieve a zero slump in 3DPGC [60]. The increase in surfactant dosage enabled excellent buildability and viscosity recovery of 3DPGC due to its low density and viscosity, although yield stress dropped [124]. Increased sucrose powder concentration in 3DPGC resulted in delayed yield strength development, inferior buildability with a drop in elastic modulus, and viscosity recovery of 30.8% and 15.6%, respectively, but its influence on dynamic viscosity was negligible [113].
CMS modifies rheology by interweaving water-soluble gel and immobilizing water [116]. CMS is physically-chemically congruent with alkali-activated GGBS and can efficaciously customize its rheology at a sizable numerical scale with a reduced dose, making it an additive with potential enhancing workability for 3D printing to avoid sagging, segregating, or bleeding issues [116].
Biomass flocs, which do not mix with the distributed aluminosilicate particles in 3DPGC mixes, actually inhibit the geopolymer gel interactions, reducing yield stress in any scenario (spirulina, tetraselmis, and lignin) [118]. As a result, the coagulated structures lose some of their resistance, which reduces yield stress, further improving printability and lowering buildability. Therefore, microalgal biomasses can be employed as biofillers [118].
In an investigation, the authors found that the setting time of 3DPGC decreased with a rise in thermally treated meta-halloysite (calcined at 800 °C) due to high reactivity as compared to a negligible change in setting time for varying contents of less reactive thermally untreated reactive halloysite in 3DPGC [126]. In a previous study [134], enhanced printability, buildability (45 layers of twisted column printing), and compressive and flexural strengths (40% and 88%, respectively) were achieved with the inclusion of 1.5 wt.% of calcined halloysite clay mineral as a rheology modifier and reinforcement into 3DPGC, as compared to control printed specimens.
3.5. Aggregates
While the use of coarse aggregates hinders the extrusion process, fine aggregates, such as river sand and silica sand, are commonly utilized in 3DPGC, and the maximum size of sand particles is governed by the pump's pumping capability and nozzle size [79]. Sand having a maximum particle size of 2 mm and aggregate-to-binder ratios varying from 0.55 to 2.0 has been used for most studies on 3DPGC, as demonstrated in Table 1. The incremental addition of sand from 1.1 to 1.9 (aggregate to binder) ratio has illustrated to develop a high static yield stress, owing to which the geopolymer mixes were not extrudable and produced clogging at the outlet, despite the addition of additional water [76]. River sand consisting of 60% of grade 0–0.5 mm and 40% of grade 0.5–1 mm size particles was utilized in the 3DPGC mixture, which exhibited excellent shape retention and buildability by printing 25 layers (30 cm) [106]. Moreover, good cohesiveness and reduced flowability of the mix were obtained. Also, higher yield shear stress and plastic viscosity were noticed. The just-add-water 3DPGC mixture's [65] excellent extrudability and buildability were due to the constant gradation of the three sand kinds achieved by the Fuller Thompson theory. The efficient printing of the 940 mm tall column [65] displayed the optimum mixture's superior buildability over the previously produced printable one-part geopolymer, which had a buildability of up to 300 mm [66].
The recycled finely crushed aggregates used in 3DPGC with construction and demolition waste in the absence of admixture enhanced the viscosity of the mix without adversely affecting its strength [119]. In this case, the attached cement, which has hardened due to aging, may act as a silicon/calcium source during depolymerization, leading to a strong bond between the fresh binding material and old aggregates. An increase in the content of aggregates enhances the mixture’s yield stress and viscosity. Binder paste composition controls the structural buildup and thixotropy [123].
3.6. Curing Conditions
The curing conditions, i.e., curing temperature and relative humidity, along with curing time duration, affect the properties of 3DPGC. As observed from Table 1, the curing temperature varies from ambient to 75 °C, whereas the relative humidity ranges from 40% to 95%. For 3DPGC, usually heat curing is conducted for a maximum of 24 h, while ambient curing may vary from 7 days to 28 days until the day of testing. Moreover, after casting, the 3DPGC specimens are sealed using plastic bags, sheets or containers to prevent excessive moisture loss. Due to the pores getting filled with the reaction products developed by the extended curing periods of 3DPGC, the mechanical anisotropy reduces [133].
Geopolymer strength does not alter appreciably over time following heat curing, as previously described in the literature [140-143]. While heat curing is known to improve the mechanical properties of FA-based two-part geopolymers, the one-part geopolymers can provide good mechanical behavior at ambient temperature curing, depending on the geopolymerization reaction mechanism. The printed layers using metakaolin-based 3DPGC adhere well to one another under temperature (14-20 °C) and relative humidity conditions (43-63%) [51], also indicating the relation between the consolidation of printed material and time. In a study on just-add-water 3DPGC [111], heat curing (for 24 h at 60 °C) resulted in a considerably more significant loss (63%) in bond strength of the samples between layers printed with the more extended open period of 15 min when compared to samples cured at room temperature for 28 days (25%). While heat curing leads to the flexural strength enhancement of 3DPGC mixtures containing limestone, the trend is reversed in 3DPGC mixtures containing GGBS [140], which give greater shrinkage, resulting in tremendous microcracking [144, 145]. The ambient temperature curing method is especially advantageous in gaining excellent mechanical properties and reducing the expense and environmental implications associated with the heat curing method. In a research attempt [146], a unique circuit system was employed to obtain the regulated instant heating potential of steel cable reinforcement, thus ensuring stronger structural integrity of the printed component while also improving buildability.
In this section of the review, several key findings can be observed. Class-F low-calcium FA and GGBS are prominent choices as primary binders owing to their global availability. The combination or partial replacement of these materials significantly influences properties of 3DPGC, including setting time, flowability, and compressive strength. Research shows that the replacement of FA with GGBS in geopolymer mixtures impacts thixotropic open time, with potential advantages for 3D printing time control. However, this replacement may lead to decreased compressive strength. GGBS demonstrates a notable influence on early-age compressive strength, emphasizing its role in the fresh properties of geopolymer pastes.
Further investigations revealed the complex interplay between aluminosilicate precursor ratios. Optimal mix proportioning considers extrudability, buildability, interlayer bond strength, and drying shrinkage simultaneously. Novel methods, such as on-demand setting through precursor slurry mixing at the print head, showcase the evolving strategies for improving 3DPGC rheology. SF emerges as a valuable addition, enhancing yield stress and thixotropic behavior owing to its unique properties. The particle size of additives like SF impacts extrudability, with smaller sizes favoring improved particle packing and reduced apparent viscosity. The inclusion of metakaolin, steel slag, and brick waste as precursors diversely affects rheological and structural properties. These alternative materials contribute to the eco-friendliness of 3DPGC, depicting the potential for sustainable construction practices.
Focusing on alkali activators, the choice between sodium (Na) and potassium (K) considerably influences compressive strength, open time, and shape retention. The molar compositions of 3DPGC play a crucial role in geo-polymerization processes, affecting setting time, open time, and compressive strength. Lower silicate/activator ratios expedite reactions, reducing setting time and open time, while higher ratios enhance compressive strength.
The incorporation of additives serves to tailor rheological and structural properties. CMC, nano-clay, and other additives influence viscosity, yield stress, and extrudability. The careful selection and dosage of additives are pivotal in achieving desirable 3DPGC characteristics.
Fine aggregates, such as river sand and silica sand, are preferred over coarse aggregates to facilitate the extrusion process. Their particle size and ratio to binder impact static yield stress, buildability, and shape retention.
Curing conditions, including temperature, humidity, and duration, remarkably influence the final properties of 3DPGC. The choice between heat curing and ambient curing affects mechanical properties, with considerations for bond strength and microcracking.
In conclusion, the comprehensive analysis of aluminosilicate precursors, alkali activators, molar compositions, additives, aggregates, and curing conditions provides valuable insights into optimizing 3DPGC formulations for enhanced printability and hardened state properties. The diverse range of materials and parameters explored in this review contributes to the evolving understanding of 3DPGC technology for sustainable and efficient construction practices.
4. MIXING REGIME FOR PREPARATION OF 3DPGC
The presented data in Table 2 outline various mixing regimes for the preparation of geopolymer mixtures for 3DPGC, as reported in the literature. The analysis illustrates a diverse range of methodologies, including both one-part and two-part mixing approaches, with distinct stages and equipment usage. For two-part geopolymers, mixing durations and sequences vary across studies, with dry mixing of binders and aggregates being a common initial step. The addition of fibers, thixotropic modifiers, and activators is often a gradual process to ensure uniform dispersion.
Notably, the hobart mixer and planetary mixer are frequently employed for two-part mixing, each contributing to specific advantages such as improved extrusion rheology or prevention of fiber bundles. In one-part geopolymers, water is introduced along with thixotropic thickeners, and the mix is stirred at varying speeds for optimal dispersion. The use of Hobart mixers in the case of one-part geopolymers is prominent, ensuring thorough mixing of binders, aggregates, activators, and additives.
In certain instances, a resting period is introduced after the initial mixing stages to improve workability. Quality control is emphasized through separate mixing regimes for each stage, enhancing the overall uniformity of 3DPGC. Challenges, such as a drop in workability during mixing stages, are addressed with specific solutions, such as halting stirring to clean the mixer. The use of additives like VMA is highlighted for improving extrusion rheology, emphasizing the importance of careful admixture incorporation.
Attempting to apply the multi-level material design [147] to 3DPGC suggests that rheology is primarily influenced by the nature of the precursors and admixtures used, which will affect pumpability and buildability and, eventually, the structural characteristics of 3DPGC. Incomplete mixing or a shorter mixing duration required may result in unreacted ingredient particles in the mix, affecting the pore structure, rheology, and mechanical properties of 3DPGC. It is vital to avoid agglomeration and confirm the uniform distribution of fibers when used in 3DPGC since it can result in choking or blockage at the print head, the formation of cold joints, or adversely affect flexural and inter-layer bond strengths. Typical mixing regimes adopted for the preparation of geopolymer mixtures (one-part and two-part) for 3DPGC are presented in Table 2. The binders are usually mixed dry to give a homogeneous mix. The addition of fibers and aggregates is done either before or after the addition of water to the mix. The time of mixing of ingredients also varies in different studies.
The diverse mixing regimes in Table 2 indicate the adaptability of geopolymer mixtures for 3DPGC to different methodologies. The choice of mixing equipment, sequence, and duration play pivotal roles in achieving optimal rheological properties, preventing issues like fiber agglomeration, and ensuring uniform distribution of additives. This comprehensive review underscores the importance of tailoring mixing regimes to specific requirements, contributing to the broader understanding and advancement of 3DPGC.
Ref. | One-part/Two-part | Mixing Regime for 3DPGC | Remarks | |||
---|---|---|---|---|---|---|
Stage-1 | Stage-2 | Stage-3 | Stage-4 | |||
[106, 139] | Two-part | All binders and aggregates were mixed dry at 250 RPM for 2 min. | Additives (fibers and thixotropic modifier) were added slowly and were mixed dry at 250 RPM for 2 min. | Alkali activators were mixed for 5 min at 700 RPM and then added to dry mix and mixed at 250 RPM for 2.5 min, accompanied by stirring at 450 RPM. | - | A planetary mixer was used. Aggregates and additives were added initially to the dry mix before the addition of alkali activators. |
[114] | Two-part | Binders, aggregates, and retarders were mixed dry for 3 min at low speed. | 7 min mixing was done after adding activator solutions to the dry mix. | After obtaining a uniform mixture, VMA was added, and mixing was carried out for 5 min. | - | Hobart mixer was utilized. Extrusion rheology can be improved by adding VMA after retarder has been mixed. |
[77, 148] | Two-part | Binder and aggregates were mixed dry for 1 min at low speed. | Add alkaline solution and mix for 4 min. | To confirm uniform dispersion of fibers, gradually add fibers to the mixture. | After obtaining a uniform mixture, VMA was added, and mixing was done for 2 min. | Hobart mixer was employed. Fibers were not added initially to the dry mix. No fiber bundles or segregation was observed during mixing. |
[60] | Two-part | All binders were mixed dry for 2-3 min at low speed, accompanied by inclusion of thixotropic additives. | Add alkaline solution and mix at medium speed for 1 min. | Aggregates were poured and mixed for 1-2 min. | To achieve proper workability, little water was added. | Hobart planetary mixer was used. Aggregates were not added initially to the dry mix. |
[75] | Two-part | Binders, aggregates, and reinforcing elements were mixed dry for 2 min. | Add activator solution and mix for 3 min. | - | - | Auto-mortar mixer was utilized. Aggregates and reinforcing elements were added initially to the dry mix before the addition of alkali activators. The same mixing regime was separately followed for each layer to enhance quality control. |
[99] | Two-part | All binders were mixed dry at minimum speed for 2 min. | Add activator solution and mix for 2 min. | Allow the mixture to rest for 30 seconds. | Aggregates were poured and mixed at maximum speed for 1 min. To achieve proper workability, little water was added. | Hobart mixer was used. Aggregates were not added initially to the dry mix. |
[126] | Two-part | The binder and aggregates were mixed dry for 30 seconds. | Additives were added to the dry mixture gradually. | Add activator solution and mix for 5 min. | - | An electric mixture was utilized. Aggregates were added initially to obtain the dry mix. |
[149] | Two-part | The binder and aggregates were blended dry for 3 min at 50 RPM. | Activator solution was mixed with already prepared sucrose (retarder) solution and added to the dry mix. 90% of the total water was added and mixed for 8 min. | The remaining 10% mixed solution was added gradually and mixed. | - | A horizontal mixer was used. The total mixing duration was 15 min. |
[132] | Two-part | Binder and aggregates mixed dry for 60s at 60 RPM. | Add the required amount of water slowly and mix at the same speed varying from 1 to 29 min as per demand. | Add activator solution slowly for 30 seconds while operating the mixer at 124 RPM. | - | The precursor slurry was activated in-line before extrusion by mixing activators at the print head. |
[50] | One-part | Add water to the thixotropic thickener and mix them properly. | Binders, aggregates, and activator were mixed dry for 1 min at low speed. | Add thixotropic thickener solution and stir at slow speed for 1 min. | Stir the mix at high speed for 2-3 min. | Full dispersion of the admixture was ensured through high-speed stirring of the mix. |
[68] | One-part | Binders, aggregates, and activator were mixed dry for 5 min. | Add water and mix for 3 min. | - | - | - |
[108] | One-part | Binders, aggregates, and activator were mixed dry for 2 min. | Add water and mix for 10 min. | - | - | Hobart mixer was used. |
[110] | One-part | Binders, aggregates, solid activator, and retarder were mixed dry for 3 min. | Add water and mix thoroughly for 12 min. | Add fibers and mix for 12 min. | VMA was added and mixing was performed for 5 min. | Hobart mixer was utilized. Extrusion rheology can be improved by adding VMA after the retarder has been mixed in. Fibers were not added initially to the dry mix. |
[112] | One-part | Binders, aggregates, solid activator, retarder, and fibers were mixed dry for 3 min. | Slowly add water and mix for 10 min. | - | - | Hobart mixer was employed. Retarder and fibers were added initially to the dry mix before the addition of water. |
[65] | One-part | Binders, aggregates, solid activator, and retarder were mixed dry for 3 min at slow speed. | Gradually add water and mix for 3 min at a slow speed. | Stir the mixture for 7 min at high speed. | - | Hobart mixer was used. Thorough mixing of all the ingredients was ensured by stirring the mixture at high speed. |
[113] | One-part | Binders, aggregates, solid activator, retarder, and thixotropic additive were mixed dry at 61 RPM for 90 seconds. | Water to be mixed was poured in two steps. In step 1, it was slowly added and stirred for 15 min. Stirring was halted for 30 seconds in between, to clean the mixer to improve mixing capacity. Moreover, to confirm homogeneous distribution after the addition of water, mixing was done for 4, 9, and 14 min at 113 RPM. | After 10 min of stirring in stage 2, workability of the mix dropped drastically. Workability was regained when the remaining water was mixed in step 2. | - | Hobart mixer was utilized. The solid activator could only be dissolved entirely after 15 min of mixing. |
5. INFLUENCE OF REINFORCING ELEMENTS ON 3DPGC
According to Table 3, fiber insertion has a considerable effect on flexural, tensile, and interlayer bond strengths, although its effect on compressive strength is less pronounced due to the intrinsic anisotropy of 3DPGC specimens. Introducing fibers (hooked-end steel 1%, PP 0.5%) during stacking can modify bond strength [75]. The layer matrix may not be the same for fiber distribution in paste. An uneven surface may prevent layer adhesion, especially if steel fibers are utilized, which is not encouraged [75]. The maximum strength in the perpendicular direction increased from 22 MPa to 36 MPa when the volume of PP fibers was increased from 0% to 0.25 vol.% [77]. Because of the higher porosity and stiffness of the mix [149-151], the compressive and inter-layer bond strengths decreased beyond 0.25% fiber addition. Using 0.25% fibers increased flexural strength by 17-34%, but lowered interlayer bond strength because of the tightening of the matrix [16]. During flexural tests, the bottom layer failed in tension, not in shear [16]. Longitudinal orientation had the highest mean compressive strength, followed by perpendicular and lateral. PVA fibers caused the least loss in interlayer bond strength, while PBO fibers improved flexural strength. Using the three-point bending test, the 15 N/mm2 strength in flexure showed a suitable printing speed, good layer adhesion, and fiber alignment, which offset the detrimental effect of voids [51]. The 3D-printed samples had fibers oriented along the print direction [110, 152]. Fibers only helped fracture bridging [153] in lateral and perpendicular directions, not longitudinal (along the printing path). 3DPGC compression strength was anisotropic based on loading direction, irrespective of layer count. The number of printed layers affects the flexural behavior of 3D-printed specimens in four-point bending tests [110]. Two-layered specimens demonstrated increased first crack strength and rupture modulus. One-layered specimens have a higher deflection capacity than two-layered specimens [110].
In 3D printing, fresh concrete is subject to shrinkage cracking since no formwork is used. Microwave heating can promote hydration (self-desiccation) and moisture loss, leading to crack formation [115]. To preserve mechanical performance and durability, 1% micro PVA fibers (6 mm long, 26 μm diameter) are employed. Fibers affect 3DPGC's porosity and shrinkage [32]. The inclusion of fibers in the mix was assumed to have reduced micropores [98]. An FA-based geopolymer mix with 0.25% 4 mm-long microglass fibers reduced shrinkage and distortion in the plastic state in a similar way [76]. As the nano-clay particles dispersed and the fibers bridged cracks, the mixture's mechanical performance, shape retention, and buildability increased greatly, as evidenced by its outstanding microstructural properties and lowest pores anisotropy [139].
Ref. | Reinforcing Element | Content | Length (mm) | Diameter (μm) | Highlights | |
---|---|---|---|---|---|---|
[16] | PVA fibers | 0.25% vol | 6 | 26 | CS = 18.4 to 27.7 MPa, FS = 9.0 to 10.3 MPa, IBS = 2.33 to 2.58 MPa. | |
PP fibers | 11.2 | |||||
PBO fibers | 12 | |||||
[77] | PP fibers | 0%, 0.25%, 0.5%, 0.75%, and 1% vol. | 6 | 11.2 | Spread diameter = 134-158 mm, AP = 10.1-14.1%; CS = 22-36 MPa. | |
[98] | Chopped glass fibers | 0.25%, 0.5%, 0.75%, and 1% | 3, 6, and 8 | - | TS = 1.5 MPa for 3 mm fiber, FS = 7 MPa for 8 mm fiber. | |
[76] | Micro glass fibers | 0.25 wt.% | 4 | - | BU - 60 cm tall free form structure was printed having a width 35 cm and comprising of 60 layers of 10 mm thickness, YS = 0.6-1.0 kPa. | |
[79] | Alkali-resistant glass fibers | 0.5% | 6 | - | Static YS = 13522-17401 N/m2, Dynamic YS = 2991-3622 N/m2, Plastic viscosity = 113-186 Ns/m2; CS = 36 MPa-57 MPa. | |
[67] | PVA fibers | 0.5 wt.% (hybrid reinforcement) | 8 | 1.4 | FS improved by up to 290%. | |
Stainless steel cable | 1000, 1500, and 2000 | |||||
[68] | Steel | Each layer has only one cable entrained. | - | 1200 | Micro-cables enhanced TS and strain by 158% and 43.8%, respectively, with adhesive bond strength = 3.34-4.00 MPa and ultimate bond strength = 4.03-4.79 MPa. | |
Nylon | 1300 | |||||
Carbon | 1400 | |||||
Aramid | 800 × 1200 | |||||
Polyethylene | 1200 | |||||
[102] | PP fibers | 0.56 wt.% (composite reinforcement) | - | - | For mold-casted samples, density = 2.2 g/cm3, TS = 2.84 MPa, CS = 40.5 MPa. | |
Stainless steel micro cable | 1200 | |||||
[103] | Carbon fibers | 1% (by mass) | 5 | 8 | Density at 28 days = 1.62 g/cm3 (without fibers), 1.48 g/cm3 (flax), 1.58 g/cm3 (carbon). | |
Green tow flax fibers | 30-50 | - | ||||
[112] | Wollastonite micro-fibers | Fine sand was partially replaced (10%). | Average aspect ratio = 19:1 | CS = 49.1 MPa, FS = 12.0 MPa. | ||
[121] | Wollastonite micro-fibers | Fine sand was partially replaced (5%, 10%, 15%, 20%, and 30%). | Average aspect ratio = 19:1 | Optimum volume = 10%; EX - 300 mm square slab having 5 layers with layer height = 10 mm, length of layer = 4810 mm; BU – 200 mm × 300 mm column comprising 23 layers; CS decreased 3-10%, FS increased 20-54%. | ||
[75] | Hooked-end steel fibers | 1% | 40 | 615 | Reduction in workability by 4% and 33% while increase in FS by 20% and 3% with steel and PP fibers addition, respectively. | |
PP fibers | 0.5% | 5 | 22 | |||
[110] | Oil-coated PVA fibers | 2% | 8 | 40 | Bulk density = 1500 kg/m3, apparent porosity = 28%, CS = 25.1-49.8 MPa, rupture modulus = 8.6-10.2 MPa, deflection capacity = 2.9-5.3 mm. | |
[51] | Wollastonite fibers | - | - | - | FS = 15 MPa. | |
Glass fibers | ||||||
[127] | Kenaf straw core | 0 and 1.5 wt.% | - | 10-20 mesh | - A decrease of 10.1% in dry density was observed with an increase in the amount of kenaf straw core from 0% to 1.5%. - As compared to reference samples, a rise of 67.63% in thickness shape retention and 189.19% in viscosity recovery was witnessed by a combination of kenaf straw core and kenaf fibers in 3DPGC, along with a 68% reduction in setting time and good bending resistance. - Kenaf fibers and kenaf straw core were responsible for the bridging mechanism and skeleton role, respectively, resulting in crack control and improved shape stability. |
|
Kenaf fibers | 0 and 0.2 wt.% | 15 | - | |||
[154] | Short carbon fibers | 1, 2, 3, 4, 5, and 6 wt.% | 600 μm | 5.7 (thick) | - YS enhanced by 63% to 601.8% with rising fiber proportion from 0 to 6 wt.% respectively. - At 3 wt.% fiber content, CS and FS were 375.8% and 309.2% greater respectively, compared to non-reinforced 3DPGC. - Achieved lightweight 3DPGC composites with excellent BU, shape retention, and high toughness. |
A previous study [103] examined two production procedures (cast and injected samples—3D printing simulations), curing duration (7 and 28 days), and composites (short fiber-reinforced geopolymers and plain samples). Flax fiber injection specimens illustrated maximum flexural strength after 28 days, up to 36% higher than casting specimens [103]. Due to the high dose, carbon fiber specimens' flexural strength was not improved. Flax-fibered specimens outperformed carbon-fibered ones [103]. Reinforcement was inserted into the geopolymer matrix using a method that allowed steel cable to enter the extruded filament seamlessly [67]. 8 mm PVA fibers were utilized in the matrix to create interlocking between the fibers and prevent cable slippage. In the early stages of tensile stress, short fibers can bridge microcracks; however, in the latter stages of crack propagation, longer fibers begin to function. The hybrid reinforcement technique increased geopolymer composites' flexibility by up to 290% relative to the control specimen. The first fracture load and fracture toughness of hybrid reinforced geopolymer composite specimens reinforced with cable increase as the diameter of the steel cable increases [67]. Two incline-crossed and concentric path printing setups were employed to make the samples [102]. Each filament has a micro cable in the center. The use of PP fibers prevents shrinking [154, 155]. An 8-fold and a 70-fold increase in flexural strength and deflection resistance over unreinforced geopolymer composites were found in the incline-crossing printing configuration [102]. The strength of micro-cables under a variety of loading conditions was evaluated using both continuous and simultaneous strengthening approaches [68]. 7 shares and 19 strands per share comprised the micro-cables. The specimens were created using a concentric route and two crosshatch zigzag designs. A pull-out test was utilized to assess the bonding properties. The tensile behavior was mostly a result of the cable reinforcing designs.
In summary, the meticulous exploration of reinforcing elements in 3DPGC underscores the critical interplay between fiber incorporation and material performance. Key findings highlight the significant influence of fibers on flexural, tensile, and interlayer bond strengths. Notably, the anisotropic nature of 3DPGC, coupled with the intricate relationship between fiber volume and mechanical properties, highlights the need for precise engineering in material design. Optimizing the volume of PP fibers showcases a substantial increase in perpendicular strength, yet careful consideration is required to avoid compromising compressive and interlayer bond strengths beyond a certain threshold. The effects of different fiber types, such as the minimal loss in interlayer bond strength with PVA fibers and improved flexural strength with PBO fibers, emphasize the importance of tailored material selection. The exploration extends to the realm of micro-reinforcement strategies, introducing hybrid approaches with steel cables and varied fiber lengths. This innovation improves flexibility and fracture toughness, paving the way for advanced applications in construction. The intricate balance between short and long fibers in tension stages highlights the dynamic nature of the reinforcing mechanisms at play.
Furthermore, the study delves into the challenges associated with porosity, decreased interlayer bond strength, and workability degradation in the presence of fibers. Flexural strength increases with fiber incorporation over 0.25%, but workability of the mix degrades due to porosity and decreased interlayer bond strength. Further, different fiber types have different effects on workability of the mix. To improve the micro-reinforcement impact, specific pretreatment measures are required. As a result, polymer-based cables should be studied to increase corrosion resistance in comparison to steel cables.
In conclusion, this section not only contributes to the nuanced understanding of 3DPGC behavior under diverse reinforcing elements but also charts a course for future advancements. The delicate optimization of material composition, coupled with innovative reinforcement strategies, propels the scientific community toward the development of 3DPGC with enhanced precision, durability, and application versatility.
Ref. | Geopolymer Component | Material Composition | W | YS | V | ST | T | SR | PQ | BU | P | CS | FS | IBS |
---|---|---|---|---|---|---|---|---|---|---|---|---|---|---|
[80, 140] | Aluminosilicate precursors | FA | ↑ | ↓ | ↓ | ↑ | - | - | - | ↓ | - | - | - | - |
[61, 66] | GGBS | ↓ | ↑ | ↓ | ↓ | ↑ | - | - | - | - | ↑ | - | - | |
[50, 80] | SF | ↓ | ↑ | ↓ | - | ↑ | ↑ | ↑ | ↑ | - | ↑ | - | - | |
[51, 125] | Metakaolin | ↓ | - | - | ↓ | ↑ | ↑ | - | - | - | - | - | - | |
[66, 96, 114] | Alkali activators and molar compositions | Na-based activator | ↑ | ↓ | - | - | - | ↓ | - | - | - | ↑ | - | - |
K-based activator | ↓ | ↑ | - | - | - | ↑ | - | - | - | ↓ | - | - | ||
[96, 97, 114, 130] | SiO 2 /M 2 O (M = Na or K) | - | ↑ | ↑ | ↓ | - | ↑ | - | - | - | ↓ | - | ↓ | |
[105] | Silicate/activator ratio | - | - | - | ↑ | - | - | - | - | - | ↑ | - | - | |
[85, 101] | Solution/binder ratio | - | ↓ | ↓ | - | - | - | - | - | - | - | - | - | |
[51, 104, 125] | Liquid/solid ratio | ↑ | ↓ | - | - | - | - | - | - | - | - | - | - | |
[104] | Activator content | - | ↓ | - | ↑ | - | - | - | - | - | ↑ | - | - | |
[76, 101, 117, 139] | Additives | Nano attapulgite clay | ↓ | ↑ | ↑ | - | ↑ | ↑ | - | ↑ | ↓ | ↑ | ↑ | - |
[60, 79] | Actigel | ↓ | - | - | - | ↑ | - | - | - | - | - | - | - | |
[60] | Cellulose | ↓ | - | - | - | ↑ | - | - | - | - | - | - | - | |
[79] | Bentonite clay | ↓ | - | - | - | ↑ | - | - | - | - | - | - | - | |
[106] | Nano graphite platelets | ↓ | - | - | - | - | ↑ | - | ↑ | - | - | ↑ | - | |
[77, 114, 138] | VMA | ↓ | ↑ | ↑ | ↓ | ↑ | ↑ | - | - | - | - | - | - | |
[140] | Fine limestone | - | - | - | - | - | ↑ | - | ↑ | - | - | - | - | |
[140] | Alumina powder | - | - | - | ↑ | - | - | - | - | - | - | - | - | |
[78, 116] | Sodium carboxymethyl starch | ↓ | ↑ | ↑ | ↑ | - | ↑ | - | ↑ | ↑ | ↓ | ↓ | - | |
[113] | Sucrose powder | ↑ | ↓ | - | ↑ | - | - | - | ↓ | - | - | - | - | |
[118] | Microalgal biomass | - | ↓ | - | - | - | - | - | ↓ | - | - | - | - | |
[126, 134] | Calcined halloysite clay mineral | - | - | - | ↓ | - | - | - | ↑ | ↑ | ↑ | ↑ | - | |
[76, 130] | Aggregates | Aggregate/binder ratio | ↓ | ↑ | ↑ | - | - | ↑ | ↓ | ↑ | - | - | - | ↑ |
[65, 106] | Aggregate size | ↑ | - | - | - | - | ↓ | ↓ | ↓ | ↑ | ↑ | - | - | |
[68, 75, 121, 154] | Reinforcing elements | Fibers and steel micro-cables | ↓ | ↑ | - | - | - | ↑ | ↓ | ↑ | ↓ | - | ↑ | ↑ |
The impact of geopolymer material composition and mix design on the rheological and structural behaviors of 3DPGC, as discussed comprehensively in Section 4, is summarized in Table 4.
The comprehensive analysis presented in Table 4 illuminates the intricate relationship between geopolymer material composition, mix design, and resulting rheological and structural properties of 3DPGC. Key insights can be gleaned from the summarized influence of various components on properties crucial for successful 3D printing.
Components such as FA, GGBS, and metakaolin exhibit varying impacts on workability, yield stress, and viscosity. FA enhances workability but decreases yield stress, while GGBS and metakaolin show contrasting effects. Alkali activators, including Na-based and K-based activators, play a crucial role, with sodium-based activators generally improving workability and compressive strength, but potassium-based activators enhance yield stress and shape retention. SiO2/M2O (M = Na or K) considerably influences multiple properties, contributing to improved yield stress, viscosity, and shape retention. The aggregate-to-binder ratio and aggregate size impacts properties like workability, yield stress, and porosity, with a careful balance required for optimal performance.
Various additives, including nano-clay, actigel, cellulose, and nanographene platelets, display distinct effects on thixotropy, print quality, and yield stress. The introduction of fibers and steel micro-cables influences multiple parameters, with a general trend toward improving yield stress, compressive strength, and buildability, while impacting workability and print quality.
The findings underscore the delicate balance needed in geopolymer composition for 3DPGC, with different components contributing synergistically or adversely to specific properties. SiO2/M2O (M = Na or K) emerges as a critical parameter influencing both rheological and structural aspects, highlighting the need for precise control over alkali activator composition. The study lays the foundation for tailored geopolymer formulations, enabling the optimization of workability, structural strength, and print quality in 3DPGC. In conclusion, this systematic exploration not only advances our understanding of the intricate interplay within geopolymer compositions but also provides a scientific roadmap for formulating 3DPGC with superior performance characteristics. The nuanced insights garnered from this analysis pave the way for informed material design strategies in the burgeoning field of 3D-printed construction materials.
CONCLUSION
3D printing technology offers several benefits over traditional construction methods in the field of building applications. The quest for a sustainable approach to replace conventional concrete has been a major issue due to its environmental impact. An environmentally friendly and more sustainable alternative to typical OPC-based concrete is geopolymer, which is made from industrial waste. The strong mechanical qualities and improved durability of geopolymers allow for a reduction in carbon footprint. Despite the advantages of geopolymer over OPC, the research conducted into using geopolymer in 3D printing is scarce.
The rheology requisites in terms of printability (pumpability and extrudability) and buildability, which distinguish 3DPGC from conventional concrete, are discussed. Some typical mixing regimes adopted for the preparation of geopolymer mixtures (two-part and one-part) for 3DPGC are reported. The printability, buildability, and structural characteristics are greatly dependent on the material design of the geopolymer mixture used for 3D printing. An in-depth review of the influence of mix design parameters of geopolymer formulation, such as aluminosilicate source materials, alkali activators, admixtures, aggregates, reinforcing elements, and curing conditions, on the properties of 3DPGC is systematically presented.
In conclusion, the detailed exploration of the rheological and structural aspects of 3DPGC provides a comprehensive understanding of the complex interplay between material composition, mix design, and processing parameters. The study delves into fundamental metrics like yield stress and plastic viscosity, emphasizing their significance in characterizing the flow behavior of the geopolymer slurry. Thixotropy, a time-dependent decrease in viscosity under increased shear stress, is identified as a crucial property for ensuring flowability and extrudability required for successful 3D printing.
The investigation extends to the critical parameters of printability (pumpability and extrudability) and buildability, shedding light on the challenges associated with layer deposition, structural integrity, and the prevention of failure due to gravity-induced stresses. The review systematically examines the material composition and mix design of 3DPGC, emphasizing the influence of aluminosilicate precursors, alkali activators, additives, aggregates, and curing conditions on properties such as workability, yield stress, viscosity, and structural build-up rate.
The exploration of different mixing regimes for the preparation of geopolymer mixtures demonstrates the role of equipment, sequence, and duration in achieving optimal rheological properties. The diverse methodologies, including one-part and two-part mixing approaches, underscore the adaptability of geopolymer mixtures to various methodologies, emphasizing the need for tailored mixing regimes to meet specific 3DPGC requirements.
Finally, the in-depth analysis of reinforcing elements provides valuable insights into the effects of fibers and steel micro-cables on flexural, tensile, and interlayer bond strengths. The section illustrates the delicate balance required in material design to optimize reinforcement while addressing challenges such as porosity, decreased interlayer bond strength, and workability degradation.
This systematic and comprehensive review not only advances the current understanding of 3DPGC but also serves as a valuable resource for researchers and practitioners seeking to optimize geopolymer formulations for 3D printing applications. The insights provided pave the way for future advancements, informed material design strategies, and continued evolution of 3D-printed construction materials toward enhanced precision, durability, and sustainability.
CHALLENGES AND RESEARCH OPPORTUNITIES
Based on this comprehensive review, research areas have been outlined and suggested for future studies, as follows:
- Precursor and activator effects:
- Challenge: Investigating the effects of precursor type, activator type, concentration, molar ratios, and chemical admixtures on 3DPGC properties is complex due to the numerous variables involved.
- Opportunity: Developing a systematic and standardized testing methodology to comprehensively study the multifaceted influences of different precursor and activator combinations on the properties of 3DPGC.
- Optimal mixing regime:
- Challenge: Determining the optimal mixing regime for 3DPGC is challenging due to the varied nature of the geopolymer formulation and its impact on the final product's characteristics.
- Opportunity: Conducting extensive experimental and computational studies to identify the most effective mixing methods for achieving desirable properties in 3DPGC, considering factors such as mixing speed, duration, and order of addition.
- Diversification of aluminosilicate precursors:
- Challenge: Limited investigations have explored unconventional aluminosilicate precursors for 3DPGC, hindering the understanding of the full spectrum of available materials.
- Opportunity: Evaluating the use of alternative aluminosilicate sources such as red mud, granite powder, marble dust, rice husk ash, construction and demolition wastes, and mine tailings to expand the range of sustainable materials for 3DPGC.
- User-friendly activators:
- Challenge: Current activator solutions are corrosive and hazardous, posing safety concerns. Exploring user-friendly alternatives is necessary.
- Opportunity: Research and develop solid activators or one-part geopolymer systems that are safer, easier to handle, and have the potential for large-scale application in 3DPGC.
- Interaction of admixtures:
- Challenge: Understanding the intricate interactions between accelerators, retarders, thixotropy modifiers, and VMAs in 3DPGC formulations is crucial for optimizing printability and buildability.
- Opportunity: Performing in-depth studies and simulations to unravel the synergistic or antagonistic effects of various admixtures, providing insights for fine-tuning their concentrations in 3DPGC mixtures.
- Rapid setting and hardening materials:
- Challenge: Identifying and incorporating rapid setting and hardening materials while maintaining desired properties are a complex task.
- Opportunity: Exploring novel materials and formulations that enhance the speed of setting and hardening in 3DPGC, ensuring compatibility with the 3D printing process.
- Sustainable aggregates:
- Challenge: The high cost associated with fine aggregates in 3DPGC necessitates research on sustainable alternatives without compromising performance.
- Opportunity: Investigating the partial or complete replacement of fine sand with geopolymer aggregates or other sustainable materials, assessing both economic and environmental aspects.
- Incorporation of organic fibers:
- Challenge: Understanding the impact of organic fibers on 3DPGC characteristics and optimizing their use are a relatively unexplored area.
- Opportunity: Evaluating the influence of different types and concentrations of organic fibers on the mechanical properties and printability of 3DPGC, aiming for enhanced performance.
- Durability and microstructure analysis:
- Challenge: Long-term performance prediction of 3DPGC and comprehensive microstructure analysis pose challenges owing to the complex interactions within the material.
- Opportunity: Doing extensive research on the durability aspects of 3DPGC, including exposure testing, and employing advanced imaging techniques for a detailed microstructure analysis to understand the material's behavior over time.
- Curing conditions and real-field applications:
- Challenge: Optimizing curing conditions, especially ambient curing, for 3DPGC in real-field construction applications is challenging.
- Opportunity: Examining the effects of ambient curing on the hardened qualities of 3DPGC and developing practical strategies for extrusion-based printing simultaneously with heat curing in real-field scenarios.
- Sustainability and life cycle assessment:
- Challenge: Assessing the sustainability and conducting life cycle assessments of 3DPGC involves considering a wide range of environmental factors.
- Opportunity: Developing a comprehensive framework for sustainability assessment and life cycle analysis of 3DPGC, considering factors such as raw material extraction, production, transportation, and end-of-life considerations.
- Topology optimization for material efficiency:
- Challenge: Implementing topology optimization methods for 3DPGC to minimize material consumption requires a balance between structural integrity and material efficiency.
- Opportunity: Exploring advanced optimization algorithms and design methodologies to achieve the maximum advantages of 3D printing, focusing on reducing material consumption without compromising structural performance.
- Machine learning and numerical modeling:
- Challenge: Predicting and controlling material composition parameters for 3DPGC prior to the printing process are intricate and demand advanced modeling techniques.
- Opportunity: Integrating machine learning and numerical modeling methods to develop predictive models for 3DPGC, aiding in the control of mix design and rheological and structural properties and facilitating real-field applications.
These challenges and research opportunities collectively aim to advance the understanding and application of 3DPGC in the construction sector. Researchers and practitioners can address these issues to contribute to the development of more efficient, sustainable, and widely applicable 3D printing technologies for construction materials.
AUTHORS’ CONTRIBUTIONS
Conceptualization, P.B., A.B. and S.S.; methodology, P.B., A.B. and S.S.; validation, A.B. and S.S.; formal analysis, A.B.; investigation, P.B., A.B. and S.S.; resources, A.B.; writing—original draft preparation, P.B., A.B. and S.S.; writing—review and editing, A.B.; project administration, A.B.; All authors have read and agreed to the published version of the manuscript.