All published articles of this journal are available on ScienceDirect.
Vertical Extension and Improving of Existing Buildings
Abstract
Low-density urban models, widely diffused in Spain until 2008, have been strongly criticized because they produce a great strain on the land, high infrastructure costs, increasing maintenance expenses, energy waste and pollution from excessive transport, time wasted commuting and more bedroom communities. To counterbalance this effect, opponents are claiming for a review of the capacity that the conventional city, with its higher population density and mixed uses, may still possess.
One possibility that has been explored is the vertical extension of buildings, which capitalizes on the remaining buildable space characteristic of many older buildings, and at the same time, refurbishes the housing block and improves standards of energy efficiency, safety and accessibility.
The challenge is not only technical - it is clear what needs to be done and how to do it - but it is also social and fiscal; in other words, how do we get organized and how do we finance such a project? The preferred construction system for vertical extensions is industrialized and uses two main materials: steel and wood. The system involves the use of two-dimensional panels and 3D pods that, once completed in the factory, are transported to the worksite, lifted by a crane and installed on the roof of the building. From refurbishing the existing building to adding the new vertical extension, the entire operation takes four months.
The experience of this vision and its application in the area of the Example in Barcelona, coming soon to other central neighborhoods in Spanish cities, allows us to present our first results: the detection of over 2,000 buildings with remaining buildable space, the need to vertically extend 50 buildings and our completed projects, in some cases already inhabited, of which half a dozen are currently undergoing environmental evaluation using our own tool.
1. INTRODUCTION
The urban explosion in the last 20 years in the majority of Spanish cities has taken over more land in urban areas than in the previous 2000 years [1]. These cities have witnessed the way that urban space has multiplied to the detriment of rural spaces and how the network of roadways has provoked a dissection of the land, shattering the ecosystem.
The resulting legacy of this accelerated and expansive growth is what we know nowadays as urban sprawl [2]. This type of development has provoked an uncontrollable consumption of the land and uses an important amount of energy and resources for urban planning and transport means, while exposing us to the nature of consumption in itself, which tends to outdate new progress in record time. We are exploiting and deconstructing environmental systems beyond their limits, thus fostering an unsustainable environment, and we must correct it.
The European Union warns of the inconveniences of sprawled, spread or unorganized [3] urban areas in its “White Book of Sustainability in Urban Planning” by the Social and Economic Committee and the Ministry of Spanish Housing. As a solution, they propose a compact city to reduce environmental impact, avoid social segregation and improve economic inefficiency derived from high energy and construction costs and infrastructure maintenance.
The viability of the compact city addresses variables of building density, spatial distribution and a percentage of green space and roadways; at the same time, the compact city reduces the disconnection between urban structure and function. Compactness is presented as a sustainable model in which close contact, sharing and information exchange in society and elements of the urban system are facilitated. In this way, all resources are used efficiently [4].
In response to the need for a compact, complex and efficient city, and to address ecological issues, we propose a new kind of urbanism organized by a three-tier strategy: aboveground, ground level and underground (Fig. 1) with vertical and horizontal consistency to achieve a higher level of self-sufficiency and habitability [5]. In established compact cities, this new approach means intervening in existing buildings by readapting and refurbishing architectural heritage, and by reprojecting the city in terms of layers.
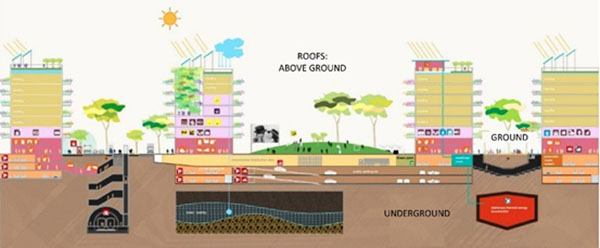
Refurbishment is the best solution for sustainability, as it requires much less energy than new construction by preserving, recovering and regenerating buildings [6]; not to mention the savings in urbanization costs and expenses involved in developing services and facilities for residents, as well as costs associated with expanding the transportation infrastructure.
Proceeding from the concept of levels, intervention in the compact city occurs by proposing vertical extensions in buildings and redesigning their skins and the way they relate to the surrounding environment regarding the cityscape, sustainable systems and infrastructures. Taking into account the compact city, ecological urbanism, sustainable construction and refurbishment, we propose a new way to build up and consolidate the city.
1.1. Barcelona
This new urban approach in the city of Barcelona, in the compact Eixample neighborhood, is possible within the framework of land-use planning, with the type of construction characteristic of buildings from the end of the XVIII century and beginning of the XIX, and with the approval of the municipal department of architectural heritage.
Over time, Cerdà’s Eixample has allowed for additions and reinterpretations of existing buildings. A general understanding of the buildings and the way the Eixample was developed is necessary for correct architectonic performance.
The area of the Eixample redefined the city of Barcelona, both in scale and dimension while complying with hygienic and functional criteria [7]. It allowed for the growth demanded by the congested city within the walls.
This period of prolific construction in the Eixample, after the walls were demolished in 1845, fortified building code regulations that bolstered the quality of the construction [8] and made it possible to do vertical extensions. Urban planning for an expansion neighborhood fostered the development of new masonry technology; mechanically-produced bricks and industrial quicklime production, along with fine mason workmanship, would guarantee quality results.
Masonry construction became the solution for the structural system and enclosures, the main elements being staircases, load-bearing and interlocking walls. The load-bearing capacity of masonry construction was not a concern, as it was strong enough to resist the static forces to which it was subjected. The methodology required detailed construction and performance criteria, resulting in a support system which optimized the structure and allowed it to bear more weight.
It was not until the middle of the XIX century when important vertical extensions were developed, as most of the city’s available plots were becoming occupied during that time. Until then, urban planners had never considered increasing the regulatory height of buildings.
The Land Plot Ordinance of 1860-90 established a maximum height of 20m for buildings. The City Block Ordinance of 1891-1941 increased land occupation by 73.6% and building length (from the street to the block center) along to 28m. The interior patio could reach 4.4m. In the “Congested Ordinance” of 1942-76 [9], building height increased to 24.4m (including a ground floor, seven additional floors, plus the top floor and penthouse), while patio height reached 5.5m. These were the first regulations that outlined vertical extensions as overall growth throughout the Eixample. The skyline of the Eixample radically changed, not only because of the regulatory height increase, but also because of the stepped geometry of roof structures. All additions, built on-site, were partial constructions that did not comply with composition guidelines for height nor sectional elements of the existing building.
The Metropolitan General Plan Ordinance (1976) redefined the maximum regulatory height of buildings, reducing it to 20.75m and 4.5m for patios.
Nowadays, the skyline is broken. According to the in-depth analysis conducted by “La casa por el tejado” [10] following the new regulations, there are some 800,000m2 of remaining buildable space distributed throughout some 1,800 buildings in the central area of the Eixample (Fig. 2).
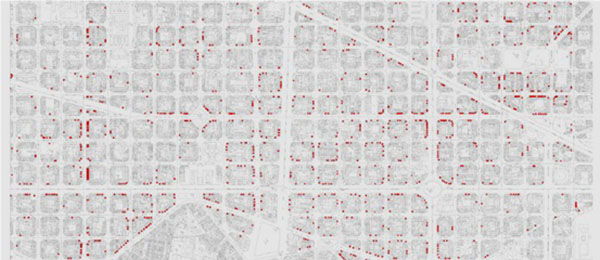
Considering the history of the city, the environment, social burden and sustainable systems and guidelines, the possibility of the vertical extension leads us to consider a new architectural approach: vertical extensions through industrialized architecture.
The proposal to vertically extend through industrialized design in the center of Barcelona is innovative [11]. Moreover, the presence of industrialized construction as a comprehensive solution is very low [12]. The integrated approach of improving the existing buildings and adding the industrialized vertical extension is original and introduces a new operation and management model to the market.
2. METHODOLOGY
A methodology of double intervention is proposed: refurbish the existing building and capitalize on remaining buildable space by adding vertical extensions.
After purchasing the vertical extension title or rights to exploit the unfinished space, the project is developed and the municipal works permit is requested. Once the project is underway, the work takes places on-site and in the factory: the existing building is refurbished and prepared to host the new extension, while the industrialized pods or modules that will complete the extension are produced. In the final phase, both processes come together where assembly meets finishing touches; a one-hundred-year-old building meets a new penthouse. From start to finish, many experts weigh in: economists, lawyers, architects, engineers, builders, skilled laborers and representatives from the public administration, all of whom are coordinated by a management team (overseeing the entire process) and a project manager (design and construction process).
2.1. Study and Objectives
In this stage (Fig. 3) we must consider the building’s history by compiling current graphic material with archived documents in order to study its composition, relationship with the environment, style, designer and any modifications subsequent to its original construction. From a technical perspective, we must consider structures, construction methods, installations and finishes. The current condition of the building must be evaluated to determine any modifications from the original state, the state of preservation of aesthetic and structural features, and any damage, which may threaten its stability or durability.
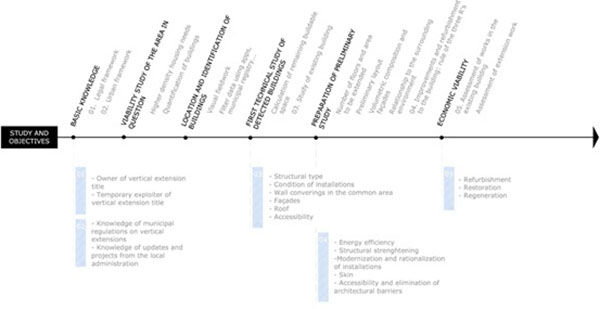
Considering the building will host one or more new floors, it is necessary to carry out a comprehensive study of its load-bearing capacity in order to identify any elements that will be removed, including obsolete construction like storage rooms, old water tanks, precarious or unstable homes and, sometimes, the upper slab and foundation of the Catalan roof. This process allows us to create a balance between the extracted weight and the added weight, which gives us the required information to calculate the load of the structure, determining the need (or not) to reinforce the structure or original foundation. The study is done through small excavations in strategic points in the foundation, as well as a geotechnical study of the land, the extraction of a section of the load-bearing wall (80 x 80 cm) with which a compression test is done in an approved laboratory, thus establishing useful resistance values for the calculation.
All of these steps (Fig. 3) make up part of a technical protocol established by the Bureau of Technical Control (OCT), which allows us to obtain Decennial Insurance for safeguarding the quality of the construction. The study and objectives stage is completed in compliance with current regulations regarding accessibility, fire protection, structural safety, installations and heritage aspects [13]. This information facilitates us in developing a list of improvements or upgrades to the existing building, a key factor for the evaluation and economic viability of the project.
2.2. Technical Project and Implementation
Both projects have two parts: the refurbishment of the building and its vertical extension (Fig. 4). The objective is to achieve a unitary result, both in terms of its adaptation to composition and its environmental behavior. The intervention is global and must meet the demands of the Building Evaluation Report [14].
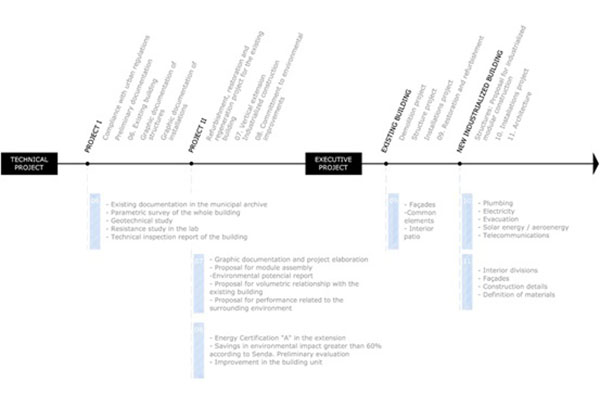
2.3. Refurbishment: Observations
If required, structural support may involve using underpinnings or micropiling to reinforce the foundation; adding thickening agents to strengthen load-bearing walls; repairing cracks, vertical collapses or slabs in poor condition; and preparing the rooftop with a transitional substructure, which will host the industrialized penthouses.
The installations are modified and replaced to comply with current regulations, with a specially designed project for each one (supply and drainage of water, gas, electricity, telecommunications, etc.). This allows for adaptation to modern uses, as well as the reduction of lighting consumption in common areas. In buildings where there is no elevator, one that complies with standards of energy efficiency is installed. Additionally, the intercom system between the flats and the front door is replaced.
The walls and cladding are refurbished through the façade and interior patios according to municipal heritage standards, including damage repair (cracks, deterioration, etc.), cleaning and painting of vertical walls, as well as the restoration of deteriorated elements to their original state. Repairing or replacing damaged woodwork, which does not comply with required sealing standards, is also evaluated. Air conditioners are removed and placed on the roof. The hall and stairwell are restored in a similar way, by recovering the cladding as much as possible (stucco, stone), woodwork and original fittings typical of modernisme or noucentisme.
2.4. Vertical Extension: Observations
In addition to the superior production speed and lightweight design of the penthouses, the industrialized, tailor-made construction model also provides social benefits (safe and comfortable working environment, less accidents and disturbance to the building), economic advantages (developing several vertical extensions simultaneously means competitive prices, less time spent on-site, the property becomes marketable sooner) and improved environmental circumstances (reduction in materials and waste [15, 16], increase in recycling during the manufacturing phase and toward the end of its life [17], higher quality and better durability).
The project is designed based on standards of industrialized construction (modularity, repetition, dry joints, lightness, etc.) and is conceived to take form in a factory where it is manufactured, assembled, disassembled and transported to be reassembled on-site. It is divided into three large work blocks: Architecture, Structure and Installations. The Architecture block includes aspects on composition, similarity to the original building, use, materials (function and environmental footprint are considered), taking into account functional and performance requirements set forth in current regulations [13], as well as heritage standards established by the local administration. The Structure block incorporates the application of lightness standards in the supporting elements of the extension, optimization of the existing structure and foundation and the adaptation of the modular structure for transport and new assembly of the extension in the original building. Lastly, the Installations block includes the application of energy efficiency standards, which allow us to achieve maximum quality ratings on the mandatory Energy Certification and with our own global environmental quality tool, Senda [18]. Joining the modules or other construction components on-site requires very precise installation assembly.
2.5. Construction Process: Work on the Existing Building and in the Factory
This stage (Fig. 5) takes place in the building with traditional construction methods, as well as in the factory under industrialized methods. High coordination is required in both work environments.
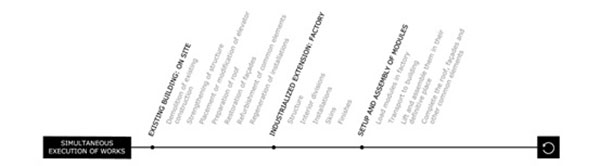
The construction in the building is executed following a planning process that ensures concurrence with the modular construction of the extension. Conventional techniques, also known as wet construction methods, are used, except in the interface of the structure between the existing building and the extension, where prefabricated elements, like supports, beams and connectors are used.
Construction of the extension takes place in a factory, which provides the infrastructure, dimensions and machinery that allow us to build several vertical extensions simultaneously. At the same time, the buildings are refurbished. Depending on the complexity and the size (each extension represents about 500m2), it takes approximately eight weeks to build the penthouses, while another six weeks are dedicated to on-site finishes.
This type of construction, which is based on a structure of steel prisms enclosed by wooden or steel panels containing a thermal insulation nucleus, requires a detailed and well-defined plan with no margin for improvisation once the plan is budgeted and closed. The system involves programs that incorporate information about each project, like BIM, as well as those used for manufacturing, which use CAD-CAM technology.
Once the construction phase is finalized in the factory, the modules (3D) or panels (2D) are taken apart in order to plan for the joints that will be fitted on-site. Structural components, closures and installations are identified according to their order of assembly and connection. The next step entails loading the trucks with the modules using an overhead crane. In order to avoid deformations, it might be necessary to use auxiliary support such as spreaders, pillars or tensors that may be disassembled once the modules are installed in the building.
By placing a large-load crane in the street (which implies some restrictions in transport), the modules are lifted from the trucks to the top of the building. The process (Fig. 6) typically lasts one day for each extension, including time for setting up and taking down the crane.
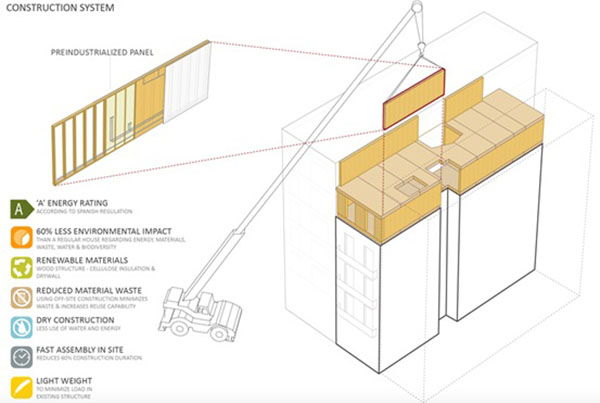
On the same day, once the modules are fitted to their host, the next step involves waterproofing the exposed part of the roof between the modules as well as between the new extension and the existing building. Moving forward, the interior unions are fitted, the installations are connected and tested, the façades are finished and a comprehensive review is done to analyze the minor details that will affect the finishes. At the same time, work is still being done on the existing building to refurbish and reform common areas, and to homogenize old and new elements. The construction process, in total, takes three months (Fig. 7).
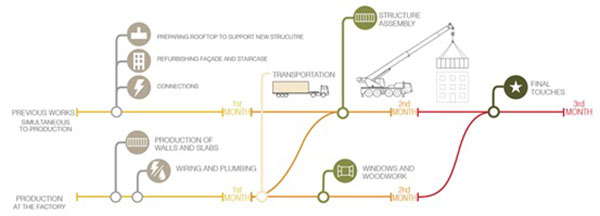
3. EXAMPLES OF APPLIED METHODOLOGY
The methodology described for refurbishing buildings and expanding them by vertical extension has been applied to seven buildings (Table 1) in the neighborhood of the Eixample in Barcelona as of September 2015. In the following sections we present three examples of applied methodology, which examine structural aspects (Aragó 359), general improvements to the existing building (Letamendi 29) and environmental improvements by vertical extension (E. Granados 69). This will allow us to view the achieved results. By the end of 2016, we estimate to intervene in twelve new buildings, including in Madrid and Pamplona.
Building | Refurbishment | Vertical Extension |
---|---|---|
Plaça del Doctor Letamendi, 29 | Common areas, the majority of the flats in the building, elevator installation. | Two penthouses on one floor, 200m2 area. |
Carrer d’Aragó 359 | Common areas, elevator installation. | Two penthouses, 150m2 and four flats, 300m2 area. |
Passeig de Sant Joan, 59 | Common areas, elevator extension. | Two penthouses on one floor, 150m2 area. |
Carrer de Roger de Llúria, 41 | Common areas, top floor, elevator installation. | One penthouse on one floor, 170m2 area. |
Carrer de Girona, 81 | Common areas, elevator extension. | One penthouse on one floor, 120m2 area. |
Carrer de Còrsega, 685 | Common areas, elevator installation. | Two penthouses, 160m2 area and three flats, 240m2 area. |
Carrer d’Enric Granados, 69 | Common areas, elevator installation. | Two penthouses on one floor, 200m2 area. |
3.1. Structural Studies and Design Process of the Existing Building and its Vertical Extension
From a structural standpoint, interventions raising the height over existing buildings can be exemplified in typical cases.
In the most favorable case, various existing constructions on the roof are removed as well as the top layer of the roof, and a storey of new construction is added. The load that was removed is similar to or even greater than the added weight (e.g.: Girona81).
In the worst case, few existing constructions are removed from the roof and two new levels are added. The load that was removed is less than the added weight (e.g.: Aragó 359). However, experience shows that in the majority of cases it was not necessary to reinforce the structure of the existing building.
The process of analysis and structural design proceeds through the following steps: 1) Analysis of the loads of the existing building and the weight that is removed. 2) Geo-technical study, determining the values for permissible stress of the ground. 3) Analysis of the maximum permissible stress of the load-bearing walls and foundation. 4) Study of the loads of the constructions added on the top (whose structural design is conducted in parallel, aiming for a minimal dead load and environmental impact of the materials used) and their effect on the walls, foundation and the ground. 5) Design of the system of load transmission between the constructions added to the roof and the existing building. 6) Checking that the effect of the added construction (and the corresponding use overload that have to be considered according to building standard regulations) on the walls, foundations and ground do not exceed the maximum permissible values (considering also the safety factors specified in the regulations).
In the case of Girona 81, there is a slight decrease in the total weight of the building (weight removed plus the weight of the added construction). As a result, the applied stress in the ground is 0,33N/mm2 with the limit state of rupture of the ground at 0,38N/mm2 after applying a safety factor of 3. The foundation of the party wall has a slight decrease in load from 134,85kN/m2 to 133,82kN/m2. The applied stress in the most unfavorable part of the section of the masonry wall (15cm in thickness) on the top side of the foundation is 1,24N/mm2, which is an acceptable value (the Spanish Technical Building Code sets the minimum resistance to compression for solid brick walls at 2N/mm2). The modules of the constructions added to the top are supported on an edge beam made of reinforced concrete with dimensions 15 x 20cm. The support with the most unfavorable load is 9,48T and the masonry wall bellow the edge beam has an applied stress of 0,79N/mm2.
In the case of Aragó 359, there is an increase in the total weight of the building (weight removed plus the weight of the added construction). As a result, the applied stress in the ground is 0,20N/mm2 with the limit state of rupture of the ground at 0,35N/mm2 after applying a safety factor of 3. The foundation of the party wall has a slight increase in load from 151,35 kN/m2 to 195,82 kN/m2. The applied stress in the most unfavorable part of the section of the masonry wall (15cm in thickness) on the top side of the foundation is 1,60N/mm2, which is an acceptable value (according to tensile strength tests the resistance is 7N/mm2 with a calculation value of 2,8 after applying a safety coefficient of 3).
The following Table 2 synthesizes some characteristics of the existing building, the evaluation process, the vertical extension added and the subsequent intervention.
Structure | Description | Observations | Tests | Function | Reinforcement |
---|---|---|---|---|---|
Floor | Fill of 0,9m thickness over hard clay and silt | Breaking load with a safety factor 3, of 3,8 kg/cm3 | Geotechnical probes, determine real tension below foundation | Supports the load of the building and the vertical extension of two floors | Not necessary |
Foundations | 0,6 m wide and 1,25 m high footings set in clay and silt | No significant deficiencies | Visual inspection for digging, test real tension below foundation | Supports the load of the building and the vertical extension of two floors | Not necessary |
Load-bearing walls | 0,3 m wide solid ceramic brick | No significant deficiencies | Test for limits, response not inferior to the effect of own weight, overloads, etc.. | Supports the load of the building and the vertical extension of two floors | Not necessary |
Upper slab | Slabs of ceramic bricks on steel joists | No significant deficiencies | Test for limits, response not inferior to the effect of own weight, overloads, etc.. | A structure which distributes the load of the vertical extension and resists horizontal forces must be incorporated | Make a chained beam of the support walls with forged cement |
Vertical Extension | 3 dimensional steel frame, welded | Folded steel slab with concrete layer | Design which complies with modern regulations | Supports standard use, transport and lifting | - |
3.2. Intervention in Plaça del Doctor Letamendi 29: Improvements to the Building
In this case, almost the entire building was refurbished (including the majority the homes and common areas). Not only did this allow us to develop an agenda of improvements, which was more ambitious than usual, but we were also able to become familiar with the condition of the whole building, most likely a representation of the typical state of many other buildings. In Table 3 below we highlight the changes between the initial and final state of the intervention.
Before | After | |
---|---|---|
Functionality Existing flats Terrace |
Four homes in a state of deterioration with deficiencies Out of use, obsolete installations, high side walls |
All homes refurbished and in use New penthouses, green roof, reduced side walls |
Accessibility Vertical mobility Communication |
The stairway was the only method to ascend (5 floors) Telecommunication installation with deficiencies |
Renovated stairway and incorporation of elevator New intercom system and telecommunication installation |
Safety Structures Installation |
Slabs between floors with affected materials Residual water pipes with cracks and leaks |
Repair and reinforcement of slab and load-bearing walls Replacement of pipes and new connections |
Heritage Main façade Interior spaces |
Deteriorated, discolored or missing closures, Walls, ceilings and carpentry in poor condition or modified from original |
Refurbishment of walls, carpentry and decorative elements Restoration of walls and woodwork to their original state |
Sustainability Existing building New penthouses |
Skin without insulation, inefficient installations, lack of comfort - |
Insulation in façades, efficient climate control, better waterproofing Thermal quality superior to standard regulation in walls and woodwork |
Economy Current expenses Revaluation |
High, but insufficient to maintain and refurbish the building - |
Minor given the incorporation of new neighbors in flats and penthouses Estimation: 35% for a sale; 70% for rental |
3.3. Intervention in Carrer d’Enric Granados 69: Environmental Aspects of the Vertical Extension
In this case, we applied the methodology and environmental evaluation tool Senda in greater depth. Senda was designed specifically for new penthouses as a product of vertical extensions in existing buildings. In compliance with the mandatory Energy Certification [19] and by using calculations of energetic performance in simulations that were tested during the development of Senda, the tool exposes a high potential for improvement with vertical extensions when compared to traditional performance. The expected environmental results are highlighted below Table 4.
Parameter | Reference building | Project building | Improvement |
---|---|---|---|
Heating demand (CTE HE1) | 24,81 kWh/m2 yearly | 10,93 kWh/m2 yearly | 56% |
Cooling demand (CTE HE1) | 15,00 kWh/m2 yearly | 2,33 kWh/m2 yearly | 85% |
Non-renewable primary energy (CTE HE0) | 57,22 kWh/m2 yearly | 25,30 kWh/m2 yearly | 56% |
Total CO2 emissions (Energy Certification) | 19,30 kgCO2/m2 yearly | 4,10 kgCO2/m2 yearly | 79% |
Category (Energy Certification) | D | A | 79% |
Global savings of impacts (Senda tool) | 0% | 62% | 62% |
4. DISCUSSION OF THE APPLIED METHODOLOGY
The examples of applied methodology in the present article have been chosen because of their relationship to three key features regarding viability: structural aspects (all three buildings support the remaining buildable space without intervention, which would render them unviable for the purpose of this article); general improvements to the buildings (how the quality of life of the residents improves and what it involves); and environmental improvements in the extension (reduction of impact). Verifying technical, social and environmental features (not developed in this article) allows us to expand the possibilities of intervention, which requires the vision of urban planning proposed at the beginning of the article.
- In this type of intervention, we must consider the limitations of structural elements. In effect, in vertical extensions with more than one floor (there are some programmed with up to four) there may be indications that the existing structure will not bear the load of the extension. Although not always, in these cases it is possible that the extra cost needed to reinforce the foundation and support walls would be compensated by the large area to be expanded, thus distributing the costs among the various units of housing to be sold. As a result, we expect that the methodology can be applied.
- At least in the present case, speaking in terms of general improvements to existing buildings, it can be difficult to recognize their value increase in the property. Residents who were consulted reported that they do not always consider the palpable economic increase in rental and sales prices (between 15% and 30%, according to our own data) when their façades are refurbished, patios renewed, historical elements restored or an elevator installed. This change, which is slow and gradual, requires an adjustment in the methodology in order to apply it to a larger number of cases and increase the number of people who can benefit from it.
- When discussing environmental improvements of the extension, it is important to note that the applied methodology cannot be generalized to all interventions. This is partially due to the fact that each location has its own conditions; for example, it is possible that sun exposure is insufficient to retain heat inside in the winter or to supply enough energy for solar installations. We also have verified that occasionally the shape of the extension involves a large quantity of skin compared to the rooftop, which increases the chances of heating gains or losses and infiltration through walls, ceilings and woodwork. It is also important to consider that there is a lack of environmental training in the team of technicians currently operating in the market, limiting the quality of the product, something that can be overcome by including training and awareness in the methodology.
CONCLUSION
- A review of the urban development model allows us to redirect our focus on the renewal of city centers, detecting high proportions of remaining buildable space on rooftops (around 2,500 buildings which make up 800,000m2 of buildable space in the Eixample of Barcelona alone).
- Acknowledging the upper layer of our cities, specifically in terms of the potential of remaining buildable space, makes it possible to undertake the improvement of existing buildings and provide new high-quality homes, at least in the seven completed cases. This results in improved quality of life for the community.
- Thanks to innovation in our methodology, our database, professional team and business model, we are able to move forward with an important number of projects (7 worksites, 7 licenses in progress, 27 titles acquired or in final negotiations).
- The presented methodology has been applied to and made possible in at least seven projects although, as previously mentioned, it requires certain adjustments to respond to unexpected or changing situations (recognizing the increase of property value, improvements in energy efficiency in the existing building, etc.) In that sense, the methodology must not be considered definitive, but rather as a part of the innovative process.
- Using industrialized and lighter construction methods in vertical extensions on 100-year-old buildings is an innovative approach that supports and simplifies refurbishment (no significant previous cases have been detected). Research and development applied to optimize results will allow us to improve solutions to a greater extent (time, cost, quality).
CONFLICT OF INTEREST
The authors confirm that this article content has no conflict of interest.
ACKNOWLEDGEMENTS
The authors would like to thank the following people for their collaboration: the members of the technical team from La Casa por el Tejado, its external collaborators and those who provided the reference images. Without them this article would not have been possible.