All published articles of this journal are available on ScienceDirect.
Improvement of Locally Available Raw Bentonite for Use as Drilling Mud
Abstract
Background:
Bentonite clays are widely used in a drilling operation and play a vital role as a drilling fluid. Bentonite clay mud performs several functions during the drilling operation and facilitates the drilling process.
Objective:
In this study, the locally available raw bentonite clays were investigated to evaluate its potential use as a mud for borehole drilling operation after its improvement with the additives.
Method:
Rheological properties such as plastic viscosity, yield point and gel strength were evaluated by using a viscometer and filtrate loss test was performed by using filter press on both locally available raw bentonite clays and the commercial bentonite named as Mill gel.
Results:
From the test results obtained for the up gradation of clays with the different beneficiating materials, the drastic increase in the plastic viscosity, yield point and gel strength has been observed. It shows that Xanthum gum produced better results for the improvement of rheological properties of such clays. Carboxymethyl cellulose and starch were used as additives and it has been observed that carboxymethyl cellulose has improved both viscosity and filtrate loss control, whereas starch muds have the best filtration control properties.
Conclusion:
Improved bentonite clays have rheological and filtration characteristics that have satisfied American Petroleum Institute specification at optimum conditions of clay. It was concluded that improved clays are the suitable material for the drilling operations and suitable to substitute commercial bentonite.
1. INTRODUCTION
Bentonite is a rock mainly formed from the alteration of volcanic ash and is very rich in montmorillonite (>80%) from the smectite group [1-4]. It is generally classified into two types, namely sodium (Na) or calcium (Ca). Ca-bentonite with Ca++ as a dominant exchangeable cation has a low swelling and water absorption ability, while the Na-bentonite carrying Na++ as a dominant exchangeable cation, exhibits more swelling and absorb a large amount of water to form a more viscous fluid [3]. Most of the montmorillonite deposits available worldwide are calcium types. However, there are some deposits of Na-montmorillonite available in Mexico, Argentina, South Africa, Turkey, Japan, and Australia [5].
Bentonite is in high demand for various industrial applications. It can be used as a drilling mud for oil wells and as a sealant or liner for dams and landfills projects. It has also special use in cosmetics, pharmaceuticals, foods, ceramics, paints, paper and iron industries [6-13]. The valuable use of bentonite in different industries attributes to its important physical properties such as small particle size, high surface area, high viscosity, absorption and swelling properties, cation exchange capacity, high bond strength, plasticity and impermeability [8, 9, 14, 15].
There are different kinds and grades of bentonite deposits in Pakistan [16-23]. Huge reserves of bentonite are available in Karrak [24], Mirpur [25], Rawalpindi, Attock and Jhelum areas [17]. But, still, there are several bentonite deposits that need to be explored. Recently, some studies have been done to explore the potential of the indigenous material to be used as a bleaching or decolourization agent [26], removal of magnesium [27] pozzolan for cement replacement [28-31] and its use in pharmaceutical industry [24]. But, there are very few works found in literature which can describe the utilization of bentonite clay with the intention of drilling fluid formulation, although its large deposits have been discovered in various parts of Pakistan. As a result, most of the bentonite is imported from other countries by the petroleum industry for carrying out drilling works in Pakistan. Clearly, there exists need to experimentally investigate the suitability of the bentonite deposits in Pakistan as a replacement of imported bentonite for use in oil well-drilling. Most of the bentonite deposits available in Pakistan are Ca type or Na-Ca type [24]. So, it is commonly known that even a good quality Na-bentonite in natural form does not fulfill the standard requirement for drilling mud [32]. There is a need to either activate or add some polymer to upgrade the raw Na-Ca bentonite and even to Ca-bentonite to meet the American Petroleum Institute (API) standards. The minimum viscosity at 600 rpm should be 30Cp and maximum filtration loss should be 15 cm3 in order to fulfill the requirement of API standard for drilling mud [33]. Many investigators modified the raw natural bentonite by adding polymers and similar compounds and found it very effective in getting high viscosity and low filtrate losses [34-41].
The aim of this study was to investigate the use of bentonite as a drilling fluid and explore its use with different kinds of additives to enhance the performance of bentonite as drilling mud to acceptable standards. This study will provide a platform to encourage the use of local bentonite as drilling mud and thus to save a lot of money which is spent on importation of bentonite from other countries for oil well drilling. Research based on effective and efficient local sourcing will result in promoting development of industrial sector, mining and quarrying techniques. Marketing future of bentonite is quite bright in Pakistan, provided the indigenous material is upgraded up to international standard.
2. MATERIALS AND METHOD
2.1. Sample Collection and Preparation
The bentonite samples were collected from seven different sources of Khyber Pakhtunkhwa, Punjab provinces and also from Azad Jammu & Kashmir and Federally Administrated Tribal Areas (FATA) of Pakistan. Unfortunately, the local unskilled workers have applied only crude and risky mining methods for extraction of bentonite. The miner digs out narrow holes along the deep slope and excavates the bentonite by hand as shown in Fig. (1). The available bentonite layer was used for collecting its fresh samples. Two sources (Jhelum and Jundola) were selected for detail investigation of its potential use as an oil well drilling mud. The collected samples were first crushed to smaller particles and left for a week in sunlight for drying. The samples were then placed in an oven at the standard temperature for complete drying before grinding. Samples were then ground by the mechanical grinder and passed through Sieve No. 200 using a mechanical sieve shaker to meet the API standards [42]. Commercially available bentonite (Mill Gel) were used as a reference bentonite and xanthan gum, carboxy methyl cellulose (CMC HV), starch were used as an additive for improving the characteristic of raw bentonite.
2.2. Chemical Analysis
XRF (X-ray fluorescence) were made for all the samples by using X-ray spectrometer in the Geoscience Laboratories Islamabad as shown in Table 1. Chemical analysis results showed that the Al2O3/SiO2 ratio is approximately 1/3 or more for all the samples, and found similar to Wyoming bentonite and satisfy the basic requirement in montmorillonite. As the mass ratio of Na/Ca for Jhelum and Jundola bentonite is 1.5 and 1.6, respectively and the mass ratio of (Na + K)/(Ca + Mg) for both the bentonite is around 2, so both bentonite fall within the category of Sodium Bentonite [43].
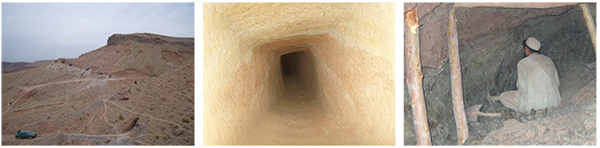
Oxides | Attock | Cherat | Gari Chundun | Jhelum | Azakhel | Jhandola | Bimber | ||
---|---|---|---|---|---|---|---|---|---|
SiO2 | 49.9 | 51.4 | 52.0 | 48.6 | 50.4 | 53.5 | 50.9 | ||
Al2O3 | 18.2 | 21.4 | 16.2 | 18.7 | 18.9 | 18.6 | 17.8 | ||
Fe2O3 | 3.2 | 5.8 | 4.6 | 3.3 | 4.7 | 7.5 | 3.3 | ||
TiO2 | 0.3 | 0.5 | 0.5 | 0.4 | 0.6 | 0.6 | 0.4 | ||
MgO | 0.1 | 0.2 | 0.1 | 0.1 | 0.1 | 0.1 | 0.1 | ||
Na2O | 4.2 | 3.5 | 4.1 | 4.0 | 3.5 | 3.9 | 4.0 | ||
CaO | 2.8 | 1.2 | 3.3 | 2.7 | 2.1 | 2.4 | 1.8 | ||
K2O | 0.3 | 0.5 | 1.2 | 1.6 | 4.0 | 0.5 | 1.4 | ||
SO3 | 0.5 | 1.3 | 1.4 | 0.7 | 1.1 | 1.9 | 0.7 | ||
P2O5 | 0.1 | 0.1 | 0.1 | 0.1 | 0.2 | 0.1 | 0.1 | ||
LOI | 20.5 | 14.0 | 16.5 | 19.7 | 14.4 | 14.1 | 18.9 |
2.3. Mixing Method and Drilling Fluid Preparation
The performance of drilling fluids and additives was tested according to the API standard procedures which are compiled in the API specification 13A [42]. A base liquid and an additive need to be fully mixed or dissolved into a liquid to get a homogenized fluid, known as drilling mud. A Hamilton Beach commercial mixer as shown in Fig. (2a) was used to prepare drilling mud for various laboratory tests. This mixer conforms to the API specifications 13A. The control mud sample was prepared by adding 21 g (6%) Mill Gel to 350 ml of water while increasing weights of 21 g, 40 g, 60 g, 80 g and 100 g of Jhelum and Jundola were added to 350 mL water to prepare different mud weights. Commercially available additives (Xanthan gum, CMC HV, starch) were used to apply improvement tests on Jhelum and Jundola mud samples of 6% (21g/350 mL) by mass according to API standards
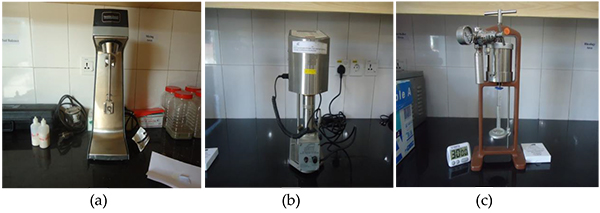
2.4. Rheological Characterization
Different parameters were used to evaluate the mud rheology which included plastic viscosity, yield point and gel strength. These parameters were measured with the help of a multi-speed viscometer (Model 900) as shown in Fig. (2b) by changing a number of additives that included Xanthan gum, CMC HV, starch and their blend.
2.5. Filtration Tests
A filter press as given in Fig. (2c) was used to determine the filtrate loss of different solution by applying a standard cell pressure of 100 ± 1.0 PSI (690 ± 6.9 kPa) to the top cap using a back pressure regulator attached to a nitrogen tank within 30 seconds for a 30 minute test as recommended by the API standards [43]. At the end of 30 min, filtrate volume was measured in a graduated cylinder through the drain tube.
3. RESULTS AND DISCUSSION
3.1. Rheological Properties of the Raw Jhelum and Jundola Bentonite:
The rheological parameters including plastic viscosity, apparent viscosity, yield point and gel strength of the mud at different concentrations of Jhelum and Jundola bentonites (21g, 40g, 60g, 80g and 100g) in 350 mL of water was compared to commercial bentonite (Mill Gel) at 21 g/350 mL (6% by mass) according to API specification as shown in Figs. (4, 5). The rheological properties showed a major increase in the apparent viscosity, plastic viscosity, yield point and gel strength because of the increase in the concentration of both bentonites from 20 g to 100 g. The optimum rheological properties observed which approximates that of Mill Gel as 80 g/350 mL and 60 g/350 mL for Jhelum and Jundola bentonites, respectively.
The dependence of apparent viscosity on shear rate (rpm) at different clay concentrations from 20–100 g/350 mL is shown in Fig. (3). It was observed that apparent viscosity was high in the initial stages but it starts decreasing and become constant at later ages. This indicated that viscosity at low shear was increased with enhanced clay concentration. Both the Jhelum and Jundola muds demonstrated remarkable improvement in the rheology as the concentration of the clay increased which has shown their capabilities for drilling purposes.
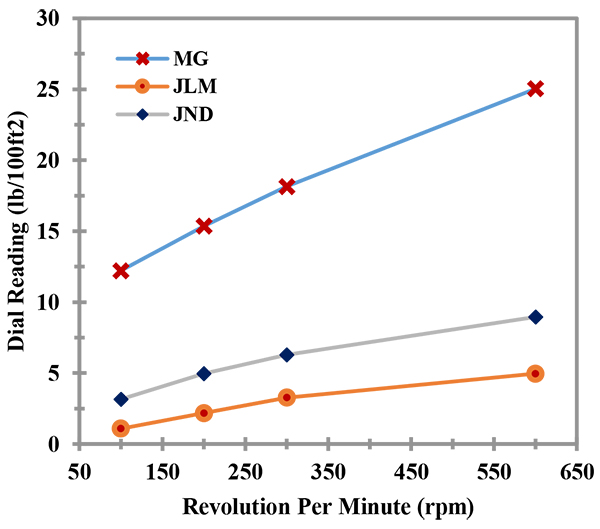
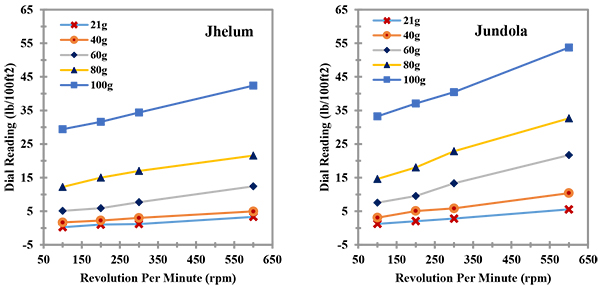
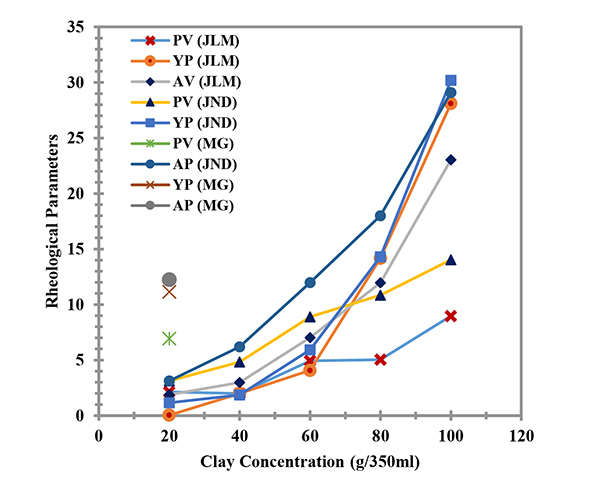
3.2. Filtration Properties of the Raw Jhelum and Jundola Bentonite:
When the weight percent of the clay was increased, the filtration properties of the local clay mud systems showed distinct changes at different mud levels. A decrease in the filtrate loss with the increase in the percentage of Jhelum clay was noted. However, it was higher than the filtrate loss of 21g/350mL (Mill gel) at all of the clay concentrations of the local clays. On the contrary with the Jundola bentonite, the filtrate loss decreased at 100g/350mL. It was a low level than the imported bentonite at standard API concentration of 21g/350mL as given in Fig. (6). These results revealed that low bentonite concentrations are needed to be applied in local raw bentonite system. This can be done by adding chemicals or polymers that will check fluid losses during the drilling processes.
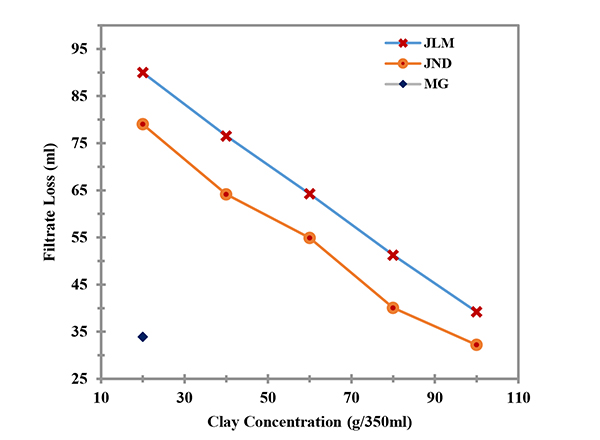
3.3. Improvement Tests
Rheological parameters were measured for Jhelum and Jundola mud. These included plastic viscosity, yield point and gel strength and filtration properties. It was observed that both of the properties were improved with the addition of commercially available additives (Xanthan gum, CMC HV and Starch) which are commonly used by the drilling industry in the oil-well drilling. After measuring the individual and combined effects of these additives, the improved bentonite results were compared with the commercial bentonite (Mill gel) muds.
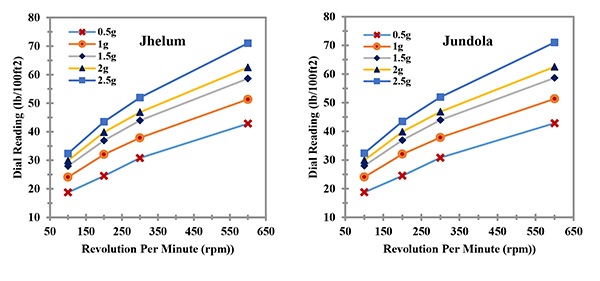
3.3.1. Rheological properties of the improved Jhelum and Jundola Bentonite:
Xanthan gum (XG) was used to improve the rheological properties of raw bentonites. The addition of XG resulted in a significant increase of the dial readings of the mud at all speeds at a constant concentration (21g/350mL) of both Jhelum and Jundola muds as shown in Figs. (7, 8). It indicated a notable increase in the apparent viscosity, plastic viscosity and yield point. For instance, the dial reading at 600 rpm increased sharply from 5 to 70 with the addition of 9.5% Xanthan gum to 21g/350 mL Jhelum mud. It represented an increase of 13 folds in the dial readings and has given an increase of 6.5 and 40 times in the plastic viscosity and yield point respectively. Tests results showed an improved performance in the mud which will result in better drilling performance. The effect of Xanthan gum also indicated an upward trend in the formation of 10 sec and 10 min Gel strength. This demonstrated an ability of the drilling mud to suspend drill solid and weighing material when circulation was stopped.
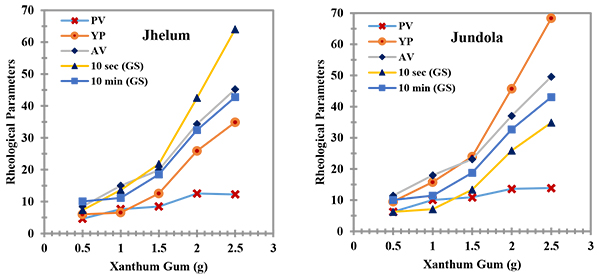
When Jundola bentonite was also compared with the Jhelum bentonite, the former exhibited a great increase in the rheological parameters (plastic viscosity, apparent viscosity, yield point and gel strength) at the same concentrations of both bentonite clays (21g/350mL) and additives. The combined effect of the constant amount of Xanthan gum (1g) and varied amount of carboxymethyl cellulose was observed. High viscosity (CMC HV) indicated an excellent result in controlling both the rheological and filtration properties as shown in Figs. (9, 10). When 5% Xanthan gum and 9.5% CML HV were added to 21g/350mL Jhelum mud, the dial reading at 600 rpm greatly increased from 5 to 63. It has given 11.5 folds increase in the dial readings and enhanced plastic viscosity and yield point to 8 and 31 times, respectively. This showed a rheological requirement for drilling purpose and met the API standards. The Jundola bentonite revealed better result in plastic viscosity, yield point and formation of gel strength than Jhelum bentonite.
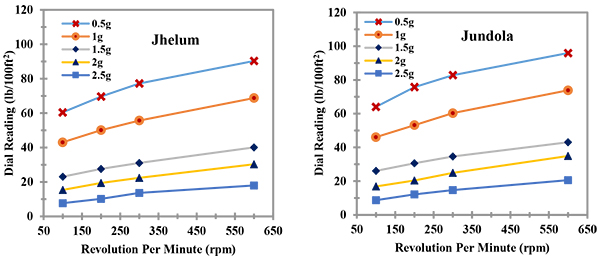
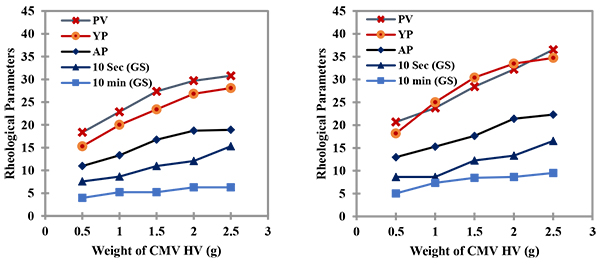
3.3.2. Filtration Properties of Improved Jhelum and Jundola Bentonite:
The filtration properties of Jhelum and Jundola muds under the combined effect of CMC HV + Xanthan gum at standard clay concentration (21g/350mL) are presented in Fig. (11a). There was a drastic decrease in the filtrate loss as the amount of CMC HV in the mud was increased. When 7% CMC (HV) and 1g of Xanthan gum were added to the Jhelum bentonite mud samples, a reduced filtrate loss was noted i. e., 3.4 times to its original loss. This decrease in filtrate loss of the clay showed that the beneficiation improved the ability of the clay particles to remain in the suspension. As compared to Jhelum bentonite, the Jundola bentonite mud showed a better result in controlling the filtrate loss behavior of mud at the same concentration of additives.
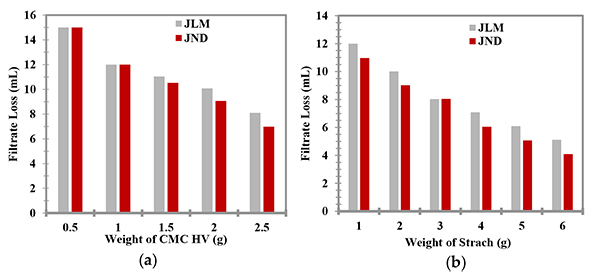
The filtration properties for both bentonites were evaluated by adding Starch and Xanthan gum together at standard clay concentration (21g/350Ml). The starch beneficiated Jhelum samples gave an improvement in the filtration properties as shown in Fig. (11b). An addition of 12% starch and Xanthan gum to beneficiate the Jhelum mud samples resulted in 3.7 folds reduction in the filtrate loss. This could be explained by the suspending and flocculating properties of starch. Similarly, there was a reduction of about 55% and 33% in the mud cake thickness as starch and CMC HV was used to support the local mud. The rate at which fluid was lost is a function of the thickness of filter cake. The decrease in the filtrate loss and mud cake thickness of the Jhelum and Jundola muds improved the overall ability of the mud to minimize the issue which normally occurs because of high filtrate.
CONCLUSION
Locally available raw bentonite from Jhelum and Jhandola areas were improved by adding additives such as Xanthum gum, CMC HV and starch to fulfill the API requirements. With the increase of clay concentration, both the filtration and rheological properties were improved and the optimum concentrations of 80 g/350 mL for Jhelum and 60 g/350 mL for Jundola bentonite were found. When beneficiated at 21 g/350 mL with 9.5% Xanthan gum, clay exhibited 13 folds increase in the dial readings that gave an increase of 6.5 and 40 times in the plastic viscosity and yield point, respectively. The addition of 12% starch and 1g Xanthan gum to upgrade the Jhelum mud samples resulted in 3.7 folds reduction in the filtrate loss and 55% and 33% in mud cake thickness, respectively. It is concluded that both Jhelum and Jundola bentonite has the potential to substitute the commercial bentonite and met the API standards when they were improved with Xanthum gum, CMC HV and starch. Further research is needed to evaluate the properties of the local mud by adding some locally available low-cost additives to enhance its rheological properties and filtration loss to fulfill the API standard for oil-well drilling.
ETHICS APPROVAL AND CONSENT TO PARTICIPATE
Not applicable.
CONSENT FOR PUBLICATION
Not applicable.
CONFLICT OF INTEREST
The authors declare no conflict of interest, financial or otherwise.
ACKNOWLEDGEMENTS
We want to thank MOL (Oil and Gas Co.) Pakistan and Baker Hughes (oil well drilling company) for allowing us to perform our testing in their state of the art labs.